Abstract
To produce high-purity Mg metal directly from MgO, the scale-up of a novel electrolytic process using a metal cathode and vacuum distillation was investigated. The electrolysis of MgO was conducted in MgF2–LiF molten salt using Cu or Ag cathode and graphite anode at 1053 K. The influence of the cathode metal and the concentration of Mg in the Mg alloy on the current efficiency was investigated. In addition, the interaction of Al2O3 in contact with the electrolyte and cathode was studied. When electrolysis was carried out with an applied current of 8.81–9.59 A for 75–95 h, Mg alloys such as Mg2Cu and MgAg were produced with a current efficiency of 82.2–88.0%. In addition, owing to the reaction between the Mg alloy and Al2O3, a dense layer of magnesium aluminum oxide was produced. Afterward, when the vacuum distillation of the Mg alloys was conducted at 1300 K, 99.9997% Mg metal was obtained.
Graphical Abstract













Similar content being viewed by others
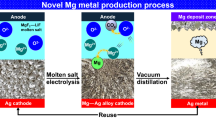
References
National Renewable Energy Laboratory (2010) Vehicle technologies program. U.S. Department of Energy. https://www.energy.gov/sites/prod/files/2014/03/f13/materials_tech_goals.pdf. Accessed 11 Jan 2021
Gray JE, Luan B (2002) Protective coatings on magnesium and its alloys—a critical review. J Alloys Compd 336:88–113
Roskill (2016) Magnesium metal: Global industry, markets and outlook to 2020. Roskill Information Services Ltd., London
Bray EL (2017) Magnesium [advance release] in metals and minerals. In: 2017 minerals yearbook, US geological survey, Reston, VA
Tauber M (2019) 2018 global primary magnesium supply and demand balance and outlook. In: 76th International Magnesium Association World Magnesium Conference, Budapest, 15–17 May 2019
Wada Y, Fujii S, Suzuki E, Maitani MM, Tsubaki S, Chonan S, Fukui M, Inazu N (2017) Smelting magnesium metal using a microwave pidgeon method. Sci Rep 7:46512
Pidgeon LM, Alexander WA (1944) Thermal production of magnesium—pilot plant studies on the retort ferrosilicon process. Trans Am Inst Min Met Eng 159:315–352
Friedrich HE, Mordike BL (2006) Magnesium technology: metallurgy, design data, appplications. Springer, Berlin
Kipouros GJ, Sadoway DR (1987) The chemistry and electrochemistry of magnesium production. In: Mamantov G, Mamantov CB, Braunstein J (eds) Advances in molten salt chemistry, vol 6. Elsevier, Amsterdam, pp 127–209
Kim JI, Nguyen HN, You BS, Kim YM (2019) Effect of Y addition on removal of Fe impurity from magnesium alloys. Scr Mater 162:355–360
Holcroft G (2018) Novel modular process to produce magnesium metal from serpentinite mine tailings. In: 75th international magnesium association world magnesium conference, New Orleans, 16–18 May 2018
Wallevik O, Kaasa OJ, Endal G (1988) Cathode for magnesium production. US Patent 4784742A, 1988
Sharma RA (1996) A new electrolytic magnesium production process. JOM 48:39–43
Leonard N, Korenko M, Larson C, Blood K, Venstrom LJ, Nudehi S, Duncan S, Diver R, Simko F, Priscak J, Schoer J, Kissinger PT, Palumbo R (2016) The thermal electrolytic production of Mg from MgO: a discussion of the electrochemical reaction kinetics and requisite mass transport processes. Chem Eng Sci 148:155–169
Yerkes LA (1942) Electrolytic method for producing magnesium alloys. US Patent 2431723A, 1942
Krishnan A, Lu XG, Pal UB (2005) Solid oxide membrane process for magnesium production directly from magnesium oxide. Metall Mater Trans B 36:463–473
Powell AC IV, Derezinski SJ III (2013) Primary production of elements. US Patent 8460535B2, 2013
Guan X, Pal UB, Powell AC (2014) Energy-efficient and environmentally friendly solid oxide membrane electrolysis process for magnesium oxide reduction: experiment and modeling. Metall Mater Trans E 1:132–144
Powell AC IV (2018) Final scientific/technical report of industrial scale-up of low-cost zero-emission magnesium by INFINIUM electrolysis. https://www.osti.gov/biblio/1431302. Accessed 11 Jan 2021
Lee TH, Okabe TH, Lee JY, Kim YM, Kang J (2020) Molten salt electrolysis of magnesium oxide using a liquid-metal cathode for the production of magnesium metal. Metall Mater Trans B 51:2993–3006
Lee TH, Okabe TH, Lee JY, Kim YM, Kang J (2021) Development of a novel electrolytic process for producing high-purity magnesium metal from magnesium oxide using a liquid tin cathode. J Magnes Alloy. https://doi.org/10.1016/j.jma.2021.01.004
Kim Y, Yoo J, Kang J (2020) Applicability of the electrochemical oxygen sensor for in-situ evaluation of MgO solubility in the MgF2-LiF molten salt electrolysis system. Metals 10:906
Kim Y, Kang J (2021) Viscosity of molten MgF2-LiF-MgO system and structure investigation using classical molecular dynamic simulations. J Non-Cryst Solids 552:120377
Barin I (1995) Thermochemical data of pure substances. VCH Verlagsgesellschaft mbH, Weinheim
Bale CW, Belisle E, Chartrand P, Decterov SA, Eriksson G, Gheribi AE, Hack K, Jung IH, Kang YB, Melancon J, Pelton AD, Petersen S, Robelin C, Sangster J, Spencer P, Van Ende MA (2016) Factsage thermochemical software and databases, 2010–2016. Calphad 54:35–53
Kang J, Okabe TH (2014) Thermodynamic consideration of the removal of iron from titanium ore by selective chlroination. Metall Mater Trans B 45:1260–1271
Takeda O, Uda T, Okabe TH (2014) Rare earth titanium group metals and reactive metals production. In: Seetharaman S (eds) Treatise on process metallurgy, vol 3. Elsevier, Amsterdam, pp 995–1069
Acknowledgements
The authors are grateful to Dr. DongEung Kim of the Korea Institute of Industrial Technology for the discussions throughout this study. In addition, the authors thank Dr. Jae-Yeol Yang, Dr. Jae-Sik Yoon, and Ms. Jiyoung Baek for their technical support. Furthermore, the authors are grateful to all the members of the Geoanalysis Department of KIGAM for their technical assistance. This research was supported by the National Research Council of Science & Technology (NST) grant by the Korea government (MSIT) (No.CRC-15-06-KIGAM).
Author information
Authors and Affiliations
Corresponding author
Ethics declarations
Conflict of interest
The authors declare that they have no conflict of interest.
Additional information
The contributing editor for this article was Hongmin Zhu.
Publisher's Note
Springer Nature remains neutral with regard to jurisdictional claims in published maps and institutional affiliations.
Supplementary Information
Below is the link to the electronic supplementary material.
Rights and permissions
About this article
Cite this article
Lee, DH., Jeoung, HJ., Lee, TH. et al. Scale-Up Study of Molten Salt Electrolysis using Cu or Ag Cathode and Vacuum Distillation for the Production of High-Purity Mg Metal from MgO. J. Sustain. Metall. 7, 883–897 (2021). https://doi.org/10.1007/s40831-021-00367-x
Received:
Accepted:
Published:
Issue Date:
DOI: https://doi.org/10.1007/s40831-021-00367-x