Abstract
This paper presents the development of an analytical model of steel–concrete partially composite beams subjected to fire. The model includes consideration of temperature dependent material properties, temperature dependent interface slip between concrete and steel, non-uniform temperature distributions throughout the cross-section and the effect of different rates of thermal expansion at the concrete–steel interface. Model predictions showed good agreement with the results of fire tests on two composite beams reported in an earlier companion paper as well as with limited experimental data published in literature. An extensive parametric study was undertaken by using the proposed model. Parameters considered in this study included geometric dimensions of the composite beam, material grades of steel and concrete, shear connection ratio, reinforcing steel ratio in the concrete slab, and load level on the beam. The parametric study clearly shows that shear connection ratio and load level significantly influence the fire performance of partially composite beams. The critical temperatures with shear connection ratio of 50%, 75% and 100% are 645°C, 602°C and 548°C, respectively, under load level of 0.6. The critical temperatures under load ratio of 0.5, 0.6 and 0.7 are 468°C, 553°C and 633°C respectively, with a shear connection ratio of 50%.













Similar content being viewed by others
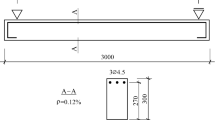
Abbreviations
- \( \sigma_{c,T} \) :
-
Stress of concrete at elevated temperature
- \( f_{c,T} \) :
-
Ultimate stress of concrete at elevated temperature
- \( \varepsilon_{c,T} \) :
-
Strain of concrete at elevated temperature
- \( \varepsilon_{c1,T} \) :
-
Strain at the ultimate stress of concrete at elevated temperature
- \( \varepsilon_{cu1,T} \) :
-
Ultimate strain of concrete at elevated temperature
- \( E_{c,T} \) :
-
Elastic modulus of concrete at elevated temperature
- \( E_{c} \) :
-
Elastic modulus of concrete at room temperature
- \( T_{c} \) :
-
Temperature of concrete
- \( \sigma_{s,T} \) :
-
Stress of steel at elevated temperature
- \( \varepsilon_{s} \) :
-
Strain of steel
- \( f_{p,T} \) :
-
Proportional limit of steel at elevated temperature
- \( f_{y,T} \) :
-
Yield stress of steel at elevated temperature
- \( E_{s,T} \) :
-
Elastic modulus of steel at elevated temperature
- \( \varepsilon_{y,T} \) :
-
Strain of steel at elevated temperature
- \( \varepsilon_{p,T} \) :
-
Strain at the proportional limit
- \( \varepsilon_{t,T} \) :
-
Limiting strain for yield stress
- \( \varepsilon_{u,T} \) :
-
Ultimate strain of steel at elevated temperature
- \( V_{T} \) :
-
Shear load on the stud at elevated temperatures
- \( V_{u} \) :
-
Shear resistance of the stud at room temperatures
- \( m \) :
-
Material dependant parameters of shear stud
- \( n \) :
-
Material dependant parameters of shear stud
- \( s \) :
-
Slip of the stud at elevated temperatures
- \( s_{u} \) :
-
Ultimate slip of the stud at elevated temperatures
- \( V_{\hbox{max} } \) :
-
Maximum shear force of stud
- \( s_{\hbox{max} } \) :
-
Maximum slip of stud
- \( V_{\hbox{min} } \) :
-
Minimum shear force of stud
- \( s_{\hbox{min} } \) :
-
Minimum slip of stud
- \( V_{j} \) :
-
Shear force on the shear stud j
- \( M_{c} \) :
-
Interior bending moment of concrete slab
- \( M_{s} \) :
-
Interior bending moment of steel beam
- \( h_{c} \) :
-
Thickness of concrete slab
- \( h_{s} \) :
-
Height of steel beam
- \( \varphi_{s,T} \) :
-
Curvature of steel beam at elevated temperature
- \( \varphi_{c,T} \) :
-
Curvature of concrete slab at elevated temperature
- \( \varepsilon_{ct,T} \) :
-
Concrete strain at the top boundary of slab
- \( \gamma \) :
-
Relative height of compressive area of concrete slab
- \( \varphi_{c,th} \) :
-
Curvature of concrete slab results by non-uniform temperature
- \( \varepsilon_{{s{\text{t}},T}} \) :
-
Steel strain at top boundary of steel beam
- \( \varepsilon_{cb,T} \) :
-
Concrete strain at bottom boundary of slab
- \( \varepsilon_{th} \) :
-
Difference of thermal strain between steel and concrete
- \( \varepsilon_{sd,T} \) :
-
Steel strain at bottom boundary of steel beam
- \( \alpha_{s} \) :
-
Thermal expansion coefficient of steel
- \( \alpha_{c} \) :
-
Thermal expansion coefficient of concrete
- \( T_{s,tf} \) :
-
Temperature of top flange of steel beam
- \( T_{c,b} \) :
-
Temperature of concrete slab at the bottom boundary
- \( A_{s} \) :
-
Sectional area of steel beam
- \( \varphi_{s,th} \) :
-
Thermal curvature of steel beam result by non-uniform temperature
- R :
-
Load ratio of composite beam
- η :
-
Shear connection ratio of composite beam
- α :
-
Enforcing steel ratio in concrete slab
- Q :
-
Grade of steel
- C :
-
Grade of concrete
- \( b_{\text{eff}} \) :
-
Effective width of concrete slab in composite beam
References
Ranzi G, Bradford MA (2007) Composite beams with both longitudinal and transverse partial interaction subjected to elevated temperatures. Eng Struct 29:2737–2750
Kwon G, Engelhardt MD, Klingner RE (2011) Experimental behavior of bridge beams retrofitted with postinstalled shear connectors. J Bridge Eng 16 (4):536–545
EN 1994-1-2 (2006) Eurocode 4: design of composite steel and concrete structures-part 1–2: general rules—structural fire design. European Committee for Standardization, Brussels
British Standards Institution (1990) BS 5950: Part 3, Section 3.1. Code of practice for design of simple and continuous composite beams. London
CECS200: 2006 (2006) Technical Code for Fire safety of Steel Structure in Buildings, Chinese Planning Press, Beijing
Wang W, Engelhardt MD, Li GQ et al. (2016) Behavior of steel–concrete partially composite beams subjected to fire—Part 1:Experimental study. Fire Technol. doi: 10.1007/s10694-016-0618-y.
Loh HY, Uy B, Bradford MA (2004) The effects of partial shear connection in the hogging moment regions of composite beams Part II—analytical study. J Constr Steel Res 60(6):921–962
Santos HAFA, Silberschmidt VV (2014) Hybrid equilibrium finite element formulation for composite beams with partial interaction. Compos Struct 108(2):646–656
Benedetti A, Mangoni E (2007) Analytical prediction of composite beams response in fire situations. J Constr Steel Res 63(2):221–228
Hozjan T, Saje M, Srpcic S et al. (2011) Fire analysis of steel–concrete composite beam with interlayer slip. Comput Struct, 89(1–2):189–200
Li GQ, Wang WY (2013) A simplified approach for fire-resistance design of steel–concrete composite beams. Steel Compos Struct 14(3):295–312
Selden K L, Varma AH (2016) Flexural capacity of composite beams subjected to fire: fiber-based models and benchmarking. Fire Technol 52:995–1014
Wu DY, Zhang M, Ling ZB (2010) Mechanics property analysis of steel–concrete composite beams based on relative interface slip. J East China Jiaotong Univ 21(6):27–35
Chen LZ (2014) The Structural Behavior of Composite Beams in Fire Considering Interface Slip and Uplift Effects. Ph.D. thesis, Tongji University, China
ENV 1992-1-2 (2004) Eurocode 2: design of concrete structures, Part1-2: general rules-structural fire design, European Committee for Standardization, Brussels
Guo ZH, Li W (1993) Deformation testing and constitutive relationship of concrete under different stress-temperature paths. J Civil Eng 26(5):58–69
ENV 1993-1-2 (2006) Eurocode 3: design of steel structures, Part1-2: general rules-structural fire design. European Committee for Standardization, Brussels
Mirza O, Uy B (2009) Behavior of headed stud shear connectors for composite steel–concrete beams at elevated temperatures. J Constr Steel Res 65(3):662–674
Wang H (2004) Experimental and theoretical study on external prestressed steel concrete composite beam. Master thesis, Tongji University, China
Zhang SZ (1997) A study on the behavior of stud-connector under cyclic loading. J Harbin Inst Archit Eng 30(5):187–192.
Benedetti A, Mangoni E (2007) Analytical prediction of composite beams response in fire situations. J Constr Steel Res 63: 221–228
Wainman DE, Kirby BR (1987) Compendium of UK Standard Fire Test Data, Unprotected Structural Steel-1, British Steel Corporation
MATLAB (2005) MATLAB user manual version 7.1 (R14). Math Works Incorporation, Natick
Acknowledgments
This material is based upon the work supported by the Open Research fund of State Key Laboratory for Disaster Reduction in Civil Engineering (Grant number:SLDRCE-MB-05). The assistance of the staff in Ferguson Structural Engineering Laboratory in the University of Texas at Austin, and the support of China Scholarship Council are also greatly acknowledged.
Author information
Authors and Affiliations
Corresponding author
Appendix 1: Details of Composite Beam Model
Appendix 1: Details of Composite Beam Model
1.1 Thermal Curvatures Calculation
Figure 14a shows the distribution of temperatures over the depth of the composite beam used in the model. As would be expected when a fire occurs underneath the beam, the steel beam has higher temperatures than the concrete. Because of the low thermal conductivity of concrete, a nonlinear variation of temperature with depth is expected in the concrete slab. Although steel and concrete have similar coefficients of thermal expansion, the different temperature fields within the two materials joined compositely lead to different rates of expansion and, consequently, to a complex stress state, particularly in the shear connectors.
If we consider the nonlinear distribution of temperature through the thickness of the slab, the free thermal strain of the concrete slab through the thickness should also be nonlinear, as is shown in Fig. 14b. The free thermal strain can be expressed as:
where, \( T_{0} \) is the room temperature.
However, the actual thermal strain through the thickness of the slab must also be linear according to the plane sections remain plane assumption. The thermal strains \( \varepsilon_{c1} \) and \( \varepsilon_{c2} \) are assumed to be the actual thermal strain at the top and bottom surface of the concrete slab, respectively. Therefore, the difference between the actual thermal strain and free thermal strain can be calculated as
Since the composite beam is assumed to be simply supported with a roller at one end, there is no external force and moment developed at the ends when the temperature rises. Based on equilibrium of axial force and bending moment in the concrete slab, as is shown in Eqs. (17)–(18), the values of \( \varepsilon_{c1} \) and \( \varepsilon_{c2} \) can be obtained.
Hence, the thermal curvature of the concrete slab can be computed as:
The procedure for calculating the thermal curvature of the concrete slab is summarized in the flow chart shown in Fig. 15. This is an iterative procedure that is assumed to converge if moment M or axial force N in the slab are smaller than 10−4.
As for the steel beam, in order to simplify the calculation procedure, the contribution of the web to the thermal curvature of the entire section is neglected and the thermal curvature (Fig. 14c) can then be expressed as:
where, \( T_{s,bf} \) is the temperature at the bottom flange of steel beam; \( T_{s,tf} \) is the temperature at the top flange of steel beam; \( h_{s} \) is the height of steel beam and \( h_{c} \) is the thickness of concrete slab.
1.2 Mechanical Analysis of Composite Beam
As explained in Sect. 4.1, the composite beam model assumes all shear force at the steel–concrete interface is resisted by the shear studs. Shear forces exist at the boundary of the steel beam and the slab, and these shear forces produce axial force and flexure in the steel beam and concrete slab separately. Figure 16 shows the shear forces at the boundary of the top flange of the steel beam and the bottom of the concrete slab. Figure 16b shows simplified free body diagrams. As shown in this figure, the axial force and bending moment in the concrete slab or steel beam between shear stud i and shear stud j can be calculated as:
where, \( V_{j} \) is the shear force on the shear stud j; \( M_{c} \) is the bending moment in the concrete slab and \( M_{s} \) is the bending moment in the steel beam.
1.3 Curvature and Strain Calculations
According to the second assumption explained in Sect. 4.1, plane sections remain plane within the concrete slab and within the steel beam, although there is a strain discontinuity at the interface. In addition, the concrete slab and steel beam have similar curvatures. The strain on the section can be represented as in Fig. 17a. The curvature of the slab can be expressed as:
where \( \varphi_{c,T} \) is the curvature of concrete slab at elevated temperature; \( \varepsilon_{ct,T} \) is the concrete strain at the top of the slab; \( \gamma \) is the relative height of compressive area of the concrete slab; and \( \varphi_{c,th} \) is the thermal curvature of the concrete slab induced` by non-uniform temperature expansion.
Therefore, the relative slip strain on the boundary of the steel beam and the concrete slab after taking the different thermal expansion into consideration can be written as
where
\( \varepsilon_{{s{\text{t}},T}} \) is the steel strain at the top boundary of the steel beam; \( \varepsilon_{{c{\text{b}},T}} \) is the concrete strain at the bottom of the slab; \( \varepsilon_{th} \) is the difference of thermal expansion strain between steel and concrete; \( \varepsilon_{sd,T} \) is the steel strain at the bottom of the steel beam; \( T_{s,tf} \) is the temperature of the top flange of the steel beam; and \( T_{c,b} \) is the temperature at the bottom of the concrete slab.
Substituting Eqs. (25)–(27) into (24), results in:
1.4 Mechanical Analysis of Concrete Slab
For the concrete slab, a coordinate system is defined, as shown in Fig. 17b. The strain for one position which is \( y^{{\prime }} \) away from the top of slab can be given as
Based on the strain–stress relationship of concrete at elevated temperatures given in Eurocode 2 [15], the stress in the concrete \( \sigma_{c} \left( {y^{{\prime }} } \right) \) can be obtained. Further, the axial force and bending moment in the concrete slab can be calculated as:
where \( b_{\text{eff}} \) is the effective width of the concrete slab.
1.5 Mechanical Analysis of Steel Beam
As for the steel beam, another coordinate system is defined, as shown in Fig. 17c. The axial force and bending moment in the steel beam are denoted as \( N_{\text{s}} \), \( M_{s} \), respectively. Since it assumed that no external axial force is applied on the composite beam, \( N_{\text{s}} \) can be calculated as:
The axial strain in the steel beam generated by axial force is:
where \( A_{s} \) is cross sectional area of steel beam.
The curvature of the steel beam after taking the non-uniform thermal expansion into consideration can be expressed as
where \( \varphi_{s,T} \) is the mechanical curvature of the steel beam at elevated temperature; and \( \varphi_{s,th} \) is the thermal curvature of the steel beam.
The strains at the top and bottom of the steel beam induced by bending moment are denoted as \( \varepsilon_{st,T} \) \( \varepsilon_{sb,T} \), respectively, and their corresponding expressions are:
Therefore, the total strain at the top of the steel beam is the sum of axial strain and bending strain, and can be written as
The strain for a fiber that is \( y^{{{\prime \prime }}} \) away from the top of the steel beam can be given as:
Based on the strain–stress relationship of steel at elevated temperatures given in Ref. [18], the stress in the steel beam \( \sigma_{s} \left( {y^{{{\prime \prime }}} } \right) \) can be obtained. Further, the axial force and bending moment in the steel beam can be calculated as:
where \( b_{s} \) is the width of the steel beam.
The procedure for the strain calculation in the concrete slab and steel beam is summarized in the flow chart shown in Fig. 18. Using this procedure, the strain distribution in the composite beam can be obtained by equilibrium between internal and applied external forces on the composite beam.
1.6 Deflection and Slip Calculation
A computer program using the software package MATLAB [23] was developed based on the analytical model presented above. First, thermal strains in the concrete slab were computed according to flow chart in Fig. 15. Next, mechanical strains in the steel beam and concrete slab were computed according to flow chart in Fig. 18, and then the deflection and slip in the composite beam can be computed based on the flow chart shown in Fig. 19. Finally, the defection-temperature curve and slip-temperature curve can be plotted. From the curves, the critical temperature in the bottom flange of the steel beam can be determined.
Rights and permissions
About this article
Cite this article
Wang, W., Wang, K., Engelhardt, M.D. et al. Behavior of Steel–Concrete Partially Composite Beams Subjected to Fire—Part 2: Analytical Study. Fire Technol 53, 1147–1170 (2017). https://doi.org/10.1007/s10694-016-0624-0
Received:
Accepted:
Published:
Issue Date:
DOI: https://doi.org/10.1007/s10694-016-0624-0