Abstract
Carbon fiber–reinforced polymers (CFRP) are widely utilized in the aerospace field due to their significant specific strength, specific modulus, and strong design ability. However, anisotropy and low interlaminar bonding strength lead to burr, tear, lamination, and other damages in CFRP machining. In this paper, a 3D finite element model for the milling of CFRP was carefully developed, and the cutting forces, the interlaminar stress, and the interlaminar damage were properly obtained. Typically based on the developed model, the effects of geometric parameters of the multi-tooth milling tool were precisely analyzed. Next tool geometries were optimized for suppressing the interlaminar damage in the milling of CFRP. Results convincingly show that the multi-tooth milling tool with the geometry of 1.4 mm length of the micro tooth, 38.2° left helix angle, 11 left-handed chip grooves, 15° right helix angle, 12 right-handed helix grooves, approximately rectangular of section shape of the chip groove, 10° rake angle, and 15° clearance angle efficiently delivers the optimal performance. Besides, cutting performance of numerous coated tools was also studied. Results typically show that the multi-tooth milling tool with a diamond coating maintains significant advantages in aspects of the tool life and costs compared with the uncoated and diamond-like carbon coating (DLC)-coated tools.























Similar content being viewed by others
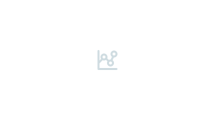
Data availability
The data that support the findings of this study are available from the corresponding author upon reasonable request.
References
Friedrich K, Almajid AA (2013) Manufacturing aspects of advanced polymer composites for automotive applications. Appl Compos Mater 20:107–128
Geier N, Davim JP, Szalay T (2019) Advanced cutting tools and technologies for drilling carbon fibre reinforced polymer (CFRP) composites: a review. Compos Part A-Appl S 125:105552. https://doi.org/10.1016/j.compositesa.2019.105552
Isbilir O, Ghassemieh E (2012) Finite element analysis of drilling of carbon fibre reinforced composites. Appl Compos Mater 19:637–656
Yashiro T, Ogawa T, Sasahara H (2013) Temperature measurement of cutting tool and machined surface layer in milling of CFRP. Int J Mach Tool Manu 70:63–69
Wang FJ, Zhang BY, Ma JW, Bi GJ, Hu HB (2019) Computation of the distribution of the fiber-matrix interface cracks in the edge trimming of CFRP. Appl Compos Mater 26:159–186
Chen T, Gao F, Li SY, Liu XL (2018) The comparative study on cutting performance of different-structure milling cutters in machining CFRP. Appl Sci 8(8):1353
Wang FJ, Zhang BY, Jia ZY, Zhao X, Wang Q (2019) Structural optimization method of multitooth cutter for surface damages suppression in edge trimming of Carbon Fiber Reinforced Plastics. J Manuf Process 46:204–213
Voss R, Seeholzer L, Kuster F, Wegener K (2017) Influence of fibre orientation, tool geometry and process parameters on surface quality in milling of CFRP. CIRP J Manuf Sci Tec 18:75–91
Jenarthanan MP, Jeyapaul R (2015) Analysis and optimisation of machinability behaviour of CFRP composites using fuzzy logic. Pigm Resin Technol 44(1):48–55
Han SC, Chen Y, Xu JH, Zhou JW (2013) Experimental study of tool wear in milling multidirectional CFRP laminates. Mater Sci Forum 770:276–280
Liu HL, Zhang JB, Wang Z, Zhang JP, Li G (2013) Cutting tool selection in CFRP and AFRP machining. Aerosp Mater Technol 43(4):95–98
Liu JD, Li YS, Yan GH, Huang LK, Yang XF, Yu DM (2015) Experimental study on surface quality in milling carbon fiber reinforced plastics. Key Eng Mater 667:62–67
Wang FJ, Yan JB, Zhao M, Wang D, Wang XN, Hao JX (2020) Surface damage reduction of dry milling carbon fiber reinforced plastic/polymer using left–right edge milling tool. J Reinf Plast Comp 39(11–12):409–442
De Lacalle LNL, Lamikiz A, Campa FJ, Valdivielso AF, Etxeberria I (2009) Design and test of a multitooth tool for CFRP milling. J Compos Mater 43(26):3275–3290
Mahdi M, Zhang L (2001) A finite element model for the orthogonal cutting of fiber-reinforced composite materials. J Mater Process Tech 113(1):373–377
Arola D, Sultan MB, Ramulu M (2002) Finite element modeling of edge trimming fiber reinforced plastics. J Manuf Sci E-T ASME 124(1):32–41
Hashin Z (1980) Failure criteria for unidirectional fiber composites. J Appl Mech 47(2):329–334
Hashin Z, Rotem A (1973) A fatigue criterion for fiber-reinforced materials. J Compos Mater 7(4):448–464
Yang L, Yan Y, Kuang NH (2013) Experimental and numerical investigation of aramid fibre reinforced laminates subjected to low velocity impact. Polym Test 32(7):1163–1173
Santiuste C, Soldani X, Maria HM (2010) Machining FEM model of long fiber composites for aeronautical components. Compos Struct 92(3):691–698
Qin XD, Li YH, Wang B, Ji CH, Guo CY, Wang H, Xin HG (2016) Simulation of effect of fiber direction on cutting process of CFRP. Mech Sci Technol Aerosp Eng 35(3):472–476
Phadnis VA, Makhdum F, Roy A, Silberschmidt VV (2013) Drilling in carbon/epoxy composites: experimental investigations and finite element implementation. Compos Part A-Appl S 47:41–51
Faraz A, Biermann D, Weinert K (2009) Cutting edge rounding: an innovative tool wear criterion in drilling CFRP composite laminates. Int J Mach Tools Manuf 49:1185–1196
Niu B, Xu HZ, Zhang QC (2020) Effects of chip groove geometry parameters on milling composite using micro-tooth milling cutter. Tool Engineering 54(12):26–30
Ishida T, Noma K, Kakinuma Y, Aoyama T, Hamada S, Ogawa H, Higaino T (2014) Helical milling of carbon fiber reinforced plastics using ultrasonic vibration and liquid nitrogen. Proc CIRP 24:13–18
Funding
The authors would like to acknowledge the financial support received from the Natural Science Foundation of China (Nos. 52075380 and 51775373) and the Natural Science Foundation of Tianjin (No. 19JCYBJC19000).
Author information
Authors and Affiliations
Contributions
Jian Liu: investigation, experimental design, data analysis, writing, and editing. Xinkai Tang: finite element model, numerical and experimental data analysis, writing, and editing. Shipeng Li: investigation, preparation of experimental materials, review, and editing. Xuda Qin: investigation, preparation of experimental materials, review, and editing. Hao Li: review and editing. Weizhou Wu: review and editing. Yadav Srijana: review and editing. Wentao Liu: review and editing. Haibao Liu: review and editing.
Corresponding author
Ethics declarations
Ethics approval
Not applicable.
Consent to participate
Not applicable.
Consent for publication
Not applicable.
Competing interests
The authors declare no competing interests.
Additional information
Publisher's Note
Springer Nature remains neutral with regard to jurisdictional claims in published maps and institutional affiliations.
Rights and permissions
About this article
Cite this article
Liu, J., Tang, X., Li, S. et al. Optimization of multi-tooth milling tool for interlaminar damage suppression in the milling of carbon fiber–reinforced polymers. Int J Adv Manuf Technol 121, 1235–1251 (2022). https://doi.org/10.1007/s00170-022-09369-9
Received:
Accepted:
Published:
Issue Date:
DOI: https://doi.org/10.1007/s00170-022-09369-9