Abstract
This paper provides a mechanistic understanding of hydrogen-microstructure-strain interactions in a finely-grained 25Cr–7Ni super duplex stainless steel subjected to dynamic tensile loading. Miniature-sized tensile specimens were hydrogen-charged for up to nine days, and the microstructure was imaged, in-situ, during mechanical tensile testing. Digital image correlation analysis of the recorded images revealed that the austenite phase underwent softening while the ferrite phase hardened due to uptaken hydrogen. Severe strain localization occurred due to dissolved hydrogen in the microstructure resulting in hydrogen-induced cracks. Mobile hydrogen atoms caused softening of the microstructure while trapped hydrogen reasoned hardening. The austenite’s hydrogen absorption capacity is decisive for the susceptibility to hydrogen embrittlement.
Graphical Abstract













Similar content being viewed by others
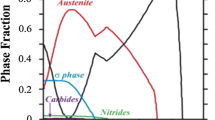
Data Availability
The data that support the findings of this study are available from the corresponding author upon reasonable request.
Code Availability
The codes and mathematic algorithms used to produce the data will be made available by the corresponding author upon reasonable request.
References
C. Örnek, T. Müller, U. Kivisäkk, F. Zhang, M. Långberg, U. Lienert, K.-H. Hwang, E. Lundgren, J. Pan, Corros. Sci. 175, 108899 (2020)
C. Örnek, A. Larsson, G.S. Harlow, F. Zhang, R. Kroll, F. Carlà, H. Hussain, U. Kivisäkk, D.L. Engelberg, E. Lundgren, J. Pan, Scripta Mater. 187, 63 (2020)
C. Örnek, A. Larsson, G.S. Harlow, F. Zhang, R. Kroll, F. Carlà, H. Hussain, U. Kivisäkk, D.L. Engelberg, E. Lundgren, J. Pan, Corros. Sci. 176, 109021 (2020)
A. Turk, S.D. Pu, D. Bombač, P.E.J. Rivera-Díaz-del-Castillo, E.I. Galindo-Nava, Acta Mater. 197, 253 (2020)
T. Mente, T. Boellinghaus, Weld World 58, 205 (2014)
C. Örnek, P. Reccagni, U. Kivisäkk, E. Bettini, D.L. Engelberg, J. Pan, Int. J. Hydrog. Energy 43, 12543 (2018)
C. Örnek, C. Leygraf, J. Pan, NPJ Mater. Degrad. 3, 8 (2019)
C. Örnek, D.L. Engelberg, J. Strain Anal. Eng. Des. 51, 207 (2016)
R. v. Mises, Nachrichten von der Gesellschaft der Wissenschaften zu Göttingen, Mathematisch-Physikalische Klasse 1913, 582 (1913)
T. Mente, T. Bollinghaus, Weld World 56, 66 (2012)
Recommended Practice DNV-RP-F112 Design of Duplex Stainless Steel Subsea Equipment Exposed to Cathodic Protection (Det Norkse Veritas, 2008)
U. Kivisäkk, Mater. Sci. Eng., A 527, 7684 (2010)
M.S. Hazarabedian, A. Viereckl, Z. Quadir, G. Leadbeater, V. Golovanevskiy, S. Erdal, P. Georgeson, M. Iannuzzi, Corrosion 75, 824 (2019)
A. Yousefi, G. Itoh, ISIJ Int. 58, 561 (2018)
V. Grozovski, S. Vesztergom, G.G. Láng, P. Broekmann, J. Electrochem. Soc. 164, E3171 (2017)
J.H. Huang, C.J. Altstetter, Metall. Mater. Trans. A 26, 1079 (1995)
A. Turnbull, R.B. Hutchings, Mater. Sci. Eng. A 177, 161 (1994)
C. Örnek, D.L. Engelberg, Mater. Sci. Eng. A 666, 269 (2016)
J.-O. Nilsson, G. Chai, U. Kivisäkk, in Proceedings of the International Conference & Expo: Duplex 2007, Grado, 18–20 June 2007. (Associazione Italiana di Metallurgia, Milano, 2007), p. 73
Y. Aboura, K.L. Moore, Appl. Surf. Sci. 557, 149736 (2021)
A. Hussein, A.H.M. Krom, P. Dey, G.K. Sunnardianto, O.A. Moultos, C.L. Walters, Acta Mater. 209, 116799 (2021)
H.K.D.H. Bhadeshia, ISIJ Int. 56, 24 (2016)
G. Chai, S. Ronneteg, U. Kivisäkk, R.L. Peng, S. Johansson, Steel Res. Int. 80, 482 (2009)
U. Kivisäkk, S. Ciurea, in Proceedings of the 18th International Corrosion Congress 2011, Perth, 20-24 November 2011. vol. 2 (Australasian Corrosion Association, Kerrimuir, 2011), p. 1549
S.P. Lynch, Stress Corrosion Cracking (Woodhead Publishing, Place Published, 2011), pp. 90–130
R. Kirchheim, Scripta Mater. 62, 67 (2010)
S. Lynch, Corros. Rev. 30, 105 (2012)
A. Tehranchi, B. Yin, W.A. Curtin, Philos. Mag. 97, 400 (2017)
Acknowledgements
Cem Örnek is grateful for the financial support from TÜBİTAK (The Scientific and Technological Research Council of Turkey) under contract number 118C227 within the program 2232: International Fellowship for Outstanding Researchers. Dr Ulf Kivisäkk, Sandvik Materials Technology AB, is thanked for material provision. The National Research Center on Membrane Technologies (MEM-TEK) at Istanbul Technical University is thanked for granting access to their scanning electron microscopy system.
Author information
Authors and Affiliations
Contributions
Cem Örnek: Conceptualization, Methodology, Software, Formal Analysis, Investigation, Visualization, Data Curation, Writing Original Draft, Writing Review & Editing, Project Administration, Funding Acquisition, Resources, Supervision; Bilgehan M. Şeşen: Software, Investigation, Visualization; Mustafa K. Ürgen: Writing Review & Editing, Project Administration, Resources, Supervision.
Corresponding author
Ethics declarations
Conflict of interest
The authors declare that they have no known competing financial interests or personal relationships that could have influenced the work reported in this paper.
Additional information
Publisher's Note
Springer Nature remains neutral with regard to jurisdictional claims in published maps and institutional affiliations.
Supplementary Information
Below is the link to the electronic supplementary material.
https://www.youtube.com/watch?v=sTU3Z7fAs0Y. Video 1: DIC microstrain analysis results showing the von Mises strain evolution in the duplex microstructure without hydrogen charging. The colours indicate the von Mises strains in per cent. The transparent background shows the microstructure, with the ferrite phase being contrasted as dark and the austenite phase shown as bright islands. The frame rate is 25 frames/sec. The specimen was elongated with a strain rate of 0.005 mm/min. Images were captured every ~ 10 s using an all-in-focus controllable digital optical microscope. The video shows images taken for 03 h:15 min:14 s until 600 MPa, which is approximately the macroscopic yielding point. The pixel resolution is 6.4 pixels/µm. The subset size for calculation was 23 pixels with a step size of 11 (MP4 12861 kb)
https://youtu.be/QEbryv3p-m8. Video 2: DIC microstrain analysis results showing the von Mises strain evolution in the duplex microstructure that was pre-charged with hydrogen for 62 h with a galvanostatic current density of − 38 mA/cm2. The colours show the von Mises strains in per cent. The transparent background shows the microstructure, with the ferrite phase being contrasted as dark and the austenite phase shown as bright islands. The frame rate is 25 frames/sec. The specimen was elongated with a strain rate of 0.005 mm/min. Images were captured every ~ 10 s using an all-in-focus controllable digital optical microscope. The video shows images taken for 03 h:04 min:10 s until 600 MPa, approximately the macroscopic yielding point of the as-received microstructure (no hydrogen). The pixel resolution is 6.4 pixels/µm. The subset size for calculation was 23 pixels with a step size of 11 (MP4 13058 kb)
https://youtu.be/XKR3LN2t6Uc. Video 3: DIC microstrain analysis results showing the von Mises strain evolution in the duplex microstructure that was pre-charged with hydrogen for nine days with a galvanostatic current density of − 38 mA/cm2. The colours show the von Mises strains in per cent. The transparent background shows the microstructure, with the ferrite phase being contrasted as dark and the austenite phase shown as bright islands. The frame rate is 25 frames/sec. The specimen was elongated with a strain rate of 0.005 mm/min. Images were captured every ~ 10 s using an all-in-focus controllable digital optical microscope. The video shows images taken for 09 h:37 min:58 s until 600 MPa, approximately the macroscopic yielding point of the as-received microstructure (no hydrogen). The pixel resolution is 3.2 pixels/µm. The subset size for calculation was 17 pixels with a step size of 5 (MP4 16588 kb)
https://youtu.be/Y2BYfRa5Ezc. Video 4: DIC microstrain analysis results showing the von Mises strain evolution in the duplex microstructure pre-charged with hydrogen for 9 days with a galvanostatic current density of − 38 mA/cm2. The colours show the von Mises strains in per cent. The transparent background shows the microstructure, with the ferrite phase being contrasted as dark and the austenite phase shown as bright islands. The frame rate is 25 frames/sec. The specimen was elongated with a strain rate of 0.005 mm/min. Images were captured every ~ 10 s using an all-in-focus controllable digital optical microscope. The video shows images taken for 09 h:37 min:58 s until 600 MPa, approximately the macroscopic yielding point of the as-received microstructure (no hydrogen). The pixel resolution is 3.2 pixels/µm. The subset size for calculation was 17 pixels with a step size of 5. The arrows show the deformation vectors, which indicate the direction of the strain (MP4 48632 kb)
Rights and permissions
About this article
Cite this article
Örnek, C., Şeşen, B.M. & Ürgen, M.K. Understanding Hydrogen-Induced Strain Localization in Super Duplex Stainless Steel Using Digital Image Correlation Technique. Met. Mater. Int. 28, 475–486 (2022). https://doi.org/10.1007/s12540-021-01123-2
Received:
Accepted:
Published:
Issue Date:
DOI: https://doi.org/10.1007/s12540-021-01123-2