Abstract
Current guidelines for Human-Robot Collaboration (HRC) allow a person to be within the working area of an industrial robot arm whilst maintaining their physical safety. However, research into increasing automation and social robotics have shown that attributes in the robot, such as speed and proximity setting, can influence a person’s workload and trust. Despite this, studies into how an industrial robot arm’s attributes affect a person during HRC are limited and require further development. Therefore, a study was proposed to assess the impact of robot’s speed and proximity setting on a person’s workload and trust during an HRC task. Eighty-three participants from Cranfield University and the ASK Centre, BAE Systems Samlesbury, completed a task in collaboration with a UR5 industrial robot arm running at different speeds and proximity settings, workload and trust were measured after each run. Workload was found to be positively related to speed but not significantly related to proximity setting. Significant interaction was not found for trust with speed or proximity setting. This study showed that even when operating within current safety guidelines, an industrial robot can affect a person’s workload. The lack of significant interaction with trust was attributed to the robot’s relatively small size and high success rate, and therefore may have an influence in larger industrial robots. As workload and trust can have a significant impact on a person’s performance and satisfaction, it is key to understand this relationship early in the development and design of collaborative work cells to ensure safe and high productivity.
Similar content being viewed by others
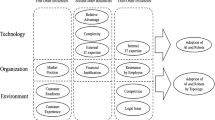
Avoid common mistakes on your manuscript.
1 Introduction
Robotics within industry has seen a significant uptake in recent years, with increases in sales reaching a peak in 2018 [1]. Despite a decrease in overall robot sales to industry in 2019 and 2020, collaborative robots have seen an increase in sales [2]. This can be attributed to the changing demands of robots in automation and collaborative robots seeing significant increases in application [3]. Whereas robots are capable of high payload and exposure to hazardous chemicals, they lack the adaptability of a human worker. Human–Robot Collaboration (HRC) aims to combine these strengths to increase overall productivity, whilst maintaining the safety of the worker.
Traditionally, the concept of maintaining safety has been limited to physical safety (the actions of the robot do not result in an injury to the human). As industrial robot arms have been completely separated from human workers by physical barriers, the interest in understanding the impacts on a person’s psychological safety has been minimal. International standards ISO 10218–1:2011 and ISO/TS 15,066:2016 [4, 5] show the manufacturing industry is opening to HRC and can provide solutions for maintaining physical safety without the use of physical barriers, and research is expanding to also examine psychological safety (risks to human cognitive/affective wellbeing) [6, 7].
Two key robot attributes that can be controlled and adjusted without significant offline time to maintain physical safety are the robot’s speed and proximity. Although speed (250 mm/s) and proximity limits are defined in current safety standards in relation to physical risk, psychological safety is not considered in the guidance. This is key, as failure to address the human element when increasing automation has been shown to limit the successful integration of new technology [8]. In this paper, it is proposed that variations in a robot’s attributes operating within the envelope of safe speed and proximity set by the HRC guidelines can influence a person’s psychological safety.
For the purpose of this paper, HRI considers any situation where a robot’s actions, or inactions, result in a reaction from a human (and vice versa) and HRC considers any situation where the robot and the human work together to complete a task. Studies in mobile robotics have revealed a range of factors linked to changes in a person’s psychological safety. The study of such relationships are sparse for robot arms, and the extent to which findings from mobile robots experiments can be generalized to robot arms is debated [9,10,11]. First, the key psychological constructs will be discussed, with their relevance to increased automation and robotics.
1.1 Workload
As HRC will predominantly take place in industrial work settings, an important psychological state to consider is workload. In fields which have seen increased levels of automation, the impacts on workload have been a topic of research for over 40 years. With no universally accepted and clear definition of workload [12] this study uses the definition of workload used for the development of the widely used and verified NASA-Task Load IndeX (NASA-TLX): “the cost incurred by a human operator to achieve a particular level of importance” [13].
Workload has been identified as a key factor to influence human performance, with an optimal level from which deviation can be detrimental [14,15,16,17]. Too high and the person risks fatigue and illness, too low and the person may lose focus in the task. However, the specific elements of an automated system that influence workload levels, and the optimal levels required for specific tasks, are important to understand as these are linked to performance and accident prevention [14]. For example, levels of automation have been shown to influence a person’s workload during driving [18] and teleoperation tasks [19, 20] but these findings cannot be directly extrapolated to other tasks. Additionally, relationships between a robot’s speed and a person’s psychological safety have been identified in social robotics research but without exploring workload specifically [21,22,23,24]. Thus, although general trends can be identified, it is difficult to generalise or compare research findings outside of the specificities of respective studies, primarily due to differences in research methods and contexts. Early studies in the context of industrial robots for HRC have shown that working within a robot’s operating area increases workload [25, 26], but few have studied the effects of changing robot attributes on workload. Therefore, to optimise the design of industrial HRC, it is important to identify which specific robot attributes lead to changes in operator workload and how they impact upon effective HRC.
Industrial HRC research using formal Ergonomics / Human Factors methods is uncommon. For example, Tan et al. [9], studied the skin potential reflex (SPR) of participants collaborating with an industrial robot arm operating at 250, 500, and 1000 mm/s as an objective measure of workload and collected self-reported levels of ‘fear’ and ‘surprise’ as a subjective measure of workload—but provided no clear definitions of these constructs to participants or validation of how they reliably represent workload. They found both higher SPR and ‘fear’ and ‘surprise’ levels at speeds greater than 500 mm/s, suggesting that workload would not only be dependent on the task but also the robot’s speed, but findings may not truly reflect the construct of workload. Many psychological and affective states, such as ‘comfort’, ‘fear’, ‘surprise’, ‘anxiety’, etc., can be considered subjective manifestations of a persons’ psychological safety as we know that extreme levels can cause deleterious effects on wellbeing. Some of these have been found associated with workload, such as the decreasing comfort resulting in an increase in workload [13, 27]. Therefore, although it is not yet possible to directly link these psychological / affective states and workload, they are likely to be a part of the relationship between robot attributes and psychological safety outcomes.
Butler and Agah [28] studied the relationship between a mobile robot’s speed and human ‘comfort’ in a study which involved the robot approaching participants directly at a slow (254 mm/s) or a fast (1016 mm/s) speed condition, after which they rated their level of ‘comfort’ using a scale. This study established that participant ‘comfort’ decreased in the fast speed condition, suggesting an increase in workload may have also occurred. Similarly, Kulic and Croft [29] gathered self-reported measures of ‘anxiety’, ‘calm’, and ‘surprise’ when a robot arm moved using 2 different path planners under 3 different speed settings (0.31, 1.57 and 3.14 rad/s). They found positive correlations between robot speed and participants’ ‘surprise’, and between speed and ‘anxiety’, and a negative correlation between speed and ‘calm’ levels. As with [9], an increase in ‘surprise’ may have an effect on the person’s workload, suggesting a positive correlation between speed and workload, but the exact nature and strength of relationships between these psychological outcomes and workload is not yet confirmed. A study by Koppenborg et al., [30] directly measured the influence of the changing speed of an industrial robot arm during HRC on workload in a virtual environment. The results showed a significant increase in workload from the low-speed setting (750 mm/s) to the high-speed setting (1400 mm/s). Although the study is limited by the lack of presence that an actual robot would provide, the results further reinforce link between workload and robot speed during HRC than previous work. It is also noteworthy that the majority of speeds used in these studies exceed the maximum 250 mm/s safety guidance limit for HRC. To the knowledge of the authors of the present paper, there are no studies to date that have assessed the effects of an industrial robot arm’s speed during HRC, within the speed envelope defined by ISO/TS 15,066:2016, which this paper seeks to address.
Compared to speed, the effect of the robot’s proximity in HRI has seen a greater amount of research. This is due to the prevalence of social robots that are, by definition, designed for close proximity. The majority of the studies reviewed for this paper developed their models around the Proxemics model by Hall [31], which defines the socially acceptable distances around a person for Human–Human Interaction. Kim and Mutlu [32] assessed the participant’s ‘comfort’, ‘pleasure’, and ‘likeability’ via questionnaire during multiple tasks when a mobile robot was at 0.46 and 1.2 m. They found that when co-operating with the robot, participants reported lower ‘comfort’ and ‘likeability’ when the robot was closer. This decrease in comfort with reduced separation was also reported with robot arms [33, 34], as well as an increase in workload [9].
A means of overcoming subjective uncertainty is to objectively measure participant’s changes in position. This is demonstrated in Stark et al.[10], where the reactions of participants to a robot arm’s proximity during HRC were monitored. As the robot arm entered the personal zone of the person (0.45–1.2 m), they physically moved away suggesting they were not comfortable with that proximity. Walters et al., [35] attempted to identify some of the factors that influence the accepted proximity, focusing on the participant’s level of control and their personality. When the robot is static and the participant is approaching, the majority (60%) would move to within the intimate zone (0.15–0.45 m) compared to only 38% of participants accepting of the robot approaching up to 0.5 m. This indicates that when participants are in control of the proximity, they feel more comfortable however, this was not supported in other studies [36]. The robot’s size and “gaze” direction have also been shown to influence the allowable distance [28, 37, 38]. From these studies, it appears that the proximity of the robot has an impact on person’s comfort during HRI and, therefore, potentially on their workload. However, the studies into the effects of an industrial robot arm’s proximity during HRC whilst adhering to the guidance set in ISO/TS 15,066:2016 are few and limited. With physical barriers being removed and the increased sophistication of collision avoidance algorithms for application in HRC, it is imperative that such attributes of the robot (and the psychological factors they impact upon) be further understood.
Although these comparisons are not direct between robot attributes and workload, they can be used to inform. They demonstrate that a person’s psychological safety can be influenced by changing robot speed and proximity. A major limitation in HRI and HRC studies is the lack of valid and reliable measures, and consistent experimental methods. Furthermore, HRC studies are rarely conducted under the industrial settings which they are intended for. Whilst some have used established reliable tools for subjective measures, such as the NASA TLX, others have not used rigorously tested scales. Alternatively, objective measures can be task specific, where the choice of which element of the activity is contributing to the workload of the task allows for subjectivity [17, 39, 40]. Indeed, a great deal of research has not accounted for the possibility that results may reflect task characteristics and complexity rather than effects of robot attributes. This study aims to rectify this oversight, by having the impact of speed and proximity on a person’s psychological responses as the primary research focus. Furthermore, the dependent variables will use clear definitions for the psychological concepts that are adopted from previously used surveys where the focus has been on the increasing use of automation/robotics in an industrial setting.
A key challenge when measuring workload is that it can vary based on the individual, the task at hand, and the environment in which the task is being conducted [40]. In order to understand workload, the different aspects which contribute to it should be considered. Cain [12] postulated that these aspects can be divided into 3 categories: the amount of work and number of things to do, the subjective psychological experiences of the human, and the time required to complete the task. These criteria fall in line with the variables measured by the most commonly used subjective workload scales. Of these, two that are frequently compared are the NASA-Task Load IndeX (NASA-TLX) [13] and the Subjective Workload Assessment Technique (SWAT) [41]. In direct comparisons, there has been little evidence that either scale shows a greater sensitivity to changes in users’ workload, however, both showed higher sensitivity in comparison with other scales [12, 42, 43]. A key difference is user acceptability, which is higher in NASA-TLX and attributed to the faster completion of the scale, therefore, this was chosen as the scale for this study. The NASA-TLX [44] measures 6 subscales: Mental Demand (MD), Physical Demand (PD), Temporal Demand (TD), Performance, Effort, and Frustration. The average of the scores obtained on each of those subscales provides an overall workload score [44, 45]. For this study, the Raw TLX (RTLX) was used, in which the weighting of the subscales is omitted. This was chosen as the test is simpler to apply, and comparative studies show no consensus of an effect on the sensitivity of the scale [45].
1.2 Trust
Another key psychological state which has been highly related to performance with automation is ‘trust’ [46]. Like workload, trust is also problematic to define and there is no universal definition, so it is highly important to consider the context and system attributes for which it is being investigated. For this study, the definition used was “the attitude that an agent will help an individual’s goals in a situation characterised by uncertainty and vulnerability” [46], where the agent is the robot. As the level of trust the operator has in the system increases, the efficiency of the system increases making it a desirable concept to better understand in industry [47,48,49]. There is a limit to the system efficiency increasing, as increasing trust may result in passivity or complacency in the task, leading to difficulty in detecting changes/faults in the system. Too little trust, however, and the person will be more likely to interfere with the process [47, 50]. As with workload, deviations from the optimal level can have detrimental effects.
Hancock et al. [51] ran a meta-analysis and identified 3 main categories of factors which could affect a person’s trust during HRI: the human, the robot, and the environment. Amongst the factors falling under the Robot category, the robot’s performance had the largest impact. The robot’s attributes (proximity, shape, anthropomorphism, personality, and type) were also shown to be significant factors. MacArthur et al. [34] manipulated the speed and proximity of a mobile robot approaching participants, after which they would then complete Human Robot Trust Scale and Negative Attitudes Towards Robots Scale surveys. They found that participants’ trust was reduced by decreasing proximity and increasing speed of the robot.
Whilst the trust scales mentioned above are sufficient for quantifying general trust in HRI, as outlined it is important to consider the impact of specific robot attributes where possible. A more focused measurement tool for industrial HRC was developed by Charalambous et al. [52] to account for the impact of robot attributes on operator trust in collaborative tasks. As this scale was developed with industrial robot arms and end-effectors it was deemed the most relevant for this study.
As outlined, direct analysis of the relationship between robot speed and proximity with workload and trust has been highly limited and previous findings are largely incomparable. This highlights a gap in knowledge, which the present study aims to begin filling. It measures the impact of an industrial robot arm’s speed and proximity setting on a person’s workload and trust during a HRC task. Workload and trust have been identified as key metrics in task performance, whilst speed and proximity have been identified as two robot attributes which impact on a person’s psychology during HRI. Based on our current knowledge, the aim of the present study is to determine if there is a link between the speed and proximity setting of an industrial robot during HRC with a person’s workload and trust. This will be tested by the following hypotheses:
H1:
The speed of the robot arm will influence workload during HRC.
H2:
The proximity setting of the robot arm will influence workload during HRC.
H3:
The speed of the robot arm will influence trust during HRC.
H4:
The proximity setting of the robot arm will influence trust during HRC.
2 Method
2.1 Design
The task was designed to replicate an assembly task in a collaborative cell with a human and robot team. The assembly task was a simplified version of a common task that is found in aircraft assembly. In this task, the robot completed a pick and place operation whilst equipped with an avoidance algorithm. The robot collected a pipe, brought the pipe to the first foam block with a pre-drilled hole, and held the pipe in position until the participant pushed a release button, at which point the robot released the pipe and then moved to collect the next pipe. Once the participant had deemed the robot had moved to a safe distance away (as instructed in the briefing), they positioned the pipe correctly into the hole and tightened two pipe connectors onto the robot side of the pipe and confirmed by visual inspection that the pipe connectors were in contact with the foam block. During this, the robot collected the next pipe and brought it to the next foam block. A vision system monitored the participant’s head and hand locations, and should a potential collision be detected the robot changed path. The changed path was always in the x-direction away from the participant, with the distance in the x-direction determined by the proximity setting away from the participant’s head or hands (whichever was closest to the Tool Centre Point) using an iteration on a repulsive vectors algorithm (see Fig. 1). After reaching the next foam block, the robot held its position until the participant pushed the release button, at which point it moved to collect the final pipe. The third pipe had no assembly required, and participants only positioned the pipe in the hole. The ability for the participant to adjust the distance to the robot was a deliberate one, as it was deemed that forcing the participants to remain in fixed position even after they had completed the task would have a large impact. A time-lapse of the experiment can be found in Fig. 2.
The avoidance motion taken by the robot to avoid a collision with an obstacle where i represents the current position, i + 1 represents the next waypoint, 1 and 2 represent avoidance waypoints, obs represents the proximity setting, and the obstacle is either the head, left hand or right hand (depending on which is closest to TCP, and then in priority order of avoiding the head over the hands)
2.2 Participants
Eighty-three participants were recruited between May and October 2019. Forty were students and staff at Cranfield University, and 43 were from the Academy for Skills & Knowledge Centre and BAE Systems in Samlesbury, United Kingdom. The participant’s age range at Cranfield was 21–53 years (median = 25 years), with 15 female and 25 male participants. The participants’ age range at Samlesbury was 16–59 years (median = 19 years), with 35 male and eight female participants. The experience of the participants is shown in Fig. 3.
2.3 Materials and Apparatus
The experiment involved participants working together with a Universal Robots UR5 to complete a task. The UR5 was chosen as it has been designed for HRC and is seeing deployment in different areas of manufacturing to assist workers. The position of the participants in the collaborative workspace was monitored by a Microsoft Kinect v2 vision system. The position of the participants and the position of the Tool Centre Point (TCP) of the UR5 were processed by an obstacle avoidance algorithm developed by Matthew Story, one of the authors, running on Visual Basic Studio 2017. The set up can be found in Fig. 4, where the blocks were located 0.62–0.72 m away from the base of the UR5, and 0.3 m distance separation between each other. Positioned next to the first two foam blocks were a set of white pipe connectors. The surveys used for the study were the RTLX [13] and the Trust in Human Robot Collaboration Scale [52].
The study was conducted in accordance with the General Data Protection Regulation 2018, with data fully anonymized during processing. A risk assessment was conducted for the study and was granted ethical approval by Cranfield University. Participants were provided with a bump cap and safety glasses to ensure their protection. This research complied with the American Psychological Association Code of Ethics and was approved by the Institutional Review Board at Cranfield University.
2.4 Procedure
After a briefing, the participants completed a consent form and a brief demographic questionnaire. Prior to beginning the study, participants were given their safety cap and glasses and they were then offered the opportunity to complete the task whilst the robot was stationary to ensure they understood the task and able to complete what was asked of them prior to beginning the main task performance session. Participants were informed they could complete the task at a pace they were comfortable with.
Each participant underwent one data collection session, which consisted of completing the same task 6 times with the combination of a given speed and proximity changing for each task in a counterbalanced measures design. The speed was the linear velocity of the TCP, and the distance was determined as the distance between the TCP of the UR5 and the participants’ limb (head, right hand or left hand) which was closest to the UR5. There were 3 speed settings chosen for the UR5 robot to operate at during the different conditions. These were 60%, 80%, and 100% of the maximum speed the robot could run in accordance with ISO/TS 15066:2016 (36, 48, and 60 degrees/s for joint movements and 150, 200, and 250 mm/s for linear movements respectively). There were 2 proximity settings chosen for the UR5 robot to operate at during the separate tasks, 0.2m and 0.3m. The distances were determined through the calculation of the minimum safe distance set out in ISO/TS 15066:2016 (0.182m at 250 mm/s). The upper distance of 0.3m was chosen due to the limitations in the size of the UR5. After each time completing the task, participants were asked to complete the survey forms. Participants were informed that each run was under varying conditions but not informed until after the study what the changes were. Upon completion of all runs and surveys, participants were asked if they had any questions or comments regarding the study.
3 Results
A linear mixed-effects model (LMM) analysis was run for workload using IBM SPSS Statistics 26. This technique is used to identify relationships in data comprising different categories, with both fixed and random effects, as is the case with the within-subjects repeated-measures data produced in this study. A linear mixed-effects model analysis was therefore chosen as it can be used to describe nonlinear relationships across time with missing data points [53]. Analysis with incomplete/unbalanced data, and acceptable type I error rates when observing participants in multiple conditions has seen linear mixed effects models receive more attention over recent years [54].
Location (Cranfield or Samlesbury), speed, and proximity were entered as fixed factors, participant treated as random factors, and workload as the dependent variable. There was no significant relationship between location and workload (F(1, 80.808) = 0.985, p = 0.324), and both the interaction effect between location and speed (F(2, 191.850) = 0.815, p = 0.444) and location and proximity setting (F(1, 79.793) = 0.031, p = 0.970) with workload were not significant.
There was a significant relationship for workload with speed (F(2, 191.850) = 9.450, p < 0.001) but not for proximity setting (F(1, 79.793) = 3.026, p = 0.086) (see Fig. 5). The interaction effect between speed and proximity setting on workload was not significant (F(2, 184.820) = 0.031, p = 0.970) (see Table 1).
To determine the changes between the speed variables, paired t-tests were run, with a Bonferroni correction applied to the level of significance (p = 0.05/3 = 0.0167). The paired t-tests showed a significant difference between 60 and 100% (p < 0.001), and 80% and 100% (p = 0.002) (see Table 2).
The same analysis was run for the workload subscales and speed. There was a significant relationship between speed and mental demand (F(2, 246.040) = 3.814, p = 0.023), temporal demand (F(2, 161.340) = 31.958, p < 0.001), performance (F(2, 182.148) = 4.707, p = 0.010), effort (F(2, 175.690) = 13.625, p < 0.001), and frustration (F(2, 157.815) = 10.284, p < 0.001) (see Fig. 6). To determine the changes between the speed variables, paired t-tests were run (see Table 3), with a Bonferroni correction applied to the level of significance (p = 0.05/3 = 0.0167).
An LMM analysis was also run for trust. The appropriateness of LMM for trust followed the same rationale as for workload. Location, speed, and proximity were first entered as fixed factors, participant treated as random factors, and workload as the dependent variable. There was no significant relationship between location and workload (F(1, 80.762) = 0.090, p = 0.765), and both the interaction effect between location and speed (F(2, 168.950) = 0.502, p = 0.606) and location and proximity setting (F(1, 71.633) = 2.266, p = 0.137) with workload were not significant.
There was no significant relationship between trust and speed (F(2, 168.950) = 2.587, p = 0.078) nor with proximity setting (F(1, 71.633) = 1.711, p = 0.195) (see Fig. 7). The interaction effect between speed and proximity setting on trust was not significant (F(2, 192.415) = 0.143, p = 0.867) (see Table 4).
An LMM was also run to determine if the experience of the participants with robots would influence either workload or trust, with experience as a fixed factor and participant as a random factor. The experience levels are found in Fig. 3 and Fig. 8. There was no significant relationship between experience and workload (F(4, 77.870) = 0.925, p = 0.454) nor between experience and trust (F(4, 77.731) = 0.373, p = 0.827). The interaction effect between speed and experience on workload was significant (F(8, 175.301) = 2.087, p = 0.039), however the interaction effect between proximity and experience on workload was significant (F(4, 76.281) = 0.207, p = 0.934).
4 Discussion
In this study, the aim was to determine whether there was a link between a small (relative to the person), low payload robot arm’s speed and proximity setting, and levels of human workload and trust. Hypothesis 1 was supported by the data. Hypothesis 1 put forward that the speed of the robot arm will influence workload during HRC, which was shown in the data with a significant positive relationship between speed and workload. However, this positive relationship was not significant when comparing 60% and 80% of the maximum speed of the UR5, suggesting that the speed only impacts on overall workload above a critical threshold. The concept of a critical threshold for robot speed has been reported in previous studies [28, 55]–[21], however these studies used higher speeds than is considered safe by the guidance set in ISO/TS 15066:2016.
The present study used speeds within the envelope for HRC as defined by ISO/TS 15066. The present results suggest that speeds within the acceptable brackets deemed physically safe can impact an operator’s workload. Furthermore, the workload of the operator can be affected by the robot’s speed even when the task to be completed is of low complexity, as shown in the study by the overall average workload score being in the lower end of the scale. The low complexity may also play a key role on the speed threshold for increasing workload. As the task increases in complexity, the threshold may decrease, as operators are required to dedicate more resources to the task and less to monitoring the robot. A more developed understanding of the changes in workload can be gained from the analysis of the changes in the subscales with speed.
The speed threshold, for example, can be better understood when looking at the subscales. Although an increase in speed resulted in significant changes in the temporal demand and effort subscales between 60% and 80% speed, this was offset by the decrease in frustration. Therefore, although the overall workload may not significantly differ the reasons for the values differ. Higher levels of the temporal demand and effort subscales that occurred with increasing speed may be attributed to participants feeling the need to complete the task faster to keep up with the robot (as reported by some participants). Although this was only reported by some of the participants in casual ad-hoc manner, the finding does suggest a potential competitive element brought in that would differentiate between the lower speed settings and the highest speed setting. As shown in [32], this sense of competing with the robot displays differing effects on the person’s psychological wellbeing with respect to the robot attributes, when compared to collaborating. Although that study focused on changes in proximity when competing or collaborating, the findings can be used to illuminate potential causes for the changes in the workload subscales. The decrease in frustration suggests that speed below a certain value would be detrimental. Participants’ frustration was shown to have a negative relationship with speed, agreeing with the findings of [56]. However, whereas that study reported frustration as a result of confusion over the robot’s intent, the frustration in this study may have been due to participants feeling delayed in completing the task. At the highest speed, participants may have felt the urge to keep up with the robot and increased their effort in order to do this, but this was not a behaviour reciprocated by the robot whilst the participants were waiting for the robot. The increase in frustration at the lowest speed was verbally expressed by 10 participants in the post study question. It was also noted that during the task runs at lower speeds, more participants would lose focus on the task, and begin reading posters in the lab instead. This highlights the importance of developing a minimum speed for the robot to operate at as well, to ensure optimal focus and avoid distraction and potential injury.
Despite the increase in effort and temporal demand, participants did not report a change in their perceived performance with changing speed. However, the lack of relationship between perceived performance and speed may be attributed to the scale used and the simplicity of the task meaning that participants would always succeed (outside of robot error). Performance also lacked an objective measure and was therefore prone to subjectivity. Except for the first run, participants would consider performance a complete success unless a failure in the UR5 resulted in them being unable to complete the task. This is also reflected in participants reporting a high rate of performance (the scales in RTLX are flipped for performance, so a low score on RTLX indicates participants felt a high level of performance).
The findings for the workload and workload subscales indicate that more fine-tuned guidance, taking into consideration psychological factors, could further define the optimal robot’s speed so that it is not only safe for one’s physical integrity, but also optimal for one’s work efficiency and job satisfaction. The identification of a relationship within this envelope provides further justification for the need to better understand the psychological impacts on a person during HRC. This is further reinforced by findings in previous studies which provide links, direct and indirect, between a robot’s speed and the person’s workload.
Hypothesis 2
was not supported by the data. The relationship between proximity setting and workload being not significant is not supported by previous studies in workload [9] and other social psychological factors [28, 33, 34]. A possible cause for this was initially thought to be due to the participant’s ability to move freely in the collaborative workspace leading to the objective proximity being similar for both settings. This was demonstrated by analysis of the objective positional data of the participant’s head whilst both participant and robot were in the collaborative workspace. Whilst the robot was engaged in avoidance behaviour in the 0.3 m setting, participant’s heads were on average 0.1 m closer (in the x-direction, see Fig. 1) to the base of the robot than in the 0.2 m setting. However, the UR5 TCP only averaged a difference between the 2 settings of 0.03 m (in the x-direction), which may have been a result of the TCP reaching the avoidance limit that was put in place to prevent a joint limit violation. Despite this, the avoidance algorithm was able to maintain a distance above the proximity settings for 99.775% of the recorded data points whilst the robot was in the collaborative work area. Of note, the average distances for all settings are > 0.7 m, suggesting that the participants spend more time at a distance greater than the proximity setting, but the difference in head position as a result of proximity setting implies that they were still influenced by it.
The participants moving as a response to the robot would suggest there would be an increase in workload, such as in Stark et al., [10] as participants were devoting more resources to monitoring the robot than to completing the task. Therefore, participants may have devoted a similar level of resources to moving either towards or away from the robot. This would also agree with findings in [25] and [57] where an industrial robot arm entering the collaborative area increased workload. By entering the collaborative area, the distance was reduced between the robot and participant. This suggests a proximity threshold, where the workload is increased should the robot exceed a certain point but does not significantly change within that area, in a similar way to the Human-Human boundaries of proxemics [31]. A proximity threshold may explain not finding a significant interaction between proximity setting and workload in this study, as the distance between the proximities was not large enough to significantly influence the person’s workload. Another explanation may be supported by the findings in Walters et al., [35] where participants reported a higher ‘comfort’ when in control of the proximity. It may have been the case that the workload was not significantly different because the participants felt they were dictating the proximity more than the robot, despite objective data showing they adhered to the difference in proximity. This is supported by the UR5 having a maximum reach of 0.85m, enabling participants to move to a perceived safe distance without disengaging from the task. In the post experiment interview, four participants verbally reported feeling less comfortable when the robot was closer, and three participants stated they did not notice a difference in the proximity. As all these participants would have experienced the same conditions and been maintain the same distance away from the robot, this highlights the subjectivity of perceived proximity. Initially the experience of the participants was considered, however the reported experience by these participants was inconsistent with this reasoning. The findings in this study, along with the findings of previous studies, suggest that a threshold may exist for the proximity between the robot TCP and the person which can influence workload and that after crossing this threshold the workload of the person may not increase as long as they are able to dictate the distance within that area. This would be an area worth investigating in future studies, where workload is evaluated based on the person being able to control their proximity whilst completing a task.
Hypothesis 3
and Hypothesis 4, which put forward an influence on trust by speed and proximity setting, respectively, were not supported by the data, as trust remained consistently on the higher end of the scale. The high levels of trust are consistent with the task completion rate, where only 3.43% of the runs were not completed due to an error, none of which involved a collision. This is reflected in the high perceived performance mentioned previously. Of the failed runs, the majority were a result of the robot overcompensating to avoid a collision, resulting in a joint limit violation. The high levels of trust may also be attributed to the relatively small size and payload of the robot, and the low threat levels of the objects it was manipulating. This perceived low level of threat prompted one participant to ask why the PPE provided was necessary as they did not perceive that the robot could harm them. A lack of previous studies into direct changes in trust with robot speed and proximity setting limit conclusions that can be drawn. As with workload, it is possible that a threshold exists for the interaction between speed, proximity setting and trust. Future studies could examine the relationship between robot failure with speed and proximity setting, to determine if participants would experience lower trust in a faster moving/closer proximity robot after a failed task. The high trust may also be linked to the control over their position and of the release of the pipe by the robot. A future study where the robot exhibits greater autonomy may also provide greater insight into the relationship between robot attributes and trust.
One's experience with robots was considered a cofounding variable and was, as a result, measured. No significant difference in workload nor trust was found between the different levels of experience. The location, whether the participants were from the Samlesbury pool or the Cranfield pool, was added to the mixed model to account for the higher homogeneity within each group. The lack of significant relationship may be linked to the results found with experience. Firstly, despite the Samlesbury participants being primarily of an aircraft manufacturing background, they had similar levels of experience with robotics as those from the University (as expected from general trends in aircraft manufacturing highlighted in the literature). Secondly, it was found that the participant’s experience did not have a significant relationship with either workload or trust. A potential cause for this may be the wording in the survey, which asked for participant’s experience with a robot but not collaborating with a robot. Therefore, a participant may have put a few encounters with a robot but have not collaborated with a robot to complete a task. The results from this study still provide useful inferences, especially as the low experience in HRC reflects an industry wide level in aircraft manufacture. These low levels of experience also factor into an area of research which is even more limited in data, the effects of long-term interaction of HRC in industry. Changes in the interactive effects between the robot attributes and the person’s psychological attributes as the person gains more experience in HRC is an area which requires further investigation for successful implementation of the technology.
5 Conclusions
The main application for this research is in the development of guidance for improving psychological safety in industrial HRC. This study establishes that there are relationships between two key robot attributes and psychological measures that have been developed in other industrial processes with increasing automation but are lacking in HRC. As concepts such as workload and trust have been linked to a person’s performance, efficiency, and acceptance of automation [8, 17, 33, 58], an improved understanding of the influence of robot attributes on them is paramount. The changes in workload with speed are prevalent as they were significant despite the small size and low payload of the robot used. This study provides a basis for that understanding and establishes the existence of the psychological relationships for a robot acting under safe industrial HRC guidance. Further studies into the variables discussed would be beneficial to the field, especially in establishing a proximity setting threshold and further understanding trust in HRC. These studies would be further enhanced by developing an understanding of the effects of long-term interactions with industrial robots during HRC on a person’s workload and trust, as this has been significantly lacking in previous studies despite the increased purchases of collaborative robots.
Data Availability
The datasets generated during and/or analysed during the current study are available from the corresponding author on reasonable request.
References
World Robotics (2019) Executive summary -world robotics 2019 industrial robots
IFR (2020) Executive summary world robotics 2020 industrial robots
Villani V, Pini F, Leali F, Secchi C (2018) Survey on human-robot collaboration in industrial settings: safety, intuitive interfaces and applications. Mechatronics. https://doi.org/10.1016/j.mechatronics.2018.02.009
ISO (2011) ISO 10218 Robots and robotic devices - safety requirements for industrial robots, with parts I (‘Robots’) and 2 (‘Robot systems and integration’)
ISO (2016) ISO/TS 15066 - Collaborative robots: present status
Nonaka S, Inoue K, Arai T, and Mae Y (2004) Evaluation of human sense of security for coexisting robots using virtual reality. 1st report: evaluation of pick and place motion of humanoid robots. IEEE International Conference on Robotics and Automation, 2004. Proceedings. ICRA ’04. 2004, Vol. 3, pp. 2770–2775 https://doi.org/10.1109/ROBOT.2004.1307480
Sisbot EA, Marin LF, Alami R, and Simeon T (2006) A mobile robot that performs human acceptable motions. In IEEE International Conference on Intelligent Robots and Systems, pp 1811–1816 https://doi.org/10.1109/IROS.2006.282223
Charalambous G, Fletcher S, Webb P (2015) Identifying the key organisational human factors for introducing human-robot collaboration in industry: an exploratory study. Int J Adv Manuf Technol 81(9–12):2143–2155. https://doi.org/10.1007/s00170-015-7335-4
Tan JTC, Duan F, Zhang Y, Watanabe K, Kato R, and Arai T (2009) Human-robot collaboration in cellular manufacturing: Design and development. 2009 IEEE/RSJ International Conference on Intelligent Robots and Systems, pp 29–34 https://doi.org/10.1109/IROS.2009.5354155
Stark J, Mota RRC, and Sharlin E (2018) Personal space intrusion in human-robot collaboration. https://doi.org/10.1145/3173386.3176998
Story M, Jaksic C, Fletcher SR, Webb P, and Carberry J (2019) Evaluating the use of human aware navigation in industrial robot arms. In ICRES 2019: International Conference on Robot Ethics and Standards, pp 79–86
Cain B (2007) A review of the mental workload literature. No. 1998, 2007
Hart SG, Staveland LE (1988) Development of NASA-TLX (Task Load Index): results of empirical and theoretical research. Adv Psychol 52:139–183. https://doi.org/10.1016/S0166-4115(08)62386-9
Parasuraman R, Sheridan TB, Wickens CD (2008) Situation awareness, mental workload, and trust in automation: viable, empirically supported cognitive engineering constructs. J Cogn Eng Decision Making 2(2):140–160. https://doi.org/10.1518/155534308X284417
Yurko YY, Scerbo MW, Prabhu AS, Acker CE, Stefanidis D (2010) Higher mental workload is associated with poorer laparoscopic performance as measured by the NASA-TLX tool. Simul Healthcare 5(5):267–271. https://doi.org/10.1097/SIH.0b013e3181e3f329
Loft S, Sanderson P, Neal A, Mooij M (2007) Modeling and predicting mental workload in en route air traffic control: Critical review and broader implications. Hum Factors 49(3):376–399. https://doi.org/10.1518/001872007X197017
Gombolay M, Bair A, Huang C, Shah J (2017) Computational design of mixed-initiative human–robot teaming that considers human factors: situational awareness, workload, and workflow preferences. Int J Robot Res. https://doi.org/10.1177/0278364916688255
Shah SJ, Bliss JP, Chancey ET, Christopher Brill J (2015) Effects of alarm modality and alarm reliability on workload, trust, and driving performance. Proceed Human Factors Ergon Soc 2015(2008):1535–1539. https://doi.org/10.1177/1541931215591332
A. Steinfeld et al. (2006) Common metrics for human-robot interaction. HRI 2006: Proceedings of the 2006 ACM Conference on Human-Robot Interaction, vol. 2006, pp 33–40 https://doi.org/10.1145/1121241.1121249
Kaber DB, Onal E, Endsley MR (2000) Design of automation for telerobots and the effect on performance, operator situation awareness, and subjective workload. Human Factors Ergon Manuf 10(4):409–430. https://doi.org/10.1002/1520-6564(200023)10:4%3c409::aid-hfm4%3e3.0.co;2-v
Shibata S, Inooka H (1998) Psychological evaluations of robot motions. Int J Ind Ergon 21(6):483–494. https://doi.org/10.1016/S0169-8141(97)00004-8
Dautenhahn K, Woods S, Kaouri C, Walters ML, Koay KL, and Werry I (2005) What is a robot companion - friend, assistant ot butler?
Lauckner M, Kobiela F, and Manzey D (2014) Hey robot, please step back!’- Exploration of a spatial threshold of comfort for human-mechanoid spatial interaction in a hallway scenario. IEEE RO-MAN 2014 - 23rd IEEE International Symposium on Robot and Human Interactive Communication: Human-Robot Co-Existence: Adaptive Interfaces and Systems for Daily Life, Therapy, Assistance and Socially Engaging Interactions, pp 780–787, https://doi.org/10.1109/ROMAN.2014.6926348
Sardar A, Joosse M, Weiss A, and Evers V (2012) Don’t stand so close to me: Users’ attitudinal and behavioral responses to personal space invasion by robots. HRI’12 - Proceedings of the 7th Annual ACM/IEEE International Conference on Human-Robot Interaction, pp 229–230 https://doi.org/10.1145/2157689.2157769
Johnson TL, Fletcher SR, and Kutka R (2019) Understanding how proximity to a robot affects perceived workload. pp 29–30
Walton M (2013) In the context of wing equipping – A framework for safeguarding direct cooperation between high load, industrial robots and human operators. Cranfield University
Finomore VS Jr. (2008) Workload and stress measurements in the study of sustained attention
Butler JT, Agah A (2001) Psychological effects of behavior patterns of a mobile personal robot. Auton Robot 10(2):185–202. https://doi.org/10.1023/A:1008986004181
Kulic D, and Croft E (2005) Anxiety detection during human-robot interaction. 2005 IEEE/RSJ International Conference on Intelligent Robots and Systems, IROS, pp 389–394 https://doi.org/10.1109/IROS.2005.1545012
Koppenborg M, Nickel P, Naber B, Lungfiel A, Huelke M (2017) Effects of movement speed and predictability in human–robot collaboration. Human Factors Ergon Manuf 27(4):197–209. https://doi.org/10.1002/hfm.20703
Hall ET (1996) The hidden dimension: man’s use of space in public and private
Kim Y, Mutlu B (2014) How social distance shapes human-robot interaction. Int J Hum Comput Stud 72(12):783–795. https://doi.org/10.1016/j.ijhcs.2014.05.005
Lasota PA, Shah JA (2015) Analyzing the effects of human-aware motion planning on close-proximity human-robot collaboration. Hum Factors 57(1):21–33. https://doi.org/10.1177/0018720814565188
MacArthur KR, Stowers K, Hancock PA (2017) Human-robot interaction: proximity and speed—slowly back away from the robot! Adv Human Factors Robots Unmanned Syst 499:365–374. https://doi.org/10.1007/978-3-319-41959-6
Walters ML et al. (2005) The influence of subjects’ personality traits on predicting comfortable human-robot approach distances. Proceedings of COGSCI 2005 Workshop, pp 29–37 https://doi.org/10.1109/ROMAN.2005.1513803
Takayama L, and Pantofaru C (2009) Influences on proxemic behaviors in human-robot interaction. In 2009 IEEE/RSJ International Conference on Intelligent Robots and Systems, IROS 2009. No. 2009, pp 5495–5502 https://doi.org/10.1109/IROS.2009.5354145
Obaid M, Sandoval EB, Zlotowski J, Moltchanova E, Basedow CA, and Bartneck C (2016) Stop! That is close enough. How body postures influence human-robot proximity. 25th IEEE International Symposium on Robot and Human Interactive Communication, RO-MAN 2016. pp 354–361 https://doi.org/10.1109/ROMAN.2016.7745155
Ratsamee P, Mae Y, Ohara K, Takubo T, Arai T (2013) Human–robot collision avoidance using a modified social force model with body pose and face orientation. Int J Humanoid Rob 10(01):1350008. https://doi.org/10.1142/S0219843613500084
Stanton NA, Young MS (2006) Automatic intelligent cruise control. J Intell Syst 15(1–4):357–387. https://doi.org/10.1515/JISYS.2006.15.1-4.357
Estes S (2015) The workload curve: subjective mental workload. Hum Factors 57(7):1174–1187. https://doi.org/10.1177/0018720815592752
Reid GB, Shingledecker CA, and Eggemeier FT (1981) Application of conjoint measurement to workload scale development. In Proceedings of the Human Factors Society Annual Meeting, pp 522–526
Rubio S, Díaz E, Martín J, Puente JM (2004) Evaluation of subjective mental workload: a comparison of SWAT, NASA-TLX, and workload profile methods. Appl Psychol 53(1):61–86. https://doi.org/10.1111/j.1464-0597.2004.00161.x
Hill SG, Iavecchia HP, Byers JC, Bittner AC, Zaklad AL, Christ RE (1992) Comparison of four subjective workload rating scales. Hum Factors 34(4):429–439. https://doi.org/10.1177/001872089203400405
Hart SG (1986) NASA Task load Index (TLX). Volume 1.0; Paper and pencil package. https://doi.org/10.1016/j.apcatb.2004.05.003
Hart SG (2006) Nasa-Task Load Index (NASA-TLX); 20 years later. Proceed Human Factors Ergon Soc Annu Meet 50(9):904–908. https://doi.org/10.1177/154193120605000909
Lee JD, See KA (2004) Trust in automation: designing for appropriate reliance. Hum Factors 46(1):50–80. https://doi.org/10.1518/hfes.46.1.50_30392
Chen M, Nikolaidis S, Soh H, Hsu D, and Srinivasa S (2018) Planning with trust for human-robot collaboration https://doi.org/10.1145/3171221.3171264
Salem M, Lakatos G, Amirabdollahian F, and Dautenhahn K (2015) Would you trust a (faulty) robot?. In Proceedings of the Tenth Annual ACM/IEEE International Conference on Human-Robot Interaction - HRI ’15. pp 141–148 https://doi.org/10.1145/2696454.2696497
Freedy A, DeVisser E, Weltman G, and Coeyman N (2007) Measurement of trust in human-robot collaboration. In Proceedings of the 2007 International Symposium on Collaborative Technologies and Systems, CTS, pp. 106–114 https://doi.org/10.1109/CTS.2007.4621745
Hussein A, Elsawah S, Abbass HA (2020) Trust mediating reliability-reliance relationship in supervisory control of human-swarm interactions. Hum Factors 62(8):1237–1248. https://doi.org/10.1177/0018720819879273
Hancock PA, Billings DR, Schaefer KE, Chen JYC, De Visser EJ, Parasuraman R (2011) A meta-analysis of factors affecting trust in human-robot interaction. Hum Factors 53(5):517–527. https://doi.org/10.1177/0018720811417254
Charalambous G, Fletcher S, Webb P (2016) The development of a scale to evaluate trust in industrial human-robot collaboration. Int J Soc Robot 8(2):193–209. https://doi.org/10.1007/s12369-015-0333-8
Krueger C, Tian L (2004) A comparison of the general linear mixed model and repeated measures ANOVA using a dataset with multiple missing data points. Biol Res Nurs 6(2):151–157. https://doi.org/10.1177/1099800404267682
Boisgontier MP, and Cheval B (2016) The anova to mixed model transition. Neuroscience and biobehavioral reviews, (vol. 68). Elsevier Ltd, pp. 1004–1005 https://doi.org/10.1016/j.neubiorev.2016.05.034
Shi D, Collins EG, Donate A, Liu X, Goldiez B, and Dunlap D (2008) Human-aware robot motion planning with velocity constraints. In 2008 International Symposium on Collaborative Technologies and Systems, CTS’08. pp. 490–497 https://doi.org/10.1109/CTS.2008.4543969.
Severinson-Eklundh K, Green A, Hüttenrauch H (2003) Social and collaborative aspects of interaction with a service robot. Robot Auton Syst 42(3–4):223–234. https://doi.org/10.1016/S0921-8890(02)00377-9
Walton M (2013) In the context of wing equipping—A framework for safeguarding direct cooperation between high load, industrial robots and human operators
Weinrich CH, Volkhardt M, Einhorn E, and Gross HM (2013) Prediction of human avoidance behavior by lifelong learning for socially compliant robot navigation. In Systems, Man, and Cybernetics (SMC), 2013 IEEE International Conference on. no. Icra, pp 376–381 https://doi.org/10.1109/ICRA.2013.6630603
Acknowledgements
The research is funded by EPSRC Centre for Innovative Manufacturing and Intelligent Automation and BAE Systems
Funding
This study was funded an EPSRC BAE Systems Case Award.
Author information
Authors and Affiliations
Corresponding author
Ethics declarations
Conflict of interest
The authors declare they have no conflict of interest.
Informed Consent/Research Involving Human Participants
The study was conducted in accordance with the General Data Protection Regulation 2018, with data fully anonymized during processing. A risk assessment was conducted for the study and was granted ethical approval by Cranfield University. Participants were provided with a bump cap and safety glasses to ensure their protection. This research complied with the American Psychological Association Code of Ethics and was approved by the Institutional Review Board at Cranfield University.
Additional information
Publisher's Note
Springer Nature remains neutral with regard to jurisdictional claims in published maps and institutional affiliations.
Rights and permissions
Open Access This article is licensed under a Creative Commons Attribution 4.0 International License, which permits use, sharing, adaptation, distribution and reproduction in any medium or format, as long as you give appropriate credit to the original author(s) and the source, provide a link to the Creative Commons licence, and indicate if changes were made. The images or other third party material in this article are included in the article's Creative Commons licence, unless indicated otherwise in a credit line to the material. If material is not included in the article's Creative Commons licence and your intended use is not permitted by statutory regulation or exceeds the permitted use, you will need to obtain permission directly from the copyright holder. To view a copy of this licence, visit http://creativecommons.org/licenses/by/4.0/.
About this article
Cite this article
Story, M., Webb, P., Fletcher, S.R. et al. Do Speed and Proximity Affect Human-Robot Collaboration with an Industrial Robot Arm?. Int J of Soc Robotics 14, 1087–1102 (2022). https://doi.org/10.1007/s12369-021-00853-y
Accepted:
Published:
Issue Date:
DOI: https://doi.org/10.1007/s12369-021-00853-y