Abstract
The computational algorithm of a crystal-plastic-based FLD predictive model (VPSC-FLD) developed in Jeong et al. (Model Simul Mater Sci Eng, 2016. https://doi.org/10.1088/0965-0393/24/5/055005) is enhanced. A real-time monitor process runs while the forming limit diagram is calculated by parallel computation on various strain loading paths. The monitor process enables the CPU workers to communicate with each other so that the unnecessary model runs can be determined and terminated on the fly. Moreover, the advanced numerical algorithm suggested earlier by Schwindt et al. (Int J Plast 73:62–99, 2015. https://doi.org/10.1016/j.ijplas.2015.01.005) is implemented to VPSC-FLD. The new numerical algorithm and real-time monitor has improved both the overall computational speed and the efficiency in parallel computation. The enhanced VPSC-FLD model is applied for austenitic and ferritic stainless samples in terms of flow stress–strain curve, R-values, and forming limit diagram. The linearization scheme applied on the local constitutive description is studied to reveal its impacts on various macroscopic properties. It is found that the linearization scheme with the best fit on uniaxial data is not necessary the one that gives the best predictive accuracy on the forming limit prediction.










Similar content being viewed by others
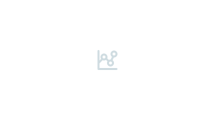
References
S. Keeler, W. Backhofen, Plastic instability and fracture in sheet stretched over rigid punches. ASM Trans. Q. 56, 25–48 (1964)
F. Abu-Farha, L.G. Hector, M. Khraisheh, Cruciform-shaped specimens for elevated temperature biaxial testing of lightweight materials. JOM 61, 48–56 (2009). https://doi.org/10.1007/s11837-009-0121-8
Y. Hanabusa, H. Takizawa, T. Kuwabara, Numerical verification of a biaxial tensile test method using a cruciform specimen. J. Mater. Process. Technol. 213, 961–970 (2013). https://doi.org/10.1016/j.jmatprotec.2012.12.007
J. Li, J.E. Carsley, T.B. Stoughton, L.G. Hector, S.J. Hu, Forming limit analysis for two-stage forming of 5182-O aluminum sheet with intermediate annealing. Int. J. Plast. 45, 21–43 (2013). https://doi.org/10.1016/j.ijplas.2012.10.004
A.F. Graf, W.F. Hosford, Calculations of forming limit diagrams for changing strain paths ALEJANDRO. Metall. Trans. A 24, 2497–2501 (1993). https://doi.org/10.1007/BF02646528
T.B. Stoughton, General forming limit criterion for sheet metal forming. Int. J. Mech. Sci. 42, 1–27 (2000). https://doi.org/10.1016/S0020-7403(98)00113-1
K. Yoshida, T. Kuwabara, M. Kuroda, Path-dependence of the forming limit stresses in a sheet metal. Int. J. Plast. 23, 361–384 (2007). https://doi.org/10.1016/j.ijplas.2006.05.005
Z. Marciniak, K. Kuczyński, T. Pokora, Influence of the plastic properties of a material on the forming limit diagram for sheet metal in tension. Int. J. Mech. Sci. 15, 789–800 (1973). https://doi.org/10.1016/0020-7403(73)90068-4
Y. Jeong, M.S. Pham, M. Iadicola, A. Creuziger, T. Foecke, Forming limit prediction using a self-consistent crystal plasticity framework: a case study for body-centered cubic materials. Model. Simul. Mater. Sci. Eng. (2016). https://doi.org/10.1088/0965-0393/24/5/055005
C. Schwindt, F. Schlosser, M.A. Bertinetti, M. Stout, J.W. Signorelli, Experimental and Visco-Plastic Self-Consistent evaluation of forming limit diagrams for anisotropic sheet metals: an efficient and robust implementation of the M-K model. Int. J. Plast 73, 62–99 (2015). https://doi.org/10.1016/j.ijplas.2015.01.005
F. Barlat, O. Richmond, Prediction of tricomponent plane stress yield surfaces and associated flow and failure behavior of strongly textured f.c.c. polycrystalline sheets. Mater. Sci. Eng. 95, 15–29 (1987). https://doi.org/10.1016/0025-5416(87)90494-0
K. Inal, K.W. Neale, A. Aboutajeddine, Forming limit comparisons for FCC and BCC sheets. Int. J. Plast. 21, 1255–1266 (2005). https://doi.org/10.1016/j.ijplas.2004.08.001
C. John Neil, S.R. Agnew, Crystal plasticity-based forming limit prediction for non-cubic metals: application to Mg alloy AZ31B. Int. J. Plast. 25, 379–398 (2009). https://doi.org/10.1016/j.ijplas.2008.05.003
J.S. Nagra, A. Brahme, R.K. Mishra, R.A. Lebensohn, K. Inal, An efficient full-field crystal plasticity-based M-K framework to study the effect of 3D microstructural features on the formability of polycrystalline materials. Model. Simul. Mater. Sci. Eng. (2018). https://doi.org/10.1088/1361-651X/aadc20
J.W. Signorelli, M.A. Bertinetti, P.A. Turner, Predictions of forming limit diagrams using a rate-dependent polycrystal self-consistent plasticity model. Int. J. Plast. 25, 1–25 (2009). https://doi.org/10.1016/j.ijplas.2008.01.005
H. Wang, P.D. Wu, K.P. Boyle, K.W. Neale, On crystal plasticity formability analysis for magnesium alloy sheets. Int. J. Solids Struct. 48, 1000–1010 (2011). https://doi.org/10.1016/j.ijsolstr.2010.12.004
P.D. Wu, K.W. Neale, E. Van Der Giessen, On crystal plasticity FLD analysis. Proc. R. Soc. A Math. Phys. Eng. Sci. 1, 2 (1997). https://doi.org/10.1098/rspa.1997.0099
K. Yoshida, T. Ishizaka, M. Kuroda, S. Ikawa, The effects of texture on formability of aluminum alloy sheets. Acta Mater. 55, 4499–4506 (2007). https://doi.org/10.1016/j.actamat.2007.04.014
K. Chung, H. Kim, C. Lee, Forming limit criterion for ductile anisotropic sheets as a material property and its deformation path insensitivity. Part I: deformation path insensitive formula based on theoretical models. Int. J. Plast. 58, 3–34 (2014). https://doi.org/10.1016/j.ijplas.2014.03.009
Q. Hu, L. Zhang, Q. Ouyang, X. Li, X. Zhu, J. Chen, Prediction of forming limits for anisotropic materials with nonlinear strain paths by an instability approach. Int. J. Plast. 103, 143–167 (2018). https://doi.org/10.1016/j.ijplas.2018.01.006
M. Kuroda, V. Tvergaard, Forming limit diagrams for anisotropic metal sheets with different yield criteria. Int. J. Solids Struct. 37, 5037–5059 (2000). https://doi.org/10.1016/S0020-7683(99)00200-0
J. Lian, F. Shen, X. Jia, D.C. Ahn, D.C. Chae, S. Münstermann, W. Bleck, An evolving non-associated Hill48 plasticity model accounting for anisotropic hardening and r-value evolution and its application to forming limit prediction. Int. J. Solids Struct. 151, 20–44 (2017). https://doi.org/10.1016/j.ijsolstr.2017.04.007
L. Zhang, J. Wang, Modeling the localized necking in anisotropic sheet metals. Int. J. Plast. 39, 103–118 (2012). https://doi.org/10.1016/j.ijplas.2012.05.005
J.W. Hutchinson, K.W. Neale, Sheet Necking-II. Time-independent behavior. Mech. Sheet Met. Form. (2011). https://doi.org/10.1007/978-1-4613-2880-3_6
J.W. Hutchinson, K.W. Neale, Sheet Necking-III. Strain-rate effects. Mech. Sheet Met. Form. (2011). https://doi.org/10.1007/978-1-4613-2880-3_11
A. Gupta, M. Ben Bettaieb, F. Abed-Meraim, S.R. Kalidindi, Computationally efficient predictions of crystal plasticity based forming limit diagrams using a spectral database. Int. J. Plast. 103, 168–187 (2018). https://doi.org/10.1016/j.ijplas.2018.01.007
D. Steglich, Y. Jeong, Texture-based forming limit prediction for Mg sheet alloys ZE10 and AZ31. Int. J. Mech. Sci. 117, 102–114 (2016). https://doi.org/10.1016/j.ijmecsci.2016.08.013
R.A. Lebensohn, C.N. Tomé, A self-consistent anisotropic approach for the simulation of plastic deformation and texture development of polycrystals: application to zirconium alloys. Acta Metall. Mater. 41, 2611–2624 (1993). https://doi.org/10.1016/0956-7151(93)90130-K
J.W. Hutchinson, Bounds and self-consistent estimates for creep of polycrystalline materials. Proc. R. Soc. A Math. Phys. Eng. Sci. 348, 101–127 (2006). https://doi.org/10.1098/rspa.1976.0027
C. Tome, G.R. Canova, U.F. Kocks, N. Christodoulou, J.J. Jonas, The relation between macroscopic and microscopic strain hardening in F.C.C. polycrystals. Acta Metall. 32, 1637–1653 (1984). https://doi.org/10.1016/0001-6160(84)90222-0
C.N. Tomé, Self-consistent polycrystal models: a directional compliance criterion to describe grain interactions. Model. Simul. Mater. Sci. Eng. 7, 723–738 (1999). https://doi.org/10.1088/0965-0393/7/5/305
Y. Jeong, F. Barlat, M.-G. Lee, Application of crystal plasticity to an austenitic stainless steel. Model. Simul. Mater. Sci. Eng. (2012). https://doi.org/10.1088/0965-0393/20/2/024009
H. Wang, P.D. Wu, C.N. Tomé, Y. Huang, A finite strain elastic-viscoplastic self-consistent model for polycrystalline materials. J. Mech. Phys. Solids 58, 594–612 (2010). https://doi.org/10.1016/j.jmps.2010.01.004
R.A. Lebensohn, C.N. Tomé, P.J. Maudlin, A selfconsistent formulation for the prediction of the anisotropic behavior of viscoplastic polycrystals with voids. J. Mech. Phys. Solids 52, 249–278 (2004). https://doi.org/10.1016/S0022-5096(03)00114-5
R. Masson, M. Bornert, P. Suquet, A. Zaoui, An affine formulation for the prediction of the effective properties of nonlinear composites and polycrystals. J. Mech. Phys. Solids 48, 1203–1227 (2000). https://doi.org/10.1016/S0022-5096(99)00071-X
C.N. Tomé, R.A. Lebensohn, Manual for code Visco-Plastic Self-Consistent (VPSC) (2009)
O. Engler, C.N. Tomé, M.Y. Huh, A study of through-thickness texture gradients in rolled sheets. Metall. Mater. Trans. A Phys. Metall. Mater. Sci. 31, 2299–2315 (2000). https://doi.org/10.1007/s11661-000-0146-7
M.Y. Huh, J.H. Lee, S.H. Park, O. Engler, D. Raabe, Effect of through-thickness macro and micro-texture gradients on ridging of 17%Cr ferritic stainless steel sheet. Steel Res. Int. (2005). https://doi.org/10.1002/srin.200506098
M.P. Miller, T.J. Turner, A methodology for measuring and modeling crystallographic texture gradients in processed alloys. Int. J. Plast. 17, 783–805 (2001). https://doi.org/10.1016/S0749-6419(00)00068-1
D. Raabe, Inhomogeneity of the crystallographic texture in a hot-rolled austenitic stainless steel. J. Mater. Sci. 30, 47–52 (1995). https://doi.org/10.1007/BF00352130
I. Tikhovskiy, D. Raabe, F. Roters, Simulation of earing of a 17% Cr stainless steel considering texture gradients. Mater. Sci. Eng. A 488, 482–490 (2008). https://doi.org/10.1016/j.msea.2007.11.063
F. Bachmann, R. Hielscher, H. Schaeben, Texture analysis with MTEX—free and open source software toolbox. Solid State Phenom. 160, 63–68 (2010). https://doi.org/10.4028/www.scientific.net/SSP.160.63
Y. Jeong, M.S. Pham, M. Iadicola, A. Creuziger, Forming limit diagram predictions using a self-consistent crystal plasticity model: a parametric study. Key Eng. Mater. 651–653, 193–198 (2015). https://doi.org/10.4028/www.scientific.net/kem.651-653.193
J.A. Nelder, R. Mead, A simplex method for function minimization. Comput. J. 7, 308–313 (1965). https://doi.org/10.1093/comjnl/7.4.308
E. Jones, T. Oliphant, P. Peterson, SciPy: Open source scientific tools for Python (2001). http://www.scipy.org/
T.E. Oliphant, SciPy: open source scientific tools for Python. Comput. Sci. Eng. (2007). https://doi.org/10.1109/MCSE.2007.58
C. Du, F. Maresca, M.G.D. Geers, J.P.M. Hoefnagels, Ferrite slip system activation investigated by uniaxial micro-tensile tests and simulations. Acta Mater. 146, 314–327 (2018). https://doi.org/10.1016/j.actamat.2017.12.054
Y. Jeong, F. Barlat, M.-G. Lee, Crystal plasticity predictions of forward-reverse simple shear flow stress. Mater. Sci. Forum 702–703, 204–207 (2012). https://doi.org/10.4028/www.scientific.net/MSF.702-703.204
H. Wang, P.D. Wu, C.N. Tomé, Y. Huang, A finite strain elastic–viscoplastic self-consistent model for polycrystalline materials. J. Mech. Phys. Solids 58, 594–612 (2010). https://doi.org/10.1016/j.jmps.2010.01.004
F. Barlat, Crystallographic texture, anisotropic yield surfaces and forming limits of sheet metals. Mater. Sci. Eng. 91, 55–72 (1987). https://doi.org/10.1016/0025-5416(87)90283-7
K. Bandyopadhyay, S. Basak, K.S. Prasad, M.-G. Lee, S.K. Panda, J. Lee, Improved formability prediction by modeling evolution of anisotropy of steel sheets. Int. J. Solids Struct. 156, 263–280 (2018). https://doi.org/10.1016/j.ijsolstr.2018.08.024
Acknowledgements
The support from National Research Foundation of Korea (NRF-2017R1D1A1B03031052) is kindly acknowledged.
Author information
Authors and Affiliations
Corresponding author
Additional information
Publisher's Note
Springer Nature remains neutral with regard to jurisdictional claims in published maps and institutional affiliations.
Rights and permissions
About this article
Cite this article
Jeong, Y., Manninen, T. Enhancement in Viscoplastic Self-Consistent FLD Prediction Model and Its Application for Austenitic and Ferritic Stainless Steels. Met. Mater. Int. 25, 1548–1563 (2019). https://doi.org/10.1007/s12540-019-00292-5
Received:
Accepted:
Published:
Issue Date:
DOI: https://doi.org/10.1007/s12540-019-00292-5