Abstract
Copper coatings are an important group of decorative-protective materials characterised by high corrosion resistance, excellent thermal and electrical conductivity, which lately gained more significance due to their antimicrobial activity. The main aim of the presented research was to electrodeposit homogenous copper coatings from the non-cyanide electrolyte solution in galvanostatic conditions on steel (1.4024) and nickel (Ni201) substrates, commercially used for surgical instruments. The effect of substrate finishes used in the production line, by shot peening with glass balls, corundum treatment and brushing on the coatings surface formation, was investigated. The substrates’ and coatings’ microstructural properties were analyzed by scanning and transmission electron microscopy, atomic force microscopy, and X-ray diffraction analysis. The current efficiency of the copper reduction on nickel and steel substrates was found to be above 95%. The copper layers adhere to both substrates, except those deposited on a brushed surface. Regardless of the substrate used, they have a nanocrystalline structure with an average crystallite size of 30 nm. Moreover, the coating surface morphology, which affects the nature of interaction with microorganisms, was effectively modified by the appropriate substrate finishing without changing the electrodeposition conditions.
Similar content being viewed by others
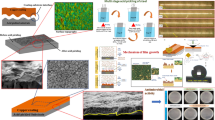
Avoid common mistakes on your manuscript.
1 Introduction
Copper coatings are commonly applied in many industrial sectors due to their high corrosion resistance, excellent electrical and thermal conductivity. Recently, copper has also gained renewed attention as an antimicrobial material, which can serve as the protective barrier inactivating pathogenic microorganisms by so-called ‘contact killing’, especially needed on the surface of medical elements and devices [1]. Therefore, our research is associated with copper coatings dedicated to surgical tool production [2].
It is assumed that the release of copper ions from copper and copper alloy surfaces can generate hydroxyl radicals as well as inactivate metalloproteins resulting in the bacterial membrane and intracellular damage. Among numerous methods of coating preparation, electroplating, based on the electrolysis reactions, is a relatively simple and low-temperature (not exceeding 100 °C) way of producing such material with the desired thickness, chemical composition, and microstructure. Additionally, Zeiger et al. [3] reported that the electrodeposited copper layer revealed enhanced antibacterial properties compared with the polished and native rolled copper due to a more effective release of copper ions determined by the layer’s rougher structure.
The copper coatings electrodeposition from an aqueous solution is the subject of numerous scientific studies. Various types of baths containing different complexing agents: glutamate [4], lactate [5], ethylenediamine [6], triethanolamine [7], aminoacetate [8], tartrate [9], pyrophosphate [10], methanesulfonate [11], and ammonia [12] were tested. However, in practice, most copper coatings are deposited from sulphate and cyanide baths, ensuring high process efficiency and low operating costs. Cyanide solutions allow to obtain uniform coatings, well adherent to the steel substrate, but are highly toxic and provide environmental problems with the disposal of spent solutions. Hence, the use of sulphate-based baths can be treated as the compromise between producing coatings with satisfactory quality and ecological aspects. These are solutions with simple compositions based on copper (II) sulphate and sulfuric (VI) acid, characterised by high durability and low price [13].
Therefore, sulphate baths were selected to produce antipathogenic copper coatings on stainless steel (1.4024) and nickel (Ni201) substrates, commercially used for surgical instruments like tweezers. The first problem to be solved was to determine the impact of substrate finishes methods used in the surgical tools production line by shot peening with glass balls, corundum treatment, brushing, and electropolishing techniques on the electrodeposition process and quality of the coatings. To verify this effect, the substrates and coatings microstructures were analysed in detail by scanning and transmission electron microscopy, atomic force microscopy, and X-ray diffraction methods.
2 Materials and methods
Copper layers were electrochemically deposited on stainless steel (1.4024) and nickel (Ni201) planar cathodes with a working area of 0.06 dm2, provided by the Factory of Medical Instruments CHIRMED. Different surface finishes (applied in the production line): matt finish prepared on the SABLUX machine by shot peening with glass balls of the average size of 40-70 µm (MATT1) and 70–110 µm (MATT2); electropolished with corundum particles of the average size of 425–500 µm (ECOR) using the Flex Kraft rectifier (voltage of 9 V, for 2 minutes) and brushing (BRUSHED) on the polishing disc with the gradation of 240 were tested. Before the experiments, all substrates were cleaned in ethanol using the ultrasound field. The steel substrates were additionally etched in NaOH and HCl solutions to remove the oxide layers. The electrolysis was conducted in an acidic aqueous electroplating bath containing 240 g/l of copper (II) sulphate and 60 ml/l of sulfuric (VI) acid, in the galvanostatic conditions (3 A/dm2), at room temperature (24 ± 1 °C), for 10 minutes. A copper sheet of ~0.25 dm2 area was used as an anode. The current efficiency of copper electrodeposition was calculated as the ratio of the deposited mass to the theoretical mass according to Faraday’s law (1, 2):
where:
The coatings’ surface morphology and cross-section microstructure were analyzed by scanning electron microscopy (SEM) using an FEI ESEM XL-30 microscope. Thin foils from selected samples of ~100 nm thickness for transmission electron microscopy (TEM, Tecnai G2, 200 kV) observations were prepared by the focused ion beam (FIB) technique (Thermo Fisher Scientific SCIOS 2 Dual-Beam). Additionally, the atomic force microscope (AFM) operating in the tapping mode (SPM Innova, Bruker with the NanoScope Analysis 1.4 software) was applied to the surface topography analysis and roughness measurements in the imaging area of 100 μm x 100 μm, 20 μm x 20 μm and 2 μm x 2 μm according to ISO-25178 standard. The sample's surface was analyzed and compared using the AFM images, the parameters of the mean roughness Sa, kurtosis, and skewness. Before each measurement, the sample was placed in ethanol, cleaned for 30 minutes in ultrasound, and then dried. The phase composition and the average crystallite size (based on the Scherrer method) were analyzed by the X-ray diffraction technique (D8 Discover, Bruker with a cobalt anode, with a wavelength of 1.79 Å).
3 Results and discussion
Copper electrodeposition from non-cyanide electrolyte solution on the steel substrate is challenging due to the contact exchange of the copper ions/iron pair and iron passivation. Therefore, it was necessary to use chemical etching to provide good adherence to the steel substrate. As shown in Fig. 1, all coatings are generally characterized by good adhesion to the steel substrate. The current efficiency of copper electrodeposition on steel and nickel substrates at the same operating conditions was not affected by the type of surface finishing being above 95 %.
SEM images of the surface and cross-section of copper coatings electrodeposited on the steel substrate with different finishes. The first row on the left shows the steel substrate surface, while the middle one copper coating surface electrodeposited on the steel. On the right row, the coating/steel substrate cross-sections are presented
The microstructure and surface development significantly affect physico-chemical properties of electrodeposited copper coatings and play a major role in pathogen contact killing [3]. On the substrates’ surface the presence of firmly bounded parts of glass particles and corundum was found, examples of which were indicated by arrows in Figs 1 and 2. Matt finish by shot peening with glass balls and electropolished with corundum particles are finishing methods (described in Experimental section) applied on final products. Therefore, after the process, local incorporation of the ceramic material into the substrate surface is observed and according to the manufacturer, their presence is inevitable.
SEM images of the surface and cross-section of copper coatings electrodeposited on the nickel substrate with different finishes. The first row on the left shows the nickel substrate surface, while the middle one copper coating surface electrodeposited on the nickel. On the right row, the coating/substrate cross-sections are presented
However, during the electrodeposition, it was possible to build up these electrochemically non-active places with a copper layer, and only local areas with still visible particles were observed. For brushed substrates, the surface of the steel and nickel was contamination free. Growing coatings imitated the surface topography of substrates, which is especially visible on the brushed substrate and formed the characteristic globular surface morphology, also observed for deposits obtained from glutamate [4], tartrate [9], and methanesufonic-based [11] electrolyte solutions.
Figures 3 and 4 show the AFM topography images of nickel and steel substrates with different surface finishes, and copper layers electrodeposited on them. The surface topography of almost all materials has a multi-scale nature, which should be considered depending on the analyzed properties and their intended use [14]. Therefore, in the atomic force microscopy measurements of copper coatings, which are tested as antipathogenic layers for medical, reusable instruments, different imaging scales were used—2 µm × 2 µm, 20 µm × 20 µm and 100 µm × 100 µm. The roughness of the surface analyzed on a smaller scale (2 µm × 2 µm, 20 µm × 20 µm) can provide information about the adhesion of bacterial or viral cells to the coatings [15]. On the other hand, surface topography analysis on a larger scale (100 µm × 100 µm) should also be conducted as a factor affecting the hydrophobicity of coatings, their mechanical, wear and anticorrosion properties [16]. These dependencies will be the subject of our next paper.
As seen in three-dimensional AFM images (Figs. 3 and 4), the substrates after shot-peening and corundum treatment had a non-directional, randomly deformed surface. On the other hand, the application of the brushing procedure caused the formation of parallel and uniform scratches on the surface. These substrates (both Ni and steel) were characterized by the lowest surface roughness in comparison with the MATT1, MATT2 and ECOR. However, this finishing method negatively affects the adhesion of the copper coating to the steel substrate, resulting in the local layer delamination (Fig. 1).
Regardless of the measurement scale for ECOR substrates, the largest surface heterogeneity and roughening was observed, which was also confirmed by the SEM cross-section observations.
During electrodeposition layer crystallisation occurs preferentially on the cathode (substrate) protrusions compared to the valley regions, which are not equally supplied with metal ions in the diffusion layer. Hence, such localised metal ion discharge, determined by the distribution and size of these defects, leads to a surface roughness increase with the electrodeposition time [17]. Therefore, the obtained copper coatings are characterized by a higher roughness than the substrates on which they were deposited (Fig. 5).
Such cavities may be privileged places for the microorganism's accumulation (especially when their size is comparable), increasing the available contact area and facilitating adhesion processes [15]. As for the substrates, the roughness values registered for electrodeposited copper coatings increase with the increase of the analyzed area. The layer’s surface on the smaller scale has a globular and irregular character. However, on images of coatings deposited on MATT1, MATT2 and BRUSHED substrate, taken from 100 µm x 100 µm, these structures are much smaller (needle-like) than observed for the coatings obtained on the ECOR substrate.
The surface roughness was evaluated based on the roughness profile deviation (Sa), and the parameters of kurtosis (Sku) and skewness (Ssk). In the column chart (Fig. 5), the average roughness values for substrates and coatings are presented. Figure 6 shows the dependence of kurtosis (Sku) and skewness (Ssk) for all tested surfaces. For both substrates, these values are close to the standard values characteristic of steel [18].
Roughness profiles of substrates’ and copper coatings’ surfaces are close to normal Gaussian distribution, corresponding to the skewness parameter (Ssk) and kurtosis parameter (Sku) equal to 0.90. For all measured surfaces with randomly located globular structures, a predominance of peaks and numerous pits/valleys were observed. Both the AFM images, the roughness characteristics based on the parameters of skewness and kurtosis, and the values of the mean roughness Sa are not mutually exclusive, moreover, they complement and confirm each other.
In Fig. 7 the X-ray diffraction patterns of copper layers electrodeposited on steel and nickel substrates were presented. Regardless of the substrate used, copper coatings have strong (111) as well as (200), (220), (311) peak intensities, which is in good agreement with results presented in the literature for coating obtained from glutamate [4] and sulphate baths [19]. No significant change in the preferred orientation with the applied substrate and finishing method was observed. Moreover, all analyzed deposits are nanocrystalline with an average crystallite size of 30 ± 6 nm.
For more detailed microstructural analysis, the thin lamellas of copper coatings deposited on the MATT1 steel and nickel substrates were observed using TEM. In Fig. 8, bright field images and corresponding selected area diffraction patterns from copper coatings as well as from steel and nickel substrates were presented. Layers electrodeposited on both of the analyzed substrates are well-adherent. It is visible that the coatings’ crystallite size is greater than that observed for substrates that were obtained from X-ray diffraction data, where crystallites are treated as the smallest, undistorted regions in the material [20]. Regardless of the substrates used, coatings’ grains/clusters of grains limited by “visible” grain boundaries using TEM have a length of 120–400 nm and a width of 30–300 nm. Additionally, the TEM observations of as-deposited Cu coatings revealed a substantial number of twins located within individual grains, which is typical for materials obtained in non-equilibrium processes, such as electrodeposition [21]. These were predominantly formed during the growth process. The appearance of additional microstructural features in the form of coherent Σ3 twin boundaries may lead to an increase of the coatings mechanical properties affecting both their yield strength as well as plasticity.
4 Conclusions
Copper coatings were electrodeposited from the non-cyanide electrolyte solution on steel (1.4024) and nickel (Ni201) substrates, commercially used for surgical instruments production, to obtain potentially antipathogenic surfaces. The influence of substrate finishing procedures by the shot peening with glass balls, electropolishing with corundum particles, and brushing on the electrodeposition process, as well as the coatings’ microstructure formation, was analysed. The cathodic current efficiency of copper electrodeposition on steel and nickel substrates was not affected by the type of surface finishing and was about 95 %. However, it significantly affects the substrate surface topography, which translates into the copper layer growth. All copper layers are metallic, have a crystalline structure, globular surface morphology and are generally characterized by good adhesion to the nickel and steel substrate, but their surface roughness is different. Substrates after matting and especially electropolishing with corundum are rough and characterized by a non-directional, randomly deformed surface morphology. After brushing on steel and nickel substrates, the formation of the less developed surface with parallel and uniform scratches was observed. It was confirmed that copper coatings imitated the substrate surface. Hence, the coating surface, which affects the nature of interaction with microorganisms, can be effectively modified and optimised by the appropriate choice of substrate finishing method without changing the electrodeposition conditions.
Data availability
The data analyzed during the current study will be available upon reasonable request.
References
Bharadishettar N, Bhat KU, Panemangalore DB. Coating technologies for copper based antimicrobial active surfaces: a perspective review. Metals (Basel). 2021. https://doi.org/10.3390/met11050711.
https://antipathcoat.wixsite.com/antipathcoat. Accessed 27 Jan 2023
Zeiger M, Solioz M, Edongué H, Arzt E, Schneider AS. Surface structure influences contact killing of bacteria by copper. Microbiologyopen. 2014. https://doi.org/10.1002/mbo3.170.
Ibrahim MAM, Bakdash RS. New non-cyanide acidic copper electroplating bath based on glutamate complexing agent. Surf Coat Technol. 2015. https://doi.org/10.1016/j.surfcoat.2015.10.024.
Kamel MM, El_moemen AA, Abd A, Rashwan SM, Bolbol AM. Electrodeposition of nanocrystalline copper deposits using lactic acid-based plating bath. Metall. 2018;6:179–83.
Wang X, Cao L-A, Yang G, Qu X-P. Study of direct Cu electrodeposition on ultra-thin Mo for copper interconnect. Microelectron Eng. 2016. https://doi.org/10.1016/j.mee.2016.07.001.
Krishnan RM, Kanagasabapathy M, Jayakrishnan S, Sriveeraraghavan S, Anantharam R, Natarajan SR. Electroplating of copper from a non-cyanide electrolyte. Plat Surf Finish. 1995;82(7):56–9.
Kublanovsky V, Litovchenko K. Mass transfer and mechanism of electrochemical reduction of copper (II) from aminoacetate electrolytes. J Electroanal Chem. 2000. https://doi.org/10.1016/S0022-0728(00)00372-7.
Ballesteros JC, Chainet E, Ozil P, Meas Y, Trejo G. Electrodeposition of copper from non-cyanide alkaline solution containing tartrate. Int J Electrochem Sci. 2011;6:2632–51.
Li Q, Hu J, Zhang J, Yang P, Huc Y, An M. Screening of electroplating additive for improving throwing power of copper pyrophosphate bath via molecular dynamics simulation. Chem Phys Lett. 2020. https://doi.org/10.1016/j.cplett.2020.
Fabbri L, Giurlani W, Mencherini G, De Luca A, Passaponti M, Piciollo E, Fontanesi C, Caneschi A, Innocenti M. Optimisation of thiourea concentration in a decorative copper plating acid bath based on methanesulfonic electrolyte. Coat. 2022. https://doi.org/10.3390/coatings12030376.
Ibrahim MAM. Copper electrodeposition from non-polluting aqueous ammonia baths. Plat Surf Finish. 2000;87(7):67–72.
Gamburg YD, Zangari G. Theory and practice of metal electrodeposition. New York: Springer; 2011.
Sanner A, Nohring WG, Thimons LA, Jacobs TDB, Pastewka L. Scale-dependent roughness parameters for topography analysis. Appl Surf Sci Adv. 2022. https://doi.org/10.1016/j.apsadv.2021.100190.
Zheng S, Bawazir M, Dhall A, Kim HE, He L, Heo J, Hwang G. Implication of surface properties bacterial motility and hydrodynamic conditions on bacterial surface sensing and their initial adhesion. Front Bioeng Biotechnol. 2021. https://doi.org/10.3389/fbioe.2021.643722.
Jacobs TDB, Junge T, Pastewka L. Quantitative characterization of surface topography using spectral analysis. Surf Topogr Metrol Prop. 2017. https://doi.org/10.1088/2051-672X/aa51f8.
Watanabe T. Nano-plating microstructure control theory of plated film and data base of plated film microstructure. 1st ed. The Netherlands: Elsevier Ltd; 2004.
Mwema FM, Akinlabi ET, Oladijo OP. Effect of substrate type on the fractal characteristics of AFM images of sputtered aluminium thin films. Mater Sci. 2020. https://doi.org/10.5755/j01.ms.26.1.22769.
Defforge T, Coudron L, Ménard O, Grimal V, Gautier G, Tran-Van F. Copper electrodeposition into macroporous silicon arrays for through silicon via applications. Microelectron Eng. 2013. https://doi.org/10.1016/j.mee.2013.01.014.
Zhong Y, Ping D, Song X, Yin F. Determination of grain size by XRD profile analysis and TEM counting in nano-structured Cu. J Alloys Compd. 2009. https://doi.org/10.1016/j.jallcom.2008.08.075.
Kurapova O, Grashchenko AS, Archakov I, Golubevd SN, Konakov VG. The microstructure and mechanical properties of twinned copper-bismuth films obtained by DC electrodeposition. J Alloys Compd. 2021. https://doi.org/10.1016/j.jallcom.2020.158007.
Funding
This work was supported by the National Centre for Research and Development in the frame of the M-ERA.NET program under Grant MERA.NET2/2020/AntiPathCoat/4/2021.
Author information
Authors and Affiliations
Corresponding author
Ethics declarations
Conflict of interest
The authors have no competing interests to declare relevant to this article's content.
Ethical approval
This manuscript presents original work that has not been published previously and is not under consideration for publication elsewhere. No studies on human or animal subjects were conducted.
Additional information
Publisher's Note
Springer Nature remains neutral with regard to jurisdictional claims in published maps and institutional affiliations.
Rights and permissions
Open Access This article is licensed under a Creative Commons Attribution 4.0 International License, which permits use, sharing, adaptation, distribution and reproduction in any medium or format, as long as you give appropriate credit to the original author(s) and the source, provide a link to the Creative Commons licence, and indicate if changes were made. The images or other third party material in this article are included in the article's Creative Commons licence, unless indicated otherwise in a credit line to the material. If material is not included in the article's Creative Commons licence and your intended use is not permitted by statutory regulation or exceeds the permitted use, you will need to obtain permission directly from the copyright holder. To view a copy of this licence, visit http://creativecommons.org/licenses/by/4.0/.
About this article
Cite this article
Bigos, A., Bugajska, M., Kwiecien, I. et al. Antipathogenic copper coatings: electrodeposition process and microstructure analysis. Archiv.Civ.Mech.Eng 23, 233 (2023). https://doi.org/10.1007/s43452-023-00772-x
Received:
Revised:
Accepted:
Published:
DOI: https://doi.org/10.1007/s43452-023-00772-x