Abstract
Severe friction at the cutter-chip interface increases tool surface wear and reduces tool life. The friction could be reduced by introducing cutting fluids between cutter and chip. The lubrication of cutting fluids depends on its penetration. The ability of cutting fluids to penetrate into the cutting zone can be enhanced by the surface texture of the cutters. In this paper, microgroove-liked textures with different groove width were fabricated on the rake-face of the cemented carbide YS8 cutters with femtosecond laser. The effect of micro-textures on the lubrication of cutting fluids in cutting zone was investigated in cutting H13 hot die steel tests with textured and non-textured cutters under full lubrication. Results showed that micro-textures enhanced penetration of the cutting fluid, improved the lubrication in the cutter-chip interface, and significantly reduced cutting force and tool wear compared to untextured tools. The micro-textured tool with groove width of 50 μm had the best performance among all tested tools. Mechanism responsible was found that cutting fluids can continuously penetrate into the cutting contact area through the sufficient space provided by the microgrooves on the rake-face.


















Similar content being viewed by others
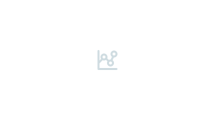
References
Puls H, Klocke F, Lung D (2014) Experimental investigation on friction under metal cutting conditions. Wear 310:63–71
Kishawy HA, Dumitrescu M, Ng EG, Elbestawi MA (2005) Effect of coolant strategy on tool performance, chip morphology and surface quality during high-speed machining of A356 aluminum alloy. Int J Mach Tools Manuf 45:219–227
Sreejith PS (2008) Machining of 6061 aluminium alloy with MQL, dry and flooded lubricant conditions. Mater Lett 62:276–278
DeChiffre L (1981) Lubrication in cutting-critical review and experiments with restricted contact tools. ASLE Trans 24:340–344
Xavior MA, Adithan M (2009) Determining the influence of cutting fluids on tool wear and surface roughness during turning of AISI 304 austenitic stainless steel. J Mater Process Technol 209:900–909
Ayed Y, Germain G, Ammar A, Furetb B (2015) Tool wear analysis and improvement of cutting conditions using the high-pressure water-jet assistance when machining the Ti17 titanium alloy. Precis Eng-J Int Soc Precis Eng Nanotechnol 42:294–301
Ayed Y, Germain G, Ammar A, Furet B (2013) Degradation modes and tool wear mechanisms in finish and rough machining of Ti17 titanium alloy under high-pressure water jet assistance. Wear 305:228–237
da Silva RB, Machado AR, Ezugwu EO, Bonney J, Sales WF (2013) Tool life and wear mechanisms in high speed machining of Ti–6Al–4V alloy with PCD tools under various coolant pressures. J Mater Process Technol 213:1459–1464
Su GS, Guo YK, Song XL, Tao H (2016) Effects of high-pressure cutting fluid with different jetting paths on tool wear in cutting compacted graphite iron. Tribol Int 103:289–297
Sartori S, Ghiotti A, Bruschi S (2018) Solid lubricant-assisted minimum quantity lubrication and cooling strategies to improve Ti6Al4V machinability in finishing turning. Tribol Int 118:287–294
Shokoohi Y, Khosrojerdi E, Shiadhi BHR (2015) Machining and ecological effects of a new developed cutting fluid in combination with different cooling techniques on turning operation. J Clean Prod 94:330–339
Sharma AK, Tiwari AK, Dixit AR, Singh RK, Singh M (2018) Novel uses of alumina/graphene hybrid nanoparticle additives for improved tribological properties of lubricant in turning operation. Tribol Int 119:99–111
Chan CY, Lee WB, Wang H (2013) Enhancement of surface finish using water-miscible nano-cutting fluid in ultra-precision turning. Int J Mach Tools Manuf 73:62–70
Singh RK, Sharma AK, Dixit AR, Tiwari AK, Pramanik A, Mandal A (2017) Performance evaluation of alumina-graphene hybrid nano-cutting fluid in hard turning. J Clean Prod 162:830–845
Vladescu SC, Olver AV, Pegg IG, Reddyhoff T (2015) The effects of surface texture in reciprocating contacts–an experimental study. Tribol Int 82:28–42
Vladescu SC, Olver AV, Pegg IG, Reddyhoff T (2016) Combined friction and wear reduction in a reciprocating contact through laser surface texturing. Wear 358(359):51–61
Biboulet N, Bouassida H, Lubrecht AA (2015) Cross hatched texture influence on the load carrying capacity of oil control rings. Tribol Int 82:12–19
Gachot C, Rosenkranz A, Hsu SM, Costa HL (2017) A critical assessment of surface texturing for friction and wear improvement. Wear 372:21–41
Gherca A, Fatu A, Hajjam M, Maspeyrot P (2017) Influence of surface texturing on the hydrodynamic performance of a thrust bearing operating in steady-state and transient lubrication regime. Tribol Int 102:305–318
Tala-Ighil N, Fillon M (2015) Surface texturing effect comparative analysis in the hydrodynamic journal bearings. Mech Ind 16:302
Wang T, Huang WF, Liu XF, Li YJ, Wang YM (2014) Experimental study of two-phase mechanical face seals with laser surface texturing. Tribol Int 72:90–97
Adjemout M, Andrieux A, Bouyer J, Brunetiere N, Marcos G, Czerwiec T (2017) Influence of the real dimple shape on the performance of a textured mechanical seal. Tribol Int 115:409–416
Shen C, Khonsari MM (2016) The effect of laser machined pockets on the lubrication of piston ring prototypes. Tribol Int 101:273–283
Sudeep U, Tandon N, Pandey RK (2015) Tribological studies of lubricated laser-textured point contacts in rolling/sliding reciprocating motion with investigations of wettability and nanohardness. Tribol Trans 58:625–634
Segu DZ, Choi SG, Choi JH, Kim SS (2013) The effect of multi-scale laser textured surface on lubrication regime. Appl Surf Sci 270:58–63
Gropper D, Wang L, Harvey TJ (2016) Hydrodynamic lubrication of textured surfaces: a review of modeling techniques and key findings. Tribol Int 94:509–529
Ibatan T, Uddin MS, Chowdhury MAK (2015) Recent development on surface texturing in enhancing tribological performance of bearing sliders. Surf Coat Technol 272:102–120
Wu Z, Deng JX, Chen Y, Xing YQ, Zhao J (2012) Performance of the self-lubricating textured tools in dry cutting of Ti-6Al-4V. Int J Adv Manuf Technol 62:943–951
Deng JX, Lian YS, Wu Z, Xing YQ (2013) Performance of femtosecond laser-textured cutting tools deposited with WS2 solid lubricant coatings. Surf Coat Technol 222:135–143
Xing YQ, Deng JX, Li SP, Yue HZ, Meng R, Gao P (2014) Cutting performance and wear characteristics of Al2O3/TiC ceramic cutting tools with WS2/Zr soft-coatings and nano-textures in dry cutting. Wear 318:12–26
Lian YS, Deng JX, Yan GY, Cheng HW, Zhao J (2013) Preparation of tungsten disulfide (WS2) soft-coated nano-textured self-lubricating tool and its cutting performance. Int J Adv Manuf Technol 68:2033–2042
Deng JX, Song WL, Zhang H, Yan P, Liu AH (2011) Friction and wear behaviors of the carbide tools embedded with solid lubricants in sliding wear tests and in dry cutting processes. Wear 270:666–674
Enomoto T, Sugihara T (2010) Improving anti-adhesive properties of cutting tool surfaces by nano−/micro-textures. CIRP Ann-Manuf Technol 59:597–600
Cheng RY (1992) Principle of metal cutting. China Machine Press, Beijing
Shaw MC (1984) Metal cutting principles. Oxford University Press, New York
Wang B, Liu Z (2016) Evaluation on fracture locus of serrated chip generation with stress triaxiality in high speed machining of Ti6Al4V. Mater Des 98:68–78
Sharma V, Pandey PM (2016) Recent advances in turning with textured cutting tools: a review. J Clean Prod 137:701–715
Falco SW, Eduardo DA, Rocha MA (2001) Application of cutting fluids in machining processes. J Braz Soc Mech Sci Eng 23:227–240
Trent EM (1988) Metal cutting and the tribology of seizure: I seizure in metal cutting. Wear 128:29–45
Godlevski VA, Volkov AV, Latyshev VN, Maurin LN (2010) A description of the lubricating action of the tribo-active components of cutting fluids. Lubr Sci 11:51–62
Godlevski VA, Volkov AV, Latyshev VN, Maurin LN (2010) The kinetics of lubricant penetration action during machining. Lubr Sci 9:127–140
Chen YP, Zhang CB, Shi MS, Wu JF, Petersonb GP (2009) Study on flow and heat transfer characteristics of heat pipe with axial “Ω”-shaped microgrooves. Int J Heat Mass Transf 52:636–643
Funding
This work is supported by the Major Program of Shandong Province Natural Science Foundation (ZR2018ZB0522), National Natural Science Foundation of China (51675311), and Development Plan of Science and Technology of Shandong Province (2017GGX30115).
Author information
Authors and Affiliations
Corresponding author
Additional information
Publisher’s note
Springer Nature remains neutral with regard to jurisdictional claims in published maps and institutional affiliations.
Rights and permissions
About this article
Cite this article
Ge, D., Deng, J., Duan, R. et al. Effect of micro-textures on cutting fluid lubrication of cemented carbide tools. Int J Adv Manuf Technol 103, 3887–3899 (2019). https://doi.org/10.1007/s00170-019-03763-6
Received:
Accepted:
Published:
Issue Date:
DOI: https://doi.org/10.1007/s00170-019-03763-6