Abstract
This paper provides a compact and efficient 167-line MATLAB code for thermoelastic topology optimization considering transient heat conduction, in view of designing structural components subjected to thermo-mechanical loads. The thermo-mechanical response is determined through finite-element modeling and discretized in time with an implicit finite difference scheme. A density-based topology optimization procedure is developed and applied to a standard compliance minimization problem extended with thermal boundary conditions. The sensitivity analysis is carried out by means of the adjoint variable method in combination with the discretize-then-differentiate approach for computational efficiency. The proposed methodology and its implementation in MATLAB are explained in detail. Furthermore, numerical examples are presented to demonstrate the influence of several parameters with respect to the thermo-mechanical loading and the transient heat conduction analysis. The results show that the thermo-mechanical load ratio significantly affects the optimized topology, as well as the thermal response time related to the transient thermal loading. Finally, the effect of the time-dependent loading is investigated based on a weighted formulation for the objective function to influence the optimization and to obtain a more mechanically or thermally optimized structure.
















Similar content being viewed by others
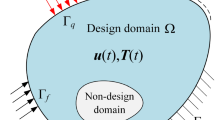
Data availability
The latest version of the developed code is available online at https://github.com/tcooms/TopOpt-ThermoElastic.
References
Stoiber N, Kromoser B (2021) Topology optimization in concrete construction: a systematic review on numerical and experimental investigations. Struct Multidiscip Optim 64(4):1725–1749. https://doi.org/10.1007/S00158-021-03019-6
Vantyghem G, De Corte W, Shakour E, Amir O (2020) 3D printing of a post-tensioned concrete girder designed by topology optimization. Autom Constr 112:103084. https://doi.org/10.1016/j.autcon.2020.103084
Jewett JL, Carstensen JV (2019) Topology-optimized design, construction and experimental evaluation of concrete beams. Autom Constr 102:59–67. https://doi.org/10.1016/J.AUTCON.2019.02.001
Bendsøe MP (1989) Optimal shape design as a material distribution problem. Struct Optim 1(4):193–202. https://doi.org/10.1007/BF01650949
Deaton JD, Grandhi RV (2014) A survey of structural and multidisciplinary continuum topology optimization: post 2000. Struct Multidiscip Optim 49(1):1–38. https://doi.org/10.1007/s00158-013-0956-z
Bendsøe M, Sigmund O (2003) Topology optimization: theory, methods and applications. Springer, Berlin
Bourdin B, Chambolle A (2003) Design-dependent loads in topology optimization. ESAIM Control Optim Calc Var 9:247–273. https://doi.org/10.1051/COCV:2002070/
de Kruijf N, Zhou S, Li Q, Mai Y-W (2007) Topological design of structures and composite materials with multiobjectives. Int J Solids Struct 44(22):7092–7109. https://doi.org/10.1016/j.ijsolstr.2007.03.028
Rodrigues H, Fernandes P (1995) A material based model for topology optimization of thermoelastic structures. Int J Numer Methods Eng 38(12):1951–1965. https://doi.org/10.1002/NME.1620381202
Diaz A, Benard A (2003) Topology optimization of heat-resistant structures. In: ASME 2003 international design engineering technical conferences and computers and information in engineering conference. https://doi.org/10.1115/DETC2003/DAC-48769
Gao T, Zhang W, Zhu J, Xu Y, Bassir D (2008) Topology optimization of heat conduction problem involving design-dependent heat load effect. Finite Elem Anal Des 44(14):805–813. https://doi.org/10.1016/j.finel.2008.06.001
Gao T, Zhang W (2010) Topology optimization involving thermo-elastic stress loads. Struct Multidiscip Optim 42(5):725–738. https://doi.org/10.1007/S00158-010-0527-5
Gao T, Xu P, Zhang W (2016) Topology optimization of thermo-elastic structures with multiple materials under mass constraint. Comput Struct 173:150–160. https://doi.org/10.1016/j.compstruc.2016.06.002
Zhu X, Zhao C, Wang X, Zhou Y, Hu P, Ma Z-D (2019) Temperature-constrained topology optimization of thermo-mechanical coupled problems. Eng Optim 51(10):1687–1709. https://doi.org/10.1080/0305215X.2018.1554065
Deaton JD, Grandhi RV (2013) Stiffening of restrained thermal structures via topology optimization. Struct Multidiscip Optim 48(4):731–745. https://doi.org/10.1007/s00158-013-0934-5
Hou J, Zhu J-H, Li Q (2016) On the topology optimization of elastic supporting structures under thermomechanical loads. Int J Aerosp Eng. https://doi.org/10.1155/2016/7372603
Ooms T, Vantyghem G, Thienpont T, Van Coile R, De Corte W (2022) Different approaches for topology optimization of building structures subjected to thermo-mechanical loads due to fire. In: ACSMO 2022, Asian congress of structural and multidisciplinary optimization 2022, proceedings, p 8. https://acsmo2022.org/
Iradukunda A-C, Vargas A, Huitink D, Lohan D (2020) Transient thermal performance using phase change material integrated topology optimized heat sinks. Appl Therm Eng 179:115723
Banthiya A, Ozguc S, Pan L, Weibel JA (2022) Topology optimization of an air-cooled heat sink for transient heat dissipation using a homogenization approach. In: 2022 21st IEEE intersociety conference on thermal and thermomechanical phenomena in electronic systems (iTherm), pp 1–7
Pizzolato A, Sharma A, Maute K, Sciacovelli A, Verda V (2017) Topology optimization for heat transfer enhancement in latent heat thermal energy storage. Int J Heat Mass Transf 113:875–888
Lohan DJ, Dede EM, Allison JT (2020) A study on practical objectives and constraints for heat conduction topology optimization. Struct Multidiscip Optim 61(2):475–489. https://doi.org/10.1007/S00158-019-02369-6
Wu S, Zhang Y, Liu S (2021) Transient thermal dissipation efficiency based method for topology optimization of transient heat conduction structures. Int J Heat Mass Transf 170:121004
Long K, Wang X, Gu X (2018) Multi-material topology optimization for the transient heat conduction problem using a sequential quadratic programming algorithm. Eng Optim 50(12):2091–2107
Zhao Q, Zhang H, Wang F, Zhang T, Li X (2021) Topology optimization of non-Fourier heat conduction problems considering global thermal dissipation energy minimization. Struct Multidiscip Optim 64(3):1385–1399. https://doi.org/10.1007/s00158-021-02924-0
Dbouk T (2017) A review about the engineering design of optimal heat transfer systems using topology optimization. Appl Therm Eng 112:841–854
Li Q, Steven GP, Xie YM (2001) Thermoelastic topology optimization for problems with varying temperature fields. J Therm Stress 24(4):347–366. https://doi.org/10.1080/01495730151078153
Li Y, Saitou K, Kikuchi N (2004) Topology optimization of thermally actuated compliant mechanisms considering time-transient effect. Finite Elem Anal Des 40(11):1317–1331
Madsen S, Lange NP, Giuliani L, Jomaas G, Lazarov BS, Sigmund O (2016) Topology optimization for simplified structural fire safety. Eng Struct 124:333–343. https://doi.org/10.1016/j.engstruct.2016.06.018
Hooijkamp E, van Keulen F (2017) Topology optimization for linear thermo-mechanical transient problems: modal reduction and adjoint sensitivities. Numer Methods Eng 113(8):1230–1257. https://doi.org/10.1002/nme.5635
Leader MK (2021) Stress-based topology optimization for steady-state and transient thermoelastic design. PhD thesis
Ogawa S, Yamada T (2022) Topology optimization for transient response problems involving thermoelastic materials. Finite Elem Anal Des 201:103695
Ogawa S, Yamada T (2022) Topology optimization for transient thermomechanical coupling problems. Appl Math Model 109:536–554
Chen J, Zhao Q, Zhang L, Ma K (2023) Topology optimization of transient thermo-elastic structure considering regional temperature control. Acta Mech Solid Sin. https://doi.org/10.1007/s10338-022-00377-6
Li S, Zhang Y, Liu S, Wu S (2023) Topology optimization of thermoelastic structures under transient thermal loads limited to stress constraints. Struct Multidiscip Optim 66(1):9
Ooms T, Vantyghem G, Thienpont T, Van Coile R, De Corte W (2023) Compliance-based topology optimization of structural components subjected to thermo-mechanical loading. Struct Multidiscip Optim 66(6):126. https://doi.org/10.1007/s00158-023-03563-3
Zienkiewicz OC, Taylor RL, Zhu JZ (2013) The finite element method: its basis and fundamentals. Butterworth-Heinemann, Oxford
Reddy JN, Gartling DK (2010) The finite element method in heat transfer and fluid dynamics, 3rd edn. CRC Press, Boca Raton
Logan DL (2016) A first course in the finite element method, 6th edn. Cengage Learning, Boston
Svanberg K (1987) The method of moving asymptotes—a new method for structural optimization. Int J Numer Methods Eng 24(2):359–373. https://doi.org/10.1002/nme.1620240207
Sigmund O (2007) Morphology-based black and white filters for topology optimization. Struct Multidiscip Optim 33(4):401–424. https://doi.org/10.1007/s00158-006-0087-x
Tortorelli DA, Michaleris P (1994) Design sensitivity analysis: Overview and review. Inverse Probl Eng 1(1):71–105. https://doi.org/10.1080/174159794088027573
Jensen JS, Nakshatrala PB, Tortorelli DA (2014) On the consistency of adjoint sensitivity analysis for structural optimization of linear dynamic problems. Struct Multidiscip Optim 49(5):831–837. https://doi.org/10.1007/s00158-013-1024-4
Günther-Hanssen O (2020) Topology optimization of transient thermo-mechanical problems using multiple materials (Master's dissertation). Lund University, Lund, Sweden
Lazarov BS, Wang F, Sigmund O (2016) Length scale and manufacturability in density-based topology optimization. Arch Appl Mech 86(1):189–218. https://doi.org/10.1007/s00419-015-1106-4
Andreassen E, Clausen A, Schevenels M, Lazarov BS, Sigmund O (2011) Efficient topology optimization in MATLAB using 88 lines of code. Struct Multidiscip Optim 43(1):1–16. https://doi.org/10.1007/s00158-010-0594-7
Wang F, Lazarov BS, Sigmund O (2011) On projection methods, convergence and robust formulations in topology optimization. Struct Multidiscip Optim 43(6):767–784. https://doi.org/10.1007/s00158-010-0602-y
Sigmund O (2022) On benchmarking and good scientific practise in topology optimization. Struct Multidiscip Optim 65(11):315. https://doi.org/10.1007/s00158-022-03427-2
Stolpe M, Svanberg K (2001) An alternative interpolation scheme for minimum compliance topology optimization. Struct Multidiscip Optim 22:116–124. https://doi.org/10.1007/s001580100129
Bruyneel M, Duysinx P (2005) Note on topology optimization of continuum structures including self-weight. Struct Multidiscip Optim 29(4):245–246. https://doi.org/10.1007/s00158-004-0484-y
Acknowledgements
The authors would like to thank Professor Krister Svanberg of the Royal Institute of Technology (KTH), Stockholm, for providing the MATLAB files for the MMA algorithm used in this study.
Funding
This research was supported by Ghent University.
Author information
Authors and Affiliations
Corresponding author
Ethics declarations
Conflict of interest
On behalf of all authors, the corresponding author states that there is no conflict of interest.
Additional information
Publisher's Note
Springer Nature remains neutral with regard to jurisdictional claims in published maps and institutional affiliations.
Electronic supplementary material
Below is the link to the electronic supplementary material.
Appendices
Appendix 1. Verification of the sensitivity analysis
The adjoint sensitivities, expressed by Eq. (29) in Sect. 3.3, are verified briefly according to [35]. The central finite difference scheme is used to calculate the numerical sensitivities, given by
The numerical sensitivities for a coarse mesh of \(30\times 10\) elements are compared to the corresponding analytical sensitivities in Fig. 17. Clearly, the maximum relative error of \(\mathcal{O}\left({10}^{-5}\right)\) between the numerical and analytical sensitivities can be considered negligible and this confirms the validity of the proposed sensitivities.
Appendix 2. A 167-line MATLAB code for thermoelastic topology optimization considering transient heat conduction


Appendix 3. Notes on the MATLAB implementation
In this appendix, several parts of the provided code in Appendix 2 are discussed. The MATLAB code is based on previous work of the authors [35], the steady-state variant top_tml_shc.m, which is an extension of the popular top88.m code by Andreassen et al. [45]. The focus of this section is on the additions and modifications to the above-mentioned codes and both references are highly recommended for a full understanding of the presented code.
3.1 Thermal FEA
A thermal analysis is added to the standard structural compliance minimization code developed by Andreassen et al. [45]. In line 5, the time increment \(\Delta t={t}_{f}/{t}_{N}\) is defined, followed by the mechanical and thermal properties in lines 6 and 7. In addition to the element thermal stiffness matrix \({{\varvec{K}}}_{th}^{e}\) prepared in lines 10–12, in case of transient heat conduction, the element capacity matrix \({{\varvec{C}}}^{e}\) is required as well, which is prepared in a similar format in lines 13–15. Furthermore, an additional variable Tini is declared in line 32 to reset the variables Told and Tnew in line 99 before the thermal analysis each iteration.
The density function and its first derivative for the material interpolation, as determined in Sect. 3.2, are written into a separate function MaterialInterpolation(x,M0,M1,pM) below the main code in lines 164–167, and reused for the interpolation of all material properties in lines 90–93. The inputs of the function are the density field \(\overline{{\varvec{x}} }\), the material properties \({M}_{0}\) and \({M}_{1}\), and the penalization factor \({p}_{M}\).
In lines 95–98, the global capacity matrix \({\varvec{C}}\) and global thermal stiffness matrix \({{\varvec{K}}}_{th}\) are assembled. Hereafter, in line 99, the necessary temperature and heat load vectors are initialized (or reset) for the thermal analysis in lines 101–105, which is carried out iteratively for all time steps. Similar to the steady-state variant in [35], this study imposes thermal Dirichlet conditions or fixed temperatures on the design domain as a thermal load case. Therefore, the matrix formulation of the thermal FEA is rewritten in function of free (unknown) and constrained (known) thermal DoFs for the calculation of the temperature field \({{\varvec{T}}}^{\left(t\right)}\)
where superscripts \(c\) and \(f\) indicate the constrained and free thermal DoFs, respectively. Double superscripts refer to the corresponding row and column indices of the coefficient matrices, respectively.
Furthermore, to calculate the temperature field \({{\varvec{T}}}^{\left(t\right)}\), Eq. (43) is rearranged to extract the unknown temperatures \({{{\varvec{T}}}^{f}}^{\left(t\right)}\) as a function of the temperatures from the previous time step \(t-1\)
This can be further simplified to
where the assumption is made that the thermal boundary conditions are constant in time, such that the temperature field \({{{\varvec{T}}}^{c}}^{\left(t\right)}\equiv {{{\varvec{T}}}^{c}}^{\left(t-1\right)}\).
As mentioned in Sect. 4.5, due to the linearity and more specifically the temperature-independency of the material properties, the first term between parentheses in Eq. (45), containing the coefficient matrices \({\varvec{C}}\) and \({{\varvec{K}}}_{th}\), only needs to be decomposed once every iteration, which is stored in a new variable dCK in line 100, using the decomposition() function. This variable is then reused in both line 103 and line 128 for significant speed improvements, especially for a large number of time steps. The linear system for the thermal analysis is solved in line 103, where Qnew is a temporary variable for the pseudo-heat load vector. Afterwards, in line 104, the variable Told is updated with the new temperature field Tnew and the latter is stored in the temperature matrix T.
3.2 Thermo-mechanical load vector
The implementation of the thermo-mechanical load vector is adapted from [35], but now accounts for the time-discretization. As a result, the temperature difference vectors \(\Delta {{\varvec{T}}}^{\left(t\right)}\) and thermo-mechanical load vectors \({{\varvec{F}}}_{th}^{\left(t\right)}\) are stored in matrices with \({t}_{N}+1\) columns, which are declared and pre-allocated in lines 51–52 as DT and Fth, respectively. Both matrices are calculated in lines 107–108, except for the first column that contains zeros due to the absence of thermal loading in time step \(t=0\). The constant part of the thermo-mechanical load vector is defined as Fth0 in line 8.
For an efficient implementation of the thermo-mechanical load vector and the sensitivity analysis afterwards, the element-temperature matrix \({{\varvec{T}}}_{T}\) and thermo-mechanical transformation matrix \({{\varvec{T}}}_{TM}\) were already introduced in [35]. The definitions of these matrices and their implementation allow for the extension to multiple temperature fields in matrix form.
3.3 Mechanical FEA
The mechanical FEA is prepared in lines 34–49. Importantly, the variables for the displacement matrix U and global load matrix F are pre-allocated with \({t}_{N}+1\) columns in lines 46–47. This allows for the calculation of the displacement fields \({{\varvec{U}}}^{\left(t\right)}\), as the response to the corresponding global load vectors \({{\varvec{F}}}^{\left(t\right)}\), for all time steps \(t\) as the solution of just 1 linear system in line 113. This method is similar to a problem with multiple load cases as discussed in [45].
3.4 Sensitivity analysis
The sensitivity analysis is implemented in lines 115–139. The necessary modifications for the implementation of weighted objective (see Sect. 4.4) are already implicitly included in the presented code.
The sensitivities determined in Eq. (29) are rewritten to facilitate the calculation of the different constituent terms. Both \(d{c}_{1}\) and \(d{c}_{2}\) are declared as matrices with \({t}_{N}+1\) columns for all time steps and pre-allocated as dc1 and dc2 in lines 57–58
where \(d{c}_{1}\) represents the first summation term of Eq. (29) and \(d{c}_{2}\) represents the second term, for which the subparts \(d{c}_{2}^{i}\) \(\left(i=a,b,c\right)\) with different coefficient matrices are separately calculated in lines 131–133, expressed as
In line 117, ct is defined as a vector containing the step compliances \({c}^{\left(t\right)}\) for all time steps \(t\). Afterwards, the first displacement field in step \(t=0\) is extracted in line 118 and then used for the calculation of the corresponding compliance \({c}^{\left(0\right)}\) in lines 119–120. The first contribution in \(d{c}_{1}\) is then computed in line 121 as it does not depend on \({{\varvec{\mu}}}^{\left(t\right)}\). The other contributions are calculated in line 130 in a similar manner.
The backward calculation of the adjoint variables \({{\varvec{\mu}}}^{\left(t\right)}\) is carried out in lines 123–135, starting from \(t={t}_{N}+1\to 2\). This allows for the calculation of \({dc}_{2}^{c}\) for which \({{\varvec{T}}}^{\left(t-1\right)}\) is required. In line 56, \({{\varvec{\mu}}}^{\left(t\right)}\) is declared and pre-allocated as a zero matrix mu with \({t}_{N}+2\) columns, where the last column always contains zeros in accordance with the expression for the adjoint variable in Eq. (27). For each time step, in line 124, the corresponding displacement and temperature fields are extracted from their respective matrices, which are defined in the previous sections. The remaining step compliances are calculated in lines 125–126. The pseudo-heat load vector \({{\varvec{Q}}}_{adj}^{\left(t\right)}\) for the adjoint problem, as expressed in Eq. (28), is calculated in line 127 and used in line 128 for the computation of the adjoint variable \({{\varvec{\mu}}}^{\left(t\right)}\). In line 129, the adjoint variable is stored in a temporary variable mui to apply indexing in lines 131–132. All three contributions to \(d{c}_{2}\) are cumulated and stored in dc2 in line 134. Finally, in lines 136–137, the total compliance \(c\) is determined and the sensitivities are calculated based on Eq. (46).
3.5 Replication of results
The presented results can be replicated with the developed MATLAB code in Appendix 2, albeit with the necessary modifications discussed in several sections. The MATLAB files mmasub.m and subsolv.m for implementing the MMA algorithm are freely available on http://www.smoptit.se/ under the GNU General Public License (GPLv3). One should reference them correctly in line 3 of the MATLAB code to carry out the optimization procedure. Furthermore, the mmasub.m file is modified, such that parameters move and asyinit are equal to 0.2 and 0.1, respectively.
The optimization procedure can then be executed by a command of the following form:

where the function variables directly refer to the parameters used in the paper.
For example, the optimization with default parameters can be solved using the following command:

Even though the results can be replicated by running the same code files with the exact set of parameter values, result may differ slightly based on the MATLAB version and the hardware used to run the optimizations.
The latest version of the developed code is available online at https://github.com/tcooms/TopOpt-ThermoElastic.
Rights and permissions
Springer Nature or its licensor (e.g. a society or other partner) holds exclusive rights to this article under a publishing agreement with the author(s) or other rightsholder(s); author self-archiving of the accepted manuscript version of this article is solely governed by the terms of such publishing agreement and applicable law.
About this article
Cite this article
Ooms, T., Vantyghem, G., Thienpont, T. et al. Thermoelastic topology optimization of structural components at elevated temperatures considering transient heat conduction. Engineering with Computers (2023). https://doi.org/10.1007/s00366-023-01907-7
Received:
Accepted:
Published:
DOI: https://doi.org/10.1007/s00366-023-01907-7