Abstract
One of the most important components in a microfluidic system is the microchannel which involves complicated flow and transport process. This work presents microscale thermal fluid transport process inside a microchannel with a height of 37 μm. The channel can be heated on the bottom wall and is integrated with arrays of pressure and temperature sensors which can be used to measure and determine the local heat transfer and pressure drop. A more simplified model with modification of Young’s Modulus from the experimental test is used to design and fabricate the arrays of pressure sensors. Both the pressure sensors and the channel wall use polymer materials which greatly simplifies the fabrication process. In addition, the polymer materials have a very low thermal conductivity which significantly reduces the heat loss from the channel to the ambient that the local heat transfer can be accurately measured. The airflow in the microchannel can readily become compressible even at a very low Reynolds number condition. Therefore, simultaneous measurement of both the local pressure drop and the temperature on the heated wall are required to determine the local heat transfer. Comparison of the local heat transfer for a compressible airflow in microchannel is made with the theoretical prediction based on incompressible airflow in large scale channel. The comparison has clarified many of the conflicting results among different works.














Similar content being viewed by others
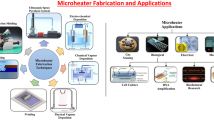
Abbreviations
- A :
-
Cross section area of the channel
- b :
-
Width of the diaphragm
- c p :
-
Specific heat of air
- D h :
-
Hydraulic diameter, 2H
- e :
-
Enthalpy
- E :
-
Young’s Modulus
- Gz :
-
Graetz number defined by Eq. 29
- H :
-
Channel height
- h o :
-
Convective heat transfer coefficient based on the flow temperature at the inlet
- h b :
-
Convective heat transfer coefficient based on the bulk temperature of the flow
- k :
-
Specific heat ratio, c p/c v
- K :
-
Thermal conductivity of air
- \( \dot{m} \) :
-
Mass flow rate of the air in the channel
- Nu :
-
Nusselt number defined by Eq. 21
- p :
-
Pressure
- Pr :
-
Prandtl number, ν/α
- \( \dot{q} \) :
-
Heat transfer rate
- \( \dot{q}_{\text{w}} \) :
-
The heat flux imposed along the bottom wall by the electric heaters
- Re :
-
Reynolds number, UDh/υ
- t :
-
Thickness of the diaphragm
- T :
-
Temperature
- U :
-
Mean flow velocity in the channel
- u :
-
Streamwise velocity
- v :
-
Velocity in the y-axis
- w :
-
Channel width
- x :
-
Streamwise distance from the entrance of the channel
- y :
-
Normal distance from the heated wall
- α:
-
Thermal diffusivity of air
- β:
-
Poisson’s ratio
- δ:
-
Deformation of the diaphragm
- ε:
-
Strain in the diaphragm
- ν:
-
Kinematic viscosity of air
- ρ:
-
Density of air
- b:
-
Bulk
- i:
-
Inlet
- o:
-
Outlet
- w:
-
Wall
- x :
-
A streamwise location from the entrance of the channel
References
Bayraktar T, Pidugu SB (2006) Review: characterization of liquid flows in microfluidic systems. Int J Heat Mass Transf 49:815–824
Boresi AP, Schmidt RJ, Sidebottom OM (1993) Advanced mechanics of materials. Wiley, New York, pp 538–539
Choi SB, Barron RF, Warrington RO (1991) Fluid flow and heat transfer in microtubes. ASME DSC 32:123–134
Craighead H (2006) Future lab-on-chip technologies for interrogating individual molecules. Nature 442(27):387–393
Dellmann L, Roth S, Beuret C, Racine GA, Lorenz H, Despont M, Renaud P, Vettiger P (1997) Fabrication process of high aspect ratio elastic structures for piezoelectric motor applications. In: Proceedings of the Transducers ’97, Chicago, USA
Dongari N, Sharma A, Durst F (2009) Pressure-driven diffusive gas flows in micro-channels: from the Knudsen to the continuum regimes. Microfluid Nanofluid 6:679–692
Guckel H (1990) Surface micromachined pressure transducer. Sens Actuators A 28:133–146
Guckel H, Christenson TR, Skrobis KJ, Sniegowski JJ, Kang JW, Choi B, Lovell EG (1990) Microstructure sensors. In: IEEE international electron devices meeting, pp 613–616
Incropera FP, DeWitt DP, Bergman TL, Lavine AS (2007) Fundamentals of heat and mass transfer, chap 8, 6th edn. Wiley, New York
Jiang L, Wong M, Yitshak Z (1999) Phase change in microchannel heat sinks with integrated temperature sensors. J Microelectromech Syst 8:358–365
Kays WM, Crawford ME, Weigand B (2005) Convective heat and mass transfer, chap 8, 4th edn. McGraw-Hill, New York
Ko HS (2009) Fabrication and development of micro fluidic system with embedded micro pressure and temperature sensors for study of thermal and fluid flow properties. PhD thesis, National Cheng Kung University, Tainan, Taiwan
Ko HS, Liu CW, Gau C (2007a) A novel fabrication for pressure sensor with polymer material and evaluation of its performance. J Micromech Microeng 17:1640–1648
Ko HS, Liu CW, Gau C, Yang CS (2007b) Fabrication and design of a heat transfer micro-channel system by a low temperature MEMS technique. J Micromech Microeng 17:983–993
Ko HS, Liu CW, Gau C, Jeng DZ (2008) Flow characteristics in a microchannel system integrated with arrays of micro pressure sensors using polymer material. J Micromech Microeng 18:075016
Koo J, Kleinstreuer C (2003) Liquid flow in microchannels: experimental observations and computational analyses of microfluidics effects. J Micromech Microeng 13:568–579
Lee WY, Wong M, Zohar Y (2002) Pressure loss in constriction microchannels. J Microelectromech Syst 11(3):236–244
Li D (2004) Electrokinetics in microfluidics, vol 2. Elsevier, Boston
Lorenz H, Despont M, Fahrni N, LaBianca N, Renaud P, Vettiger P (1997) A low-cost negative resist for MEMS. J Micromech Microeng 7:121–124
Morini GL (2004) Single-phase convective heat transfer in microchannels: a review of experimental results. Int J Therm Sci 43:631–651
Naito E (1984) Laminar heat transfer in the entrance region between parallel plates—the case of uniform heat flux. Heat Transf Jpn Res 13(3):92–106
Natrajan VK, Christensen KT (2010) The impact of surface roughness on flow through a rectangular microchannel from the laminar to turbulent regimes. Microfluid Nanofluid 9:95–121
Peng XF, Peterson GP (1996) Convective heat transfer and flow friction for water flow in microchannel structures. Int J Heat Mass Transf 39:2599–2608
Peng XF, Peterson GP, Wang BX (1994) Frictional flow characteristics of water flowing through rectangular microchannels. Exp Heat Transf 7:249–264
Prasher RS, Chang J-Y, Sauciuc I, Narasimhan S, Chau D, Chrysler G, Myers A, Prstic S, Hu C (2005) Nano and micro technology-based next generation package-level cooling solution. Intel Technol J 9(4):285–296
Rohsenow WM, Hartnett JP, Ganic EN (1985) Handbook of heat transfer fundamentals, 2nd edn. McGraw-Hill, New York, pp 7–49
Rostami AA, Mujumdar AS, Saniei N (2002) Flow and heat transfer for gas flowing in microchannel: a review. Heat Mass Transf 38:359–367
Tuckerman DB, Pease RFW (1981) High-performance heat sinking for VLSI. IEEE Electron Device Lett 2:126–129
Wu HY, Cheng P (2003) Friction factors in smooth trapezoidal silicon microchannels with different aspect ratios. Int J Heat Mass Transf 46:2519–2525
Yu D, Warrington RO, Barron R, Ameel T (1995) An experimental and theoretical investigation of fluid flow and heat transfer in microtubes. In: Proceedings of ASME/JSME thermal engineering joint conference, Maui, pp 523–530
Zohar Y, Lee YK, Lee WY, Jiang L, Tong P (2002) Subsonic gas flow in a straight and uniform microchannel. J Fluid Mech 472:125–151
Acknowledgment
This research was sponsored by Council of Taiwan under contact no. NSC 97-2221-E-006-057-MY2.
Author information
Authors and Affiliations
Corresponding author
Rights and permissions
About this article
Cite this article
Ko, H.S., Gau, C. Microscale thermal fluid transport process in a microchannel integrated with arrays of temperature and pressure sensors. Microfluid Nanofluid 10, 793–807 (2011). https://doi.org/10.1007/s10404-010-0710-4
Received:
Accepted:
Published:
Issue Date:
DOI: https://doi.org/10.1007/s10404-010-0710-4