Abstract
It is well known that the mechanical properties of spheroidal graphite cast iron deeply depend on the volume of pearlite matrix microstructures. Therefore, the theoretical criterion of pearlite matrix nucleation is considered important in this graphite cast iron that to obtain the higher mechanical properties of graphite cast iron, the pearlite stabilizing element such as Mn or Cu is very important. The present work aims to study the influence of manganese (Mn) content and heat treatment on the mechanical properties of 3% or 4% (Solution Strengthened Ferritic Ductile Iron-SSFDI) of silicon (Si) containing spheroidal graphite cast irons. The six 3.6%C–3%Si melts with different chemical compositions from 0.2 to 1.7 mass% of Mn content were produced using a high-frequency induction furnace. The melt was poured into a Y-block CO2 sand mold of 25 or 40 mm in thickness. The microstructure analysis and mechanical testing were performed for as-cast and some heat treatment conditions, such as annealing or air cooling. As a result, the tensile strength had a good relationship with the area fraction of pearlite, over 600 MPa in UTS, and high proof stress for some 3 or 4%Si–Mn series samples in the as-cast condition. By the heat treatment from the unique (α + γ) region, the 3% Si sample showed over 800 MPa and over 10% in elongation. And 4%Si–1.5%Mn (SSFDI) series sample showed over 600 MPa in UTS and over 15% in elongation which was prepared by annealing heat treatment to reduce to less than 5% of the area fraction of pearlite. This study suggests that it can be understood of the correlation between optimizing the heat treatment condition and mechanical properties of SSFDI cast irons.
Similar content being viewed by others
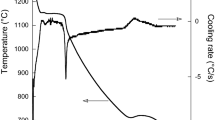
Avoid common mistakes on your manuscript.
Introduction
Spheroidal graphite cast iron is used for many structural materials, high-load applied heavy-duty parts and complex forms for automotive applications combining good machinability and lower cost.1
To obtain the high strength and high toughness performance of spheroidal graphite cast iron, many researchers have tried to improve and study the high tensile and large elongation characteristics by the addition of elements, heat treatment and processing method.
The mechanical properties of spheroidal graphite cast irons mainly depend on the matrix microstructures, to obtain high tensile strength, then the pearlitic matrix microstructure is preferred and to obtain high elongation, the ferritic matrix is preferred.2
Alloying elements such as manganese (Mn) are also well known; the pearlite promotes and stabilizes the matrix microstructure of spheroidal graphite. In addition, nickel (Ni), manganese (Mn), and copper (Cu) are also used in similar effects for ductile cast irons. To do this, the influence of the addition of these combined alloying elements and heat treatment has also been investigated.3,4
Silicon is well known as it promotes the ferritic/graphitization element for spheroidal graphite cast iron.
Recently, reports and studies of the silicon (Si) solid solution type spheroidal graphite cast iron5,6 have been activated by many researchers. Not only in European countries1,7,8,9 but also in Japan,10,11 this attractive material as the solid solution Si spheroidal graphite cast irons (SSFDI) material, is attractive due to the higher strength (UTS and 0.2% proof stress) and higher elongation compared to the conventional spheroidal graphite cast irons.
The silicon solid solutions act to obtain the higher proof stress (0.2% stress), which means they improve the yield ratio (i.e.: 0.2% stress/UTS) and have a clear advantage over the machine design such as weight saving and low cost.
However, it has been reported that the addition of Si content appears to affect the brittleness behavior over 4.5%Si contents, and there is some tradeoff between the strength/hardness and elongation in many situations.5,6,7,8,9,10,11
In addition, it is also remarked that the impact characteristics on high temperature and higher transition temperature of SSFDI materials are definite areas of concern, and which desired improvement to the beneficial characteristics.
Furthermore, to obtain the higher elongation, Ikawa et al.12 have reported very unique heat treatment, which condition was heated up to (α + γ) region to obtain complexed duplex microstructure of spheroidal graphite cast iron. In addition, Gundlach13 has already reported the development of high-strength ferritic cast iron by using several heat treatment conditions. We are also very interested in that to adapt this heat treatment on high-Si contain spheroidal graphite cast iron.
Due to that, clarifying the co-relationship between the Si content and heat treatment of manganese alloyed spheroidal graphite cast irons is valuable from the viewpoint of mechanical design and expands the application in the future.
Therefore, this work aims to study the influence of not only the content of Mn, but also Si, and heat treatment on the mechanical properties of 3 to 4% of silicon-containing spheroidal graphite cast irons.
Experimental Details
A 20 kg charge of high-purity pig iron (3.2%C, 0.24%Si) and low carbon steel was melted in a high-frequency induction furnace. The Si contents were adjusted by adding Fe–75%Si alloy at 1450 °C to obtain the desired 3%Si and 4%Si contents as shown in Figure 1. After melting, it was heated up to 1500 °C, and the chemical composition was adjusted to 0.2, 0.6, 0.8, 1.2, 1.5, and 1.7%Mn, for each 3%Si and 4%Si series were by the addition of Fe–75%Mn alloy. The melt was spheriodizing treated by the addition of Fe–45%Si–5.5%Mg alloy, and subsequently, after inoculation with Fe–50%Si alloy, the melt was poured into the 25-mm Y-block (for the tensile test) i.e., Figure 2a, 40-mm Y-block (for heat treatment) i.e., Figure 2b, and 30-mm-conventional CE thermal analysis mold. The heat-treating samples were cut off from the bottom portion of the Y-block, details as shown in Figure 2.
For the as-cast condition, the specimen for the microstructural analysis was taken from the bottom of each Y-block. For the heat treatment samples, the machined tensile specimens were employed, and we have polished and observed the cross-section on the chuck part of the tensile specimen.
The microstructures of these specimens were observed with a magnification of x100. The graphite and microstructures, such as nodularity percent of graphite, mean diameter of graphite, count of graphite nodules, the area fraction of graphite, and the area fraction of ferrite and pearlite matrix microstructures, were analyzed by using the image analysis software.
The hardness of specimens was measured with Brinell hardness (indent dia.; 10 mm, load; 29.4 kN, holding time; 30 s), and the matrix hardness (HV 0.5) was measured by micro Vickers hardness tester with values averaged from five measurements. Tensile testing was performed with tensile test pieces of 8 mm in diameter and 40 mm in gauge length (i.e., diameter to gauge length ratio is 1:5.) as shown in Figure 3 and using Instron #5582 (floor type; 100 kN) with 1 mm/min in crosshead speed at room temperature. Ultimate tensile strength (UTS) and elongation were determined from the results of stress–strain curves, and the 0.2% proof stress was estimated by the offset method of the curves. The fracture surfaces of tensile specimens were observed by field-emission scanning electron microscopy (SEM) (Hitachi FE-SEM: S-4800, S-800).
Results and Discussion
The chemical compositions of as-cast samples are listed in Table 1. The amount of additive Mn changes from 0.2 to 1.7%, Si changes from 3 to 4%, and the 3%Si series samples recognize rare earth (RE) elements subtly affected by the graphite nodularization agent. Other chemical elements present quite small deviations of composition for all samples and recognize nominal composition ranges of spheroidal graphite cast iron compared to other articles.8,9,10
As-cast Condition
Figure 4 shows the microstructures of as-cast samples from the Y-block series. As seen in metallographic observation, the microstructure of each sample is affected by additive elements of Mn and/or Si. Thus, the higher Mn content samples have the higher pearlitic matrix microstructures, and the higher Si content samples have the higher ferritic matrix microstructures. The size of graphite obtains a similar tendency by the addition of Si content which trend is similar results reported.8,10
The results of the microstructural analysis organized, the relationship between the area fraction of pearlite and Mn content is shown in Figure 5. On the other hand, microstructures of the higher than 3%Si–1.7%Mn sample from the thermal analysis molds crystalized the cementite structure due to the Mn addition and large cooling rate compared to the Y-blocks one.
Figure 6 shows the relation between the results of the tensile test and the area fraction of pearlite as the function of Si content. The trend of tensile properties varies the area fraction of pearlite; the higher pearlite fraction samples show coexistence of the higher tensile strength and lower elongation. The dashed line inset of Figure 6 was the tensile strength calculated from the role of the mixture by using 400 MPa as ferrite and 900 MPa as pearlite matrix microstructure. It seemed that the actual strength was saturated in the higher tensile region. Especially in the case of the 4%Si series sample shows less than 5% in elongation over 5% of the pearlite area fraction, even if the tensile strength shows over 600 MPa and graphite nodularity is not affected by the addition of Mn and Si. These values of tensile characteristics are similar levels compared to the reports.10,11,13,14,15,16,17
The higher Si content sample shows a higher 0.2% proof strength due to the solid solution effect in the ferrite matrix acting to the resistance to slip on the dislocation of the ferrite structure as shown in Figure 7. The high-Si content samples possess a higher 0.2% proof strength and this beneficial property suggests the expands the design and usage/applications for high Si-cast irons from the other same mentioned.13,14,17,18,19,20,21
Heat Treatment for the 3%Si Series Sample
These results of the previous section suggest that the higher Si content samples tend to brittleness fracture in tensile properties, and to obtain the coexistence of tensile strength and elongation, the 3%Si series sample has more potential compared to the 4%Si series sample. Subsequently, the 3% Si series samples were heat treated by air cooling from α + γ co-dual phase range to obtain higher strength with remaining ductility, the 4% Si series samples were heat treated by annealing to obtain higher ductility to decompose the pearlite structure as reported by Ikawa12 and Gundlach.13
From this literature, the phase diagrams have already been reported. We thought that by using these complex (α+γ+G) regions, the mechanical properties could be improved. For example, if the sample has air cooling from the over-eutectoid point then the pearlite structure will be obtained, the tensile strength increase, and ductility will be decreased. If the sample has furnace cooling from the over eutectoid point then the ferrite structure will be obtained, the tensile strength decrease, and ductility will be increased. So, it can change two parameters to optimize the heat treatment condition such as heating temperature and cooling rates.21,22
To adjust the cooling rate for the semi-air cooling, we carried out the Isowool® (Isolite insulating products Co., Ltd. JAPAN) ceramic fiber blanket (77%SiO2 +20%(CaO+MgO)), and samples were wrapped by the blanket into the electric furnace.
The conditions are listed below:
-
(1)
Furnace cooling: Full annealing
-
(2)
Semi-furnace cooling: The tops opened when full annealing
-
(3)
Semi-air cooling: Natural air cooling from a wrapped double ceramic fiber blanket
-
(4)
Air cooling: Forced fan-cooling
Figure 8a shows the results of the influence of cooling rate on microstructure for various cooling rates. The heating condition was heated up to 830 °C and lasted 2 h. By the furnace cooling, the pearlite structure was de-composite to ferrite and carbon. By the air cooling, the fine pearlite and ferrite-mixed microstructure was obtained. From these results, it has chosen the air-cooling condition.
Figure 8b shows the results of the influence of heating temperature on microstructures for air cooling specimens. By these results, it can be chosen two temperatures (i.e., 830 and 850 °C) for the heated-up temperature.
Figure 9 shows the relationship between tensile properties and area fraction of pearlite for the 3% Si series for the existence of the heat treatment. The tensile properties are well explainable by the called 'trade-off' relationship between tensile strength and elongation. However, the higher tensile and lower elongation regions for the as-cast sample did not correspond to the linear relation between tensile strength and pearlite area fraction. This mismatch has suggested the effect of pearlite lamellar spacing by metallographic analysis. Either way, to obtain higher strength-elongation properties for fully pearlitic samples such as higher Mn content samples, adapting the heat treatment of air cooling from α + γ co-dual phase range is well effective.
Heat Treatment for the 4% Si Series Sample
Figure 10 shows the microstructures of as-cast condition and heat-treated samples for 4% Si various Mn content. In the case of the as-cast condition, the pearlite matrix microstructure increased with increasing Mn content. Although the annealing heat-treated sample shows, the matrix microstructure shows almost fully ferrite excepted over 1.5%Mn.
Figure 11 shows the relationship between the area fraction of pearlite and Mn content for the annealing sample. Compared to the as-cast condition, the area fraction of pearlite for the annealing samples toward less than 10% of pearlite area fraction even if the highest Mn content.
The summarized results of tensile properties are shown in Figure 12. Since adopting the annealing heat treatment for the high 4% Si series sample, the matrix microstructure obtained almost fully ferrite matrix microstructure except over 1.5% Mn series samples. Therefore, the tensile strength rather than elongation has dramatically improved. As-cast condition, the over 0.8% Mn series samples show tiny ductility, but the annealing sample shows over 15% in elongation. The annealing heat treatment can improve not only higher elongation but also promise higher toughness for the higher Si series samples combined with over 600 MPa-class in tensile strength.
SEM Fractography for the 4% Si Series Sample
Figure 13 shows the SEM observation photos of tensile specimens compared to as-cast and annealing samples for 4% Si series samples.
In the as-cast condition, the lower Mn content series sample shows an almost fully ductile fracture as shown in dimple forms of the nuclei of spheroidal graphite. However, the higher Mn content sample shows the brittle fracture as shown in the cleavage fracture of the ferrite matrix and the extremely small visible graphite area fraction on the fracture surface.
On the other hand, the annealed 4%Si–1.2%Mn series sample shows similar ductile fracture surfaces compared to the 4%Si–0.2%Mn as-cast sample. It can be well understood that not only tensile strength and elongation were dramatically changed by annealing but also fracture surfaces. In contrast, the annealed 4%Si–1.5%Mn samples could not completely improve the brittle fracture tendency while maintaining the higher tensile strength. These similar featured surfaces are also mentioned by the other articles.10,11,14,15,18,23,24
Therefore, these results suggest that it significantly keeps remaining less than 5% of the area fraction of the pearlite to improve elongation. Also, it supposes that ISO/EN regulation5,6 has mentioned that there should be a pearlite area fraction less than 5% in 4% Si (SSFDI) materials due to the same reason.
Conclusion
The microstructures of the 3%Si series samples are increasing of area fraction of pearlite with increasing the Mn content due to be apt to promote the pearlite structure, this resulted in the tensile strength getting a higher value and the elongation shifting lower value. However, this effect has been saturated over 700 MPa in tensile strength because of the expansion of the spacing of pearlite lamellar with increasing Mn content. The treating a normalizing heat treatment for the 3%Si series samples from the α + γ-dual phase range, the tensile strength improved without sacrificing an elongation.
The tensile properties of the 4%Si series samples show the superior within 10% of the area fraction of pearlite; the otherwise samples show a brittleness tendency in tensile properties. The treating the annealing heat treatment for the 4%Si series samples, the elongation can be improved significantly with over 600 MPa in tensile strength even if over 1.5%Mn content condition.
References
M.A. Pegoraro, C. Tenailleau, A. Ebel et al., Mater. Today Commun. 25, 101422 (2020). https://doi.org/10.1016/j.mtcomm.2020.101422
R.A. Gonzaga, Mater. Sci. Eng. A 567, 1–8 (2013). https://doi.org/10.1016/j.msea.2012.12.089
T. Nobuki, M. Hatate, T. Shiota, Int. J. Cast Met. Res. 21, 31–38 (2008). https://doi.org/10.1179/136404608X361620
T. Nobuki, M. Hatate, T. Karasudani, Y. Okuzumi, Foundry Trade J. 190(3740), 294–298 (2016)
International Standard ISO 1083: 2018(E), Spheroidal Graphite Cast Iron-Classification
European Standard EN 1563: 2018(E), Founding-Spheroidal Graphite Cast Irons, ICS 77.080.10
P. Weiß, A. Tekavčič, A.B. Polaczek, Mater. Sci. Eng. A 713, 67 (2018). https://doi.org/10.1016/j.msea.2017.12.012
C. Hartung, R. Logan, A. Plowman et al., Int. Metalcast. 14, 1195–1209 (2020). https://doi.org/10.1007/s40962-020-00469-4
C. Gebhardt, J. Nellessen, A. Bührig-Polaczek, C. Broeckmann, Metals 11, 311 (2021). https://doi.org/10.3390/met11020311
T. Kanno, Int. Metalcast. 13, 491–499 (2019). https://doi.org/10.1007/s40962-018-0283-7
T. Ikeda, T. Umetani, N. Kai, K. Ogi, N.-A. Noda, Y. Sano, Mater. Trans. 57, 2132–2138 (2016). https://doi.org/10.2320/matertrans.F-M2016832
Y. Tanaka, K. Ikawa, IMONO 47, 847–853 (1977). https://doi.org/10.11279/imono.47.12_847
R.B. Gundlach, Int. Metalcast. 14, 1065–1077 (2020). https://doi.org/10.1007/s40962-020-00489-0
R. González-Martínez, U. de la Torre, A. Ebel, J. Lacaze, J. Sertucha, Mater. Sci. Eng. A 712, 803–811 (2018). https://doi.org/10.1016/j.msea.2017.11.051
D. Franzen, P. Weiß, B. Pustal et al., Int. Metalcast. 14, 1105–1114 (2020). https://doi.org/10.1007/s40962-020-00412-7
K.A. Kasvayee, E. Ghassemali, I.L. Svensson, J. Olofsson, A.E.W. Jarfors, Mater. Sci. Eng. A 708, 159–170 (2017). https://doi.org/10.1016/j.msea.2017.09.115
D.-E. Anca, I. Stan, I. Riposan, S. Stan, Materials 15(8), 2712 (2022). https://doi.org/10.3390/ma15082712
A. Alhussein, M. Risbet, A. Bastien, J.P. Chobaut, D. Balloy, J. Favergeon, Mater. Sci. Eng. A 605, 222–228 (2014). https://doi.org/10.1016/j.msea.2014.03.057
D. Franzen, P. Weiß, B. Pustal, A. Bührig-Polaczek, Mater. Sci. Technol. 35, 687–694 (2019). https://doi.org/10.1080/02670836.2019.1582193
W. Stets, H. Löblich, G. Gassner et al., Int. Metalcast. 8, 35–40 (2014). https://doi.org/10.1007/BF03355580
P. Hammersberg, K. Hamberg, H. Borgström, J. Lindkvist, L.-E. Björkegren, Mater. Sci. Forum 925, 280–287 (2018). https://doi.org/10.4028/www.scientific.net/MSF.925.280
T. Umetani, H. Takada, T. Ikeda, T. Yamaguchi, H. Era, K. Nishio, Weld. Int. 29, 342–348 (2015). https://doi.org/10.1080/09507116.2014.921063
A. Ozel, Bayburt Üniv Fen Bilim Derg. 3(1), 41–45 (2020)
Z. Glavaš, A. Štrkalj, A. Stojaković, Metalurgija 55(3), 293–296 (2016)
Author information
Authors and Affiliations
Contributions
Tohru NOBUKI, Takanori AOKI, and Minoru HATATE have synthesized materials and measuring, estimation, and discussions about experimental data. Some sample preparations for the sample observation for OM/SEM, heat treatments, mechanical testing, and organized data were made by Takanori AOKI. Determination of structural analysis and mechanical properties and discussions were made with the supervisor as Minoru HATATE. All authors have contributed to the discussions for the manuscript and have approved the final version.
Corresponding author
Additional information
Publisher's Note
Springer Nature remains neutral with regard to jurisdictional claims in published maps and institutional affiliations.
This paper is an invited submission to IJMC selected from presentations at the 16th Asian Foundry Congress (AFC2023), held December 1 to 4, 2023, in Muroran, Japan, and has been expanded from the original presentation. This research paper was published originally in JFS (Journal of Japan Foundry Engineering Society) 94(10):2022. p 606-613. https://doi.org/10.11279/jfes.94.606.
Rights and permissions
Open Access This article is licensed under a Creative Commons Attribution 4.0 International License, which permits use, sharing, adaptation, distribution and reproduction in any medium or format, as long as you give appropriate credit to the original author(s) and the source, provide a link to the Creative Commons licence, and indicate if changes were made. The images or other third party material in this article are included in the article's Creative Commons licence, unless indicated otherwise in a credit line to the material. If material is not included in the article's Creative Commons licence and your intended use is not permitted by statutory regulation or exceeds the permitted use, you will need to obtain permission directly from the copyright holder. To view a copy of this licence, visit http://creativecommons.org/licenses/by/4.0/.
About this article
Cite this article
Nobuki, T., Aoki, T. & Hatate, M. Effects of Manganese and Heat Treatment on Mechanical Properties in Spheroidal Graphite Cast Iron. Inter Metalcast (2024). https://doi.org/10.1007/s40962-024-01389-3
Received:
Accepted:
Published:
DOI: https://doi.org/10.1007/s40962-024-01389-3