Abstract
For ensuring vehicle safety, the impact performance of wheels during wheel development must be ensured through a wheel impact test. However, manufacturing and testing a real wheel requires a significant time and money because developing an optimal wheel design requires numerous iterative processes to modify the wheel design and verify the safety performance. Accordingly, wheel impact tests have been replaced by computer simulations such as finite element analysis (FEA); however, it still incurs high computational costs for modeling and analysis, and requires FEA experts. In this study, we present an aluminum road wheel impact performance prediction model based on deep learning that replaces computationally expensive and time-consuming 3D FEA. For this purpose, 2D disk-view wheel image data, 3D wheel voxel data, and barrier mass values used for the wheel impact test were utilized as the inputs to predict the magnitude of the maximum von Mises stress, corresponding location, and the stress distribution of the 2D disk-view. The input data were first compressed into a latent space with a 3D convolutional variational autoencoder (cVAE) and 2D convolutional autoencoder (cAE). Subsequently, the fully connected layers were used to predict the impact performance, and a decoder was used to predict the stress distribution heatmap of the 2D disk-view. The proposed model can replace the impact test in the early wheel-development stage by predicting the impact performance in real-time and can be used without domain knowledge. The time required for the wheel development process can be reduced using this mechanism.
























Similar content being viewed by others
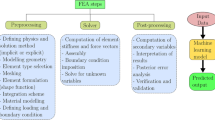
References
Ahmed E, Saint A, Shabayek AER, Cherenkova K, Das R, Gusev G, Aouada D, Ottersten B (2018) A survey on deep learning advances on different 3D data representations. arXiv preprint arXiv:1808.01462
Autodesk (2022) Retrieved from https://www.autodesk.com/products/fusion-360/
Bachmann R, Mizrahi D, Atanov A, Zamir A (2022) MultiMAE: Multi-modal Multi-task Masked Autoencoders. arXiv preprint arXiv:2204.01678
Bello SA, Yu S, Wang C, Adam JM, Li J (2020) Deep learning on 3D point clouds. Remote Sens 12:1729
Chang CL, Yang SH (2009) Simulation of wheel impact test using finite element method. Eng Failure Anal 16:1711–1719
Deng C, Qin C, Lu W (2020) Deep-Learning-Enabled Simulated Annealing for Topology Optimization. arXiv preprint arXiv:2002.01927
Essien A, Giannetti C (2020) A deep learning model for smart manufacturing using convolutional LSTM neural network autoencoders. IEEE Trans Ind Informat 16:6069–6078
Ganin Y, Lempitsky V (2015) Unsupervised domain adaptation by backpropagation. In: PMLR International Conference Machine Learning (pp 1180–1189)
Grigorescu S, Trasnea B, Cocias T, Macesanu G (2020) A survey of deep learning techniques for autonomous driving. J Field Robot 37:362–386
Gu Y, Zhang C, Golub MV (2022) Physics-informed neural networks for analysis of 2D thin-walled structures. Eng Anal Bound Elements 145:161–172
Häne C, Tulsiani S, Malik J (2017, October) Hierarchical surface prediction for 3d object reconstruction. In: 2017 IEEE International Conference 3D Vision (3DV) (pp 412–420)
Jang S, Yoo S, Kang N (2022) Generative design by reinforcement learning: enhancing the diversity of topology optimization designs. Comput Aided Des 146:103225
Khadilkar A, Wang J, Rai R (2019) Deep learning–based stress prediction for bottom-up SLA 3D printing process. Int J Adv Manufactur Technol 102:2555–2569
Kim S, Jwa M, Lee S, Park S, Kang N (2022) Deep learning-based inverse design for engineering systems: multidisciplinary design optimization of automotive brakes. Struct Multidisc Optim 65:323
Lee S, Kim H, Lieu QX, Lee J (2020) CNN-based image recognition for topology optimization. Knowl-Based Sys 108:105887
Liang L, Liu M, Martin C, Sun W (2018) A deep learning approach to estimate stress distribution: a fast and accurate surrogate of finite-element analysis. J R Soc Interface 15:20170844
Madani A, Bakhaty A, Kim J, Mubarak Y, Mofrad MR (2019) Bridging finite element and machine learning modeling: stress prediction of arterial walls in atherosclerosis. J Biomech Eng 141:25
Nie Z, Jiang H, Kara LB (2020) Stress field prediction in cantilevered structures using convolutional neural networks. J Comput Infor Sci Eng 20:011002
Oh S, Jung Y, Kim S, Lee I, Kang N (2019) Deep generative design: Integration of topology optimization and generative models. J Mech Design 141:89
Ostad-Ali-Askari K, Shayannejad M, Ghorbanizadeh-Kharazi H (2017) Artificial neural network for modeling nitrate pollution of groundwater in marginal area of Zayandeh-rood River, Isfahan. Iran KSCE J Civil Eng 21:134–140
Ostad-Ali-Askari K, Shayan M (2021) Subsurface drain spacing in the unsteady conditions by HYDRUS-3D and artificial neural networks. Arabian J Geosci 14:1–14
Qi CR, Su H, Mo K, Guibas LJ (2017) Pointnet: deep learning on point sets for 3d classification and segmentation. In: Proceeding of the IEEE Conference Computer Vision Pattern Recognition (pp 652–660)
Qian C, Ye W (2021) Accelerating gradient-based topology optimization design with dual-model artificial neural networks. Struct Multidisc Optim 63:1687–1707
Raissi M, Perdikaris P, Karniadakis GE (2019) Physics-informed neural networks: a deep learning framework for solving forward and inverse problems involving nonlinear partial differential equations. J Comput Phys 378:686–707
Raissi M, Yazdani A, Karniadakis GE (2020) Hidden fluid mechanics: learning velocity and pressure fields from flow visualizations. Science 367:1026–1030
Riegler G, Osman UA, Geiger A (2017) Octnet: Learning deep 3d representations at high resolutions. In: Proceeding of the IEEE Conference Computer Vision Pattern Recog (pp 3577–3586)
Shin S, Shin D, Kang N (2022) Topology optimization via machine learning and deep learning: A review. arXiv preprint arXiv:2210.10782
Tatarchenko M, Dosovitskiy A, Brox T (2017) Octree generating networks: Efficient convolutional architectures for high-resolution 3d outputs. In: Proceeding of the IEEE International Conference Computer Vision (pp 2088–2096)
Van der Maaten L, Hinton G (2008) Visualizing data using t-SNE. J Mach Learn Res 9:8
Yoo S, Kang N (2021) Explainable artificial intelligence for manufacturing cost estimation and machining feature visualization. Expert Syst Appl 183:115430
Yoo S, Lee S, Kim S, Hwang KH, Park JH, Kang N (2021) Integrating deep learning into CAD/CAE system: generative design and evaluation of 3D conceptual wheel. Struct Multidisc Optim 64:2725–2747
Zheng L, Kumar S, Kochmann DM (2021) Data-driven topology optimization of spinodoid metamaterials with seamlessly tunable anisotropy. Comput Methodsin Appl Mech Eng 383:113894
Acknowledgements
This work was supported by the Hyundai Motor Company, the National Research Foundation of Korea (2018R1A5A7025409), and the Ministry of Science and ICT of Korea (No. 2022-0-00969). Seungyeon Shin and Ah-hyeon Jin have contributed equally to this work.
Author information
Authors and Affiliations
Corresponding author
Ethics declarations
Conflict of interest
The authors declare that they have no known competing financial interests or personal relationships that could influence the work reported herein.
Replication of results
The code used in this study cannot be disclosed, as it is the property of the Hyundai Motor Company that funded this study.
Additional information
Responsible Editor: Lei Wang
Publisher's Note
Springer Nature remains neutral with regard to jurisdictional claims in published maps and institutional affiliations.
Rights and permissions
Springer Nature or its licensor (e.g. a society or other partner) holds exclusive rights to this article under a publishing agreement with the author(s) or other rightsholder(s); author self-archiving of the accepted manuscript version of this article is solely governed by the terms of such publishing agreement and applicable law.
About this article
Cite this article
Shin, S., Jin, Ah., Yoo, S. et al. Wheel impact test by deep learning: prediction of location and magnitude of maximum stress. Struct Multidisc Optim 66, 24 (2023). https://doi.org/10.1007/s00158-022-03485-6
Received:
Revised:
Accepted:
Published:
DOI: https://doi.org/10.1007/s00158-022-03485-6