Abstract
The innovation of advanced materials and their application to engineering structures can be related to their ease of fabricating defect-free parts. The identification of various energy sources has resulted in various new processing techniques in manufacturing and electromagnetic energy is one which offers promising qualities for high-velocity forming, welding, and compaction of metals. Bimetallic joint designs were proposed in automobiles to reduce the weight and to take advantage of properties of different metals in the same construction. Joining by fusion is impossible in certain cases due to huge differences in melting point, thermal conductivity, volumetric specific heat, and coefficient of thermal expansion. In the present study, magnetic-pulse welding of a Cu/Al joint and an ODS alloy is investigated. The formation of intermetallic phases and interface morphology is presented along with a quantitative analysis for temperature in the Al/Cu joint. Also, initial investigations on the application of electromagnetic energy for compaction of aluminum powders are reported.


















Similar content being viewed by others
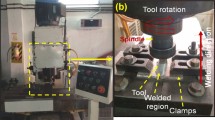
References
Murray JL (1990) Binarry Alloy Phase Diagrams. American Society for Metals
Akbari-Mousavi SAA, Barrett LM, Al-Hassanib STS (2008) Explosive welding of metal plates. J Mater Process Technol 202:224–239
Kochan A (2000) Magnetic pulse welding shows potential for automotive applications. Assem Autom 20(2):129–132
Shribman V (2001) Take advantage of the new magnetic pulse welding process. a welding review. Svetsaren Weld Rev 56(2–3):14–16
Brown WF, Bandas J, Olson NT (1978) Pulsed magnetic welding of breeder reactor fuel pin end closures. Weld J 57(6):22–26
Khrenov KK, Chudakov VA (1978) The formation of welded joints in the magnetic pulsed welding of cylindrical workpieces. Weld Prod (USSR) 25(9):19–20
Stern A, Aizenshtein M (2002) Bonding zone formation in magnetic pulse welds. Sci Technol Weld Join 7(4):339–342
Marya M, Marya S, Priem D (2009) Springer Handbook of Mechanical Engineering, volume 10, chapter Fundamentals of Magnetic Pulse Welding for the fabrication of dissimilar material structures, pages 723–732.
Aizawa T, Kashani M, Okagawa K (2005) Application of magnetic pulse welding for aluminum alloy and steel sheet joints. Welding in the World 49:212–222
Kore SD, Date PP, Kulkarni SV (2007) Effect of process parameters on electromagnetic impact welding of aluminium sheets. Int J Impact Eng 34:1327–1341
Zhang Y, Daehn G, Eplattenier PL, Suresh Babu S (2009) Experimental study and numerical simulation on magnetic pulse welding for pre-flanged aa6061-t6 and cu101 sheets. Proceedings of 8th International conference on Trends in Welding Research, pages 715–720
Zhang Y, Suresh Babu S, Daehn GS (2010) Interfacial ultra fine-grained structures on aluminium alloy 6061 joint and copper alloy 110 joint fabricated by magnetic pulse welding. J Mater Sci 45:4645–4651
Masumoto I, Tamaki K, Kojima M (1985) Electromagnetic welding of aluminum tube to aluminum or dissimilar metal cores (study on electromagnetic welding, report 1). Trans Japan Weld Soc 16(2):110–116
Marya M, Marya S, Priem D (2005) On the characteristics of electromagnetic welds between aluminum and other metals and alloys. Weld World 49:74–84
Wakeman DW (1954) American Chemical Society Monograph Series. Reynolds Publishing
Gorecki T and Michno Z 1983 Proc. Conf. `Dimeta 82', Tihany, Hungary (1982) (Diffusion and Defect Monograph Series no 7) ed F J Kedves and D L Beke (Switzerland: Trans. Tech. Publications) p 365
Hultgren R (1970) Selected Values of the Thermodynamic Properties of Binary Alloys. American Society for Metals
Allen WA, Mapes JM, Wilson W0 (1954) An effect produced by oblique impact of a cylinder on a thin target. J Appl Phys 25:675–676
Wantanabe M, Kumai S (2009) Interfacial morphology of magnetic pulse welded aluminum/aluminum and copper/copper lap joints. Mater Trans 50(2):286–292
Ben-Artz A, Stern A, Frage N, Shriban V, Sadot O (2010) Wave formation mechanism in magnetic pulse welding. Int J Impact Weld 37(4):397–404
Komelkov VS (2010) A technology for high-pulsed currents and magnetic fields. Atomizdat
Inkson BJ, Threadgill PL (1998) Friction welding of FeAl40 grade 3 ODS alloy. Mater Sci Eng, A 258(1–2):313–318
Mathon MH, Klosek V, de Carlan Y, Forest L (2009) Study of PM2000 microstructure evolution following FSW process. Journal of Nuclear Materials, 386–388:475–478. Fusion Reactor Materials, Proceedings of the Thirteenth International Conference on Fusion Reactor Materials
Mamalis AG, Manolakos DE, Kladas AG, Koumoutsos AK (2004) Electromagnetic forming and powder processing: trends and developments. Appl Mech Rev 57(4):299–324
Kononenko VV, Levina DA, Raichenko AI (1975) Electromagnetic compression of a conducting tube filled with powder. Acad Sci USSR 145:30–33
Baccino R, Rarayre C, David R (1987) Le magnéto compactage de poudres: obtenir des matériaux inédits (Magnetic compaction of powders : to obtain non-conventional materials). Magnétoformage : des applications, 58/RGE(9)
Chelluri B (1994) Dynamic magnetic consolidation (DMC) process for powder consolidation of advanced materials. Mater Manuf Process 9(6):1127–1142
Popov VA, Aksenov AA, Ivanov VV, Lesuer DR, Gulbin VN, Kobelev AG, Solonin AN, Paranin SN, Khodos II, Smirnov OM, Zayatas SV (2002) MMC production method using dynamic compaction of mechanically alloyed aluminium and silicon carbide powders. Materials Science Forum 396–402:289–294
Acknowledgments
The author would like to thank Dr. Christian Burtin for helping to carry out x-ray tomography analysis. The author would also like to acknowledge the funding received through project AMETIS and the participating institutions.
Author information
Authors and Affiliations
Corresponding author
Additional information
Doc IIW-2336, recommended for publication by Commision “Arc Welding and Filler Metals.”
Rights and permissions
About this article
Cite this article
Manoharan, P., Manogaran, A.P., Priem, D. et al. State of the art of electromagnetic energy for welding and powder compaction. Weld World 57, 867–878 (2013). https://doi.org/10.1007/s40194-013-0080-0
Received:
Accepted:
Published:
Issue Date:
DOI: https://doi.org/10.1007/s40194-013-0080-0