Abstract
The abrasion of the cutting edge by hard carbon fibers during machining of carbon fiber reinforced plastics (CFRP) causes severe tool wear. In this process, the tool wear volume exhibits a strong dependence on the cutting angle (the angle between the fiber orientation and cutting direction). In industrial applications, the perimeters of CFRP workpieces are frequently machined via contour milling. However, it is difficult to avoid cutting angles that cause rapid tool wear in this type of milling. This study proposes a novel rough milling strategy to maintain the cutting angles within a specific range by adjusting the tool feed direction and radial depth of cut to reduce tool wear. In addition, to implement the proposed method for CFRP machining, a software is developed to generate the tool path. The effectiveness of the proposed method for tool life extension during milling of CFRP is experimentally investigated.






















Similar content being viewed by others
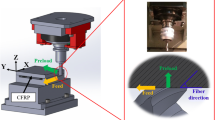
References
Fernández-Pérez, J., Díaz-Álvarez, J., Miguélez, M. H., & Cantero, J. L. (2021). Combined analysis of wear mechanisms and delamination in CFRP drilling. Composite Structures, 255,
Han, C., Kim, K. B., Lee, S. W., Jun, M. B. G., & Jeong, Y. H. (2021). Thrust Force-Based Tool wear estimation using Discrete Wavelet Transformation and Artificial neural network in CFRP Drilling. International Journal of Precision Engineering and Manufacturing, 22(9), 1527–1536.
Nor Khairusshima, M. K., Hassan, C., Jaharah, C. H., Amin, A. G., A. K. M., & Idriss, M., A. N (2013). Effect of chilled air on tool wear and workpiece quality during milling of carbon fibre-reinforced plastic. Wear, 302(1–2), 1113–1123.
Sheikh-Ahmad, J., & Sridhar, G. (2002). Edge trimming of CFRP composites with diamond coated tools: Edge wear and surface characteristics. SAE Transactions, 78–83.
Yan, C., Chen, Y., Qian, N., Guo, N., Wang, Y., Yang, H., & Zhao, B. (2022). Adaptive approaches to identify the interface in low frequency vibration-assisted drilling of CFRP/Ti6Al4V Stacks. International Journal of Precision Engineering and Manufacturing, 23(8), 895–909.
Wang, X., Kwon, P. Y., Sturtevant, C., Kim, D. D. W., & Lantrip, J. (2013). Tool wear of coated drills in drilling CFRP [Article]. Journal of Manufacturing Processes, 15(1), 127–135.
de Santana, M. I., & Polli, M. L. (2022). Effects of Tool Edge Preparation on Tool Life in Drilling of SAE4144M Steel. International Journal of Precision Engineering and Manufacturing, 23(10), 1113–1122.
Faraz, A., Biermann, D., & Weinert, K. (2009). Cutting edge rounding: An innovative tool wear criterion in drilling CFRP composite laminates. International Journal of Machine Tools and Manufacture, 49(15), 1185–1196.
Henerichs, M., Voß, R., Kuster, F., & Wegener, K. (2015). Machining of carbon fiber reinforced plastics: Influence of tool geometry and fiber orientation on the machining forces. CIRP Journal of Manufacturing Science and Technology, 9, 136–145.
Svinth, C. N., Wallace, S., Stephenson, D. B., Kim, D., Shin, K., Kim, H. Y., Lee, S. W., & Kim, T. G. (2022). Identifying abnormal CFRP Holes using both unsupervised and supervised learning techniques on In-Process force, current, and vibration signals. International Journal of Precision Engineering and Manufacturing, 23(6), 609–625.
Jia, Z., Bai, Y., Wang, F., & Hao, J. (2020). Effect of tool wear on drilling unidirectional CFRP laminates in different fiber cutting angles. The International Journal of Advanced Manufacturing Technology, 110(1), 89–99.
Teti, R. (2002). Machining of composite materials. CIRP Annals, 51(2), 611–634.
Wang, X. M., & Zhang, L. C. (2003). An experimental investigation into the orthogonal cutting of unidirectional fibre reinforced plastics. International Journal of Machine Tools and Manufacture, 43(10), 1015–1022.
Jin, F., Bao, Y., Li, B., & Jin, X. (2022). Tool wear prediction in edge trimming of carbon fiber reinforced polymer using machine learning with instantaneous parameters. Journal of Manufacturing Processes, 82, 277–295.
Qi, Z., Zhang, K., Cheng, H., Wang, D., & Meng, Q. (2015). Microscopic mechanism based force prediction in orthogonal cutting of unidirectional CFRP. International Journal of Advanced Manufacturing Technology, 79(5–8), 1209–1219.
Seeholzer, L., Kneubühler, F., Grossenbacher, F., & Wegener, K. (2021). Tool wear and spring back analysis in orthogonal machining unidirectional CFRP with respect to tool geometry and fibre orientation. International Journal of Advanced Manufacturing Technology, 115(9–10), 2905–2928.
Nguyen, D., Abdullah, B., Khawarizmi, M. S., Kim, R., D., & Kwon, P. (2020). The effect of fiber orientation on tool wear in edge-trimming of carbon fiber reinforced plastics (CFRP) laminates. Wear, 450–451, 203213.
Wang, C., Liu, G., An, Q., & Chen, M. (2017). Occurrence and formation mechanism of surface cavity defects during orthogonal milling of CFRP laminates. Composites Part B: Engineering, 109, 10–22.
Kim, M., Lee, M., Cho, G., & Lee, S. K. (2020). Effect of the Fiber orientation and the Radial depth of cut on the Flank wear in end milling of CFRP. International Journal of Precision Engineering and Manufacturing, 21(7), 1187–1199.
Mouritz, A. P. (2012). Introduction to aerospace materials. Elsevier.
Seo, J., Kim, D. Y., Kim, D. C., & Park, H. W. (2021). Recent Developments and Challenges on Machining of Carbon Fiber Reinforced Polymer Composite Laminates. International Journal of Precision Engineering and Manufacturing, 22(12), 2027–2044.
Held, M., Lukács, G., & Andor, L. (1994). Pocket machining based on contour-parallel tool paths generated by means of proximity maps. Computer-Aided Design, 26(3), 189–203.
Li, X., Liang, J., Ni, P., Wang, Y., Song, Y., & Tong, L. (2014). Novel path generation algorithm for high-speed pocket milling. International Journal of Production Research, 52(2), 397–404.
Park, S. C., & Choi, B. K. (2000). Tool-path planning for direction-parallel area milling. Computer Aided Design, 32(1), 17–25.
Fu, X., Song, K., Kim, D. M., Kang, Z., & Jun, M. B. G. (2022). Geometrical Simulation Model for Milling of Carbon Fiber Reinforced Polymers (CFRP). International Journal of Precision Engineering and Manufacturing, 23(11), 1237–1260.
Kim, G., Song, K., Jun, M. B. G., Jeong, Y. H., Kim, T. G., & Min, B. K. (2022). Effect of fiber bending induced matrix shear behavior on machined surface quality in carbon fiber reinforced plastic milling. Composite Structures, 287, 115343.
Liu, X., DeVor, R. E., & Kapoor, S. G. (2005). An Analytical Model for the prediction of Minimum Chip Thickness in Micromachining. Journal of Manufacturing Science and Engineering, 128(2), 474–481.
Popov, V. L. (2010). Contact mechanics and friction. Springer.
Acknowledgements
This work was funded by the Ministry of Trade, Industry and Energy (MOTIE), Republic of Korea (Grant Numbers 20012834 and 20018076). G. Kim was supported in part by the Yonsei University Research Fund (Post Doc. Researcher Supporting Program) of 2022 (Project Number: 2022-12-0038).
Author information
Authors and Affiliations
Corresponding author
Additional information
Publisher’s Note
Springer Nature remains neutral with regard to jurisdictional claims in published maps and institutional affiliations.
Rights and permissions
Springer Nature or its licensor (e.g. a society or other partner) holds exclusive rights to this article under a publishing agreement with the author(s) or other rightsholder(s); author self-archiving of the accepted manuscript version of this article is solely governed by the terms of such publishing agreement and applicable law.
About this article
Cite this article
Kim, G., Jo, H., Shin, J.S. et al. Tool Wear Reduction Using Directional Milling Considering Cutting Angle in Carbon fiber Reinforced Plastic Machining. Int. J. Precis. Eng. Manuf. 24, 1989–2008 (2023). https://doi.org/10.1007/s12541-023-00873-w
Received:
Revised:
Accepted:
Published:
Issue Date:
DOI: https://doi.org/10.1007/s12541-023-00873-w