Abstract
Fiber reinforced metal laminates (FMLs) are a kind of interlaminar hybrid composites made of metal sheets and fibers alternately stacked and cured at a certain pressure and temperature. In this paper, through the simulation of ABAQUS finite element software and recording the change of projectile velocity, the energy loss of projectile is calculated and the impact resistance is judged. Through the comparison of three groups of simulation experimental results, the energy absorbed by carbon fiber reinforced metal laminate is about 300 times that of aluminum alloy plate, which fully shows that carbon fiber reinforced metal composite has excellent impact resistance compared with aluminum alloy. After adding 1 wt% carbon nanotubes to carbon fiber reinforced metal laminates, the absorbed energy is about 10 times that of the original, which shows that carbon nanotubes improve the ultimate yield stress of resin and materials in epoxy resin and enhance the weakness that the composites are easy to delamination under impact load.
You have full access to this open access chapter, Download conference paper PDF
Similar content being viewed by others
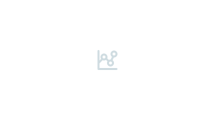
Keywords
1 Introduction
Fiber reinforced metal laminates (FMLs) are formed by alternately stacking metal material layers and fiber reinforced composite layers, similar to sandwich structure. Each material layer is bonded by adhesive under certain temperature and vacuum conditions. It can show the excellent mechanical properties of fiber composites and metal materials, the high strength, high stiffness and fatigue resistance of carbon fiber reinforced composites, as well as the high toughness and excellent damage tolerance of metal materials [1,2,3]. As an excellent modifier and reinforcing material, carbon nanotubes have attracted extensive attention of scientists all over the world [4, 5]. After adding CNTs, the performance of FMLs is greatly improved, and the crack resistance, interlaminar fracture toughness and impact resistance of the matrix are improved [6].
Avila et al. [7] studied the effect of adding nano clay to glass reinforced composites under low velocity impact. The results show that adding 5 wt% nano clay can increase the energy absorption by 48%. Khoramishad et al. [8] studied the effect of multi walled carbon nanotubes on the impact resistance of fiber metal laminates and found that adding 0.5 wt% CNT can improve the impact resistance of fiber metal laminates. Xian Xingjuan [9] studied the static and fatigue tensile failure characteristics of CFRP (epoxy resin matrix) composite laminates with 0° and 45° ply without notch and with straight edge notch through the analysis of a series of test results of 120 groups of specimens. Lin Xiaohong and others used the finite element analysis software ABAQUS/explicit for low-speed impact analysis of carbon fiber epoxy resin composites in the 0°/90° paving direction. The Johnson cook model parameters were used for aluminum alloy, and the Hashin damage criterion was used for fiber layer to establish the bonding layer element, analyze the loss of impact energy and observe and analyze the stress distribution diagram. Therefore, ABAQUS is used to simulate the results of FMLs under high-speed impact, and to simulate the impact resistance of FMLs with CNTs.
2 Preparation and Testing of Carbon Fiber Reinforced Metal Laminates Modified by Carbon Nanotubes
2.1 Preparation of Carbon Fiber Reinforced Metal Laminate
The carbon fiber reinforced metal laminate used in the experiment is composed of two metal plates and a layer of orthogonal carbon fiber woven cloth. The metal aluminum plates are aluminum alloy 2024-T3 aluminum commonly used in aircraft, with a thickness of about 0.3 mm, and the thickness of orthogonal carbon fiber woven step is about 0.25 mm. E51 epoxy resin is used between layers. CNTs were added to epoxy resin by ultrasonic method. Finally, the method of autoclave curing is used for molding (Table 1).
2.2 High Speed Impact Test
In order to explore the impact resistance of carbon fiber reinforced metal laminates modified by carbon nanotubes under high-speed conditions, this experiment mainly tested the energy absorption of aluminum plate, carbon fiber reinforced metal laminate and carbon fiber reinforced metal laminate modified by carbon nanotubes with the same thickness compared with that after complete breakdown of projectile, So as to judge the impact resistance. The experimental device is mainly composed of launcher, target box and high-speed photography system. First fix the test piece in the target box, and then spray the projectile with an air gun at high speed, and then puncture the test piece. Two high-speed cameras record the velocity of the projectile before and after passing through the test piece, as shown in Fig. 1.
The basic working principle of the experimental device is to use a high-speed camera to record the impact velocity VI of the projectile and the residual velocity VR after passing through the experimental plate. The evaluation criterion of impact resistance is the kinetic energy loss of projectile in the process of penetration Δ Ek:
In this paper, three groups of test pieces were tested: pure aluminum plate, carbon fiber reinforced metal laminate without carbon nanotubes and carbon fiber reinforced metal laminate with 1 wt% carbon nanotubes.
3 Finite Element Simulation
3.1 Model Establishment and Grid Division
In the simulation, the plate size of the test piece is 60 mm * 60 mm, as shown in Fig. 2. Orthogonal carbon fiber interlayer bonding property parameters and carbon fiber aluminum alloy interlayer bonding property parameters are shown in Tables 2 and 3 respectively. The impact projectile is made of 45# steel, the density is 7.8 g/cm3, the elastic modulus is 210 gpa, the radius R is 5 mm and the mass is 4.16 g. Considering that the number of elements affects the computer computing speed, the approximate global size of each component is 1. In the load, the contact between the projectile and the target plate adopts general contact, the contact attribute is tangential contact, normal hard contact, and the friction coefficient is 0.2. The four sides of the carbon fiber reinforced composite are completely fixed, the degrees of freedom and rotation of the projectile in three directions are limited, and the initial velocity in the negative direction of the x-axis is defined as 200 m/s. The bonding layer is very thin, so it is defined by interlayer constraints. The modeling process of carbon fiber reinforced metal laminate and carbon nanotube fiber reinforced metal laminate is exactly the same. The difference is that the mechanical properties of the bonding layer of carbon fiber reinforced metal laminate with carbon nanotubes are about 15% higher than those without carbon nanotubes.
3.2 Simulation Results and Analysis
Figure 3 shows the finite element simulation results of the three kinds of experimental parts after high-speed impact. It can be seen from the Fig. 3 that the aluminum plate has higher shape, smaller bullet holes and more regular edges after impact. Because of the high brittleness of carbon fiber plate, the damage of high speed impact is great, and the cracking phenomenon is great. Because of the dual properties of metal and composite material, the carbon fiber reinforced aluminum alloy composite has better impact resistance and smaller damage area after high speed impact.
Carbon fiber composite material stress and strain contours of each layer are shown in Fig. 4 below, the carbon fiber orientations can be found on the damage form of fiber reinforced metal laminates composite materials have great influence, therefore, in practice, according to the characteristics of different structure optimization design in the form of different bearing to meet different needs.
The output speed of the projectile in the simulation process is shown in Fig. 5 below, and the kinetic energy and energy loss of the three groups of projectile are calculated by this speed, and the results are shown in Table 4 below:
By comparing the results of three groups of simulation experiments, the energy absorption of carbon fiber reinforced metal laminates is about 300 times that of aluminum alloy plates, which fully demonstrates that the impact resistance of carbon fiber reinforced metal composites has a great advantage compared with aluminum alloy. However, when 1 wt% carbon nanotubes were added to the carbon fiber reinforced metal laminates, the absorption energy was about 10 times of the original, indicating that carbon nanotubes increased the ultimate yield stress of the resin and the material in the epoxy resin, and alleviated the weakness that the composite was easy to delaminate under impact load.
4 Conclusion
The impact resistance of carbon fiber reinforced metal composites and mechanical properties of carbon nanotube modified carbon fiber epoxy resin matrix were studied, and the conclusions were as follows:
-
(1)
Compared with traditional aluminum alloy materials, the impact resistance of carbon fiber reinforced metal composites has been greatly improved, but the delamination fracture of bond layer is still the weak part of carbon fiber reinforced metal composites.
-
(2)
Adding a certain amount of nano-materials into epoxy resin matrix can improve the impact resistance of composite materials.
-
(3)
The laying Angle of carbon fiber metal laminates has a great influence on the damage form of high-speed impact. In practical application, composite materials can be designed according to this characteristic to meet the actual demand.
References
Megahed, M., Abd El-baky, M.A., Alsaeedy, A.M., Alshorbagy, A.E.: An experimental investigation on the effect of incorporation of different nanofillers on the mechanical characterization of fiber metal laminate. Compos. B. Eng. 176, 107277 (2019)
Yao, L., Sun, G., He, W., Meng, X., Xie, D.: Investigation on impact behavior of FMLs under multiple impacts with the same total energy: Experimental characterization and numerical simulation. Compos. Struct. 226, 111218 (2019). https://doi.org/10.1016/j.compstruct.2019.111218
Bahari-Sambran, F., Eslami-Farsani, R., Arbab, C.S.: The flexural and impact behavior of the laminated aluminum-epoxy/basalt fibers composites containing nanoclay: an experimental investigation. J. Sandwich Struct. Mater. 22, 1931–1951 (2018)
Zhang, X., et al.: Effect of multi-walled carbon nanotubes addition on the interfacial property of titanium-based fiber metal laminates. Polym. Compos. 39, E1159–E1168 (2018)
Dhaliwal, G.S., Newaz, G.M.: Experimental and numerical investigation of flexural behavior of carbon fiber reinforced aluminum laminates. J. Reinf. Plast. Compos. 35, 945–956 (2016)
Zhang, H., Gn, S.W., An, J., Xiang, Y., Yang, J.L.: Impact Behaviour of GLAREs with MWCNT Modified epoxy resins. Exp. Mech. 54(1), 83–93 (2013). https://doi.org/10.1007/s11340-013-9724-7
Bahari-Sambran, F., Meuchelboeck, J., Kazemi-Khasragh, E., Eslami-Farsani, R., Arbab Chirani, S.: The effect of surface modified nanoclay on the interfacial and mechanical properties of basalt fiber metal laminates. Thin-Walled Struct. 144, 106343 (2019)
Khoramishad, H., Alikhani, H., Dariushi, S.: An experimental study on the effect of adding multi-walled carbon nanotubes on high-velocity impact behavior of fiber metal laminates. Compos. Struct. 201, 561–569 (2018)
Xingjuan, X.: Static and fatigue failure characteristics of carbon fiber reinforced epoxy composites with edge notch. Sci. China: Mathematics Physics Astronomy Tech. Sci. 02, 183–192 (1984)
Acknowledgements
This work was financially supported by the College Students' Innovative Entrepreneurial Training Plan Program (D202104022110228193), Aeronautical Science Foundation of China (2020Z055054002) and the Scientific Research Funds from Liaoning Education Department (JYT2020006 & JYT2020007).
Author information
Authors and Affiliations
Corresponding author
Editor information
Editors and Affiliations
Rights and permissions
Open Access This chapter is licensed under the terms of the Creative Commons Attribution 4.0 International License (http://creativecommons.org/licenses/by/4.0/), which permits use, sharing, adaptation, distribution and reproduction in any medium or format, as long as you give appropriate credit to the original author(s) and the source, provide a link to the Creative Commons license and indicate if changes were made.
The images or other third party material in this chapter are included in the chapter's Creative Commons license, unless indicated otherwise in a credit line to the material. If material is not included in the chapter's Creative Commons license and your intended use is not permitted by statutory regulation or exceeds the permitted use, you will need to obtain permission directly from the copyright holder.
Copyright information
© 2022 The Author(s)
About this paper
Cite this paper
Jia, Z., Xu, L., Huang, S., Xu, H., Zhang, Z., Cui, X. (2022). Preparation and Impact Resistance of Carbon Fiber Reinforced Metal Laminates Modified by Carbon Nanotubes. In: Feng, G. (eds) Proceedings of the 8th International Conference on Civil Engineering. ICCE 2021. Lecture Notes in Civil Engineering, vol 213. Springer, Singapore. https://doi.org/10.1007/978-981-19-1260-3_27
Download citation
DOI: https://doi.org/10.1007/978-981-19-1260-3_27
Published:
Publisher Name: Springer, Singapore
Print ISBN: 978-981-19-1259-7
Online ISBN: 978-981-19-1260-3
eBook Packages: EngineeringEngineering (R0)