Abstract
The focus of this work is to investigate the control strategy of twist springback of an industrial aluminium alloy extruded tube after mandrel-rotary draw bending, which is a complex nonlinear physical process with coupling multi-factor interactive effects. A particularly pronounced twist springback characteristic of an AA6060-T4 hybrid thin-walled bent tube was observed. It leads to difficulty at the assembly stage due to the inaccurate geometry of product. For an accurate modelling of material behaviours, a non-quadratic anisotropic yield criterion integrated with combined isotropic and kinematic hardening model was adopted to describe the strain-stress behaviours including anisotropy, Bauschinger effects and permanent softening. The corresponding mechanical tests, e.g., enhanced forward-reverse simple shear tests, were performed to identify the material parameters. By using the improved and validated finite element model, two process control strategies related to the mandrel nose placement and the axial push assistant loading are proposed for the assessment of the control efficiency. The simulation results indicate that the mandrel nose placement mainly affects the longitudinal angular springback but not twist deformation in the circumferential sections. The angular springback angle firstly increases and then decreases after several tests of forward mandrel nose placement. The other control strategy, additional axial push assistant loading with high boost, is able to reduce twist deformation, but the compensation of angular springback is not attained and even a slight increase is observed. It also leads to the rise of the of wrinkle tendency in the intrados sidewall. Finally, the wipe die rake is put forward to reduce the wrinkle tendency due to the high boost applied for twist control.
















Similar content being viewed by others
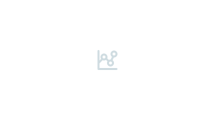
References
Ancellotti S, Benedetti M, Fontanari V, Slaghenaufi S, Tassan M (2016) Rotary draw bending of rectangular tubes using a novel parallelepiped elastic mandrel. Int J Adv Manuf Tech 85:1089–1103
Yang H, Li H, Zhang ZY, Zhan M, Liu J, Li GJ (2012) Advances and trends on tube bending forming technologies. Chinese J Aeronaut 25:1–12
Li H, Yang H, Zhan M, Kou YL (2010) Deformation behaviors of thin-walled tube in rotary draw bending under push assistant loading conditions. J Mater Process Technol 210:143–158
Zhang ZY, Yang H, Li H, Ren N, Tian YL (2011) Bending behaviors of large diameter thin-walled CP-Ti tube in rotary draw bending. Prog Nat Sci Mat Int 21:401–412
Paulsen F, Welo T (2001) Cross-sectional deformations of rectangular hollow sections in bending: part I - experiments. Int J Mech Sci 43:109–129
Paulsen F, Welo T (2001) Cross-sectional deformations of rectangular hollow sections in bending: part II - analytical models. Int J Mech Sci 43:131–152
Zhao GY, Liu YL, Yang H, Lu CH (2010) Cross-sectional distortion behaviors of thin-walled rectangular tube in rotary-draw bending process. Tran Nonferrous Met Soc China 20:484–489
Zhan M, Yang H, Huang L (2006) A numerical-analytic method for quickly predicting springback of numerical control bending of thin-walled tube. J Mater Process Technol 22:713–720
Jiang ZQ, Yang H, Zhan M, Xu XD, Li GJ (2010) Coupling effects of material properties and the bending angle on the springback angle of a titanium alloy tube during numerically controlled bending. Mater Des 31:2001–2010
Li H, Yang H, Song FF, Zhan M, Li GJ (2012) Springback characterization and behaviors of high-strength Ti–3Al–2.5V tube in cold rotary draw bending. J Mater Process Technol 212:1973–1987
Liao J, Xue X, Lee MG, Barlat F, Gracio J (2014) On twist springback prediction of asymmetric tube in rotary draw bending with different constitutive models. Int J Mech Sci 89:311–322
Xue X, Liao J, Vincze G, Gracio J (2015) Modelling of mandrel rotary draw bending for accurate twist springback prediction of an asymmetric thin-walled tube. J Mater Process Technol 216:405–417
Zhan M, Wang Y, Yang H, Long H (2016) An analytic model for tube bending springback considering different parameter variations of Ti-alloy tubes. J Mater Process Technol 236:123–137
Sitar M, Kosel F, Brojan M (2015) Numerical and experimental analysis of elastic–plastic pure bending and springback of beams of asymmetric cross-sections. Int J Mech Sci 90:77–88
Welo T, Paulsen F (1996) Local flange buckling and its relation to elastic springback in forming of aluminium extrusions. J Mater Process Technol 60(1):149–154
Zhu YX, Liu YL, Yang H, Li HP (2012) Improvement of the accuracy and the computational efficiency of the springback prediction model for the rotary-draw bending of rectangular H96 tube. Int J Mech Sci 66:224–232
Zhu YX, Liu YL, Li HP, Yang H (2013) Springback prediction for rotary-draw bending of rectangular H96 tube based on isotropic mixed and Yoshida Uemori two surface hardening models. Mater Des 47:200–209
Tang NC (2000) Plastic-deformation analysis in tube bending. Int J Press Vessel Pip 77:751–759
Al-Qureshi HA, Russo A (2002) Spring-back and residual stresses in bending of thin-walled aluminum tubes. Mater Des 23(2):217–222
Zhang ZK, Wu JJ, Guo RC, Wang MZ, Li FF, Guo SC, Wang YA, Liu WP (2016) A semi-analytical method for the springback prediction of thick-walled 3D tubes. Mater Des 99:57–67
Zhao GY, Liu YL, Yang H, Lu CH, Gu RJ (2009) Three-dimensional finite-elements modelling and simulation of rotary-draw bending process for thin-walled rectangular tube. Mater Sci Eng A 499:257–261
Li H, Yang H, Zhang ZY, Li GJ, Liu N, Welo T (2014) Multiple instability-constrained tube bending limits. J Mater Process Technol 214:445–455
Schilp H, Suh J, Hoffmann H (2012) Reduction of springback using simultaneous stretch-bending processes. Int J Mater Form 5:175–180
Welo T, Granly B (2010) A new adaptive bending method using closed loop feedback control. Trans Nonferrous Met Soc China 20(11):2111–2117
Welo T, Sætertrø K, Søvik OP (2008) Adaptive bending of aluminium extrusions using an automated closed-loop feedback approach. Int J Mater Form 1:197–200
Welo T (2014) Design for dimensional accuracy in bending operations: Introducing the concept of flatness limit curves. Proceedings of the ASME 2014 International Design Engineering Technical Conferences & Computers and Information in Engineering Conference IDETC/CIE 2014, August 17–20, 2014, Buffalo, New York, USA
Li C, Yang H, Zhan M, Xu XD, Li GJ (2009) Effects of process parameters on numerical control bending process for large diameter thin-walled aluminum alloy tubes. Tran Nonferrous Met Soc China 19:668–673
Bardelcikand A, Worswick MJ (2005) The effect of element formulation on the prediction of boost effects in numerical tube bending. Aip Conf Proc 778:774–780
Engel B, Hassan HR (2014) Investigation of neutral axis shifting in rotary draw bending processes for tubes. Steel Res Int 85(7):1209–1214
Hopperstad OS, Langseth M, Remseth S (1995) Cyclic stress-strain behaviour of alloy AA6060, part I: uniaxial experiments and modelling. Int J Plast 11(6):725–739
Hopperstad OS, Langseth M, Remseth S (1995) Cyclic stress-strain behaviour of alloy AA6060, part II: biaxial experiments and modelling. Int J Plast 11(6):741–762
Khadykoa M, Dumoulin S, Cailletaud G, Hopperstad OS (2016) Latent hardening and plastic anisotropy evolution in AA6060 aluminium alloy. Int J Plast 76:51–74
Barlat F, Brem JC, Yoon JW, Chung K et al (2003) Plane stress yield function for aluminium alloy sheets—part I: theory. Int J Plast 19:1297–1319
Chung K, Lee MG, Kim DY, Kim CM, Wenner ML, Barlat F (2005) Spring-back evaluation of automotive sheets based on isotropic-kinematic hardening laws and non-quadratic anisotropic yield functions part I: theory and formulation. Int J Plast 21:861–882
Lee JW, Lee MG, Barlat F (2012) Finite element modelling using homogeneous anisotropic hardening and application to spring-back prediction. Int J Plast 29:13–41
Lee MG, Kim DY, Kim CM, Wenner ML, Wagoner RH, Chung K (2007) A practical two-surface plasticity model and its application to spring-back prediction. Int J Plast 23:1189–1212
Xue X, Liao J, Vincze G, Barlat F (2015) Twist springback characteristics of dual-phase steel sheet after non-symmetric deep drawing. Int J Mater Form . doi:10.1007/s12289-015-1275-2In press
Rauch EF (1998) Plastic anisotropy of sheet metals determined by simple shear tests. Mater Sci Eng A 241:179–183
Vincze G (2007) Investigation methodologies for metals used in forming processes. PhD. Dissertation. University of Aveiro, Portugal
Yoon JW, Barlat F (2006) Modeling and simulation of the forming of aluminum sheet alloys. ASM Handbook, Metalworking: Sheet Forming 14B:792–826
Rauch EF, Gracio J, Barlat F (2007) Working-hardening model for polycrystalline metals under strain reversal at large strains. Acta Mater 55:2939–2948
Martins PAF, Kwiatkowski L, Franzen V, Tekkaya AE, Kleiner M (2009) Single point incremental forming of polymers. Cirp Ann Manuf Techn 58:229–232
Acknowledgements
In memory of Professor José Joaquim de Almeida Grácio (1959-2014) who initiated this industrial project at the University of Aveiro. Without him this work would not have been possible. The authors would like to thank the Portuguese Industrial Company Ciclofapril for all support concerning the experimental works. This work is also funded by the Scientific programme of Fuzhou University and the Portuguese Foundation of Science and Technology under the Projects (Ref. UID/EMS/00481/2013 and SFRH/BPD/114823/2016).
Author information
Authors and Affiliations
Corresponding author
Ethics declarations
Conflict of interest
The authors declare that they have no conflict of interest.
Rights and permissions
About this article
Cite this article
Xue, X., Liao, J., Vincze, G. et al. Control strategy of twist springback for aluminium alloy hybrid thin-walled tube under mandrel-rotary draw bending. Int J Mater Form 11, 311–323 (2018). https://doi.org/10.1007/s12289-017-1346-7
Received:
Accepted:
Published:
Issue Date:
DOI: https://doi.org/10.1007/s12289-017-1346-7