Abstract
A system for predicting the machining error for a batch of parts in CNC wheel grinding is described; the system takes the influence of technological variables into account. Analysis of their combined influence on the machining error is based on a digital twin of the plunge grinding process. The variable machining conditions for the batch of parts (shafts) is taken into account by simulating the influence of the following factors on the machining precision: fluctuations in the margin; the blunting of the wheel grains before dressing; the pliability of the machining system over the grinding length; and positions of the active monitoring instrument in cross sections of the workpiece corresponding to different pliability of the machining system.


Similar content being viewed by others
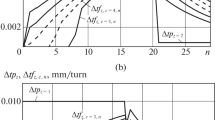
REFERENCES
Gong, Y.D., Wang, B., and Wang, W.S., The simulation of grinding wheels and ground surface roughness based on virtual reality technology, J. Mater. Process. Technol., 2002, vol. 129, pp. 123–126.
Khare, S.K. and Agarwal, S., Predictive modeling of surface roughness in grinding, Procedia CIRP, 2015, vol. 31, pp. 375–380.
Zhou, X. and Xi, F., Modeling and predicting surface roughness of the grinding process, Int. J. Mach. Tools Manuf., 2002, vol. 42, pp. 969–977.
Shirokov, A.V. and Osipov, A.P., On the issue of forecasting and ensuring the roughness parameters of the polished surface, Izv. Vyssh. Uchebn. Zaved., Mashinostr., 2007, no. 6, pp. 76–88.
Soler, Ya.I., Nguen, V.L., and Nguen, Ch.K., Prediction of shape precision of hardened steel flat parts at pendular grinding with periphery of the abrasive wheel, Mezhdunarod. Nauchno-Issled. Zh., 2013, no. 12-1, pp. 128–134.
Soler, Ya.I. and Nguyen, V.L., Modeling and predicting flatness deviations under plane grinding of parts made of 30HGSA hardened steel, Vestn. Irkutsk. Gos. Tekh. Univ., 2016, no. 4 (111), pp. 54–65.
Alsigar, M.K., Mathematical model to predict material removal rate of reverse zones, J. Adv. Res. Tech. Sci., 2018, no. 9, pp. 27–30.
Akintseva, A.V., Prokhorov, A.V., and Omelchenko, S.V., Modelling of correlation of actual and program feeds in the automatic cycle, IOP Conf. Ser.: Mater. Sci. Eng., 2020, vol. 3, art. ID 033003.
Akintseva, A.V., Pereverzev, P.P., and Ardashev, D.V., Power model of the internal grinding process, Stanki Instrum., 2019, no. 11, pp. 34–37.
Akintseva, A.V. and Pereverzev, P.P., Modeling cutting force during internal grinding with different wheel characteristics, Proc. 6th Int. Conf. on Industrial Engineering (ICIE 2020), Lecture Notes in Mechanical Engineering, Radionov, A.A. and Gasiyarov, V.R., Eds., Cham: Springer, 2021, vol. 2, pp. 548–556. https://doi.org/10.1007/978-3-030-54817-9_64
Funding
This research was funded by Ministry of Science and Higher Education of the Russian Federation (grant no. FENU-2020-0020).
Author information
Authors and Affiliations
Corresponding authors
Additional information
Translated by B. Gilbert
About this article
Cite this article
Akintseva, A.V., Pereverzev, P.P., Prokhorov, A.V. et al. Influence of Variable Machining Conditions on the Precision in CNC Plunge Grinding: Predictive Analysis by a Digital Twin. Russ. Engin. Res. 42, 721–725 (2022). https://doi.org/10.3103/S1068798X22070036
Received:
Revised:
Accepted:
Published:
Issue Date:
DOI: https://doi.org/10.3103/S1068798X22070036