Abstract
A cryogenic deep drawing process was proposed for complex curved surface part forming with aluminum alloy friction stir welded (FSW) blanks. The experimental forming limit curves (FLCs) of AA2219 alloy FSW blanks were obtained using the Nakajima tests at -196 °C. The theoretical FLC of base metal (BM) and weld zone for the FSW blank were calculated by M-K theory, respectively. The limited drawing ratio (LDR) was tested by the deep drawing of the hemispherical bottom cylindrical parts, and the splitting behavior of the drawn-part at ultra-low temperature was accurately predicted using the numerical simulations combined with theoretical FLCs. It was found that the forming limits and LDR of the FSW blanks were improved at -196 °C, and the FLD0 and LDR reached to 0.27 and 1.90, respectively. The improved cryogenic deep drawability was attributed to hyper hardening and high plasticity of the FSW blanks, which help to transfer deformation and prevent localized deformation from splitting in weak deformation zone. Finally, three effective methods were further proposed to improve cryogenic formability of FSW blanks. The increased blank holder force can ensure the suppressed co-existence of wrinkling and splitting due to increased resistance to localized deformation ability during cryogenic deep drawing. The strain distribution between the weld and BM zone of the deep drawn parts was more uniform by isothermal condition. Furthermore, the cryogenic formability can be further improved for the FSW blank with an offset weld.

















Similar content being viewed by others
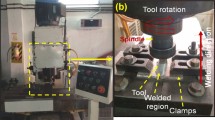
Abbreviations
- \({f_0}\) :
-
Initial thickness unevenness
- \(\bar {\varepsilon }\) :
-
Equivalent plastic strain
- \({\varepsilon _{2b}}\) :
-
Minor strain of weaker zone
- \({\sigma _{1b}}\) :
-
Major stress of weaker zone
- Δɛ 1a :
-
Major strain increment of stronger zone
- ρ :
-
Strain ratio
- K :
-
Strength coefficient
- r 0, r 45, r 90 :
-
Lankford coefficient
- φ :
-
Effective stress increment divided by major stress increment
- F, G, H, N :
-
Coefficient of Hill’s 1948 yield function
- β :
-
Effective strain increment divided by major strain
- \(\bar {\sigma }\) :
-
Equivalent stress
- \({\varepsilon _{2a}}\) :
-
Minor strain of stronger zone
- \({\sigma _{1a}}\) :
-
Major stress of stronger zone
- \({\varepsilon _3}\) :
-
Normal strain
- D 0 :
-
Initial blank diameter
- α :
-
Stress ratio
- n :
-
Strain hardening exponent
- \(\bar {r}\) :
-
True plastic strain ratio
References
Yuan S (2021) Fundamentals and processes of fluid pressure forming technology for complex thin-walled components. Engineering 7:358–366. https://doi.org/10.1016/j.eng.2020.08.014
Parente M, Safdarian R, Santos AD et al (2016) A study on the formability of aluminum tailor welded blanks produced by friction stir welding. Int J Adv Manuf Technol 83:2129–2141. https://doi.org/10.1007/s00170-015-7950-0
Zhang H, Zhan M, Zheng Z et al (2022) Forming dependence on spin roller paths for thin-walled complex components from 2195 Al-Li alloy TWBs. Int J Adv Manuf Technol 120:3113–3122. https://doi.org/10.1007/s00170-022-08974-y
Carlone P, Thuillier S, Andrade-Campos A et al (2021) Incremental forming of friction-stir welded aluminium blanks: an integrated approach. Int J Mater Form 14:1121–1137. https://doi.org/10.1007/s12289-021-01628-6
Abbasi M, Bagheri B, Abdollahzadeh A, Moghaddam AO (2021) A different attempt to improve the formability of aluminum tailor welded blanks (TWB) produced by the FSW. Int J Mater Form 14:1189–1208. https://doi.org/10.1007/s12289-021-01632-w
Fan X, Yuan S (2022) Innovation for forming aluminum alloy thin shells at ultra-low temperature by the dual enhancement effect. Int J Extrem Manuf 4:033001. https://doi.org/10.1088/2631-7990/ac6b62
Zheng K, Politis DJ, Wang L, Lin J (2018) A review on forming techniques for manufacturing lightweight complex—shaped aluminium panel components. Int J Light Mater Manuf 1:55–80. https://doi.org/10.1016/j.ijlmm.2018.03.006
Grabner F, Gruber B, Schlögl C, Chimani C (2018) Cryogenic sheet metal forming - An overview. Mater Sci Forum 941:1397–1403. https://doi.org/10.4028/www.scientific.net/MSF.941.1397
Zhang R, Shao Z, Lin J (2018) A review on modelling techniques for formability prediction of sheet metal forming. Int J Light Mater Manuf 1:115–125. https://doi.org/10.1016/j.ijlmm.2018.06.003
Ghoo BY, Park SW, Keum YT (2001) New forming limit diagram of laser tailored blank. J Strain Anal Eng Des 36:143–152. https://doi.org/10.1243/0309324011512694
Kumar G, Maji K (2022) Forming limit analysis of friction stir tailor welded AA5083 and AA7075 sheets in single point incremental forming. Int J Mater Form 15. https://doi.org/10.1007/s12289-022-01675-7
Zadpoor AA, Sinke J, Benedictus R (2008) Theoretical prediction of failure in forming of friction stir welded blanks. Int J Mater Form 1:305–308. https://doi.org/10.1007/s12289-008-0341-4
Kobayashi M, Kamada A, Terabayashi T, Asao H (1980) Press formability of face-centred cubic metals at cryogenic temperatures BT - Proceedings of the twentieth international machine tool design and research conference: Sub-conference on electrical processes. In: Tobias SA (ed). Palgrave Macmillan UK, London, pp 239–246
Wang C, Yi Y, Huang S et al (2021) Experimental and theoretical investigation on the forming limit of 2024-O aluminum alloy sheet at cryogenic temperatures. Met Mater Int 27:5199–5211. https://doi.org/10.1007/s12540-020-00922-3
Yuan S, Cheng W, Liu W (2021) Cryogenic formability of a solution-treated aluminum alloy sheet at low temperatures. J Mater Process Technol 298:117295. https://doi.org/10.1016/j.jmatprotec.2021.117295
Yuan S, Cheng W, Liu W, Xu Y (2020) A novel deep drawing process for aluminum alloy sheets at cryogenic temperatures. J Mater Process Technol 284:116743. https://doi.org/10.1016/j.jmatprotec.2020.116743
Schneider R, Grant RJ, Schlosser JM et al (2020) An investigation of the deep drawing behavior of automotive aluminum alloys at very low temperatures. Metall Mater Trans A 51:1123–1133. https://doi.org/10.1007/s11661-019-05584-4
Zadpoor AA, Sinke J, Benedictus R (2007) Mechanics of tailor welded blanks: An overview. Key Eng Mater 344:373–382
Bressan JD, Bruschi S, Ghiotti A (2016) Prediction of limit strains in hot forming of aluminium alloy sheets. Int J Mech Sci 115–116:702–710. https://doi.org/10.1016/j.ijmecsci.2016.07.040
Wang H, Yan Y, Han F, Wan M (2017) Experimental and theoretical investigations of the forming limit of 5754O aluminum alloy sheet under different combined loading paths. Int J Mech Sci 133:147–166. https://doi.org/10.1016/j.ijmecsci.2017.08.040
Li Z, Zhou G, Li D et al (2020) Forming limits of magnesium alloy AZ31B sheet at elevated temperatures. Int J Plast 135:102822. https://doi.org/10.1016/j.ijplas.2020.102822
Xiang N, Wang Z, Cai S (2018) Mechanism on increased sheet formability induced by tangential adhesive stress in sheet flexible forming process employing viscoplastic pressure-carrying medium. Int J Mach Tools Manuf 133:18–30. https://doi.org/10.1016/j.ijmachtools.2018.04.008
Chung K, Lee W, Kim D et al (2010) Macro-performance evaluation of friction stir welded automotive tailor-welded blank sheets: Part I - Material properties. Int J Solids Struct 47:1048–1062. https://doi.org/10.1016/j.ijsolstr.2009.12.022
Lee W, Chung KH, Kim D et al (2009) Experimental and numerical study on formability of friction stir welded TWB sheets based on hemispherical dome stretch tests. Int J Plast 25:1626–1654. https://doi.org/10.1016/j.ijplas.2008.08.005
Ramulu PJ, Narayanan RG (2011) Predicting the forming limit of friction stir welded blanks. AIP Conf Proc 1353:219–223. https://doi.org/10.1063/1.3589518
Ramulu PJ, Narayanan RG (2013) Experimental evaluation and prediction of forming limit of FSW blanks made of AA 6061 T6 sheets at different weld orientations and weld locations. Materwiss Werksttech 44:527–540. https://doi.org/10.1002/mawe.201300078
Cheng CH, Chan LC, Chow CL (2004) Experimental investigation on the weldability and forming behavior of aluminum alloy tailor-welded blanks. PICALO 2004–1st Pacific Int Conf Appl Laser. Opt Conf Proc 81:19–24. https://doi.org/10.2351/1.5056100
Saunders FI, Wagoner RH (1996) Forming of tailor-welded blanks. Metall Mater Trans A 27:2605–2616. https://doi.org/10.1007/BF02652354
Bandyopadhyay K, Basak S, Panda SK, Saha P (2015) Use of stress based forming limit diagram to predict formability in two-stage forming of tailor welded blanks. Mater Des 67:558–570. https://doi.org/10.1016/j.matdes.2014.10.089
Banabic D, Kami A, Comsa DS, Eyckens P (2021) Developments of the Marciniak-Kuczynski model for sheet metal formability: A review. J Mater Process Technol 287:116446. https://doi.org/10.1016/j.jmatprotec.2019.116446
Marciniak Z, Kuczyński K (1967) Limit strains in the processes of stretch-forming sheet metal. Int J Mech Sci 9:609–620. https://doi.org/10.1016/0020-7403(67)90066-5
Bleaney B, Penrose RP, Plumpton BI (1949) The theory of plane plastic strain for anisotropic metals. Proc R Soc London Ser A Math Phys Sci 198:428–437. https://doi.org/10.1098/rspa.1949.0110
Cheng W, Liu W, Yuan S (2019) Deformation behavior of Al–Cu–Mn alloy sheets under biaxial stress at cryogenic temperatures. Mater Sci Eng A 759:357–367. https://doi.org/10.1016/j.msea.2019.05.047
Cerri E, Leo P (2010) Warm and room temperature deformation of friction stir welded thin aluminium sheets. Mater Des 31:1392–1402. https://doi.org/10.1016/j.matdes.2009.08.044
Aydin H, Bayram A, Uǧuz A, Akay KS (2009) Tensile properties of friction stir welded joints of 2024 aluminum alloys in different heat-treated-state. Mater Des 30:2211–2221. https://doi.org/10.1016/j.matdes.2008.08.034
Hao Y, Liu W (2022) Analysis on exceptional cryogenic mechanical properties of AA2219 alloy FSW joints in multi-scale. Mater Sci Eng A 850:143489. https://doi.org/10.1016/j.msea.2022.143489
Wang X, Fan X, Chen X, Yuan S (2022) Forming limit of 6061 aluminum alloy tube at cryogenic temperatures. J Mater Process Technol 306:117649. https://doi.org/10.1016/j.jmatprotec.2022.117649
Li J, Nayak SS, Biro E et al (2013) Effects of weld line position and geometry on the formability of laser welded high strength low alloy and dual-phase steel blanks. Mater Des 52:757–766. https://doi.org/10.1016/j.matdes.2013.06.021
Riahi M, Amini A, Sabbaghzadeh J, Torkamany MJ (2012) Analysis of weld location effect and thickness ratio on formability of tailor welded blank. Sci Technol Weld Join 17:282–287. https://doi.org/10.1179/1362171812Y.0000000005
Narayanan RG (2015) Formability of friction stir welded sheets made of AA 6061-T6 at different weld orientations and weld locations Perumalla Janaki Ramulu Satish Vasu Kailas. Internatioanl J Mater Prod Technol 50:147–160
Bandyopadhyay K, Panda SK, Saha P, Padmanabham G (2015) Limiting drawing ratio and deep drawing behavior of dual phase steel tailor welded blanks: FE simulation and experimental validation. J Mater Process Technol 217:48–64. https://doi.org/10.1016/j.jmatprotec.2014.10.022
Acknowledgements
This research was funded by the National Natural Science Foundation of China (No. 51875125) and the National Key Research and Development Program of China (No. 2019YFA0708801).
Author information
Authors and Affiliations
Corresponding author
Ethics declarations
Ethical statements
The submission contains original research work and has been approved by all authors. The work presented in the manuscript has not been published previously.
Conflict of interest
The authors declare that they have no conflict of interest.
Additional information
Publisher’s note
Springer Nature remains neutral with regard to jurisdictional claims in published maps and institutional affiliations.
Rights and permissions
Springer Nature or its licensor (e.g. a society or other partner) holds exclusive rights to this article under a publishing agreement with the author(s) or other rightsholder(s); author self-archiving of the accepted manuscript version of this article is solely governed by the terms of such publishing agreement and applicable law.
About this article
Cite this article
Liu, W., Hao, Y., Sun, W. et al. Prediction for cryogenic formability of AA2219 alloy cylindrical parts with friction stir weld. Int J Mater Form 16, 4 (2023). https://doi.org/10.1007/s12289-022-01724-1
Received:
Accepted:
Published:
DOI: https://doi.org/10.1007/s12289-022-01724-1