Abstract
In order to improve the internal quality of cross wedge rolling (CWR) shaft, the floating-pressure method (FPM) using high-pressure gas to compact void in CWR shaft is adopted in this paper. Firstly, the theoretical relations between each influencing factor and flow stresses are deduced by establishing the mechanical model of void closure based on FPM. Then, the laws of stress variation, metal flow, void shape variation, and microstructure evolution are all analyzed by DEFORM-3D finite element software, and the mechanism of void closure based on FPM is clarified. By means of hot isostatic pressing equipment, the FPM experiments are conducted, and it is illustrated that the outer dimensions of CWR shaft are hardly affected and its internal void can be effectively eliminated. Finally, the tests of specimens’ mechanics performance show that the tensile strength of the specimen is improved and its surface hardness is slightly reduced. The research results provide a new way for improving the yield and mechanical properties of CWR shaft.
Similar content being viewed by others
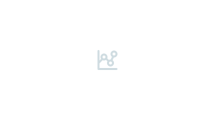
References
Shu XD, Shchukin VY, Kozhevnikova G, Sun BS, Peng WF (2014) The theory and forming technology of cross wedge rolling. Publ House Science, Beijing
Wei J, Shu XD, Tian DY, Xiang W, Wei YL, Peng WF, Liu C, Wang Y, Niu BK (2017) Study in shaft end forming quality of closed-open cross wedge rolling shaft using a wedge block. Int J Adv Manuf Technol 93:1095–1105
Pater A (1997) Study of cross wedge rolling process. J Mater Process Technol 80:370–375
Hu ZH, Zhang KS, Wang BY, Shu XD, Yang CP (2005) Forming technology and simulation of cross wedge rolling. Metallurgical Industry Press, Beijing
Liu GH, Ren GS, Xu CG, Jiang Z, Shen Z (2004) Simulation study on the formation mechanism of inner void defect in the process of cross wedge rolling. Chin J Mech Eng 40(2):150–156 (in Chinese)
Shu XD, Li GP, Zu WM (2012) Prediction of the central defect location for multi-wedge cross wedge rolling forming automobile semi-axle. Appl Sci Technol 39(2):45–48 (in Chinese)
Qiu P, Xiao H, Li M (2009) Study on the quality effect of rolled piece internal part in two rolls cross wedge rolling by J.T.S method. J Plast Eng 16(4):111–115 (in Chinese)
Qiu P, Wang J, Xiao H (2011) Study on rolled pieces internal part quality improvement during three-roll cross wedge rolling by non-uniform temperature field. China Mech Eng 22(13):1550–1554 (in Chinese)
Chen SY, Zhang KS, Yang CP, Hu ZH, Gao XY (2006) Effect of process parameters of cross wedge rolling on the internal rarefaction. Forging Stamping Technol 31:38–40 (in Chinese)
Wu M, Hua L, Shao YC, Zhou QJ (2011) Influence of the annealing cooling rate on the microstructure evolution and deformation behaviors in the cold ring rolling of medium steel. Mater Des 32:2292–2300
McClintock FA (1968) A criterion for ductile fracture by the growth of holes. J Appl Mech 35:363–371
Ren YL, Nie SM, Niu LJ, Zhu L (2008) Healing conditions of large forging internal voids defect. Chin J Mech Eng 44(2):248–252 (in Chinese)
Eshelby JD (1957) The determination of the elastic field of an ellipsoidal inclusion and related problems. Proc R Soc Lond A 241:376–396
Li Y (2009) Research on evolution of void defects in heavy forgings during upsetting process. Dissertation, Shanghai Jiaotong University (in Chinese)
Zhang XX (2009) Research on void evolution in large ingot during hot forging. Dissertation, Shanghai Jiaotong University (in Chinese)
Zhang XX, Cui ZS (2009) Z-C criterion of void closure for large-ingot hot forging and its application. Chin J Mech Eng 45(1):148–153 (in Chinese)
Zhu M, Jin QL (1992) Study on closing of internal voids of materials. Acta Armamentarium 2:59–65 (in Chinese)
Wei DB (2001) Research on the disciplinarian of inner crack healing in metal. Dissertation, University of Science and Technology Beijing (in Chinese)
Tian DY, Shu XD, Wei YL, Wang Y, Xu C, Zhu Y, Zhao ZL, He QF (2017) Influence of shape and position parameters on compaction of cross wedge rolling shaft by gas pressure. J Ningbo Univ 30(4):11–16 (in Chinese)
Tian DY, Shu XD, Wang Y, Wei YL, Yin AM (2017) Study on compacting mechanism of core void for cross wedge rolling shaft using floating-pressure method. Mech Sci Technol Aerosp Eng 36(7):1079–1084 (in Chinese)
Peng WF, Zhang JH, Huang GX, Liu WP, Shu XD, Zhu J (2016) Stress distributions during the cross-wedge rolling of composite 42CrMo/Q235 laminated shafts. Int J Adv Manuf Technol 83:145–155
Sun BS, Xu JY, Peng WF, Shu XD, Yin AM, Huang GX (2018) Experimental investigation on cross wedge rolling of composite 42CrMo/Q235 laminated shaft. Int J Adv Manuf Technol 96:895–903
Hu JJ, Li XP (2010) DEFORM-3D plastic forming CAE application tutorial. Peking University Press, Beijing
Serajzadeh S (2007) A study on kinetics static and metal dynamic recrystallization during hot rolling. Mater Sci Eng A 448(1–2):146–153
Lin YC, Chen MS, Zhong J (2009) Static recrystallization behaviors of deformed 42CrMo steel. J Cent South Univ 40(2):411–416 (in Chinese)
Wei YL, Shu XD, Han ST, Tian DY, Wei J (2018) Analysis of microstructure evolution during different stages of closed-open cross wedge rolling. Int J Adv Manuf Tech 95:1975–1988
Shao C, Liu HY, Li JT (2012) Applications of hot isostatic pressing on cast superalloy. Mater Rev 26(10):121–124 (in Chinese)
Acknowledgements
The authors would like to thank Professor Xiang from Ningbo University for providing assistance with editing this article.
Funding
This work was supported by the National Natural Science Foundation of China [Grant No. 51475247] and the Key Project of Zhejiang Natural Science Foundation of China (Grant No. LZ17E050001).
Author information
Authors and Affiliations
Corresponding author
Rights and permissions
About this article
Cite this article
Tian, D., Shu, X., Zhu, Y. et al. Closure laws of void in the core of cross wedge rolling shaft based on the floating-pressure method. Int J Adv Manuf Technol 98, 2905–2916 (2018). https://doi.org/10.1007/s00170-018-2448-1
Received:
Accepted:
Published:
Issue Date:
DOI: https://doi.org/10.1007/s00170-018-2448-1