Abstract
Surface milling is an extensively adopted post-processing technique for the assembly of carbon fiber–reinforced polymers (CFRPs) with accurate surfaces. However, CFRPs are hard-to-cut materials due to their anisotropic and laminating characteristics that frequently induce machining damages, such as burrs and interface cracks. During surface milling, the action form at any point on the tool edge on the fiber changes with the rotation of the tool and the cutting tool feeding direction, resulting in varying levels of damage in different machining areas. To ensure the high milling quality of CFRP surfaces, this study established a planning method for cutting tool feed direction for low-damage machining by accounting for the changes in the tool edge and fiber action form during CFRP surface milling. The optimal cutting tool feed direction selection range for low-damage surface milling of CFRP components was determined by calculating the changes in the instantaneous fiber cutting angle and length for different cutting tool feed directions and then analyzing the influence of different cutting tool feed directions on the degree of processing damage of CFRP components. The results indicated that to reduce the burr and interfacial cracking damage in the surface milling of CFRP components, the cutting tool feed direction should be selected from the range 0°–40° relative to the fiber ply direction of the final cutting layer. The results obtained in this study can help determine the cutting tool feed direction for the low-damage surface milling of CFRP components and provide a basis for subsequent research on tool path planning.














Similar content being viewed by others
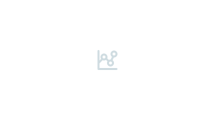
Data Availability
The raw/processed data required to reproduce these findings cannot be shared at this time as the data are part of an ongoing study.
References
Qi ZC, Liu Y, Chen WL (2019) An approach to predict the mechanical properties of CFRP based on cross scale simulation. Compos Struct 210:339–347
Rajak DK, Wagh PH, Linul E (2021) Manufacturing technologies of carbon/glass fiber-reinforced polymer composites and their properties: a review. Polymers 13(21):3721
Vicario AA, Shanmuga Ramanan SM, Arun S (2018) 3.4 composites in missiles and launch vehicles. In: Beaumont PWR, Zweben CH (eds) Comprehensive composite materials II. Elsevier, Oxford, pp 131–152
Wulfsberg J, Herrmann A, Ziegmann G, Lonsdorfer G, Stöß N, Fette M (2014) Combination of carbon 30 fibre sheet moulding compound and prepreg compression moulding in aerospace industry. Procedia Eng 81:1601–1607
Wang F, Gu T, Wang X, Jin X, Zhang B (2021) Analysis of burr and tear in milling of carbon fiber reinforced plastic (CFRP) using finite element method. Appl Compos Mater 28:991–1018
Zhang BY, Li Y, Wang FJ, Yang LL, Deng J, Lin YQ, He QS (2023) Machining inclination selection method for surface milling of CFRP workpieces with low cutting-induced damage. Composite Structures 304:13
Wang F, Li Y, Zhang B, Fan J, Yang L, Lin Y (2021) Influence of process parameters on material removal during surface milling of curved carbon fiber-reinforced plastic (CFRP) components: evaluated by a novel residual height calculation method. Int J Adv Manuf Technol 116:3405–3415
Kupski J, de Freitas ST (2021) Design of adhesively bonded lap joints with laminated CFRP adherends: review, challenges and new opportunities for aerospace structures. Compos Struct 268:113923
Liu GJ, Chen HY, Huang Z, Gao F, Chen T (2021) Surface quality of staggered PCD end mill in milling of carbon fiber reinforced plastics. Appl Sci 7(2):199
Wang FJ, Wang D, Yin JW, Yang F, Zhao M, Wang ZG (2019) Analysis of surface damage formation mechanism in milling of CFRPs. J Mech Eng 55:195–204
Wang CY, Liu GY, An QL, Chen M (2017) Occurrence and formation mechanism of surface cavity defects during orthogonal milling of CFRP laminates. Compos Part B Eng 2017(109):10–22
Jia ZY, Fu R, Niu B, Qian BW, Bai Y, Wang FJ (2016) Novel drill structure for damage reduction in drilling CFRP composites. Int J Mach Tool Manuf 110:55–65
Baraheni M, Amini S (2019) Comprehensive optimization of process parameters in rotary ultrasonic drilling of CFRP aimed at minimizing delamination. Int J Lightweight Mater Manuf 2(4):379–387
Yusuke K, Atsushi M, Iwao Y (2013) Optimization of cutting path for minimizing workpiece displacement at the cutting point: changing the material removal process, feed direction, and tool orientation. Procedia CIRP 5:31–36
Ma JW, Hu GQ, Jia ZY, Zhang N, Wang FJ (2018) Effect of geometric feature and cutting direction on variation of force and vibration in high-speed milling of TC4 curved surface. Int J Adv Manuf Technol 95(5):2207–2218
Suresh K, Yang DCH (1994) Constant scallop-height machining of free-form surfaces. J Eng Ind 116(2)
Mikó B, Varga B, Zębala W (2019) The effect of the feed direction on the micro- and macro accuracy of 3D ball-end milling of chromium-molybdenum alloy steel. Materials 12(24):4038
Zawada-Michałowska M, Kuczmaszewski J, Pieśko P (2020) Pre-machining of rolled plates as an element of minimising the post-machining deformations. Materials 13(21):4777
Hintze W, Hartmann D (2013) Modeling of delamination during milling of unidirectional CFRP. Procedia CIRP 8:444–449
Shchurov IA, Al-Taie LH (2017) Constant scallop-height tool path generation for ball-end mill cutters and three-axis CNC milling machines. Procedia Eng 206:1137–1141
Hintze W, Hartmann D, Schütte C (2011) Occurrence and propagation of delamination during the machining of carbon fibre reinforced plastics (CFRPs) - An experimental study. Compos Sci Technol 71(15):1719–1726
Amini S, Baraheni M, Mardiha A (2018) Parametric investigation of rotary ultrasonic drilling of carbon fiber reinforced plastics. Proc Institution Mech Eng 232:540–554
Funding
This work is supported by National Key R&D Program of China (Grant No. 2018YFA0702803); National Natural Science Foundation of China (Grant Nos. 52090053 and 52105432); Science and Technology Innovation Foundation of Dalian (Grant Nos. 2021RD08 and 2022JJ12GX027); Program: for Liaoning: Innovative Talents In University (XLYC1902014, XLYCYSZX1901); and Fundamental Research Funds for the Central Universities (Grant No. DUT21RC(3)002, DUT21ZD408).
Author information
Authors and Affiliations
Contributions
Fuji Wang and Lelin Yang conceived and designed the study. Lelin Yang and Yue Li performed the experiments. Yue Li and Jun Deng wrote the paper. Yongquan Lin, Qingsong He, and Rao Fu reviewed and edited the manuscript. All authors read and approved the manuscript.
Corresponding author
Ethics declarations
Ethical approval
Not applicable.
Consent to participate
Not applicable.
Consent for publication
The authors confirm that the manuscript has not been published or presented elsewhere in part or in entirety and is not under consideration by another journal. The responsible authorities at the institution where the work was conducted have provided their approval as well.
Conflict of interest
The authors declare no competing interests.
Additional information
Publisher’s note
Springer Nature remains neutral with regard to jurisdictional claims in published maps and institutional affiliations.
Rights and permissions
Springer Nature or its licensor (e.g. a society or other partner) holds exclusive rights to this article under a publishing agreement with the author(s) or other rightsholder(s); author self-archiving of the accepted manuscript version of this article is solely governed by the terms of such publishing agreement and applicable law.
About this article
Cite this article
Wang, F., Yang, L., Li, Y. et al. Planning of cutting tool feed direction for low-damage surface milling of CFRP: considering the changes in the action form of the tool edge on fiber. Int J Adv Manuf Technol 128, 5101–5116 (2023). https://doi.org/10.1007/s00170-023-12148-9
Received:
Accepted:
Published:
Issue Date:
DOI: https://doi.org/10.1007/s00170-023-12148-9