Abstract
Friction welding samples of both the fire-refined high-conductivity (FRHC) and electrolytically tough pitch (ETP) copper alloy wires have been mechanically characterized by instrumented indentation technique and tensile test. Hardness profiles in the perpendicular direction to the weld interface, in both the central and peripheral zones, of the as-welded FRHC-FRHC and ETP-ETP samples have been investigated at nano-/micrometric scale. The microstructures of welds have been observed using both the optical microscopy and scanning electronic microscopy. The results show the typical friction welding zones: the interface zone, the thermo-mechanically affected zone (TMAZ), and the transition zone between the TMAZ and the base metal zone (BMZ) that present a microstructure and hardness close to the base metal. No presence of a heat-affected zone is observed. Although both welds show the same tendency in hardness distribution, FHRC-FHRC weld presents a TMAZ narrower than ETP-ETP one, which produces a stronger drop in hardness with increasing of the distance from welding central line, and a higher difference in hardness between the central and peripheral zones. The tensile tests of ETP-ETP welds showed that all samples broke by the BMZ that is far away from the interface of the welded joint, while the most of the FRHC-FRHC welds are broken at the TMAZ region at low strengths. These appreciable differences in mechanical properties for the FHRC-FHRC welds are probably generated by a stronger variation in their microstructural properties. Therefore, it may justify the welding failures in the FHRC-FHRC weld at the typical tensile stress for an industrial cold-drawn process of wires.








Similar content being viewed by others
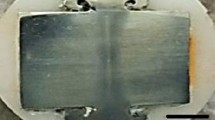
References
A. Esparducer, M.A. Fernández, M. Segarra, J.M. Chimenos, F. Espiell, M. García, and O. Guixà, Characterization of Fire-Refined Copper Recycled from Scrap, J. Mater. Sci., 1999, 34(17), p 4239–4244
A. Esparducer, M. Segarra, F. Espiell, M. Garcia, and O. Guixà, Effects of Pre-heating Treatment on the Annealing Behaviour of Cold-Drawn Fire-Refined Coppers, J. Mater. Sci., 2001, 36, p 241–245
N. Sirvent and M. Garcia, Drawability of Fire-Refined Copper in a Multiwire at High Speed, Wire J. Int., 2004, 37, p 58–61
J.O. Guixà et al., US Patent 6797082 ES Patent 9900254
M. Martínez, A.I. Fernández, M. Segarra, H. Xuriguera, F. Espiell, and N. Ferrer, Comparative Study of Electrical and Mechanical Properties of Fire-Refined and Electrolytically Refined Cold-Drawn Copper Wires, J. Mater. Sci., 2007, 42, p 7745–7749
S.A. Fabritsiev, A.S. Pokrovsky, and M. Nakamichi, Irradiation Resistance of DS Copper Stainless Steel Joints Fabricated by Friction Welding Methods, J. Nucl. Mater., 1998, 258, p 2030–2035
M. Maalekian, Friction Welding-Critical Assessment of Literature, Sci. Technol. Weld. Join., 2007, 12, p 738–759
M. Sahin, Joining of Stainless Steel and Copper Materials with Friction Welding, Ind. Lubr. Tribol., 2009, 61, p 319–324
N. Arivazhagan, S. Singh, S. Prakash, and G.M. Reddy, Investigation on AISI, 304 Austenitic Stainless Steel to AISI, 4140 Low Alloy Steel Dissimilar Joints by Gas Tungsten Arc, Electron Beam and Friction Welding, Mater. Des., 2011, 32, p 3036–3050
S.Y. Kim, S.B. Jung, and C.C. Shur, Mechanical Properties of Copper to Titanium Joined by Friction Welding, J. Mater. Sci., 2003, 38, p 1281–1287
T. Sakthivel and J. Mukhopadhyay, Microstructure and Mechanical Properties of friction Stir Welded Copper, J. Mater. Sci., 2007, 42, p 8126–8129
M. Kimura, M. Kusaka, K. Kaizu, and A. Fuji, Effect of Friction Welding Condition on Joining Phenomena and Tensile Strength of Friction Welded Between Pure Copper and Low Carbon Steel, J. Solid Mech. Mater. Eng., 2009, 3, p 187–198
M. Sahin, E. Çil, and C. Misirli, Characterization of Properties in Friction Welded Stainless Steel and Copper Materials, J. Mater. Eng. Perform., 2012, 61, p 935–943
T. Teker, Evaluation of the Metallurgical and Mechanical Properties of Friction-Welded Joints of Dissimilar Metal Combinations AISI2205/Cu, Int. J. Adv. Manuf. Technol., 2012, 66, p 303–310
A. Kurt, I. Uygur, and U. Paylasan, Effect of Friction Welding Parameters on Mechanical and Microstructural Properties of Dissimilar AISI, 1010-ASTM B22 Joints, Weld. J., 2011, 90, p 102–106
C.A. Charitidisa, D.A. Dragatogiannisa, E.P. Koumoulosa, and I.A. Kartsonakisa, Residual Stress and Deformation Mechanism of Friction Stir Welded Aluminum Alloys by Nanoindentation, Mater. Sci. Eng. A, 2012, 540, p 226–234
M. Morales, J.J. Roa, X.G. Capdevila, M. Segarra, and S. Piñol, Mechanical Properties at the Nanometer Scale of GDC and YSZ Used as Electrolytes for Solid Oxide Fuel Cells, Acta Mater., 2010, 58, p 2504–2509
M. Morales, J.J. Roa, J.M. Perez-Falcón, A. Moure, J. Tartaj, F. Espiell, and M. Segarra, Correlation Between Electrical and Mechanical Properties in La1−x Sr x Ga1−y Mg y O3−δ ceramics used as electrolytes for solid oxide fuel cells, J. Power Sources, 2014, 246, p 918–925
M. Morales, J.M. Chimenos, F. Espiell, and M. Segarra, The Effect of Temperature on Mechanical Properties of Oxide Scales Formed on a Carbon Steel in a Simulated Municipal Solid Waste Incineration Environment, Surf. Coat. Technol., 2014, 238, p 51–57
M. Morales, J.J. Roa, X.G. Capdevila, M. Segarra, and S. Pinol, Effect of Sintering Temperature on the Mechanical Properties of Film Gd0.2Ce0.8O1.9 Electrolyte for SOFCs Using Nanoindentation, J. New Mater. Electrochem. Syst., 2009, 12, p 187–193
X.-L. Zhao, Z. Xie, and P.R. Munroe, Nanoindentation of Hard Multilayer Coatings: Finite Element Modelling, Mater. Sci. Eng. A, 2011, 528, p 1111–1116
W. Oliver and G.M. Pharr, An Improved Technique for Determining Hardness and Elastic Modulus Using Load and Displacement Sensing Indentation Experiments, J. Mater. Res., 1992, 7, p 1564–1583
M. Martínez López, Estudio y caracterización de transformados de cobre FRHC, Ph.D. Thesis, Universitat de Barcelona, 2008 [in Spanish]
J. Roa, M. Martínez, E. Rayón, N. Ferrer, F. Espiell, and M. Segarra, Hardness of FRHC-Cu Determined by Statistical Analysis, J. Mater. Eng. Perform., 2014, 23, p 637–642
Acknowledgments
The authors thank La Farga Lacambra S.A. (Les Masies de Voltregà, Barcelona, Spain) for useful discussions and for financing this work. This work was partially financed by the Spanish Government UNBA10-4E-316 and FEDER-EU.
Author information
Authors and Affiliations
Corresponding author
Rights and permissions
About this article
Cite this article
Morales, M., Xuriguera, E., Martínez, M. et al. Mechanical Characterization of Copper-Copper Wires Joined by Friction Welding Using Instrumented Indentation Technique. J. of Materi Eng and Perform 23, 3941–3948 (2014). https://doi.org/10.1007/s11665-014-1204-4
Received:
Revised:
Published:
Issue Date:
DOI: https://doi.org/10.1007/s11665-014-1204-4