Abstract
The mechanical properties and the influence mechanism of grid beetle elytron plates (GBEPn), which were fabricated from an ABS resin material using 3D printing technology, under compression were investigated. Different values of ηc, i.e., ratio of r (centerline radius of the cylinder) to L (length of the basic element), were considered for given yield stress coefficients and matching coefficient. The results revealed that the compressive strength of the GBEPn was comparable to that of the end-trabecular beetle elytron plate (EBEP), whereas the energy absorption capacity of the GBEPn was higher than that of the EBEP. When the ηc was increased, the mechanical properties of the GBEPn exhibited CEEP (compressive strength—elastic stage and energy absorption capacity—plastic stage) characteristics. The basis for the CEEP characteristics and the internal strengthening mechanism were explored. The synergistic effect of the trabeculae and the walls and, hence, the mechanical properties improved with increasing yield stress. The results of the present study will accelerate the application of beetle elytron plates.








Similar content being viewed by others
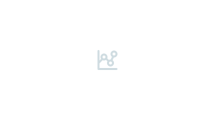
Abbreviations
- EBEP:
-
End-trabecular beetle elytron plate
- GBEP:
-
Grid beetle elytron plate
- HP:
-
Honeycomb plate
- GP:
-
Grid plate
References
Scarpa F, Blain S, Lew T, Perrott D, Ruzzene M, Yates JR (2007) Elastic buckling of hexagonal chiral cell honeycombs. Compos Part A 38:280–289
Lira C, Scarpa F (2010) Transverse shear stiffness of thickness gradient honeycombs. Compos Sci Technol 70(6):930–936
Gibson LJ, Ashby MF (1997) Cellular solid-structure and properties, 2nd edn. Cambridge University Press, China
Fan T, Zou G (2014) Influences of defects on dynamic crushing properties of functionally graded honeycomb structures. J Sandwich Struct Mater 17(3):295–307
Wadsworth DJ, Horrigan DPW, Moltschaniwskyj G, Collins I (2009) Facesheet wrinkling of damaged honeycomb sandwich structures. J Sandwich Struct Mater 11(2–3):105–131
Tang YF, Li FH, Xin FX, Lu TJ (2017) Heterogeneously perforated honeycomb-corrugation hybrid sandwich panel as sound absorber. Mater Des 134:502–512
Sun GY, Jiang H, Fang JG, Li GY, Li Q (2016) Crashworthiness of vertex based hierarchical honeycombs in out-of-plane impact. Mater Des 110:705–719
Vitale JP, Francucci G, Stocchi A (2016) Thermal conductivity of sandwich panels made with synthetic and vegetable fiber vacuum-infused honeycomb cores. J Sandwich Struct Mater 19(1):66–82
Horrigan DPW, Staal RA (2010) Predicting failure loads of impact damaged honeycomb sandwich panels—a refined model. J Sandwich Struct Mater 13(1):111–133
Wadley HNG, Fleck NA, Evans AG (2003) Fabrication and structural performance of periodic cellular metal sandwich structures. Compos Sci Technol 63(16):2331–2343
Sun GY, Huo XT, Chen DD, Li Q (2017) Experimental and numerical study on honeycomb sandwich panels under bending and in-panel compression. Mater Des 133:154–168
Han B, Qin KK, Yu B, Wang B, Zhang QC, Lu TJ (2016) Honeycomb–corrugation hybrid as a novel sandwich core for significantly enhanced compressive performance. Mater Des 93:271–282
Fan X, Verpoest I, Vandepitte D (2006) Finite element analysis of out-of-plane compressive properties of thermoplastic honeycomb. J Sandwich Struct Mater 8(5):437–458
Mozafari H, Molatefi H, Crupi V, Epasto G, Guglielmino E (2014) In plane compressive response and crushing of foam filled aluminum honeycombs. J Compos Mater 49(26):3215–3228
Stapleton SE, Adams DO (2010) Structural enhancements for increased energy absorption in composite sandwich structures. J Sandwich Struct Mater 13(2):137–158
Bai Z, Wang D, Xu Z (2015) Model creation of strain rate–dependent energy absorption for paper honeycomb sandwich structure. J Sandwich Struct Mater 17(4):359–375
Cheng S, Qiao P, Chen F (2016) Numerical analysis of I-Lam honeycomb sandwich panels for collision protection of reinforced concrete beams. J Sandwich Struct Mater 19(4):497–522
Li SQ, Li X, Wang ZH, Wu GY, Lu GX, Zhao LM (2017) Sandwich panels with layered graded aluminum honeycomb cores under blast loading. Compos Struct 173:242–254
Ding LN, Xia L, Wang X, Huang HJ, Wu ZS (2018) Mechanical properties of pultruded basalt fiber-reinforced polymer tube under axial tension and compression. Constr Build Mater 176:629–637
Gautschi W (2008) Leonhard Euler: his life, the man, and his works. SIAM Rev 50(1):3–33
Timoshenko SP, Gere JM (1961) Theory of elastic stability, 2nd edn. McGraw-Hill, New York
Brush DO, Almroth BO, Hutchinson JW (1975) Buckling of bars, plates, and shells. J Appl Mech 42(4):911
Von Kármán T, Dunn LG, Tsien HS (1940) The influence of curvature on the buckling characteristics of structures. J Aeronaut Sci 7:276–289
Von Kármán T, Tsien HS (1941) The buckling of thin cylindrical shellsunder axial compression. J Aeronaut Sci 8:303–312
Koiter WT (1967) On the stability of elastic equilibrium. Dissertation, Delft, 1945 (English translation: NASA)
Mandal P, Calladine CR (2000) Buckling of thin cylindrical shells under axial compression. Int J Solids Struct 37(33):4509–4525
Zhao XL (2000) Section capacity of very high strength (VHS) circular tubes under compression. Thin-Walled Struct 37(3):223–240
Chen JX, Wu G (2013) Beetle forewings: epitome of the optimal design for lightweight composite materials. Carbohydr Polym 91(2):659–665
Comstock JH, Needham JG (1899) The wings of insects (V): The development of the wings. Am Nat 33(395):845–860
Powell PB (1905) The development of wings of certain beetles, and some studies of the origin on the wings of insects (continued). J N Y Entomol Soc 13(1):5–22
Gokan N. On the tracheation and distribution of the sacs in elytra of Scarabaeid beetles. The annual meeting of the entomological society of Japan. Japan; 1966.)
Mitsuo M, Kitano O, Hideo K, Nobuo G, Tadao M (1984) Insect biology. Tamagawa Univ Jpn 5:56–62
Xiang CT. Mechanism of natural composite materials and composite materials research Coleoptera insects bionic design-it's gradual microstructure and mechanical behavior. Ph.D. thesis, Chongqing University, China; 1994.
Chen JX, Xie J, Wu G, Elbashiry EMA, Lu Y (2015) Review of beetle forewing structures and their biomimetic applications in China: (I). On the structural colors and the vertical and horizontal cross-sectional structures. Mater Sci Eng C 55:605–619
Chen JX, Ni QQ, Iwamoto M. A kind of sandwich plate with polygon grilling, Patent 03116503.6, CN; 2006.
Chen Q, Pugno N, Zhao K, Li ZY (2014) Mechanical properties of a hollow-cylindrical-joint honeycomb. Compos Struct 109:68–74
Xiang JW, Du JX, Li DC, Zhen C (2016) Functional morphology and structural characteristics of wings of the ladybird beetle, Coccinella septempunctata (L.). Microsc Res Tech 79(6):550–556
Xiang JW, Du JX (2017) Energy absorption characteristics of bio-inspired honeycomb structure under axial impact loading. Mater Sci Eng A 696:283–289
Ansari Z, Tan CW, Rejab MRM, Bachtiar D, Siregar J, Zuhri MYM, Marzuki NSDM (2017) Crushing behaviour of composite square honeycomb structure: a finite element analysis. J Mech Eng Sci 11(2):2637–2649
Dharmasena KP, Wadley HNG, Xue Z, Hutchinson JW (2008) Mechanical response of metallic honeycomb sandwich panel structures to high-intensity dynamic loading. Int J Impact Eng 35:1063–1074
Kyner A, Dharmasena K, Williams K, Deshpandec V, Wadleya H (2018) Response of square honeycomb core sandwich panels to granular matter impact. Int J Impact Eng 117:13–31
Chen JX, Zu Q, Wu G, Xie J, Tuo WY (2015) Review of beetle forewing structures and their biomimetic applications in China: (II). On the three-dimensional structure, modeling and imitation. Mater Sci Eng C 55:620–633
Chen JX, Zhang XM, Okabe Y, Xie J, Xu MY (2018) Beetle elytron plate and the synergistic mechanism of a trabecular-honeycomb core structure. Sci China Tech Sci. https://doi.org/10.1007/s11431-018-9290-1
Yu XD, Zhang XM, Chen JX, Zhao CQ, Zhao TD, Fu YQ (2020) The flexural property and its synergistic mechanism of multibody molded beetle elytron plates. Sci China Tech Sci. https://doi.org/10.1007/s11431-019-1470-5
Zhang XM, Chen JX, Okabe Y, ZhangPW XiongXB, Yu XD (2017) Influence of honeycomb dimensions and forming methods on the compressive properties of beetle elytron plates. J Sandwich Struct Mater 2017:109963621773199. https://doi.org/10.1177/1099636217731993
Zhang XM, Xie J, Chen JX, Okabe Y, Pan LC, Xu MY (2017) The beetle elytron plate: a lightweight, high-strength and buffering functional-structural bionic material. Sci Rep 7(1):4440
Chen JX, Yu XD, Xu MY, Okabe Y, Zhang XM, Tuo WY (2018) The compressive properties and strengthening mechanism of the middle-trabecular beetle elytron plate. J Sandwich Struct Mater. 2018;1099636218777188.
Hao N, Chen JX, Song YH, Zhang XM, Zhao TD, Fu YQ. A new type of bionic grid plate—the compressive deformation and mechanical properties of the grid beetle elytron plate. J Sandwich Struct Mater (in press)
Shi WM. Research on the connecting method and seismic behavior of beam-column joints in reinforcement and reconstruction of buildings. Master Thesis, Xi'an University of Science and Technology, China; 2011.
Acknowledgements
This work is financially supported by National Natural Science Foundation of China (Grant No. 51875102) and National Key R&D Program of China (Grant No. 2017YFC0703700).
Author information
Authors and Affiliations
Corresponding author
Ethics declarations
Conflict of interest
The authors declare that they have no conflict of interest.
Additional information
Publisher's Note
Springer Nature remains neutral with regard to jurisdictional claims in published maps and institutional affiliations.
Rights and permissions
About this article
Cite this article
Chen, J., Hao, N., Pan, L. et al. Characteristics of compressive mechanical properties and strengthening mechanism of 3D-printed grid beetle elytron plates. J Mater Sci 55, 8541–8552 (2020). https://doi.org/10.1007/s10853-020-04630-6
Received:
Accepted:
Published:
Issue Date:
DOI: https://doi.org/10.1007/s10853-020-04630-6