Abstract
Based on anti-wear theory of soil animals, the samples of impregnated diamond bit with bionic self-regenerated non-smooth surface were designed and fabricated. Such a bionic surface was characterized by concave-shape units of different scales that continuously maintained their shape and function during the whole working process. Abrasion tests were carried out to investigate the performance of samples. Results showed that the bionic samples exhibit excellent wear resistance and drilling performance under the action of bionic self-regenerated units, especially those with units of 2 mm–3 mm diameter. The particle- trapping mechanism coming from the self-regenerated concaves and the lubricating mechanism coming from the continuously self-supplying of solid lubricant are important reasons for reducing or even avoiding the severe abrasions. The improved drilling performance of bionic samples derives from, on the one hand, the back edge of bionic unit that contributes to exposing new diamond and supplying additional shear stresses to increase the cutting ability, on the other hand, the enhanced load per unit area due to the decreased contact area at the frictional interface. The relationship between the wear behavior and the scale of bionic unit was revealed. The unit of smaller scale on the bionic samples can enhance the shear stress level. Further reducing the scale to a contain extent will diminish the wear resistance of sample. While increasing the scale can lead to the poor lubricating effect.
Similar content being viewed by others
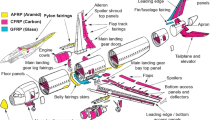
References
Lyons K D, Honeygan S, Mroz T. NETL extreme drilling laboratory studies high pressure high temperature drilling phenomena. Journal of Energy Resources Technology, 2007, 130, 791–796.
Sun Y H, Liu D J, Gao K, Xie X B, Ma Y L, Gao J H. Development of coupling bionics impregnated diamond bit. Journal of Jilin University (Engineering and Technology Edition, 2013, 43, 1566–1573 (in Chinese)
Novikov N V, Bogatyreva G P, Bogdanov R K, Il’nitskaya G D, Isonkin A M. The influence of strength characteristics of diamond grits on drilling tool performance. Journal of Superhard Materials, 2009, 31, 413–417.
Tian X F, Tian S F. The wear mechanisms of impregnated diamond bits. Wear, 1994, 177, 81–91.
Moneim M E A, Abdou S. Comments on the wear mechanisms of impregnated diamond bits. Wear, 1997, 205, 228–230.
Umanskii V P, Bugaev A A, Evdokimov V A, Brodnikovskii N P, Naidich Y V. Effect of the adhesion, concentration, size, and quality of diamond grains on the strength and wear resistance of samples modeling an impregnated layer of diamond crown bits. Powder Metallurgy and Metal Ceramics, 2011, 50, 557–563.
Pan B S, Fang X H, Niu M Y. Study on friction and wear properties of self-lubricating impregnated diamond bit cutters. Solid State Phenomena, 2011, 75, 136–139.
Li W S, Zhang J, Wang S C, Dong H F, Li Y M, Liu Y. Characterizations and mechanical properties of impregnated diamond segment using Cu-Fe-Co metal matrix. Rare Metals, 2012, 31, 81–87.
Tönshoff H K, Hillmann-Apmann H, Asche J. Diamond tools in stone and civil engineering industry: Cutting principles, wear and applications. Diamond and Related Materials, 2002, 250, 736–741.
Tan S C, Fang X H, Yang K H, Duan L C. A new composite impregnated diamond bit for extra-hard, compact, and nonabrasive rock formation. International Journal of Refractory Metals and Hard Materials, 2014, 43, 186–192.
Karakus M, Perez S. Acoustic emission analysis for rock-bit interactions in impregnated diamond core drilling. International Journal of Rock Mechanics and Mining Sciences, 2014, 68, 36–43.
Ball P. Life’s lessons in design. Nature, 2001, 409, 413–416.
Rao R P. Biomimetics. Sadhana-Academy Proceedings in Engineerings Sciences, 2003, 28, 657–676.
Vincent J F V. Biomimetics — A review. Proceedings of the Institution of Mechanical Engineers Part H-Journal of Engineering in Medicine, 2009, 223, 919–939.
Ren L Q, Li J Q, Chen B C. Unsmoothed surface on reducing resistance by bionics. Chinese Science Bulletin, 1995, 10, 77–80.
Ren L Q, Han Z W, Li J Q, Tong J. Effects of nonsmooth characteristics on bionic bulldozer blades in resistance reduction against soil. Journal of Terramechanics, 2002, 39, 221–230.
Ren L Q, Han Z W, Li J Q, Tong J. Experimental investigation of bionic rough curved soil cutting blade surface to reduce soil adhesion and friction. Soil & Tillage Research, 2006, 85, 1–12.
Zhang Z H, Ren L Q, Zhou H, Tong X. Biomimetic coupling effect of non-smooth mechanical property and microstructural features on thermal fatigue behavior of medium carbonsteel. Chinese Science Bulletin, 2009, 54, 584–591.
Ren L Q. Progress in the bionic study on anti-adhesion and resistance reduction of terrain machines. Science in China Series E-Technological Sciences, 2009, 52, 273–284.
Ren L Q, Liang Y H. Biological couplings: Classification and characteristic rules. Science in China Series E-Technological Sciences, 2009, 52, 2791–2800.
Ren L Q, Liang Y H. Biological couplings: Function, characteristics and implementation mode. Science China Technological Sciences, 2010, 53, 379–387.
Ren L Q, Liang Y H. Preliminary studies on the basic factors of bionics. Science China Technological Sciences, 2014, 57, 520–530.
Ren L Q, Tong J, Li J Q, Chen B C. Soil adhesion and biomimetics of soil-engaging components: A review. Journal of Agricultural Engineering Research, 2001, 79, 239–263.
Li J Q, Kou B X, Liu G M, Fan W F, Liu L L. Resistance reduction by bionic coupling of the earthworm lubrication function. Science China Technological Sciences, 2010, 53, 2989–2995.
Fratzl P. Biomimetic materials research: what can we really learn from nature’s structural materials? Journal of the Royal Society Interface, 2007, 4, 637–642.
Wang Z Z, Zhang Z H, Sun Y H, Gao K, Liang Y H, Li X J, Ren L Q. Wear behavior of bionic impregnated diamond bits. Tribology International, 2016, 94, 217–222.
Zhang Z H, Zhou H, Ren L Q, Tong X, Shan H Y, Liu L. Effect of units in different sizes on thermal fatigue behavior of 3Cr2W8V die steel with biomimetic non-smooth surface. International Journal of Fatigue, 2009, 31, 468–475.
Shi B R, Pei X H, Wei S B, Li Y L, Shao T M. Application of bionic non-smooth theory in solid expandable tubular technology. Proceedings of the 4th International Conference of Bionic Engineering (ICBE 2013), Nanjing, China, 2013, 476–481.
Greiner C, Schafer M. Bio-inspired scale-like surface textures and their tribological properties. Bioinspiration & Biomimetics, 2015, 10, 044001.
Ren L Q, Deng S Q, Wang J C, Han Z W. Design principles of the non-smooth surface of bionic plow moldboard. Journal of Bionic Engineering, 2004, 1, 9–19.
Jacob K T. Determination of the Gibbs energy of diamond using a solid state cell. Solid State Communications, 1995, 94, 763–765.
Zhou L, Dong G J, Zhou M. Investigation on frictional wear of single crystal diamond against ferrous metals. International Journal of Refractory Metals & Hard Materials, 2013, 41, 174–179.
Author information
Authors and Affiliations
Corresponding authors
Rights and permissions
About this article
Cite this article
Wang, Z., Gao, K., Sun, Y. et al. Effects of bionic units in different scales on the wear behavior of bionic impregnated diamond bits. J Bionic Eng 13, 659–668 (2016). https://doi.org/10.1016/S1672-6529(16)60337-2
Published:
Issue Date:
DOI: https://doi.org/10.1016/S1672-6529(16)60337-2