Abstract
Commercial purity titanium was processed by equal-channel angular pressing (ECAP) for 8 passes and then subjected to dynamic compressive testing using a split-Hopkinson pressure bar (SHPB) facility with an imposed strain rate of ~4000 s−1 and testing temperatures from 288 to 673 K. The results show that ECAP produces an average grain size of ~0.3 μm in transverse sections, but grains which are elongated in longitudinal sections. During dynamic compressive testing at temperatures ranging from 288 to 473 K, the grain shapes and sizes remain unchanged in the transverse sections, but the elongated shapes in the longitudinal sections evolve into polygons due to cell dislocation evolution. At 673 K, the grains become equiaxed with an average size of ~1.8 μm thereby demonstrating the occurrence of dynamic recrystallization. It is shown that the flow stresses decrease with increasing temperature from 288 to 673 K, and there is also a reduction in the rate of strain hardening.






Similar content being viewed by others
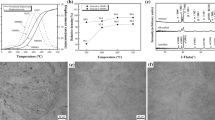
References
Valiev RZ, Islamgaliev RK, Alexandrov IV (2000) Bulk nanostructured materials from severe plastic deformation. Prog Mater Sci 45:103–189
Horita Z, Furukawa M, Nemoto M, Barnes AJ, Langdon TG (2000) Superplastic forming at high strain rates after severe plastic deformation. Acta Mater 48:3633–3640
Lee S, Utsunomiya A, Akamatsu H, Neishi K, Furukawa M, Horita Z, Langdon TG (2002) Influence of scandium and zirconium on grain stability and superplastic ductilities in ultrafine-grained Al–Mg alloys. Acta Mater 50:553–564
Kang DH, Kim TW (2010) Mechanical behavior and microstructural evolution of commercially pure titanium in enhanced multi-pass equal channel angular pressing and cold extrusion. Mater Des 31:s54–s60
Kim HS, Yoo SJ, Ahn JW, Kim DH, Kim WJ (2011) Ultrafine grained titanium sheets with high strength and high corrosion resistance. Mater Sci Eng A528:8479–8485
Semenova IP, Polyakov AV, Raab GI, Lowe TC, Valiev RZ (2012) Enhanced fatigue properties of ultrafine-grained Ti rods processed by ECAP-Conform. J Mater Sci 47:7777–7781. doi:10.1007/s10853-012-6675-9
Korznikova EA, Mironov SY, Korznikov AV, Zhilyaev AP, Langdon TG (2012) Microstructural evolution and electro-resistivity in HPT nickel. Mater Sci Eng A556:437–445
Valiev RZ, Salimonenko DA, Tsenev NK, Berbon PB, Langdon TG (1997) Observations of high strain rate superplasticity in commercial aluminum alloys with ultrafine grain sizes. Scr Mater 37:1945–1950
Park KT, Hwang DY, Shin DH (2002) Microstructural evolution and plastic flow behavior of as-equal channel angular pressed 5083 Al alloy in low temperature superplasticity regime. Met Mater Int 8:519–525
Valiev RZ, Langdon TG (2006) Principles of equal-channel angular pressing as a processing tool for grain refinement. Prog Mater Sci 51:881–981
Lee BS, Kim MH, Hwang SK, Kwun SI, Chae SW (2007) Grain refinement of commercially pure zirconium by ECAP and subsequent intermediate heat treatment. Mater Sci Eng A1087:449–451
Stolyarov VV, Zeipper L, Mingler B, Zehetbauer M (2008) Influence of post-deformation on CP-Ti processed by equal channel angular pressing. Mater Sci Eng A476:98–105
Korshunov A, Kravchenko T, Polyakov L, Smolyakov A, Vedernikova I, Morozov A (2008) Effects of the number of equal-channel angular pressing passes on the anisotropy of ultra-fine titanium. Mater Sci Eng A493:160–163
Mishra A, Martin M, Thadhani NN, Kad BK, Kenik EA, Meyers MA (2008) High-strain-rate response of ultra-fine-grained copper. Acta Mater 56:2770–2783
Zhao XC, Fu WJ, Yang XR, Langdon TG (2008) Microstructure and properties of pure titanium processed by equal-channel angular pressing at room temperature. Scr Mater 59:542–545
Li B, Joshi S, Azevedo K, Ma E, Ramesh KT, Figueiredo RB, Langdon TG (2009) Dynamic testing at high strain rates of an ultrafine-grained magnesium alloy processed by ECAP. Mater Sci Eng A517:24–29
Zhao XC, Yang XR, Liu XY, Wang XY, Langdon TG (2010) The processing of pure titanium through multiple passes of ECAP at room temperature. Mater Sci Eng A527:6335–6339
Ko YG, Shin DH, Lee S (2006) An analysis of the strain hardening behavior of ultra-fine grain pure titanium. Scr Mater 54:1785–1789
Sordi VL, Ferrante M, Kawasaki M, Langdon TG (2012) Microstructure and tensile strength of grade 2 titanium processed by equal-channel angular pressing and by rolling. J Mater Sci 47:7870–7876. doi:10.1007/s10853-012-6593-x
Gunderov DV, Polyakov AV, Semenova IP, Raab GI, Churakova AA, Gimaltdinova EI, Sabirov I, Segurado J, Sitdikov VD, Alexandrov IV, Enikeev NA, Valiev RZ (2013) Evolution of microstructure, macrotexture and mechanical properties of commercially pure Ti during ECAP-conform processing and drawing. Mater Sci Eng A562:128–136
Furukawa M, Iwahashi Y, Horita Z, Nemoto M, Langdon TG (1998) The shearing characteristics associated with equal-channel angular pressing. Mater Sci Eng A257:328–332
Stolyarov VV, Zhu YT, Alexandrov IV, Lowe TC, Valiev RZ (2001) Influence of ECAP routes on the microstructure and properties of pure Ti. Mater Sci Eng A299:59–67
Sergueeva AV, Stolyarov VV, Valiev RZ, Mukherjee AK (2001) Advanced mechanical properties of pure titanium with ultrafine grained structure. Scr Mater 45:747–752
Luo P, McDonald DT, Palanisamy S, Dargusch MS, Xia K (2013) Ultrafine-grained pure Ti recycled by equal channel angular pressing with high strength and good ductility. J Mater Process Technol 213:469–476
Nemat-Nasser S, Guo WG, Cheng JY (1999) Mechanical properties and deformation mechanisms of a commercially pure titanium. Acta Mater 47:3705–3720
Li Q, Xu YB, Bassim MN (2004) Dynamic mechanical behavior of pure titanium. J Mater Process Technol 155–156:1889–1892
Zeng ZP, Jonsson S, Zhang YS (2009) Constitutive equations for pure titanium at elevated temperatures. Mater Sci Eng A505:116–119
Wang L, Wang YC, Zhilyaev AP, Korznikov AV, Li SK, Korznikova E, Langdon TG (2014) Microstructure and texture evolution in ultrafine-grained pure Ti processed by equal-channel angular pressing with subsequent dynamic compression. Scr Mater 77:33–36
Iwahashi Y, Wang J, Horita Z, Nemoto M, Langdon TG (1996) Principle of equal-channel angular pressing for the processing of ultrafine-grained materials. Scr Mater 35:143–146
Oh-ishi K, Horita Z, Furukawa M, Nemoto M, Langdon TG (1998) Optimizing the rotation conditions for grain refinement in equal-channel angular pressing. Metal Mater Trans A 29A:2011–2013
Kim YG, Hwang B, Lee S, Lee CW, Shin DH (2009) Dynamic deformation and fracture behavior of ultra-fine-grained pure copper fabricated by equal channel angular pressing. Mater Sci Eng A504:163–168
Kolsky H (1949) An investigation of the mechanical properties of materials at very high rates of loading. Proc Phys Soc Lond B 62:676–701
Gray GT (2000) Mechanical testing and evaluation. In: Kuhn H, Medlin D (eds) ASM handbook, vol 8. ASM International, Materials Park, pp 462–476
Luo P, McDonald DT, Zhu SM, Palanisamy S, Dargusch MS, Xia K (2012) Analysis of microstructure and strengthening in pure titanium recycled from machining chips by equal channel angular pressing using electron backscatter diffraction. Mater Sci Eng A538:252–258
Mishra A, Kad BK, Gregori F, Meyers MA (2007) Microstructural evolution in copper subjected to severe plastic deformation: experiments and analysis. Acta Mater 55:13–28
Yamaguchi D, Horita Z, Nemoto M, Langdon TG (1999) Significance of adiabatic heating in equal-channel angular pressing. Scr Mater 41:791–796
Kim HS (2001) Prediction of temperature rise in equal channel angular pressing. Mater Trans 42:536–538
Nishida Y, Ando T, Nagase M, Lim SW, Shigematsu I, Watazu A (2002) Billet temperature rise during equal-channel angular pressing. Scr Mater 46:211–216
Pei QX, Hu BH, Lu C, Wang YY (2003) A finite element study of the temperature rise during equal channel angular pressing. Scr Mater 49:303
Pereira PHR, Figueiredo RB, Huang Y, Cetlin PR, Langdon TG (2014) Modeling the temperature rise in high-pressure torsion. Mater Sci Eng A593:185–188
Acknowledgements
This work was supported in part by the National Natural Science Foundation of China under Grant No. 11221202 and in part by the European Research Council under ERC Grant Agreement No. 267464-SPDMETALS. Dynamic testing was conducted using an SHPB Facility which is sponsored at the National Key Laboratory of Science and Technology on Materials under Shock and Impact and the State Key Laboratory of Explosion Science and Technology.
Author information
Authors and Affiliations
Corresponding author
Rights and permissions
About this article
Cite this article
Wang, L., Wang, Y., Zhilyaev, A.P. et al. Dynamic compressive behavior of ultrafine-grained pure Ti at elevated temperatures after processing by ECAP. J Mater Sci 49, 6640–6647 (2014). https://doi.org/10.1007/s10853-014-8306-0
Received:
Accepted:
Published:
Issue Date:
DOI: https://doi.org/10.1007/s10853-014-8306-0