Abstract
The contour method of residual stress measurement relies on the careful application of wire electro-discharge machining (WEDM) for the cutting stage. Changes in material removal rates during the cut lead to errors in the final calculated values of residual stress. In this study, WEDM cutting parameters have been explored to identify the optimum conditions for contour method residual stress measurements. The influence of machine parameters on the surface roughness and cutting artifacts in the contour cut is discussed. It has been identified that the critical parameter in improving the surface finish is the spark pulse duration. A typical cutting artifact and its impact on measured stress values have been identified and demonstrated for a contour cut in a welded marine steel. A procedure is presented to correct contour displacement data from the influence of WEDM cutting artifacts, and is demonstrated on the correction of a measured weld residual stress. The corrected contour method improved the residual stress magnitude up to 150 MPa. The corrected contour method results were validated by X-ray diffraction, incremental center hole drilling, and neutron diffraction.













Similar content being viewed by others
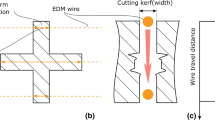
References
D.W. Brown, T.M. Holden, B. Clausen, M.B. Prime, T.A. Sisneros, H. Swenson, J. Vaja: Acta Materialia, 2011, vol. 59, pp. 864–73.
P. Pagliaro, M.B. Prime, H. Swenson, B. Zuccarello: Experimental Mechanics, 2010, vol. 50, pp. 187–94.
M.E. Kartal, C.D.M. Liljedahl, S. Gungor, L. Edwards, M.E. Fitzpatrick: Acta Materialia, 2008, vol. 56, pp. 4417–28.
A.T. DeWald, M.R. Hill: Experimental Mechanics, 2006, vol. 46, pp. 473–90.
Y. Zhang, S. Ganguly, L. Edwards, M.E. Fitzpatrick: Acta Materialia, 2004, vol. 52, pp. 5225–32.
M.B. Prime, R.J. Sebring, J.M. Edwards, D.J. Hughes, P.J. Webster: Experimental Mechanics, 2004, vol. 44, pp. 176–84.
M.B. Prime: J. Eng. Mater. Technol., 2000, vol. 123, pp. 162–68.
F. Hosseinzadeh, P. Ledgard, P.J. Bouchard: Experimental Mechanics, 2013, vol. 53, pp. 829–39.
F. Hosseinzadeh, J. Kowal, P.J. Bouchard: Journal of Engineering, 2014, http://digital-library.theiet.org/content/journals/10.1049/joe.2014.0134.
A. Kundu, P.J. Bouchard, S. Kumar, K. Venkata, J. Francis, A. Paradowska, G. Dey, C. Truman:, Sci. Technol. Weld. Join., 2013, vol. 18, pp. 70–75.
C. Arunachalam, M. Aulia, B. Bozkurt, P.T. Eubank: J. Appl. Phys., 2001, vol. 89, pp. 4255–62.
O. Dodun, A.M. Gonçalves-Coelho, L. Slătineanu, G. Nagîţ: Intl J. Advanced Manufacturing Technol, 2009, vol. 41, pp. 858–64.
M. Kunieda, B. Lauwers, K.P. Rajurkar, B.M. Schumacher: CIRP Annals - Manufacturing Technology, 2005, vol. 54, pp. 64–87.
M.B. Prime, A.L. Kastengren: in T. Proulx (Ed.) Experimental and Applied Mechanics, Volume 6, Springer New York, 2011, pp. 233–50.
B. Ahmad and M. E. Fitzpatrick: The Journal of Engineering, 2015, DOI: 10.1049/joe.2015.0084, Online ISSN 2051–3305.
G. Johnson. PhD Thesis, University of Manchester, 2008.
Acknowledgments
We wish to thank to Peter Ledgard and Damien Flack at The Open University for performing the EDM cutting. The authors are grateful for funding from the Lloyd’s Register Foundation, a charitable foundation helping to protect life and property by supporting engineering-related education, public engagement, and the application of research.
Author information
Authors and Affiliations
Corresponding author
Additional information
Manuscript submitted June 5, 2015.
Rights and permissions
About this article
Cite this article
Ahmad, B., Fitzpatrick, M.E. Minimization and Mitigation of Wire EDM Cutting Errors in the Application of the Contour Method of Residual Stress Measurement. Metall Mater Trans A 47, 301–313 (2016). https://doi.org/10.1007/s11661-015-3231-7
Published:
Issue Date:
DOI: https://doi.org/10.1007/s11661-015-3231-7