Abstract
Dielectrical fluids have substantial impact on the machining performance of electrical discharge machining (EDM). Apposite selection of these fluids enhances the material removal rate (MRR) and microhardness while abating the tool wear rate (TWR) and surface roughness. In the present research, feasibility of using cerium oxide/water (CeO2/water) dielectrical nanofluid in EDM is examined experimentally. A portable EDM has been employed for experimental test, whereby mild steel workpiece and pure copper tool electrode were used. Powder concentration of CeO2/water was varied from 0.0 to 2.0 g/L, while the current, set distance, depth of cut and delay time were kept constant at 0.8 A, 2.0 mm, 0.5 mm and 0.5 s, respectively. Results show that at 0.6 g/L concentration, MRR and machining efficiency is enhanced by 20.04% and 69.68%, while TWR is reduced by 29.25%. Minimum surface roughness is obtained at the concentration of 1.0 g/L with Ra value of 0.22 µm, whereas with distilled water dielectrical fluid this value is 1.06 µm. Scanning electron microscopy images confirm that the best surface quality with the least pores and minute microcracks is obtained at 0.6 g/L concentration. Use of CeO2/water dielectrical nanofluid also improved material hardness significantly. While the microhardness number with distilled water is 1.06 HV, it upraised as high as 1.94 HV at powder concentration of 0.6 g/L.














Similar content being viewed by others
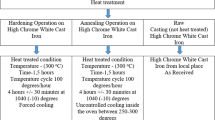
References
Liqing, L.; Yingjie, S.: Study of dry EDM with oxygen-mixed and cryogenic cooling approaches. Procedia CIRP 6, 344–350 (2013)
Wang, Y.K.; et al.: Micro EDM deposition in air by single discharge thermo simulation. Trans. Nonferr. Met. Soc. China 21, s450–s455 (2011)
Zahiruddin, M.; Kunieda, M.: Comparison of energy and removal efficiencies between micro and macro EDM. CIRP Ann. Manuf. Technol. 61(1), 187–190 (2012)
Sindhu, M.K.; Nandi, D.; Basak, I.: Electric discharge phenomenon in dielectric and electrolyte medium. Adv. Manuf. 6(4), 457–464 (2018)
Jahan, M.; Wong, Y.; Rahman, M.: A study on the quality micro-hole machining of tungsten carbide by micro-EDM process using transistor and RC-type pulse generator. J. Mater. Process. Technol. 209(4), 1706–1716 (2009)
Ho, K.; Newman, S.: State of the art electrical discharge machining (EDM). Int. J. Mach. Tools Manuf 43(13), 1287–1300 (2003)
Lan, T.S.; Yeh, L.J.: Optimum material removal control with tool life determination for machining operation. J. Mater. Process. Manuf. Sci. 10(4), 219–228 (2002)
Sidhu, S.S.; Batish, A.; Kumar, S.: Study of surface properties in particulate-reinforced metal matrix composites (MMCs) using powder-mixed electrical discharge machining (EDM). Mater. Manuf. Process. 29(1), 46–52 (2014)
Vishwakarma, M.; Parashar, V.; Khare, V.: Advancement in electric discharge machining on metal matrix composite materials in recent: a review. Int. J. Sci. Res. Publ. 2(3), 1–8 (2012)
Panda, D.K.; Bhoi, R.K.: Study of crater under single spark in electro discharge machining of very large solid by using transient three-dimensional thermal model. J. Mater. Process. Manuf. Sci. 10, 199–217 (2002)
Grosse, A.: The temperature range of liquid metals and an estimate of their critical constants. J. Inorg. Nucl. Chem. 22(1–2), 23–31 (1961)
Kibria, G.; et al.: Comparative study of different dielectrics for micro-EDM performance during microhole machining of Ti–6Al–4 V alloy. Int. J. Adv. Manuf. Technol. 48(5–8), 557–570 (2010)
Chen, S.B.; Yan,; Huang, F.: Influence of kerosene and distilled water as dielectrics on the electric discharge machining characteristics of Ti–6A1–4 V. J. Mater. Process. Technol. 87(1–3), 107–111 (1999)
Singh, S.; Bhardwaj, : A Review to EDM by using water and powder-mixed dielectric fluid. J. Miner. Mater. Charact. Eng. 10(02), 199 (2011)
Prihandana, G.S.; et al.: Effect of micro-powder suspension and ultrasonic vibration of dielectric fluid in micro-EDM processes—Taguchi approach. Int. J. Mach. Tool Manuf. 49(12–13), 1035–1041 (2009)
Kansal, H.S.; Singh,; Kumar, P.: Parametric optimization of powder mixed electrical discharge machining by response surface methodology. J. Mater. Process. Technol. 169(3), 427–436 (2005)
Korayem, M.; Zakeri, M.: Dynamic modeling of manipulation of micro/nanoparticles on rough surfaces. Appl. Surf. Sci. 257(15), 6503–6513 (2011)
Rao, P.S.; Ramji, K.; Satyanarayana, B.: Experimental investigation and optimization of wire EDM parameters for surface roughness, MRR and white layer in machining of aluminium alloy. Procedia Mater. Sci. 5, 2197–2206 (2014)
Kumar, M.S.; Datta, S; Kumar, R.: Electro-discharge machining performance of Ti–6Al–4V alloy: studies on parametric effect and phenomenon of electrode wear. Arab. J. Sci. Eng. 44(2), 1553–1568 (2019)
Liu, J.; et al.: A study of the materials removal mechanism of grinding-aided electrochemical discharge machining of metal matrix composites. Adv. Compos. Lett. 27(5), 204–211 (2018)
Kumar, A.T.; Soota, T.; Kumar, J.: Optimisation of wire-cut EDM process parameter by Grey-based response surface methodology. J. Ind. Eng. Int. 14(4), 821–829 (2018)
Bhattacharya, A.; et al.: Optimal parameter settings for rough and finish machining of die steels in powder-mixed EDM. Int. J. Adv. Manuf. Technol. 61(5–8), 537–548 (2012)
Shard, A.; et al.: Effect of B 4 C abrasive mixed into dielectric fluid on electrical discharge machining. J. Braz. Soc. Mech. Sci. Eng. 40(12), 554 (2018)
Korayem, M.; Omidi, E.: Robust controlled manipulation of nanoparticles using atomic force microscope. Micro Nano Lett. 7(9), 927–931 (2012)
Hossain, M.M.; et al.: Performance enhancement in powder mixed electrical discharge machining (PMEDM) using PEDM and multi-component metal oxide (Ni0.3Co0.1Mn0.6O) mixed dielectrical fluid. Proc. Mech. Eng. Res. Day 2018, 285–286 (2018)
Lee, C.S.; et al.: A method of hole pass-through evaluation for EDM drilling. J. Korean Inst. Ind. Eng. 38(3), 220–226 (2012)
Razak, M.A.; Abdul-Rani,; Nanimina, A.: Improving EDM efficiency with silicon carbide powder-mixed dielectric fluid. Int. J. Mater. Mech. Manuf. 3(1), 40–43 (2015)
Kurapati, V.B.; Kommineni, R.: Effect of wear parameters on dry sliding behavior of fly ash/SiC particles reinforced AA 2024 hybrid composites. Mater. Res. Express 4(9), 096512 (2017)
Assarzadeh, S.; Ghoreishi, M.: A dual response surface-desirability approach to process modeling and optimization of Al2O3 powder-mixed electrical discharge machining (PMEDM) parameters. Int. J. Adv. Manuf. Technol. 64(9–12), 1459–1477 (2013)
Syed, K.H.; Palaniyandi, K.: Performance of electrical discharge machining using aluminium powder suspended distilled water. Turk. J. Eng. Environ. Sci. 36(3), 195–207 (2012)
Abdul-Rani, A.; et al.: Machined surface quality in nano aluminum mixed electrical discharge machining. Procedia Manuf. 7, 510–517 (2017)
Ojha, K.R.; Garg,; Singh, K.: Experimental investigation and modeling of PMEDM process with chromium powder suspended dielectric. Int. J. Appl. Sci. Eng. 9(2), 65–81 (2011)
Mohal, S.; Kumar, H.: Parametric optimization of multiwalled carbon nanotube-assisted electric discharge machining of Al-10% SiCp metal matrix composite by response surface methodology. Mater. Manuf. Process. 32(3), 263–273 (2017)
Rao, T.B.: Optimizing machining parameters of wire-EDM process to cut Al7075/SiCp composites using an integrated statistical approach. Adv. Manuf. 4(3), 202–216 (2016)
Rao, T.B.; Krishna, A.G.: Simultaneous optimization of multiple performance characteristics in WEDM for machining ZC63/SiCp MMC. Adv. Manuf. 1(3), 265–275 (2013)
Baseri, H.; Sadeghian, S.: Effects of nanopowder TiO2-mixed dielectric and rotary tool on EDM. Int. J. Adv. Manuf. Technol. 83(1–4), 519–528 (2016)
Nguyen, H.P.; Pham, V.D.; Ngo, N.V.: Application of TOPSIS to Taguchi method for multi-characteristic optimization of electrical discharge machining with titanium powder mixed into dielectric fluid. Int. J. Adv. Manuf. Technol. 98(5–8), 1179–1198 (2018)
Banh, T.L.; et al.: Characteristics optimization of powder mixed electric discharge machining using titanium powder for die steel materials. Proc. Inst. Mech. Eng. Part E J. Process. Mech. Eng. 232(3), 281–298 (2018)
Sahu, R.; et al.: An innovative approach for generation of Aluminium nanoparticles using micro electrical discharge machining. Procedia Mater. Sci. 5, 1205–1213 (2014)
Loya, A.; Stair, J.L.; Ren, G.: Simulation and experimental study of rheological properties of CeO2–water nanofluid. Int. Nano Lett. 5(1), 1–7 (2015). https://doi.org/10.1007/s40089-014-0129-0
Tiwari, A.K.; Ghosh, P.; Sarkar, J.: Heat transfer and pressure drop characteristics of CeO2/water nanofluid in plate heat exchanger. Appl. Therm. Eng. 57(1–2), 24–32 (2013)
Loya, A.; Stair, J.L.; Ren, G.: The study of simulating metaloxide nanoparticles in aqueous fluid. Int. J. Eng. Res. Technol. 3(4), 1954–1960 (2014)
Rico, C.M.; et al.: Cerium oxide nanoparticles modify the antioxidative stress enzyme activities and macromolecule composition in rice seedlings. Environ. Sci. Technol. 47(24), 14110–14118 (2013)
Ramírez-Olvera, S.M.; et al.: Cerium enhances germination and shoot growth, and alters mineral nutrient concentration in rice. PLoS ONE 13(3), 0194691 (2018)
Zamiri, R.; et al.: Dielectrical properties of CeO2 nanoparticles at different temperatures. PLoS ONE 10(4), 0122989 (2015)
Helmenstine AM: Copper facts: chemical and physical properties (2019). https://www.thoughtco.com/copper-facts-chemical-and-physical-properties-606521. Accessed 20 Feb 2019
Austen Knapman: Properties of mild steel (2013). https://www.austenknapman.co.uk/blog/faqs/faq-what-is-the-melting-point-of-mild-steel/. Accessed 20 Feb 2019
EASCHEM: High purity cerium oxide powder (2019). https://www.easchem.com/1306-38-3_High+Purity+Cerium+Oxide+Powder.html?gclid=CjwKCAiA9JbwBRAAEiwAnWa4Q9LcDYAyyTA2JgZH8S5YlIeej9JuFBCDOaawTZx1886Pfb7-ydPPdxoCQsgQAvD_BwE
Modi, M.; Agarwal, G.: Design, development and experimental investigation of electro-discharge diamond surface grinding of Ti–6Al–4 V. In: Liu, X.; Jiang, Z.; Han, J. (eds.) Advanced Materials Research, vol. 418–420, pp. 1478–1481 (2012)
Purohit, R.; et al.: Optimization of electric discharge machining of M2 tool steel using grey relational analysis. Mater. Today Proc. 2(4–5), 3378–3387 (2015)
Tzeng, Y.F.; Lee, C.Y.: Effects of powder characteristics on electrodischarge machining efficiency. Int. J. Adv. Manuf. Technol. 17(8), 586–592 (2001)
Wang, X.; Feng, C.: Development of empirical models for surface roughness prediction in finish turning. Int. J. Adv. Manuf. Technol. 20(5), 348–356 (2002)
Acknowledgements
This research was funded by University of Malaya under UMRG Programme, Grant Number RP039A-15AET.
Author information
Authors and Affiliations
Corresponding author
Electronic supplementary material
Below is the link to the electronic supplementary material.
Rights and permissions
About this article
Cite this article
Hossain, M.M., Karim, M.S.B.A., Hoong, W.Y. et al. Feasibility of Using CeO2/Water Dielectrical Nanofluid in Electrical Discharge Machining (EDM). Arab J Sci Eng 45, 5435–5445 (2020). https://doi.org/10.1007/s13369-020-04404-x
Received:
Accepted:
Published:
Issue Date:
DOI: https://doi.org/10.1007/s13369-020-04404-x