Abstract
Dual-rotation friction stir welding (DR-FSW) is a new variant technique of friction stir welding. By adopting different rotation speeds for the pin and shoulder, the temperature gradient can be adjusted to help decrease overheat and the dissolution of the strengthening precipitates and produces good joints for some cases, such as thick plates. In this study, by thermal-mechanical coupling method, with the help of finite element software—DEFORM-3D, the temperature field of workpieces in DR-FSW for an 80-mm-thick 5A06 aluminum alloy was simulated, and the temperature gradients at different rotation speed ratios were calculated and analyzed. Better process parameters could be concluded using optimization. In our simulation, the rotation ratio of 200 rpm for the shoulder and 400 rpm for the pin in the first group achieved the gentlest temperature gradient in thickness direction with a temperature difference between the upper and lower surfaces of less than 30 °C. The study represents a practical reference for choosing process parameters in the actual DR-FSW process.
Similar content being viewed by others
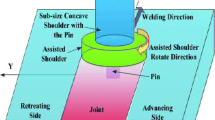
References
Nandan R, Debroy T, Bhadeshia HKDH (2008) Recent advances in friction-stir welding-process, weldment structure and properties. Prog Mater Sci 53:980–1023
He XC, Gu FS, Ball A (2014) A review of numerical analysis of friction stir welding. Prog Mater Sci 65:1–66
Thomas WM, Nicholas ED, Needham JC, Murch MG, Temple-Smith P, Dawes CJ (1991) Friction stir butt welding. International Patent Application No. PCT/GB92/02203
Mishra RS, Ma ZY (2005) Friction stir welding and processing. Mater Sci Eng R 50:1–78
Starke EA, Staley JT (1996) Application of modern aluminum alloys to aircraft. Prog Aerosp Sci 32:131–172
Heinz A, Haszler A, Keidel C, Moldenhauer S, Benedictus R, Miller WS (2000) Recent development in aluminium alloys for aerospace applications. Mater Sci Eng A 280:102–107
Longhurst WR, Cox CD, Gibson BT, Cook GE, Strauss AM, Wilbur IC, Osborne BE (2016) Development of friction stir welding technologies for in-space manufacturing. Int J Adv Manuf Technol. doi:10.1007/s00170-016-9362-1
Eslami S, Tavares PJ, Moreira PMGP (2016) Friction stir welding tooling for polymers: review and prospects. Int J Adv Manuf Technol. doi:10.1007/s00170-016-9205-0
Papahn H, Bahemmat P, Haghpanahi M, Sommitsch C (2015) Study on governing parameters of thermal history during underwater friction stir welding. Int J Adv Manuf Technol 78:1101–1111
Tomohiko G, Hiroaki S, Daisuke T, Hideaki S, Takeshi Y, Hidenori H (2005) Highly reliable tank structure of H-IIB launch vehicle. Mitsubishi Heavy Industries Ltd. Technical Review 42:1–4 http://www.mhi.co.jp/technology/review/pdf/e425/e425234.pdf
Guan Q, Luan GH (2008) The current status and development of FSW. http://info.mt.hc360.com/2008/10/09093845905.shtml
Sakano R, Murakami K, Yamashita K, Hyoe T, Fujimoto M, Inuzuka M, Nagao Y, Kashiki H (2001) Development of spot FSW robot system for automobile body members. In: Proceedings of the 3rd International Symposium of Friction Stir Welding, Kobe
Chen YC, Gholinia A, Prangnell PB (2012) Interface structure and bonding in abrasion circle friction stir spot welding: a novel approach for rapid welding aluminium alloy to steel automotive sheet. Mater Chem Phys 134:459–463
Luan GH, Ji YJ, Dong CL, Ma XS (2006) Microstructure of LY12 aluminium alloy welded joint of friction plug welding. Trans China Weld Inst 27:1–3
ZhaoYH LJD, Zhang LN, Sun ZS, Wang GQ (2010) Study on friction plug welding of 2014 aluminum alloy FSW joint. J Aeronaut Mater 30:41–46
Chen H , Liu JD, Zhang LN, Zhang YK, Du YF (2007) Study on friction plug welding of aluminum alloy. In: International Astronautical Federation - 58th International Astronautical Congress, Hyderabad
Thomas WM, Norris IM, Staines DG, Watts, ER (2005) Friction stir welding—process developments and variant techniques. In: The SME Summit 2005, Oconomowoc, Milwaukee
Schmidt H, Hattel J, Wert J (2004) An analytical model for the heat generation in friction stir welding. Model Simul Mater Sci Eng 12:143–157
Neto DM, Neto P (2013) Numerical modeling of friction stir welding process: a literature review. Int J Adv Manuf Technol 65:115–126
Park SHC, Sato YS, Kokawa H (2003) Effect of micro-texture on fracture location in friction stir weld of Mg alloy AZ61 during tensile test. Scripta Mater 49:161–166
Sato YS, Kokawa H, Enomoto M, Jogan S (1999) Microstructural evolution of 6063 aluminum during friction-stir welding. Metall Mater Trans A 30:2429–2437
Oertelt G, Babu SS, David SA, Kenik EA (2001) Effect of thermal cycling on friction stir welds of 2195 aluminum alloy. Weld J 80:71–79
Shi L, Wu CS, Liu HJ (2015) The effect of the welding parameters and tool size on the thermal process and tool torque in reverse dual-rotation friction stir welding. Int J Mach Tools Manuf 91:1–11
Li JQ, Liu HJ (2013) Effects of welding speed on microstructures and mechanical properties of AA2219-T6 welded by the reverse dual-rotation friction stir welding. Int J Adv Manuf Technol 68:2071–2083
Li JQ, Liu HJ (2014) Optimization of welding parameters for the reverse dual-rotation friction stir welding of a high-strength aluminum alloy 2219-T6. Int J Adv Manuf Technol 76:1469–1478
Shi L, Wu CS, Liu HJ (2014a) Modeling the material flow and heat transfer in reverse dual-rotation friction stir welding. J Mater Eng Perform 23:2918–2929
Shi L, Wu CS, Liu HJ (2014b) Modeling material plastic flow and thermal field in reverse dual-rotation friction stir welding. Chin J Mech Eng 50:140–146
Shi L, Wu CS, Liu HJ (2014c) Numerical analysis of heat generation and temperature field in reverse dual-rotation friction stir welding. Int J Adv Manuf Technol 74:319–334
Liu XM, Yao JS, Cai Y, Meng H, Zou ZD (2013) Simulation on the temperature field of bobbin tool friction stir welding of AA 2014 aluminium alloy. Appl Mech Mater 433-435:2091–2095
Author information
Authors and Affiliations
Corresponding author
Rights and permissions
About this article
Cite this article
Liu, X.M., Zhang, X.M., Yao, J.S. et al. Optimization of rotation speed ratio in dual-rotation friction stir welding by finite element method. Int J Adv Manuf Technol 91, 2869–2874 (2017). https://doi.org/10.1007/s00170-017-0007-9
Received:
Accepted:
Published:
Issue Date:
DOI: https://doi.org/10.1007/s00170-017-0007-9