Abstract
Full-scale pressurized creep-rupture tests were conducted on Inconel® alloy 740 cold-formed tube bends to evaluate the effect of cold-work on the performance of tube bends for high-temperature creep applications. A new method of analysis is developed that can be used to simplify the complexities of structural (geometric) effects and material degradation due to cold-work. Results show that Inconel® alloy 740 behaves similarly to other age-hardenable nickel-based alloys subjected to cold-work prior to creep testing with large reductions in rupture life and ductility and a corresponding moderate increase in minimum creep rate. The results also demonstrate that the full-size test method can be a beneficial to understanding the performance of large components in service.
Similar content being viewed by others
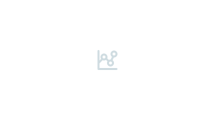
Introduction
Power steam boiler superheater and reheater components operate at temperatures and pressures where creep is the dominant deformation mode, and the fabrication of these components often involves extensive cold-bending of tubing. Because material creep behavior can be negatively affected by cold work, the ASME Boiler and Pressure Vessel Code imposes strain limits for forming without a post-bending heat-treatment that depend on the material, operation temperature, and strain level (Ref 1). The limits are based primarily on field experience. In order to use new materials in boiler design, one method to evaluate the long-term performance of cold-formed tube bends is to conduct full-size pressurized creep-rupture experiments on fabricated bends (Ref 2). The advantages of conducting full-scale tests are that strain gradients produced by forming are accounted for in the test, the complexity of creep stress redistribution and damage development is realistically reproduced, and the results can be applied directly to real components. The disadvantage is that it is difficult to separate out the effects of multiaxial creep loading and changes in material creep behavior due to cold work. Thus, the primary objective of this study is to develop a simplified analysis method to accomplish this.
The material we have chosen to investigate is the age-hardenable nickel-based alloy Inconel® 740, hereafter referred to as alloy 740. This material is a prime candidate for the highest temperature superheater and reheater components to be used in Advanced Ultrasupercritical (A-USC) steam cycles with operating steam temperatures up to 760 °C. Such materials will help to increase efficiency and decrease emissions of all effluents (including CO2) in coal-fired power plants by up to 25% over current technology (Ref 3, 4). However, very little is known about the effect of cold-work on creep in the alloy (Ref 5). Therefore, full-scale pressurized creep-rupture tests were utilized to assess the practical forming limits of the alloy and develop an improved understanding of its creep behavior in the cold-worked condition.
Background—Cold-Work and Creep of Nickel-Based Alloys
For nickel-based materials subjected to plastic deformation (pre-strain) prior to creep, creep-rupture life may increase or decrease depending on the alloy system (Ref 6). Age-hardenable nickel-based alloys of composition similar to alloy 740, which are primarily strengthened by the precipitation of gamma prime, all display significant decreases in rupture life and rupture ductility and a small increase in minimum creep rate when subjected to prior cold plastic deformation with pre-strain levels between 0.35 and 25% (Ref 7-13). The reduction in creep ductility and rupture life is due to a marked increase in cavity density in the pre-strained material as compared to un-strained material (Ref 7, 11). Research shows that very fine (submicron size) cavities are formed on grain boundaries during cold deformation (Ref 8) and in some cases are associated with grain boundary particle microcracking (Ref 9) or particle matrix interface separation (Ref 13). In general, the density of pre-strained cavities is greatest on grain boundaries parallel to the applied pre-strain stress, but creep cavitation occurs on grain boundaries normal to the axis of the applied creep stress. Torsional creep experiments designed by Dyson and co-workers showed that when the creep stress was applied on the axis orthogonal to the applied tensile stress, a larger reduction in creep life and ductility was observed compared to applying the pre-strain and creep stress in parallel direction (Ref 8). This is important in consideration of tube bend performance because the stress due to the applied pressure (hoop stress) is normal to the applied bending (cold-strain) stress. The reduced creep resistance (increase in creep rate) has been found to be independent of cavitation and may be attributed in an increase in mobile dislocation density (Ref 7, 10). Only one limited study is reported on Inconel® alloy 740 which showed the rupture life was reduced by half when pre-strain was 7.5% (Ref 11).
Experimental Procedure
Alloy 740 tubes and cold-formed tube bends with a nominal 50.8 mm diameter (dia.) and 10.2 mm wall thickness and a measured composition of (wt.%): Ni-0.03C-0.28Mn-0.42Fe-0.54Si-24.43Cr-0.94Al-1.81Ti-20.00Co-0.55Mo-1.98Nb-0.0030B-(S < 0.001-P < 0.005) were provided by Foster Wheeler Development Corp. Tensile creep specimens (un-strained) were machined from the tubes with a 6.35 mm gage dia. and 31.75 mm gage length, aged at 1073 K (800 °C) for 16 h, and uniaxial creep tests were conducted at 1073 K (800 °C) in accordance with ASTM E139. Tubes in the solution annealed condition were bent using conventional boiler tube bending equipment at room temperature to nominal radii of 171.5, 127, and 76.2 mm.
Test specimens were fabricated by sectioning the tube bends into a “J-shaped” arrangement which included the entire 180° bend and a short, ~100 mm, straight tube section on one end. Solid end caps (alloy 230) were welded (manual GTAW, alloy 263 filler metal) to each end of the specimen, and the tube was partially filled with 304 stainless steel balls to reduce the volume of gas needed for testing. A pressure stem was welded to the end cap which protruded through the furnace and was attached to standard high-pressure stainless steel autoclave tubing. Figure 1 shows the J-bend specimen during fabrication. Prior to testing, the fabricated tube bend specimens were aged for 16 h at 1073 (800 °C). Paint was used to make marks at ~25 mm intervals along the extrados of the bend and straight section. Prior to testing, after predetermined intervals, and after failure, the tube diameter was measured at each mark at 0°, 45°, 90°, and 135° around the circumference.
All specimens were tested simultaneously in a large furnace with type K thermocouples attached directly to the specimens to monitor temperature. Ar-5%He gas pressure was applied and measured individually on each specimen by an in-line pressure transducer. Testing was conducted at 1073 K (800 °C) ± 2 K (2 °C) and 485.4 bar ± 1.8 bar. Tests were interrupted periodically for strain measurement, and conducted until a through-wall leak was detected. Destructive metallographic assessments were conducted after testing utilizing optical microscopy (OM) and scanning electron microscopy (SEM). Reference 2 provides photographs of similar test specimens and the facility utilized for testing.
Results
Tube Bends
The ASME outer fiber strain (OFS) for the bends was calculated from:
where r is the tube radius and R is the bend radius (Ref 1). Table 1 provides the calculated cold-strain and time to rupture results for the tube bends. The tighter radius bends with higher cold-strain failed at shorter times compared to the bends with less cold-strain. Figure 2 is a macroscopic image of the extrados on the bend apex for the 35%OFS sample after rupture; extensive macroscopic cracking is clearly observed.
Uniaxial Creep Data
Results of uniaxial creep tests on un-strained specimens conducted at 250, 180, and 130 MPa are plotted with additional data from other heats of alloy 740 (Ref 14, 15) in Fig. 3, 4, and 5. A time-temperature parameter analysis of an alloy 740 uniaxial time to rupture, t r (h), database has been fit with good accuracy to (Ref 14):
where C is the Larson-Miller constant = 19.70, A 1 = 3.3095E04, A 2 = −3.4551E04, A 3 = −4.5335, σ is stress (MPa), and T is temperature (K). The data from this study and other heats compare well with Eq 2. The minimum creep rate data, \( \dot{\upvarepsilon }_{\min } \) (%/h), in Fig. 4 was fit to usual form (Ref 16) with a power-law (Norton) exponent of 5.3 giving:
Time to rupture data at 1073 K (800 °C) from this study on alloy 740 tubes plotted with expected behavior from Eq 2
The elongation at failure data, Fig. 5, was converted to true strain at failure (εr) and fit to the following equation for rupture times up to 7000 h:
Microstructure
Figure 6 is a SEM secondary electron image of the gage section of an un-strained uniaxial specimen after creep testing to failure for 1633.6 h. Wedge cracks and cavities are dispersed throughout the specimen on grain boundaries perpendicular (normal) to the applied stress. Figure 7 is an OM image taken after failure of the 15%OFS tube bend test. The location is the bend apex at the outer diameter (OD) of the extrados. Extensive cavitation and microcracking is observed at a much higher density compared to Fig. 6. The creep damage is aligned normal to the direction of the applied pressure (hoop) stress. Figure 8 shows this same location at a higher magnification. Cavities are primarily located on grain boundaries and in some cases twin boundaries normal to the applied hoop stress. The 25 and 35%OFS samples showed similar creep damage after testing in the same location.
Figure 9 is a number of optical images taken around the circumference of the 15%OFS tube bend for both the OD and the inner diameter (ID). The images include the apex starting at the extrados, moving 60° radially from the extrados towards the neutral axis (90°), and at the intrados (180° from the extrados) The highest degree of cavitation and microcracking is observed at the OD of the extrados. Cavitation is found in all locations, and the 120° location (not shown) was similar to the 60° findings. In these locations most cavities are isolated, but the ID of the 60° location and the OD of the intrados showed some cavity alignment, indicating a slightly more advanced degree of creep damage. Similar evaluations conducted on the 35% and 25%OFS samples revealed that the microstructures displayed similar trends. For the 15% and 25%OFS samples, intergranular creep failure initiated on the OD and progressed via linked microcracks. Similarly, the 35%OFS sample had extensive creep damage on the extrados OD (see Fig. 2), but in contrast to the other tube tests, failed at the 60° location with damage initiating on the ID.
Discussion
Analysis of Tube Bend Data
To evaluate the tube bend test results in terms of rupture life, rupture ductility, and creep deformation, several assumptions were made. For rupture life, a reference stress, which can be thought of as the ‘average’ stress in a component that controls creep deformation, was considered to relate the stress in the uniaxial creep test to the more complex geometry of the thick-wall tube bend. Recent work comparing large databases of pressurized straight tube creep-rupture tests have shown the one particular definition of the reference stress (\( \upsigma_{\text{REF}}^{\text{StraightTube}} \)) for a tube under internal pressure gives good agreement over a range of tube sizes, conditions, and materials (Ref 17-19). This definition, which has recently been adopted as an alternative for design of components in ASME boiler and pressure vessel code Section I (Ref 1), is given by:
where P is the internal pressure, r o is the external radius, and r i is the internal radius (Ref 17). Similar methods have provided a reference stress (\( \upsigma_{\text{REF}}^{\text{TubeBend}} \)) for a tube bend based on the tube thickness (t), the radius of the bend (a), and the mean diameter of the tube (b) given by:
although there is limited experimental data to verify its accuracy (Ref 20, 21). The stresses calculated for the tube bends and the straight tube section are provided in Table 2, which shows that the stress in the bends approach the straight tube stress as bend radius increases. Figure 10 compares the tube bend time to rupture results with the uniaxial un-strained data, the expected behavior for alloy 740 (Eq 2), and the minimum expected rupture life (−20% on stress). The figure shows that, even accounting for the increase in stress due to the tube geometry, the data for the tube bend failures all fall well below the uniaxial behavior and even below the minimum life. Therefore, creep life is significantly reduced in alloy 740 due to cold-straining to levels of 15% or greater.
Time to rupture for tested tube bends (stress calculated from Eq 6) compared to un-strained uniaxial data and minimum (−20%) data
Evaluation of creep ductility must take into account any ovality in the tube bend. Ovality was calculated based on the maximum (d max) and minimum (d min) diameter measurements on the OD as follows:
Since the degree of ovality may change during creep, the circumference of the oval tube, which in earlier work was only considered as a circle (Ref 2), was approximated to obtain an average strain using:
Figure 11 shows the calculated ovality and strain measurements based on Eq 7 and 8 for the 15%OFS sample including the bend and straight section regions. At time zero, when the OD creep strain is 0, the sample has 2 to 3% ovality. As creep strain accumulates, the ovality decreases. The creep strain in the bend region is relatively uniform despite differences in measured ovality, presumably because creep deformation is uniform and Eq 8 accounts for the changing ovality. At failure, the ovality in the bend is nearly zero and the scatter is the same as the straight tube section. Data from power plant piping operating in the creep regime which failed with over 100,000 h of service showed a similar finding, that is, that ovality was reduced during operation, but did not reach zero ovality until failure (Ref 22). Thus, the tube bend tests, although less than 5000 h, appear re-produce realistic long-term in-service behavior.
To analyze the observed failures strains in Table 2, the effects of multiaxiality on creep were considered. Research on notched bars of alloy 740 tested at 750 °C showed that ductility obeyed Spindler’s equation (Ref 23, 24):
where p and q are constants (= 0.15 and 1.25, respectively), σ1 is the maximum principle stress, σVM is the effective stress, and σm is the mean stress. This gives a ratio of multiaxial strain at failure to uniaxial strain at failure of ~0.70 for a tube under internal pressure. The tube geometry is considered for simplicity since the authors have no knowledge of an approximation for the principle stresses in the bend. Utilizing the relationship established for uniaxial ductility (Eq 4) and the ratio obtained from Eq 9, Table 2 compares the calculated strain at failure to the actual measured true strain at failure for the tube bends. These data show the tube bends failed at significantly lower ductility compared to the prediction, approximately 0.1 to 0.2 of the calculated strain at failure. Therefore, the dramatic reduction in rupture ductility of alloy 740 tube bends is primarily due to the effect of pre-strain (cold-work) and not multiaxility.
To evaluate the creep deformation, the OD strain measurements were averaged for the data collected on each bend and on each straight section. These data along with the rupture strain are plotted in Fig. 12. The uniaxial creep tests on alloy 740 showed an increasing creep rate (tertiary creep) with little to no primary or secondary creep typical of many nickel-based alloys. The tube ‘creep-curves’ in Fig. 11 exhibit the same behavior. Since limited interrupted measurements were made on the tubes, the minimum creep rate was measured based on the first recorded datapoint, but could be slightly lower if shorter-term measurements were made. The data are reported in Table 2 and compared to the expected minimum creep rate calculated from Eq 3. The minimum creep rate for the straight section of the tube is in good agreement with the calculated uniaxial value indicating the reference stress is an appropriate approximation for the creep behavior of the structure, and the minimum creep rate based on the first OD measurement is reasonably accurate. With decreasing bend radius, the creep rate progressively increases which is consistent with increasing stress in the bend itself. However, when compared to the uniaxial expectations, the creep rates are ~6-10 times greater in the bends than the uniaxial data. Therefore, it appears cold-work does have a measurable weakening effect on creep deformation behavior of alloy 740.
Microstructure and Evaluation of Data
Extensive cavitation was noted in the region of highest strain (OD of the extrados) after creep testing in all the samples (Fig. 6). The cavity density is much higher compared to the un-strained uniaxial tests (Fig. 5), and cavitation is primarily on grain boundaries normal to the applied stress, which in this case is the pressure (hoop) stress. The damage is consistent with other nickel-based alloys with similar levels of gamma prime such as Nimonic 80A (Ref 7) and alloy 263 (Ref 10) which were pre-strained prior to creep. In this work, alloy 740 was cold-strained in the solution annealed condition whereas all the other reported tests induced cold-strain after the aging heat-treatment (which was used to precipitate gamma prime). The current work shows, that regardless of processing path, cold-work is detrimental to creep by greatly increasing the cavitation density.
A second important observation is the role of compressive cold-strain. Figure 9 shows that the region of highest compressive cold-strain (OD of the intrados), which should be equal in magnitude to the OD of the extrados if bending is uniform, had significantly less creep damage that the region of highest tensile cold-strain. Since grain interior slip is considered to be the main source of submicron cavitation (Ref 8), and because the applied creep stress (hoop stress) was normal to the cold-strain stress, little difference should be expected. However, due to conservation of volume and the type of bending utilized, the extrados of the tube bend was thicker than the intrados. Since the analysis methodology did not account for this change in thickness, the reduction in cavitation may be simply explained by a thicker wall leading to a lower stress.
The final failure location of the 25% and 15%OFS samples was in the region of highest tensile cold-strain, indicating that cold-work is a significant factor in controlling the creep life of the tube bend. Advanced damage was observed on the 35% sample in the same location, but failure initiated on the ID. There are two factors which could lead to higher stresses in this area. First, when a thick-walled tube is elastically loaded, the highest stress is on the tube ID, but during creep this stress relaxes and the highest creep stress redistributes to the tube OD (Ref 25). Because the 35% test was the shortest in duration, the high stresses may not have fully relaxed, leading to ID damage. A second factor is the change in ovality. As the data clearly show, the creep process reduces the ovality in the tube and the strain measurements are based on an averaged circumference. However, in reality, the strain must be non-uniform, and careful inspection of the raw OD measurement data revealed that most of the creep strain accumulation was not at the intrados or extrados of the bend but rather between the two. Thus, while creep damage is unequivocally linked to the extrados where the tensile cold-strain was highest, measured creep deformation was more pronounced towards the neutral axis. The ID of the 60° location had both higher tensile cold-strain and the stress redistribution due to ovality, and hence even in the longer-term test, the level of creep damage in that location is higher than other regions around the tube, expect for the area of highest cold-strain (Fig. 8).
The analysis methodology presented in the previous section showed that the rupture life reduction, reduction in creep ductility, and increase in minimum creep rate could not be explained by geometric effects alone, but rather that prior cold-work had a significant impact on component lifetimes and creep behavior. To examine if the reductions were within expectations based on similar alloy performance, the data from Ref 7-13 were normalized relative to uniaxial experiments on un-strained material in the same studies. In this work, a parallel uniaxial study was not conducted, so the comparison is made between the measured property from the tube bend test and the expected or calculated property of interest from the analysis methods applied to uniaxial un-strained specimens in this work, all of which is found in Table 2. The OFS calculation was used as the amount of cold-work for this comparison since the results showed the creep damage was concentrated, and ultimately rupture life was controlled by the location in the tube with this nominal level of strain.
Figure 13 is a comparison of the normalized rupture life data as a function of cold-strain. An exponential line was fit through the data from Ref 7, 8, 10-12. Data from IN597 (Ref 9) and Astroloy (Ref 13) were not fit because these alloys have much higher amounts of gamma prime compared to alloy 740 and the other alloys. Additionally, the research shows particle/interface cracking as a possible mechanisms leading to enhanced cavitation which is not expected since alloy 740 was formed in the annealed condition. The tube bends were not included in the extrapolation, but inspection of the figure shows the tube bend data is generally consistent with the other data. At 15% and greater cold work, the rupture life is 0.25 or less than the non-strained material and decreases with increasing cold-work. Few data are available beyond 15%, so the extrapolation is slightly conservative, but overall the tube bend analysis appears adequate for considering the effect of rupture life reduction due to cold-work in alloy 740.
Figure 14 shows a similar result for normalized creep-rupture ductility. Again, the tube bend analysis is generally consistent with the exponential extrapolation of similar literature data. The comparison from the tube bend analysis captures the same trend as the data and shows the reduction is approximately 0.2 to 0.1. The analysis takes into account the reduction in ductility due to multiaxial creep as well as the material behavior observed in un-strained specimens where ductility was a function of test time.
Figure 15 is a plot of increase in minimum creep rate as a function of material and cold-work. A linear extrapolation of the available literature data on age-hardenable nickel-based alloys shows very good agreement both in relative increase and absolute values. This suggests that alloy 740 behaves similarly to the other alloys and that the methodology presented in this work for approximating stress in the tube bends is accurate for creep prediction.
Conclusions
Full-scale pressurized creep-rupture tests were conducted on alloy 740 cold-formed tube bends to evaluate the effect of cold-work on the performance of tube bends for high-temperature applications. Results show that the full-size test method can be used to understand the performance of these components in service. Specifically, the methodology provides a way to simplify the complexities of structural (geometric) effects and material degradation due to cold-work during creep. Observed changes in ovality were similar to in-plant observations, comparisons with expectations from uniaxial creep rate data, and comparisons with literature data on similar alloys, thus verifying the validity of the analysis methods.
Specific finding for alloy 740 were:
-
Cold-work is detrimental to the creep behavior of alloy 740 even when aging is conducted after cold-working.
-
The rupture life reduction, significant reduction in creep ductility, and moderate increase in minimum creep rate are similar to other nickel-based alloys.
-
The number of creep cavities is greatly increased in the tube bend tests normal to the pressure (hoop) stress with the areas of highest tensile cold-strain having micro- and macrocracking, consistent with literature data on similar alloys.
-
At 15%OFS (cold-work), the reduction in creep life for alloy 740 is greater than the minimum scatter band for creep data; thus, creep based designs with alloy 740 should consider lower cold-forming limits.
Additional research is required to clarify the differences observed in creep damage for tensile and compressive cold-strain and identification of a minimum acceptable cold-work limit for the alloy.
References
“2010 ASME Boiler and Pressure Vessel Code, Section I—Rules for Construction of Power Boilers,” © 2010 The American Society of Mechanical Engineers
J.P. Shingledecker, Creep Rupture Behaviour and Recrystallisation in HR6W and Haynes Alloy 230 Cold Bent Boiler Tubing for Ultrasupercritical Steam Boiler Applications, Energy Mater., 2008, 2(4), p 235–240
R. Viswanathan, R. Purgert, and U. Rao, Materials for Ultra-Supercritical Coal-Fired Power Plant Boilers, Materials for Advanced Power Engineering 2002—Proceedings Part II (Liege, Belgium), Forschungszentrum Julich GmbH, 2002, p 1109–1129
R. Viswananthan, J.F. Henry, J. Tanzosh, G. Stanko, J. Shingledecker, B. Vitalis, and R. Purgert, U.S. Program on Materials Technology for Ultra-Supercritical Coal Power Plants, J. Mater. Eng. Perform., 2005, 14(3), p 281–292
J.P. Shingledecker and I.G. Wright, Proceedings to the 8th Liege Conference on Materials for Advanced Power Engineering 2006 (Liege, Belgium), Forschungszentrum Jülich GmbH, 2006, p 107–120
M. McLean and B.F. Dyson, Modeling the Effects of Damage and Microstructural Evolution on the Creep Behavior of Engineering Alloys, J. Eng. Mater. Technol., 2000, 122, p 273–278
B.F. Dyson and M.J. Rodgers, Prestrain, Cavitation, and Creep Ductility, Met. Sci., 1974, 8, p 261–266
B.F. Dyson, M.S. Loveday, and M.J. Rodgers, Grain Boundary Cavitation Under Various States of Applied Stress, Proc. R. Soc. Lond. A, 1976, 394, p 245–259
M.S. Loveday and B.F. Dyson, Prestrain-Induced Particle Microcracking and Creep Cavitation in IN597, Acta Metall., 1983, 31, p 397–405
Y.H. Zhang and D.M. Knowles, Prestraining Effect on Creep Behavior of Nickel Base C263 Superalloy, Mater. Sci. Technol., 2002, 18, p 917–923
K. Kubushiro, K. Nomura, S. Takahashi, M. Takahashi, and H. Nakagawa, Effect of Pre-Strain on Creep Properties of Alloy 740, Advances in Materials Technology for Fossil Power Plants, Proceedings from the Sixth International Conference, Aug. 31-Sept. 3, 2010 (Santa Fe, NM, USA), EPRI, ASM International, 2010, p 164–170
H. Burt, I.C. Elliott, and B. Wilshire, Effects of Room-Temperature Prestrain on Creep-Fracture Behaviour of Nimonic 105, Met. Sci., 1981, 15, p 421–424
T. Saegusa, M. Uemura, and J.R. Weertman, Grain Boundary Void Nucleation in Astroloy Produced by Room Temperature Deformation and Anneal, Metall. Trans. A, 1980, 11A, p 1453–1458
R. Viswanathan, J. Shingledecker, J. Hawk, and S. Goodstine, Effect of Creep in Advanced Materials for Use in Ultrasupercritical Power Plants, Proceedings Creep & Fracture in High Temperature Components, 2nd ECCC Creep Conference, April 21–23, 2009 (Zurich, Switzerland), DEStech Publications, Inc., 2009, p 31–43
J. Shingledecker and M. Santella, Oak Ridge National Laboratory, Oak Ridge, TN, 2010, unpublished research
T.H. Courtney, Mechanical Behavior of Materials, Chap. 7, 2nd ed., McGraw-Hill, New York, 2000
J.D. Fishburn, Single Technically Consistent Design Formula for the Thickness of Cylindrical Sections Under Internal Pressure, Proceedings of the ASME Pressure Vessels and Piping Conference 2005—Codes and Standards PVP2005 (V1), American Society of Mechanical Engineers, 2005, p 291–295
I.J. Perrin and J.D. Fishburn, A Perspective on the Design of High-Temperature Boiler Components, Int. J. Press. Vessels Pip., 2008, 85, p 14–21
J.P. Shingledecker, Tensile and Creep-Rupture Evaluation of a New Heat of Haynes Alloy 25, ORNL/TM-2006/609, Oak Ridge, TN, February 2007
A.G. Miller, Review of Limit Loads of Structures Containing Defects, Int. J. Press. Vessels Pip., 1988, 32, p 197–327
Boiler Materials for Ultrasupercritical Coal Power Plants—Task 8, An Overview of Reference Stress Approach, USC T-6, NETL/DOE/OCDO, EPRI Palo Alto, CA, 2003
L. Yu-De and L. Zi-Li, Creep Strain, Elliptical Release and Additional Stress of the Elbows in Main Steam Piping, Int. J. Press. Vessels Pip., 1994, 57, p 135–139
J.P. Shingledecker and G.M. Pharr, The Role of Eta Phase Formation on the Creep Strength and Ductility of INCONEL® Alloy 740 at 1023 K (750 °C), Met. Trans. A, 2012, 43(6), p 1902–1910, doi:10.1007/s11661-011-1013-4
M.W. Spindler, The Multiaxial Creep Ductility of Austenitic Stainless Steels, Fatigue Fract. Eng. Mater. Struct., 2003, 27, p 273–281
I. Finnie and W.R. Heller, Creep of Engineering Materials, Chap. 7, McGraw-Hill, New York, 1959
Acknowledgments
Research at Oak Ridge National Laboratory (Oak Ridge, TN USA) was supported by the U.S. Department of Energy (DOE), Office of Fossil Energy, Advanced Research Materials Program, the DOE/OCDO USC Steam Boiler Consortium, and the ORNL SHaRE User Center, Division of Materials Sciences and Engineering, Office of Basic Energy Sciences, U.S. DOE, under Contract DE-AC05-00OR22725 with UT-Battelle, LLC. Special thanks to B. Sparks and T. Geer (ORNL) for their assistance with the experimental work and G. Stanko (Foster Wheeler Development Corp.) for supplying the material and components for this study. The support of consortium sponsors R. Romanosky and P. Rawls (NETL) is appreciated. This publication was prepared with partial support of the U.S. Department of Energy, under Award No. DE-FG26-01NT41175 and the Ohio Coal Development Office of the Ohio Department of Development under Grant Agreement Number CDO/D-0020 (now D-05-02A). However, any opinions, findings, conclusions, or recommendations expressed herein are those of the author(s) and do not necessarily reflect the views of the DOE and/or the Ohio Coal Development Office of the Ohio Department of Development.
Author information
Authors and Affiliations
Corresponding author
Rights and permissions
About this article
Cite this article
Shingledecker, J.P., Pharr, G.M. Testing and Analysis of Full-Scale Creep-Rupture Experiments on Inconel Alloy 740 Cold-Formed Tubing. J. of Materi Eng and Perform 22, 454–462 (2013). https://doi.org/10.1007/s11665-012-0274-4
Received:
Revised:
Published:
Issue Date:
DOI: https://doi.org/10.1007/s11665-012-0274-4