Abstract
The micro pattern machining on the surface of a wide mold is not easily simulated and optimized using conventional methods. This paper represents the micro pattern cutting simulation software. The software simulates micro pattern grooving in 3D geometry, predicts the cutting force and optimizes the time factor in the roughing stage. The v-groove for prism and pyramid patterns and the rectangular groove for rectangular and pillar patterns are simulated. The code of this program is built using visual C++ and OpenGL.
Similar content being viewed by others
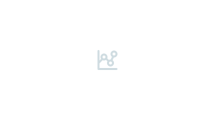
Abbreviations
- Fc :
-
cutting force
- K:
-
specific cutting energy
- A:
-
cutting area
- C:
-
experimental constant
- n:
-
experimental constant
- t:
-
chip thickness
- di :
-
cutting depth at ith step
- a:
-
angle of diamond tool and pattern
- p:
-
pitch between each pattern
- w:
-
width of rectangular tool and pattern
- Fn :
-
the maximum permissible cutting force
- dpi :
-
depth of pyramid pattern
- dri :
-
depth of pillar pattern
- dn :
-
final cutting depth
- δdi :
-
relative cutting depth
- Fi :
-
ith cutting force
- Favg :
-
average cutting force
- δdavg :
-
relative cutting depth’s average
- m:
-
number of cutting cycle
References
Hong, S. M., Je, T. J., Lee, D. J. and Lee, J. C., “Micro machining characteristics of V-shaped single crystal diamond tool with ductile workpiece,” Journal of the Korean Society of Manufacturing Process Engineers, Vol. 4, No. 4, pp. 28–33, 2005.
Arcona, C. and Dow, T. A., “An empirical tool force model for precision machining,” Journal of Manufacturing Science and Engineering, Transaction of the ASME, Vol. 120, No. 4, pp. 700–707, 1998.
Cheng, P. J., Tsay, J. T. and Lin, S. C., “A Study on instantaneous cutting force coefficients in face milling,” International Journal of Machine Tools & Manufacture, Vol. 37, No. 10, pp. 1393–1408, 1997.
Yoon, Y. S. and Lee, S. J., “Cutting force prediction in single point diamond turning,” Transactions of the KSME A, Vol. 17, No. 6, pp. 1456–1464, 1992.
Chae, J., Park, S. S. and Freiheit, T., “Investigation of microcutting operation,” International Journal of Machine Tools & Manufacture, Vol. 46, No. 3–4, pp. 313–332, 2006.
Lai, X., Li, H., Li, C. F., Lin, Z. Q. and Ni, J., “Modeling and analysis of micro scale milling considering size effect, micro cutter edge radius and minimum chip thickness,” International Journal of Machine Tools & Manufacture, Vol. 48, No. 1, pp. 1–14, 2008.
Ng, C. K., Melkote, S. N., Rahman, M. and Kumar, A. S., “Experimental study of micro- and nano-scale cutting of aluminum 7075-T6,” International Journal of Machine Tools & Manufacture, Vol. 46, No. 9, pp. 929–936, 2006.
Kim, J. D. and Kim, D. S., “Theoretical analysis of microcutting characteristics in ultra-precision machining,” Journal of material Processing Technology, Vol. 49, No. 3, pp. 387–398, 1995.
Wu, H. Y., Lee, W. B., Cheung, C. F., To, S. and Chen, Y. P., “Computer simulation of single-point diamond turning using finite element method,” Journal of Materials Processing Technology, Vol. 167, No. 2–3, pp. 549–554, 2005.
Strenkowski, J. S., Shih, A. J. and Lin, J. C., “An analytical finite element model for predicting three-dimensional tool forces and chip flow,” International Journal of Machine Tools & Manufacture, Vol. 42, No. 6, pp. 723–731, 2002.
Maekwa, K. and Itoh, A., “Friction and tool wear in nano-scale machining-a molecular dynamics approach,” Wear, Vol. 188, No. 1–2, pp. 115–122, 1995.
Aly, M. F., Ng, E., Veldhuis, S. C. and Elbestawi, M. A., “Prediction of cutting forces in the micro-machining of silicon using a hybrid molecular dynamic-finite element analysis force model,” International Journal of Machine Tools & Manufacture, Vol. 46, No. 14, pp. 1727–1739, 2006.
Lin, Z. C. and Huang, J. C., “The influence of different cutting speeds on the cutting force and strain-stress behaviors of single crystal copper during nano-scale orthogonal cutting,” Journal of Materials Processing Technology, Vol. 201, No. 1–3, pp. 477–428, 2008.
Author information
Authors and Affiliations
Corresponding author
Rights and permissions
About this article
Cite this article
Lee, JM., Je, TJ., Choi, DS. et al. Micro grooving simulation and optimization in the roughing stage. Int. J. Precis. Eng. Manuf. 11, 361–368 (2010). https://doi.org/10.1007/s12541-010-0041-0
Received:
Accepted:
Published:
Issue Date:
DOI: https://doi.org/10.1007/s12541-010-0041-0