Abstract
A surface dielectric barrier discharge plasma reactor was employed to study Hg0 oxidation in coal-fired flue gas. The experimental results showed that 98 % of Hg0 oxidation efficiency and 13.7 μg kJ−1 of energy yield were obtained under a specific energy density (SED) of 7.9 J L−1. Increasing SED was beneficial for Hg0 oxidation due to higher production of active species. Higher initial concentration resulted in lower Hg0 oxidation efficiency, but higher amount of Hg0 oxidation. Water vapor inhibited Hg0 oxidation because the generation of O3 was suppressed. The presence of NO remarkably restrained Hg0 oxidation, while SO2 showed little effect on Hg0 oxidation. Roles of active species in Hg0 oxidation were examined under different gas atmospheres (O2 and air), indicating that O3 played an important role in Hg0 oxidation. Deposits on the internal surface of the reactor were analyzed by energy dispersive spectroscopy and the product was identified as HgO.
Similar content being viewed by others
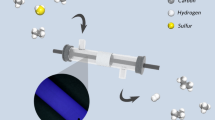
Avoid common mistakes on your manuscript.
Introduction
Mercury has been listed as a hazardous and toxic pollutant under Title III of the 1990 Clean Air Act Amendments (CAAA) in the United States because of its volatility, persistence and bioaccumulation as methylmercury in the environment and its neurological health impacts [1]. Coal-fired power plants are the major anthropogenic mercury emission sources in China and the U.S. because of the huge coal consumption for power generation [2]. Mercury is presented in coal-fired flue gas as elemental mercury (Hg0), oxidized mercury (Hg2+) and particle-bound mercury (Hgp) [3]. As reported, different species of mercury have different physical and chemical properties [4]. Hgp can be captured by particulate matter (PM) control devices such as electrostatic precipitators (ESPs) and fabric filters (FF). Hg2+ is soluble in water and has the tendency to associate with PM. Hence, Hg2+ is relatively easy to be removed from flue gas using typical air pollution control devices (APCDs). Hg0, however, is hardly captured by APCDs due to high equilibrium vapor pressure and water insoluble [5]. Therefore, with consideration of the properties of Hg2+, Hgp and Hg0, studies for the Hg0 oxidation methods should be first considered. Injection of powder activated carbon (PAC) impregnated with certain chemicals (i.e., sulfur species) has been successfully applied for the control of mercury emissions from incineration [6]. However, some drawbacks constrain the application of mercury adsorption technology in coal-fired flue gas purification, which includes high cost and high carbon-to-mercury ratio (3,000:1–100000:1).
As effective oxidation technologies, the preoxidation of Hg0 to Hg2+ is necessary for the removal of Hg0 by combining the present typical APCDs. Among preoxidation technologies under development, advanced oxidation processes (AOPs) are receiving great emphasis on pollution control because of their ability to rapidly oxidize hazardous air pollutants [7, 8]. Among the AOPs, non-thermal discharge plasmas (NTPs), which generate a large number of chemical active species such as ·O and O3, have been developed as a new method applicable for processing waste gas [9, 10], the removal of volatile organic compounds (VOCs) [11, 12] and oxidizing Hg0 [13–17]. NTP processes are highly effective in producing free radicals to enhance the removal of hazardous air pollutants.
Dielectric barrier discharge (DBD), one of NTPs, has received the most extensive investigation due to its high removal efficiency and environmental compatibility. DBD can be divided into four types based on the reactor geometry: typical DBD, surface discharge, coplanar discharge, and packed-bed discharge [12]. Surface DBD (SDBD) plasma reactors (SDBDs) have aroused considerable interest because of its unique features and characteristics, for example, SDBDs are easily manufactured than other DBD reactor, and SDBDs result in a decrease in the breakdown voltages, and thus better energy efficiency is obtained [18]. Moreover, the flue gas resistance in SDBDs is much less than that in other DBD reactors due to its wider electrode gap in SDBDs when flue gas passes through DBD reactors. Up to now, some researchers mainly focused on the removal of VOCs at low concentration levels using SDBDs [19–21]. For example, Oda et al. studied decomposition of gaseous organic contaminants by surface discharge induced plasma chemical processing (SPCP) and removal rates of 95 % for acetone and 100 % for 2-propanol were obtained using a ceramic tube reactor with strip-like electrodes [19]. Seung-Min Oh et al. used a surface discharge plasma reactor (SDBD) packed with various zeolites and the toluene adsorbed in micropores was decomposed by active oxygen species generated in the plasma zone on the zeolite surface [21]. However, only Masuda et al. [22] studied the oxidation of Hg0 in simulated flue gas using SPCP, and the study demonstrated that SPCP was a feasible technology to oxidize Hg0 in the flue gas, but the important parameters in Hg0 oxidation should be further evaluated in detail.
The objective of the study is to evaluate Hg0 oxidation performance of SDBD, and the important parameters including energy input, Hg0 initial concentration, gas atmospheres, and flue gas components (H2O, NO, SO2) were examined. In addition, the evolution of Hg0, Hg2+ and total Hg concentrations was investigated, and the Hg0 oxidation mechanisms were also identified.
Experimental Section
Experimental Setup
The experimental setup designed (Fig. 1) for study of the Hg0 oxidation was composed of a continuous gas flow sample generation system, a SDBD and a gas sampling analysis and detection system. The SDBD was comprised of a quartz tube (o.d. of 15 mm, i.d. of 12 mm and length of 260 mm), the outside of which was closely wrapped with the silver paper to act as a grounded electrode (length 200 mm). The high voltage electrode was a stainless steel wire coiled (diameter of 1 mm) on the inside of the tube. An AC voltage (50 Hz) was applied to produce the discharge plasma, and the peak voltage was varied from 4 to 12 kV. The peak voltage and current were measured with an oscilloscope (Tektronix TDS2014) equipped with a voltage probe (Tektronix P6015A) and a current probe (Tektronix P6021). The typical voltage and current waveform obtained in the experiment was shown in Fig. 2. The voltage-charge (V-Q) Lissajous method (C = 1 μF) was used to determine the discharge power (W).
Experimental Methods
All the experiments were run at a constant gas flow rate of 4.5 L min−1 at room temperature. A Dynacal mercury permeation device (VICI Metronic, Inc. USA) was used to provide trace mercury vapor of desired Hg0 concentration. The permeation device was located at the bottom of a glass U-tube that was immersed in a temperature-controlled water bath. Water vapor was generated by an evaporator and introduced into the flue gas with the carrier of air. The humidity of flue gas was measured with a humidity tester (Rotronic HP22-A + HC2-HK40). A RA-915 + mercury analyzer (Lumex, RU) coupled with RP91 was employed to measure Hg0 concentration. The balance of mercury was conducted in accordance with the ASTM method of Ontario Hydro sampling (ASTM D6784-02) [23]. The ozone (O3) concentrations in flue gas were measured by the iodometry method [24]. The deposited mercury species elements were determined by energy-dispersive X-ray spectroscopy (EDX, NORAN system).
The definition of Hg0 oxidation efficiency was as follows:
where \({\text{Hg}}_{\text{in}}^{ 0}\) and \({\text{Hg}}_{\text{out}}^{ 0}\) are the concentrations of Hg0 (μg m−3) measured at the outlet of plasma reactor without or with high voltage discharge, respectively.
The specific energy density (SED) and energy yield were calculated:
Results and Discussion
Effect of Energy input on Hg0 Oxidation Efficiency
The effect of energy input on Hg0 oxidation efficiency was illustrated in Fig. 3. Obviously, increasing SED enhanced Hg0 oxidation efficiency due to a higher energy input introduced in the discharge. With an increase of SED from 0.8 to 7.9 J L−1, Hg0 oxidation efficiency increased from 80 to 98 %. Increasing SED leads to the production of more plasma channels and chemically active species, therefore, Hg0 oxidation efficiency is enhanced. In addition, Hg0 oxidation efficiency of 80 % achieved at SED of 0.8 J L−1, indicated that SDBD showed excellent performance of Hg0 oxidation.
In order to show performances of the SDBD compared to other types of plasma reactor, a brief comparison of the present results with other similar works was summarized in Table 1. Concentric cylinder discharge reactor (CCDR) and wire-plate type reactor exhibited lower Hg0 oxidation efficiency and energy yield compared with the present study. For example, 59 % of Hg0 oxidation efficiency and 7.5 μg kJ−1 of energy yield was obtained for the CCDR [13], and 80 % of Hg0 oxidation efficiency and 2.2 μg kJ−1 of energy yield was observed for the wire-plate type reactor [25]. Hg0 oxidation efficiencies obtained by the wire-cylinder reactor [26] were comparable with that of the present research, but the energy yields were much lower than that of the present study. For ozone injection technology [13], Hg0 oxidation efficiency and energy yield were comparable with that of the present research. For example, 93 % of Hg0 oxidation efficiency and 12.3 μg kJ−1 of energy yield was obtained for the ozone injection technology [13]. Hence, it is believed that it is an alternative and efficient method for SDBD to oxidize Hg0 in the coal-fired flue gas. However, energy yield is strongly dependent on multiple factor, including air flow rate (Q), initial concentration and SED, for example, higher initial concentration and lower SED results in higher energy yield. Therefore, Table 1 gives only a qualitative and approximate comparison.
Effect of Hg0 Initial Concentration on Hg0 Oxidation Efficiency
Generally, Hg0 concentration of actual flue gas strongly varies. The effect of Hg0 initial concentration on its oxidation was studied in the range of 50–170 μg m−3, and Hg0 oxidation efficiency and energy yield were presented in Fig. 4. The results showed that Hg0 oxidation efficiency and energy yield were directly related to the initial concentration. Hg0 oxidation efficiency had a slight drop with the increase of Hg0 initial concentration from 50 to 170 μg m−3 at about 7.9 J L−1. However, energy yield remarkably enhanced from 6.3 to 21.1 μg kJ−1 under the same condition of SED. This phenomenon can be explained by the fact that the DBD energy dissipation levels remained comparable, the average energy availability per molecule decreased with the increase of the initial concentration. Hence, Hg0 oxidation efficiency decreased with an increase of the initial concentration. However, the absolute removal of Hg0 molecules increases because of higher initial concentration and higher probability of interaction with short-lived active species.
Effect of Gas Atmospheres on Hg0 Oxidation Efficiency
In order to investigate the roles of active species in Hg0 oxidation, experiments were conducted separately under oxygen and air atmospheres. The experimental results were shown in Fig. 5. As observed, Hg0 oxidation efficiencies under oxygen atmosphere were higher than that under air atmosphere. Under the condition of oxygen atmosphere, the density of oxygen-based active species produced in the discharge was larger than those under air atmosphere, resulting in higher oxidation efficiency in the case of oxygen atmosphere.
In order to study the contribution of O3 to Hg0 oxidation, the experiment of Hg0 oxidation by O3 treatment was conducted and the result was shown in Fig. 5. Herein, the O3 concentration was equal to that obtained by the discharge treatment under air atmosphere. O3 was generated by another of the same SDBD and injected into the reactor to react with Hg0. Under the condition of 0.8 J L−1, 75 % of Hg0 was oxidized, which was slightly lower than that under air atmosphere. These results indicated that (1) in the case of air atmosphere, there were other active species involved with the Hg0 oxidation in addition to O3. (2) O3 was the main active species for Hg0 oxidation.
Effect of H2O on Hg0 Oxidation Efficiency
The effect of H2O on Hg0 oxidation efficiency was presented in Fig. 6. At SED of 7.9 J L−1, compared with the dry gas, the addition of 3 and 5 % water vapor dropped Hg0 oxidation efficiency from 98 to 96 and 91 %, respectively. Therefore, the presence of H2O exhibited a slightly suppressed effect on Hg0 oxidation, and the similar result was reported by the literature [26]. H2O may react with O3 to form ·OH, resulting in the decreasing of Hg0 oxidation efficiency due to the fact that the O3/·O radicals are more effective than ·OH to oxidize Hg0. Simultaneously, ·OH can act as a promoter in the reactions (10) and (11) decreasing O3 and ·O [27–29]. As shown in Table 2, O3 concentration dropped with an increase of H2O contents, and higher O3 concentration was obtained for dry gas as compared to that for 3 and 5 % H2O. Only 10.8 μg L−1 of O3 was observed for 5 % H2O, whereas O3 concentration of 18 μg L−1 was obtained for dry gas at the same SED 7.9 J L−1. The reactions can be described as follows:
Effect of NO on Hg0 Oxidation Efficiency
NO is ubiquitous in flue gas environment and has significant impacts on Hg0 oxidation efficiency. As shown in Fig. 7, the presence of NO showed obvious inhibition on Hg0 oxidation. In the absence of NO, Hg0 oxidation efficiency was 98 % at around 7.9 J L−1, when NO concentration increased to 300 ppm, Hg0 oxidation efficiency had a dramatically decrease to 69 %, and with NO concentration increased to 600 ppm, Hg0 oxidation efficiency further dropped to 58 % at the same SED. The competitive reactions of Hg0 and NO gases with the chemical active radicals generated in the reactor. The reaction rate coefficient of NO with O3 (1.8 × 10−14 cm3 molecules−1 s−1) (Reaction 13) [29] is much faster than that of (10.5 ± 0.65) × 10−19 cm3 molecules−1 s−1 [30] for Hg0 reacting with O3, implying that the O3 can rapidly react with NO. Therefore, O3 will be preferentially exhausted, Hg0 oxidation efficiency markedly reduced, being in agreement with the results obtained in previous studies [31–33].
Effect of SO2 on Hg0 Oxidation Efficiency
The concentration of SO2 was varied to study effect of SO2 on the Hg0 oxidation (Fig. 8). As observed, no obvious decrease of Hg0 oxidation efficiency was detected when 500 ppm SO2 was introduced to the gas flow or even when SO2 concentration further increased to 1100 ppm. The reason can be explained from the difference of the possible reaction mechanisms between SO2 and active species (·OH, ·O and O3). As indicated in the previous research [28, 33], most SO2 is oxidized to HSO3 and SO3 by ·OH and ·O radicals which are the main radical species for oxidation due to the large rate constant compared with the other radical species such as O3. Therefore, the consumption of O3 by the reaction with SO2 is very minor. Additional, Hg0 and O3 ((10.5 ± 0.65) × 10−19 cm3 molecules−1 s−1) [30] reveal a relatively higher reaction rate constant than that of SO2 and O3 (2.7 × 10−23 cm3 molecules−1 s−1) [34]. Therefore, it has been clearly demonstrated that SO2 shows little impact on Hg0 oxidation.
The Mercury Mass Balance and Analysis of the Mercury Species Deposited on the Reactor Surface
The evolution of Hg0, Hg2+, and total Hg concentrations was shown in Fig. 9. With an increase of the SED, Hg0 concentration exhibited a dramatic decrease from 100 to 1.6 μg m−3, while the concentration of Hg2+ increased from 0 to 96.1 μg m−3, and then the total Hg concentration slightly decreased from 100 to 97.7 μg m−3 due to the reason that some mercury species in form of yellow deposits were accumulated on the internal surface of the reactor, presumably from the deposition of HgO formed through the oxidation of Hg0.
Energy dispersive spectroscopy (EDS) was used to determine the deposited mercury species elements and the measurement result was shown in Fig. 10. No Hg peak was detected at the blank sample and an Hg peak was detected for the inner surface of the reactor. Surface elemental composition of deposited mercury species in wt% and at.% on the inner surface of the reactor were illustrated in Table 3. For the deposited mercury species, after excluding the composition of SiO2, the at.% of O and Hg on the surface was observed to be approximately 36.71 and 34.64 %, implying that Hg/O atomic ratio (1.05) of the sample was obtained. The results indicated that the deposited mercury species predominantly existed in the form of HgO.
Conclusions
The application of SDBD for the oxidation of Hg0 in coal-fired flue gas was investigated in this study. High oxidation efficiency and energy yield of SDBD was obtained, which indicated that SDBD could be an alternative to other conventional technologies for efficient oxidation of Hg0. The investigation of contributions of active species to Hg0 oxidation indicated that O3 played a more important role during the treatment process. The deposited mercury species was monitored by EDS. Identified products were HgO.
References
Pavlish JH, Sondreal EA, Mann MD, Olson ES, Galbreath KC, Laudal DL, Benson SA (2003) Fuel Process Technol 82:89–165
Wu Y, Wang SX, Streets DG, Hao JM, Chan M, Jiang JK (2006) Environ Sci Technol 40:5312–5318
Kilgore JD, Sedman CB, Srivastava RK, Ryan JV, Lee CW, Thorneloe SA (2002) U.S. Government Printing Office Washington, DC
Wang YJ, Duan YF, Yang LG, Zhao CS, Shen XL, Zhang MY, Zhu YQ, Chen CH (2009) Fuel Process Technol 90:643–651
Scala F, Clack HL (2008) J Hazard Mater 152:616–623
Korpiel JA, Vidic RD (1997) Environ Sci Technol 31:2319–2325
Blanco MB, Bejan I, Barnes I, Wiesen P, Teruel AM (2012) Environ Sci Technol 46:8817–8825
Vandenbroucke AM, Morent R, Geyter ND, Leys C (2011) J Hazard Mater 195:30–54
Shang KF, Wu Y, Li J, Li GF, Li D, Wang NH (2006) Plasma Chem Plasma Process 26:443–454
Gutsol K, Nunnally T, Rabinovich A, Fridman A, Starikovskiy A, Gutsol A, Kemoun A (2012) Int J Hydrogen Energy 37:1335–1347
Wang HC, Li D, Wu Y, Li J, Li GF (2009) Journal of Electrostat 67:547–553
Pao CH, Chang SH, Chi KH, Chang MB (2010) J Hazard Mater 182:246–251
Byun Y, Ko KB, Cho M, Namkung W, Shin DN, Koh DJ, Kim KT (2008) Chemosphere 72:652–658
Ko KB, Byun Y, Cho M, Namkung W, Shin DN, Koh DJ, Kim KT (2008) Chemosphere 71:1674–1682
Chen Z, Mannava DP, Mathur VK (2006) Ind Eng Chem Res 45:6050–6055
Xu F, Luo Z, Cao W, Wang P, Wei B, Gao X, Fang MX, Cen KF (2009) J Environ Sci 21:328–332
Yang HM, Liu H, Wu H, Wang M (2012) Plasma Chem Plasma Process 32:969–977
Malik MA, Kolb JF, Sun Y, Schoenbach KH (2011) J Hazard Mater 197:220–228
Oda T, Yamashita R, Takahashi T, Masuda S (1996) IEEE Trans Ind Appl 32:118–124
Ogata A, Kim HH, Shigeru F, Kushiyama S, Mizuno K (2004) Appl Catal B Environ 53:175–180
Oh SM, Kim HH, Ogata A, Hisahiro E, Shigeru F, Park DW (2005) Catal Lett 99:101–104
Masuda S, Hosokawa S, Tu X, Wang Z (1995) J Electrost 34(415):438
EPA. ASTMD6784202 (1999) Washington DC, EPA
Birdsall CM, Jenkins AC, Spadinger E (1952) Anal Chem 24:662–664
Byun Y, Koh DJ, Shin DN, Cho M, Namkung W (2011) Chemosphere 84:1285–1289
Wang MY, Zhu TL, Luo HJ, Wang H, Fan WY (2011) Ind Eng Chem Res 50:5914–5919
Seethamsetty S, Dhali SK, Dave B (2001) Appl Phys Lett 79:4298–4300
Ono R, Oda T (2003) J Appl Phys 93:5876–5882
Hilda MS, Marquidia PP, Joel OPS, Carlos ETR, Juan ADG (2007) IEEE Trans Plasma Sci 35:1533–1540
Rutter AP, Shakya KM, Lehr R, Schauer JJ, Griffin RJ (2012) Atmospheric Environ 59:86–92
Wang ZH, Jiang SD, Zhu YQ, Zhou JS, Zhou JH, Li ZS, Cen KF (2010) Fuel Process Technol 91:1395–1400
Ko KB, Byun Y, Cho M, Namkung W, Hamilton IP, Shin DN, Koh DJ, Kim KT (2008) Main Group Chem 7:191–204
Ko KB, Byun Y, Cho M, Namkung W, Hamilton IP, Shin DN, Koh DJ, Kim KT (2008) Appl. Phys. Lett. 92: 251503.1-251503.3.32
Atkinsonl R, Baulch DL, Cox RA, Crowley JN, Hampson RF, Hynes RG, Jenkin ME, Rossi MJ, Troe J (2004) Atmos Chem Phys 4:1461–1738
Acknowledgments
The authors thank the National Natural Science Foundation, P.R. China (Project No. 51177007) and the Ministry of Science and Technology, P.R. China (Project No. 2009AA064101-4).
Author information
Authors and Affiliations
Corresponding author
Rights and permissions
Open Access This article is distributed under the terms of the Creative Commons Attribution License which permits any use, distribution, and reproduction in any medium, provided the original author(s) and the source are credited.
About this article
Cite this article
An, J.T., Shang, K.F., Lu, N. et al. Oxidation of Elemental Mercury by Active Species Generated From a Surface Dielectric Barrier Discharge Plasma Reactor. Plasma Chem Plasma Process 34, 217–228 (2014). https://doi.org/10.1007/s11090-013-9496-y
Received:
Accepted:
Published:
Issue Date:
DOI: https://doi.org/10.1007/s11090-013-9496-y