Abstract
The level and variation of energy partition ratio to grinding chips in high speed grinding of a nickel based alloy has been investigated. The ratio to grinding chips is evaluated by relating the heat partitioning at the chip formation area with the whole thermal system, which is used to evaluate the convection heat transfer coefficient (CHTC) of water based grinding fluid. High level of CHTCs of the grinding fluid have been identified at high grinding speeds, beneficial heat transfer conditions of low ratios to the workpiece can be achieved. As the burnout happens with the CHTC dropping down to zero level, the ratio to the workpiece and grinding chips would become much higher, around 30–40 % of the grinding heat can be taken away by grinding chips. For nickel based superalloys, it is possible to achieve high material removal rates with the effective cooling of the grinding zone.
Similar content being viewed by others
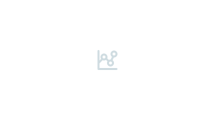
Abbreviations
- Vs :
-
Wheel speed
- Vw :
-
Worktable speed
- ap :
-
Depth of cut
- Pt :
-
Grinding power
- Ft :
-
The tangential grinding force
- bs:
-
The grinding width
- ae :
-
The grinding depth of cut
- Q’w :
-
The material removal rate per unit grinding width
- A and t:
-
Constants depending on the workpiece material and grinding conditions
- Tmax :
-
The maximum grinding temperature rise
- C:
-
C-factor in the circular moving heat source model
- qw :
-
The heat flux to the workpiece
- Ic :
-
Contact length between grinding wheel and workpiece
- βw :
-
Thermal property of the workiece material
- Rw :
-
Energy partition ratio to the workpiece
- T0 :
-
Ambient temperature
- hw :
-
A heat conduction factor
- qt :
-
The total grinding heat flux
- lc :
-
Wheel-work contact geometry
- qw :
-
Grinding heat flux partitioned to the workpiece
- qs :
-
Grinding heat flux partitioned to the grinding wheel
- qf :
-
Grinding heat flux partitioned to grinding fluid
- qch :
-
Grinding heat flux partitioned to grinding chips
- Rws :
-
The heat partition ratio in the work-wheel subsystem
- Rwch :
-
The heat partition ratio in the work-chip subsystem
- hf :
-
The convection factor of grinding fluid
- hch :
-
A heat conduction factor to grinding chips
- Rf :
-
The heat partition to grinding fluid
- Q’w :
-
Material removal rate
- qt*:
-
The variation of critical burnout heat flux
- T*:
-
The burnout threshold temperature
References
T. Tawakoli, High Efficiency Deep Grinding, VDI-Verlag and Mechanical Engineering Publications, Ltd. (MEP), London (1993).
T. Jin, D. J. Stephenson and J. Corbett, Burn threshold of high carbon steel in high efficiency deep grinding, Proc. Institution of Mechanical Engineers, Part B, Journal of Engineering Manufacture, 216 (2003) 357–364.
D. J. Stephenson, T. Jin and J. Corbett, High efficiency deep grinding of a low alloy steel with plated CBN wheels, Annals of the CIRP, 51(1) (2002) 241–244.
C. Guo, Y. Wu, V. Varghese and S. Malkin, Temperature and energy partition for grinding with vitrified CBN wheels, Annals of the CIRP, 48(1) (1999) 247–250.
N. Kim, C. Guo and S. Malkin, Heat flux and energy partition in creep-feed grinding, Annals of the CIRP, 46(1) (1997) 227–232.
B. Zhu, C. Guo, J. E. Sunderland and S. Malkin, Energy partition to the workpiece for grinding of ceramics, Annals of the CIRP, 44(1) (1995) 267–271.
S. Kohli, C. Guo and S. Malkin, Energy partition to the work-piece for grinding with aluminum oxide and CBN abrasive wheels, ASME Journal of Engineering for Industry, 117 (1993) 160–168.
C. Guo and S. Malkin, Inverse heat transfer analysis of heat flux to the workpiece: II. Application, ASME Journal of Engineering for Industry, 118 (1993) 143–149.
C. Guo and S. Malkin, Inverse heat transfer analysis of heat flux to the workpiece: I. Model, ASME Journal of Engineering for Industry, 118 (1993) 137–142.
A. Lavine, A simple model for convective cooling during grinding process, ASME Journal of Engineering for Industry, 110 (1988) 1–6.
T. C. Jen and A. S. Lavine, A variable heat flux model of heat transfer in grinding: model development, Journal of Heat transfer, 177 (1995) 473–478.
M. D. Demetriou and A. S. Lavine, Thermal aspects of grinding: the case of up-grinding, ASME Journal of Manufacturing Science and Engineering, 122 (2000) 605–611.
T. Jin, D. J. Stephenson and W. B. Rowe, Estimation of the convection heat transfer coefficient of coolant within the grinding zone, Proc. Institution of Mechanical Engineers, Part B, J. of Engineering Manufacture, 217 (2003) 397–407.
T. Jin and D. J. Stephenson, A study of the convection heat transfer coefficients of grinding fluids, Annals of the CIRP, 57(1) (2008) 367–370.
B. Lavisse, A. Lefebvre, A. A. Torrance, O. Sinot, E. Henrion, S. Lemarié and A. Tidu, The effects of the flow rate and speed of lubricoolant jets on heat transfer in the contact zone when grinding a nitrided steel, Journal of Manufacturing Processes, 35 (2018) 233–243.
W. B. Rowe, L. Zhang and M. N. Morgan, An improved fluid convection solution inconventional grinding, Proc. IMechE, Part B: J. of Engineering Manufacture, 227(6) (2013) 832–838.
W. B. Rowe and T. Jin, Temperatures in high efficiency deep grinding (HEDG), Annals of the CIRP, 50(1) (2001) 205–208.
T. Jin, W. B. Rowe and D. F. McCormack, Temperatures in deep grinding of finite workpieces, International Journal of Machine Tools and Manufacture, 42 (2001) 53–59.
T. Jin and D. J. Stephenson, Analysis of grinding chip temperature and energy partitioning in high efficiency deep grinding, Proc. Institution of Mechanical Engineers, Part B, J. of Engineering Manufacture, 220(5) (2006) 615–625.
S. Malkin and C. Guo, Thermal analysis of grinding, Annals of the CIRP, 56(2) (2007) 760–782.
C. Guo and S. Malkin, Analytical and experimental investigation of burnout in creep-feed grinding, Annals of the CIRP, 43(1) (1994) 283–286.
N. K. Kim, C. Guo and S. Malkin, Heat flux distribution and energy partition in creep-feed grinding, Annals of the CIRP, 46(1) (1997) 227–232.
T. Jin and J. Yi, Thermal Modelling and Numerical Analysis Methods for High-Speed and High-Efficiency Grinding, China Mechanical Industry Press (2016).
W. F. Ding, J. H. Xu, Z. Z. Chen, H. H. Su and Y. C. Fu, Grindability and surface integrity of cast nickel-based superalloy in creep feed grinding with brazed CBN abrasive wheels, Chinese Journal of Aeronautics, 23(4) (2010) 501–510.
I. A. Johnstone, Critical study of high efficiency deep grinding, Doctoral Dissertation, Cranfield University, England (2002).
Y. C. Fu, Z. W. Zhang, J. H. Xu, Z. C. Zhao, B. Ping, J. He, Z. W. Liu, Y. Wang and J. Yu, High efficiency deep grinding of turbine blade roots of directional solidified nickel-based super-alloy, Journal of Nanjing University of Aeronautics & Astronautics, 46(2) (2014) 190–196.
Z. W. Zhong, K. Ramesh and S. H. Yeo, Grinding of nickel-based super-alloys and advanced ceramics, Material Manufacturing Processes, 16(2) (2001) 195–207.
C. Alessandra and T. Roberto, CBN grinding performance improvement in aircraft engine components manufacture, Proc. CIRP, 9 (2013) 109–114.
Y. Qian, J. H., Xu, Y. C. Fu and L. Tian, Grinding force and specific grinding energy of nickel based superalloy during high speed grinding with CBN wheel, Diamond & Abrasives Engineering, 31(6) (2011) 33–37.
Z. Z., Chen, J. H. Xu, W. F. Ding and C. Y. Ma, Grinding performance evaluation of porous composite-bonded CBN wheels for Inconel 718, Chinese Journal of Aeronautics, 27(4) (2014) 1022–1029.
C. W. Dai, W. F. Ding, Y. J. Zhu, J. H. Xu and H. W. Yu, Grinding temperature and power consumption in high speed grinding of Inconel 718 nickel-based superalloy with a vitrified CBN wheel, Precision Engineering, 52 (2018) 192–200.
Acknowledgments
The authors would like to acknowledge the support from the research project: study on grinding technology of high precision threads on KF7 cylindrical parts (K20164), AECC South Industry Company Ltd., 426X20200002.
Author information
Authors and Affiliations
Corresponding author
Additional information
Zhentao Shang is currently an Assistant Professor in the College of Mechanical and Vehicle Engineering at Hunan University, China. He received his Ph.D. degree in Mechanical Engineering from Hunan University in 2009. His research interests include conventional and high speed grinding technologies for difficult-to-machine materials and design of special grinding machine tools.
Rights and permissions
About this article
Cite this article
Peng, K., Lu, P., Lin, F. et al. Convective cooling and heat partitioning to grinding chips in high speed grinding of a nickel based superalloy. J Mech Sci Technol 35, 2755–2767 (2021). https://doi.org/10.1007/s12206-021-0545-9
Received:
Revised:
Accepted:
Published:
Issue Date:
DOI: https://doi.org/10.1007/s12206-021-0545-9