Abstract
For simultaneous and quantitative thermophysical measurements of ultrasmall liquid volumes, we have recently developed and reported heated fluidic resonators (HFRs). In this paper, we improve the precision of HFRs in a vacuum by significantly reducing the thermal loss around the sensing element. A vacuum chamber with optical, electrical, and microfluidic access is custom-built to decrease the convection loss by two orders of magnitude under 10-4 mbar conditions. As a result, the measurement sensitivities for thermal conductivity and specific heat capacity are increased by 4.1 and 1.6 times, respectively. When differentiating between deionized water (H2O) and heavy water (D2O) with similar thermophysical properties and ~10% different mass densities, the signal-to-noise ratio (property differences over standard error) for H2O and D2O is increased by 9 and 5 times for thermal conductivity and specific heat capacity, respectively.

Similar content being viewed by others
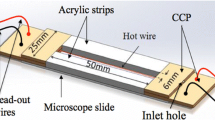
Introduction
Thermophysical properties (e.g., thermal conductivity and heat capacity) of liquids are relevant to numerous applications, including thermal management of high-power electronic devices1, energy storage/harvesting systems2, and photothermal therapies3. There have been continuous efforts to measure thermophysical properties with microfluidics-integrated sensors4,5,6 that offer the advantages of fast response time and low sample consumption. Since most microfluidic platforms for thermophysical property measurements are not equipped with direct volume or mass measurements, their measurement results tend to be extensive and thus proportional to sample quantity. To integrate thermal sensing with gravimetric sensing metrology7,8,9,10, we recently introduced simultaneous, fast, and precise thermophysical property measurements using heated fluidic resonators (HFRs)11. With HFR, three intensive properties—thermal conductivity, specific heat capacity, and density—are simultaneously obtained by resistive heating/thermometry and resonant densitometry.
To increase sensitivity in thermal sensing including calorimetry12,13, thermophysical property measurement14,15, or single-cell analysis16, there have been various studies that reduce convection loss by creating a vacuum environment around the microfluidic channel. The effect of minimizing convection loss is more significant in micro/nanostructures due to the scaling effect of heat transfer17, which indicates that convection coefficients tend to increase with decreasing characteristic dimensions. Since our previous report11 is based on the atmospheric pressure operation of HFRs, the performance of these devices can be improved by decreasing convection loss in a vacuum.
In this paper, we propose such advanced operation of HFRs in a vacuum to improve their performance during thermophysical property measurements. Minimizing convection loss in a vacuum causes more heat generation within the integrated heater to be dissipated by conduction through the liquid sample inside the integrated channel. Therefore, the temperature responses of HFRs during pulse heating with fixed power levels show higher contrast for different liquids and enhance the sensitivity of thermophysical property measurements. With a custom-built vacuum chamber, we thoroughly characterize and compare measurement variables–resistance, and resonance frequency–in atmospheric and vacuum pressures. We confirm that the vacuum operation of HFRs improves the sensitivity as well as the signal-to-noise ratio for thermophysical property measurements.
Methods
Heated fluidic resonators
HFRs are 500-µm long, 50-µm wide (16-µm of each channel), and 4-µm thick (3-µm channel height) suspended structures (MC516H, Life Analytical). The approach for mass sensing follows the procedure of previous liquid density measurements using a channel resonator18,19,20. As shown in Fig. 1a, HFRs are multilayered structures, where the thickness of each solid layer is optimized considering mass sensitivity and manufacturability. A doped and patterned polysilicon layer serves as a Joule heating electrode, and a silicon nitride layer is a fluidic channel structure and an electrical insulation layer between the channel and the heater. For thermal sensing, resistance is monitored in the time domain as resistive thermometry while a heating pulse is applied to the electrode, where an increase in resistance corresponds to an increase in temperature21. Steady-state resistance differences between the on and off states of the heating pulse and time constants of resistance at the rising edge are extracted to characterize the temperature response. Considering 30 ms of a pulse heating time as used previously11 and the increased time constant (~1 ms in atmospheric pressure) of HFR due to slowed thermal diffusion in a vacuum, pulse heating with 80-ms width and 160-ms period (50% duty) is used. A 3-mW amplitude and 3-mW DC offset are applied, which corresponds to 3 °C modulation at an average temperature of 27 °C in vacuum. Heat generation by Joule heating along the bottom heater surface is balanced with the sum of convection and conduction loss through the solid structure and liquid channel, as shown in the heat transfer diagram of the HFR (Fig. 1b). Different liquids inside the HFR change the conduction loss through the channel, resulting in a distinct temperature response at a fixed level of heating power. Figure 1c shows a scanning electron micrograph of the HFR with an integrated heater pseudocolored in red and a suspended fluidic channel pseudocolored in blue.
a 3D exploded view of a heated fluidic resonator (HFR). b Energy balance for HFR under joule heating in atmospheric and vacuum pressures. Convection loss becomes negligible in a vacuum. c Scanning electron micrograph of HFR with pseudocolored fluidic channel (blue) and heater (red). Scale bar is 100 µm. d A schematic illustration of the overall experimental setup and a photograph of the custom vacuum chamber for HFR with electrical and fluidic connections and vacuum port for advanced thermophysical property measurements with HFR in vacuum
Experimental setup with vacuum chamber
Thermophysical property measurement in a vacuum is performed with a custom vacuum chamber (Fig. 1d) that can control the environment to reduce the convective heat transfer coefficient around HFRs. The chamber is designed with fluid ports to transport liquid samples into the sensor, electrical connections for Joule heating and resistance measurements, and a transparent glass window that allows a laser to measure the resonance frequency (FC-2HVac, Life Analytical). To actuate the HFR, a piezoelectric chip (TA0505D024W, Thorlabs) is externally placed under the vacuum chamber. The chamber has an internal volume of ~0.2 mL and is connected by a vacuum pump (HiCube80, Pfeiffer Vacuum). Upon Joule heating pulses by a waveform generator (34401A, Keysight), the voltage and current are recorded simultaneously by a data acquisition module (USB-6361, National Instruments) using a voltage divider circuit to measure the resistance change over time. Inside the vacuum chamber, two pogo-pins, which are electrically insulated with chambers, are in direct contact with corresponding electrode pads, which are wired to the readout circuitry outside the chamber to ensure a stable electrical connection with negligible contact resistance (<0.1% of HFR resistance). The laser is focused on and reflected from the free end of the HFR and is monitored by a photodetector (S3096-02, Hamamatsu) to measure the resonance frequency. A phase-locked loop in a lock-in amplifier (HF2LI, Zurich Instruments) is used to record the resonance frequency in the time domain. A pressure regulator (ITV-0030, SMC) with an autosampler (MXX778, Rheodyne) is used to deliver liquid samples from small containers inside pressurized vials (50 kPa) into the HFR through 1/32-inch OD Teflon tubing. Microfluidic fittings (P-771, Upchurch) are used to connect the chamber with tubing. Details for the data acquisition have also been explained in the Supporting Information of our previous paper11.
Important variables
ΔR is the electrical resistance (R) difference between the highest and lowest levels at the steady state during square pulse heating with a 50% duty cycle. τ is the characteristic time response extracted by fitting resistance changes with the exponential decay function (\(R=A{{\rm {e}}}^{-\left(t-{t}_{0}\right)/\tau }+B\)), where A, B, and \({t}_{0}\) are constants. Δf is the difference in the time-averaged resonance frequency (f) under forced oscillation between the air-filled (f0) and specific liquid-filled HFR, simultaneously obtained with resistance monitoring.
Results and discussion
Characterization in vacuum
A comparison of the resistance (R) of HFR filled by an ethanol–water 50:50 binary mixture under atmospheric (~103 mbar) and vacuum pressures (10−4 mbar) is shown in Fig. 2a. Similar to the higher baseline of R in a vacuum environment, the resistance difference (ΔR) with the same heating power is higher in a vacuum due to the reduced convective heat loss. Another feature of operation in the vacuum environment is a long time constant (τ) due to slowed thermal diffusion. The distinct thermal behavior differences between the two environments occur due to the significant difference in the convective heat transfer coefficient for the HFR, which is expected to be ~1000 W/m2 K based on a comparative analysis of spatial temperature mapping between Raman thermometry and finite element analysis (FEA, Fig. S1). Such high heat transfer coefficients for microscale devices have been reported in theoretical17 and experimental22,23,24 works. In our recent reports25, we have characterized the temperature response in a vacuum by using FEA, as illustrated in Figs. S2 and S3.
a Resistance and b resonance frequency changes of HFR filled with the ethanol–water binary mixture (50:50 in volume) under 3-mW repeated heating pulses in atmospheric and vacuum pressures (~103 and 10−4 mbar, respectively). Gray dashed lines in a show 63% of steady-state levels which match with time constants. Gray dashed lines in b show the time-averaged resonance frequency of air-filled HFR and sample-filled HFR, with their differences denoted by Δfvac in vacuum and Δfamb in atmospheric pressure
Figure 2b shows the comparison of resonance frequency (f) simultaneously measured with Fig. 2a. The slowed thermal diffusion shown in Fig. 2a also leads to a reduced time response of f in vacuum. Resonance spectra of HFR filled with a 50% ethanol-water binary mixture in atmospheric and vacuum pressure environments are illustrated in Fig. S4, where the f is upshifted (~6.4 kHz) and the quality factor (Q-factor)26,27 is increased (~5.9 times, Fig. S5) in a vacuum because of reduced mechanical damping from the air, which increased the oscillation amplitude by a factor of ~2. Due to increased f and oscillation amplitude28, heat transfer is enhanced in a vacuum. In fact, heat transfer is reduced overall because the decrease in density of the surrounding medium that suppresses heat transfer exceeds the increase in dynamic oscillation. The stability of f represented by the Allan deviation29 is compared between atmospheric and vacuum pressures, as shown in Fig. S6, where the minimum value of the Allan deviation in a vacuum is decreased to one-fifth of the level recorded in atmospheric pressure.
Calibration of thermophysical properties
The changes in ΔR and τ of HFRs filled with six different liquids are observed in both vacuum and atmospheric pressure environments, as depicted in Fig. 3a and b, respectively. The increase in ΔR depends on the total thermal resistance of the HFR, which is related to the thermal conductivity (k) of the filled liquids. For measuring deionized water and ethanol binary mixtures, increasing the concentration of ethanol (which has a lower k than water) increases ΔR. In addition, the increase in τ depends on the total thermal capacitance of the HFR, which is related to the thermal mass or volumetric heat capacity (ρcp) of the filled liquids. Thus, increasing the concentration of ethanol reduces τ because ethanol has a lower ρcp than water. Considering the equivalent electrical circuit of a heat transfer system within the HFR (Fig. 1b), the total thermal resistance is calculated as the harmonic mean of the thermal resistances of heat conduction through a liquid sample and a solid structure of the HFR, while the total thermal capacitance is the sum of the thermal capacitance of the liquid and the solid structure. Thus, the total thermal capacitance is more dependent on the thermal properties of liquids than the thermal resistance, which results in a larger difference in τ than ΔR.
a Resistance differences and b time constants extracted from the transient resistance response for six different liquid samples (deionized water, ethanol, ethanol–water mixtures, and isopropanol). c Resistance differences (∆R) of HFR filled with various liquid samples as a function of thermal conductivity (k). d Resonance frequencies of HFR as a function of liquid mass density. Density sensitivities are indicated by gray-colored triangles positioned near the data points. e Time constant (τ) divided by ∆R (τ/∆R) as a function of volumetric heat capacity (ρcp, left) and its slope (right), and f τ/∆R divided by resonance frequency change (|∆f|) as a function of specific heat capacity (cp, left) and its slope (right). All dashed lines are curve fits of measurement results by following theoretical relationship or dimensional analysis. All error bars represent standard errors from 800 measurements. All data are compared under atmospheric and vacuum pressures (~103 and 10−4 mbar, respectively)
To ensure measurement reliability, physical relationships between the measurement variables and thermophysical properties are obtained by dimensional analysis11, as depicted in the Supporting Information. From this analysis, we found that (1) ΔR = A/(k‒B) + C for k, (2) τ/ΔR = aρcp + b for volumetric heat capacity (ρcp), and (3) τ/ΔR/|Δf| = dcp + e for specific heat capacity (cp), where A, B, C, a, b, d, and e are calibration coefficients (see Fig. S7 for details). These coefficients are extracted by curve fitting (Levenberg‒Marquardt algorithm) of measurement variables, as shown in Fig. 3c–f, where the local standards of k and ρcp by the hot-disk method30,31 (TPS 3500, Hot Disk Instruments) with density (ρ) reference from the literature32 are used. To enhance the precision of measurement, the average value and standard error from 800-pulse repetitions are obtained for both calibration and subsequent measurements.
The sensitivity of k is defined as the 1st derivative of a fitting function for ΔR (Fig. 3c) and is represented as dΔR/dk in Fig. S8. Compared to the decreasing sensitivity with a high k range in atmospheric pressure, a relatively higher sensitivity (4.1 times in the range of deionized water) is retained in a vacuum. Moreover, the sensitivity of ρ, ρcp, and cp can be represented by their slope from linear function fits, where the sensitivity of ρ with f (Fig. 3d), ρcp with τ/ΔR (Fig. 3e), and cp with τ/ΔR/|Δf| (Fig. 3f) are increased by 1.1, 1.8, and 1.6 times in vacuum, respectively. The sensitivity difference between ρcp and cp occurs due to the multiplied ρ. For a microfluidic resonator, the ρ sensitivity is proportional to the mechanical stiffness of the structure (km) divided by the effective mass33 (meff). In a vacuum, the pressure difference between the surroundings and inside the channel can induce bulging34 in the direction of channel thickness, leading to an increase in km and meff. Among those factors, an increase in km is more dominant in the characteristics of the system and leads to an improvement in ρ sensitivity. On the other hand, frequency noise is related to f, km, and the Q-factor. In a vacuum, a decrease in the density of the surrounding air reduces viscous damping, which increases the Q-factor and reduces inertial mass, which increases f. Since normalized frequency noise is reduced by the increase in km, Q-factor, and f, theoretical ρ resolution is improved by considering both ρ sensitivity and normalized frequency noise. The cp sensitivity is proportional to τ/ΔR/|Δf|. All of the variables τ, ΔR, and |Δf|, are increased in a vacuum, and the dominant increase in τ enhances cp sensitivity. Since the temperature response of the HFR is affected by both thermophysical properties and the convective heat transfer coefficient, the convective heat transfer coefficient cannot be extracted solely by monitoring temperature changes over time. By comparison of ρcp sensitivity, where the heat transfer coefficient is the sole factor to change, with FEM (Fig. S3a), the heat transfer coefficient at 10−4 mbar is calculated to be 25 W/m2 K (gray-dashed line in Fig. S3b).
Thermophysical property measurements in vacuum
To compare the signal-to-noise ratio (SNR) or sensitivity of k, deuterium oxide (D2O) was chosen as a test material (Fig. 4a). D2O and deionized water (H2O) exhibit comparable k, falling within a range where the sensitivity to k is low in ambient measurements. The higher value of ΔR in D2O occurs due to its lower k than H2O, while the higher τ of D2O occurs due to its larger ρcp, and the lower f occurs due to its larger ρ than H2O. Thermophysical properties are extracted using the calibration curve in Fig. 3 and compared with local standards represented as dark-yellow solid (D2O) and dashed lines (H2O) in Fig. 4b. Since the noise of measurement variables shows less than ~10% difference between both environments, higher sensitivity in vacuum lowers the standard errors in thermophysical property measurements, as shown in Fig. 4b. Despite these improved measurement sensitivities in the vacuum, a comparison between the measurements and local standards does not always show a consistently better match (e.g., k and cp of H2O). The difference between the measurement results and the local standards is mainly attributed to the fact that the properties of H2O are near the upper limit of the liquid properties used for calibration. If SNR is defined as the difference between H2O and D2O divided by the standard error, then the vacuum shows enhanced SNRs of those three variables (9 times for thermal conductivity, 3 times for volumetric heat capacity, and 5 times for specific heat capacity) compared to the air environment, as shown in Fig. 4c. Table 1 summarizes the sensitivity, resolution, and accuracy data for three thermophysical property measurements of D2O. Figure S9 illustrates that our measurement volume, as well as the relative error between the local standards and measured values, reached a minimum when compared to previous reports on thermal property measurements using small liquid sample volumes. The only exception to this trend occurred when using the 3-omega method with a 1 µL sample volume, which requires a frequency sweep and long measurement time.
a Resistance difference (∆R), time constant (τ), and resonance frequency (f) of HFR filled with heavy water (D2O) and deionized water (H2O). b Measurement results of thermal conductivity (k), volumetric heat capacity (ρcp), and specific heat capacity (cp) of D2O and H2O. c Signal-to-noise ratio (SNR) of thermophysical property measurements. All data are compared in atmospheric and vacuum pressures (~103 and 10−4 mbar, respectively)
Conclusion
In this paper, we improve the performance of thermophysical property measurements using our recently reported heated fluidic resonators (HFRs) by operating them in a vacuum. The vacuum chamber is constructed to decrease convection loss around the HFR, resulting in a two-orders-of-magnitude reduction in the convective heat transfer coefficient from ~1000 W/m2 K (at ~103 mbar, atmospheric pressure) to 25 W/m2 K (at 10−4 mbar, partial vacuum pressure). The reduced thermal loss and slowed thermal diffusion in vacuum increase the differences in resistance and time constants recorded for the various liquid samples. As a result, the measurement sensitivities for all three intensive thermophysical properties reported here are increased by 4.1 times for thermal conductivity, 1.8 times for volumetric heat capacity, and 1.6 times for specific heat capacity. Based on their similar thermophysical properties, using H2O and D2O allowed us to show that the signal-to-noise ratios of thermal conductivity and specific heat capacity are increased by 9 and 5 times, respectively. Thus, we highlight the sensing performance of HFR with the lowest measurement error among the real-time thermophysical property measurement methods inside microfluidics and the importance of thermal loss management in micro/nanoscale sensors.
References
Ghanbarpour, M., Bitaraf Haghigi, E. & Khodabandeh, R. Thermal properties and rheological behavior of water based Al2O3 nanofluid as a heat transfer fluid. Exp. Therm. Fluid Sci. 53, 227–235 (2014).
Shin, D. & Banerjee, D. Enhanced thermal properties of SiO2 nanocomposite for solar thermal energy storage applications. Int. J. Heat Mass Transf. 84, 898–902 (2015).
Ren, Y., Yan, Y. & Qi, H. Photothermal conversion and transfer in photothermal therapy: from macroscale to nanoscale. Adv. Colloid Interface Sci. 308, 102753 (2022).
Choi, S. R. & Kim, D. Real-time thermal characterization of 12 nl fluid samples in a microchannel. Rev. Sci. Instrum. 79, 064901 (2008).
Park, B. K., Yi, N., Park, J. & Kim, D. Note: Development of a microfabricated sensor to measure thermal conductivity of picoliter scale liquid samples. Rev. Sci. Instrum. 83, 106102 (2012).
Paul, G., Chopkar, M., Manna, I. & Das, P. K. Techniques for measuring the thermal conductivity of nanofluids: a review. Renew. Sustain. Energy Rev. 14, 1913–1924 (2010).
Yun, M., Lee, I., Jeon, S. & Lee, J. Facile phase transition measurements for nanogram level liquid samples using suspended microchannel resonators. IEEE Sens. J. 14, 781–785 (2014).
Jiang, K. et al. Thermomechanical responses of microfluidic cantilever capture DNA melting and properties of DNA premelting states using picoliters of DNA solution. Appl. Phys. Lett. 114, 173703 (2019).
Khan, M. F. et al. Heat capacity measurements of sub-nanoliter volumes of liquids using bimaterial microchannel cantilevers. Appl. Phys. Lett. 108, 211906 (2016).
Maillard, D., De Pastina, A., Abazari, A. M. & Villanueva, L. G. Avoiding transduction-induced heating in suspended microchannel resonators using piezoelectricity. Microsyst. Nanoeng. 7, 34 (2021).
Ko, J., Khan, F., Nam, Y., Lee, B. J. & Lee, J. Nanomechanical sensing using heater-integrated fluidic resonators. Nano Lett. 22, 7768–7775 (2022).
Lee, W., Fon, W., Axelrod, B. W. & Roukes, M. L. High-sensitivity microfluidic calorimeters for biological and chemical applications. Proc. Natl Acad. Sci. USA 106, 15225–15230 (2009).
Hur, S., Mittapally, R., Yadlapalli, S., Reddy, P. & Meyhofer, E. Sub-nanowatt resolution direct calorimetry for probing real-time metabolic activity of individual C. elegans worms. Nat. Commun. 11, 2983 (2020).
Burg, T. P. et al. Weighing of biomolecules, single cells and single nanoparticles in fluid. Nature 446, 1066–1069 (2007).
Wang, X., Zhao, Q., Li, Z., Yang, S. & Zhang, J. Measurement of the thermophysical properties of self-suspended thin films based on steady-state thermography. Opt. Express 28, 14560 (2020).
Inomata, N., Toda, M. & Ono, T. Highly sensitive thermometer using a vacuum-packed Si resonator in a microfluidic chip for the thermal measurement of single cells. Lab. Chip 16, 3597–3603 (2016).
Peirs, J., Reynaerts, D. & van Brussel, H. Scale effects and thermal considerations for micro-actuators. In Proc. 1998 IEEE International Conference on Robotics and Automation Vol. 2, 1516–1521 (IEEE, 1998).
Son, S., Grover, W. H., Burg, T. P. & Manalis, S. R. Suspended microchannel resonators for ultralow volume universal detection. Anal. Chem. 80, 4757–4760 (2008).
Khan, M. F. et al. Online measurement of mass density and viscosity of pL fluid samples with suspended microchannel resonator. Sens. Actuators B Chem. 185, 456–461 (2013).
Lee, I., Park, K. & Lee, J. Precision density and volume contraction measurements of ethanol–water binary mixtures using suspended microchannel resonators. Sens. Actuators A Phys. 194, 62–66 (2013).
Lee, J. et al. Electrical, thermal, and mechanical characterization of silicon microcantilever heaters. J. Microelectromech. Syst. 15, 1644–1655 (2006).
Alam, M. T., Raghu, A. P., Haque, M. A., Muratore, C. & Voevodin, A. A. Structural size and temperature dependence of solid to air heat transfer. Int. J. Therm. Sci. 73, 1–7 (2013).
Park, K., Lee, J., Zhang, Z. M. & King, W. P. Frequency-dependent electrical and thermal response of heated atomic force microscope cantilevers. J. Microelectromech. Syst. 16, 213–222 (2007).
Wang, Z. L. & Tang, D. W. Investigation of heat transfer around microwire in air environment using 3ω method. Int. J. Therm. Sci. 64, 145–151 (2013).
Ko, J., Lee, B. J. & Lee, J. Advanced thermophysical properties measurements using heater-integrated fluidic resonators. In 2023 IEEE 36th International Conference on Micro Electro Mechanical Systems (IEEE MEMS) 111–114 (2023).
Ko, J., Lee, B. J. & Lee, J. Towards highly specific measurement of binary mixtures by tandem operation of nanomechanical sensing system and micro-Raman spectroscopy. Sens. Actuators B Chem. 367, 132133 (2022).
Burg, T. P., Sader, J. E. & Manalis, S. R. Nonmonotonic energy dissipation in microfluidic resonators. Phys. Rev. Lett. 102, 228103 (2009).
Kim, T., Ko, J. & Lee, J. Self-assembled silicon membrane resonator for high vacuum pressure sensing. Vacuum 201, 111101 (2022).
Cutler, L. S. & Searle, C. L. Some aspects of the theory and measurement of frequency fluctuations in frequency standards. Proc. IEEE 54, 136–154 (1966).
Gustavsson, M., Karawacki, E. & Gustafsson, S. E. Thermal conductivity, thermal diffusivity, and specific heat of thin samples from transient measurements with hot disk sensors. Rev. Sci. Instrum. 65, 3856–3859 (1994).
Hot Disk Instruments. https://www.hotdiskinstruments.com/products-services/instruments/tps-3500/.
Linstrom, P. J. & Mallard, W. G. The NIST Chemistry WebBook: A Chemical Data Resource on the Internet. J. Chem. Eng. Data 46, 1059–1063 (2001).
Martín-Pérez, A. & Ramos, D. Nanomechanical hydrodynamic force sensing using suspended microfluidic channels. Microsyst. Nanoeng. 9, 1–8 (2023).
Martín‐Pérez, A., Ramos, D., Tamayo, J. & Calleja, M. Nanomechanical molecular mass sensing using suspended microchannel resonators. Sensors 21, 3337 (2021).
Acknowledgements
This research was supported by National Research Foundation of Korea (NRF) grants funded by the Korean government (Ministry of Science and ICT) (NRF-2020R1A2C3004885). This work was also supported by the Technology Innovation Program (00144157, Development of Heterogeneous Multi-Sensor Micro-System Platform) funded by the Ministry of Trade, Industry & Energy (MOTIE, Korea). We would like to thank Dr. Khan and his company (Life Analytical Inc.) for their collaboration in the development of heated fluidic resonators (HFRs).
Author information
Authors and Affiliations
Contributions
J.K. conducted all experiments and analyzed the data under the supervision of J.L. and B.J.L. The manuscript was written by J.K. and J.L. with input from all authors. All authors have approved the final version of the manuscript.
Corresponding author
Ethics declarations
Conflict of interest
The authors declare no competing interests.
Supplementary information
Rights and permissions
Open Access This article is licensed under a Creative Commons Attribution 4.0 International License, which permits use, sharing, adaptation, distribution and reproduction in any medium or format, as long as you give appropriate credit to the original author(s) and the source, provide a link to the Creative Commons license, and indicate if changes were made. The images or other third party material in this article are included in the article’s Creative Commons license, unless indicated otherwise in a credit line to the material. If material is not included in the article’s Creative Commons license and your intended use is not permitted by statutory regulation or exceeds the permitted use, you will need to obtain permission directly from the copyright holder. To view a copy of this license, visit http://creativecommons.org/licenses/by/4.0/.
About this article
Cite this article
Ko, J., Lee, B.J. & Lee, J. Advanced operation of heated fluidic resonators via mechanical and thermal loss reduction in vacuum. Microsyst Nanoeng 9, 127 (2023). https://doi.org/10.1038/s41378-023-00575-3
Received:
Revised:
Accepted:
Published:
DOI: https://doi.org/10.1038/s41378-023-00575-3
- Springer Nature Limited