Abstract
With the rapid development across major cities, low-capacity screw piles are adopted by builders as a viable economical option in managing risk involving settlement in soft soil deposits. Although the required installation torque and the capacity of a screw pile can be correlated to the soil shearing resistance at the interface of its shaft and helical plates, the correlated ultimate capacity of the pile is specific only to undrained conditions. Therefore, if the water table fluctuates within the embedment length of the pile, the correlated ultimate strength is not valid. This poses a serious design concern in over-consolidated fills. Therefore, due to the uncertainty associated with the compressive capacity of installed screw piles in soft saturated deposits, it is advantageous to perform a static load test to verify the serviceability and ultimate loads. In this study, four static load tests were carried out on screw piles at four different construction sites in the city of Melbourne, to study the load transfer mechanism at various levels of axial loading and subsequent unloading/reloading stages. In one of the sites, the screw pile was equipped with miniature transducers to monitor the generated total stress and pore-water pressure during the installation and post-installation. The results of this study indicated that a static load test can accurately estimate the real bearing capacity of a screw pile which differs significantly from the design geotechnical strength calculated using theoretical equations. It was concluded that in the absence of a pile load test, it is rational to adopt a geotechnical reduction factor of 0.4 and neglect the skin friction capacity of the screw pile to provide a safe foundation design.
Similar content being viewed by others
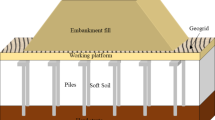
Avoid common mistakes on your manuscript.
Introduction
Screw piles are alternative and economical deep foundation systems to conventional bored piles. Screw piles are rapidly gaining growing recognition in many residential construction projects in metropolitan cities worldwide, including in Australia. The application of screw piles has been extended from residential and commercial buildings to rail, telecommunications and roads where a quick installation is required or where building work takes place adjacent to existing structures [1].
Screw piles are normally made of high tensile carbon steel with circular hollow sections (CHS) shaft equipped with one or more helices welded to the shaft that provide a self-tapping mechanism during the penetration. The hollow shaft may be filled with structural grout and is structurally engaged to the concrete slab or bearer via pile top-slab connection, which might be dowel bars, slab plates or bearer brackets. The circular hollow shaft section diameter and helix outer diameter range between 76–273 and 250–1200 mm, respectively. Table 1 shows the commonly used screw piles in Australia.
In construction sites where cut and fill methods are practised, with imported fills overlying high-bearing capacity in situ layers or where the shallow in situ layers are of low bearing capacity, screw piles can extend the load transfer mechanism from the top low-bearing capacity layer to the lower stronger layers to distribute the stress and minimise the corresponding strain. Therefore, the soil settlement is minimised and post-construction movements in buildings are mitigated. The main benefits of screw pile foundations include shorter turnaround time, ease of installation, ease of access and removal when other foundation types are no longer required. Screw piles are suitable for both tensile and compressive loads, so they have also been used for masts, signs and transmission towers [2, 3]. The installation of screw piles mimics screwing a self-tapping screw using rotary hydraulics, called the planetary drive, attached to the earthmoving equipment [4].
For installing a screw pile, a controlled torque is applied to the screw pile to achieve a sufficient screw pile axial capacity prior to refusal. During the installation, any changes in the sub-layer strata are indicated by observing changes in excavator hydraulic pressure thereby providing important quality control on the torsion capacity and load capacity of the pile [5]. The excavator hydraulic pressure readings and the applied planetary drive torque \((T)\) are usually cross-correlated to the ultimate capacity of the pile (\({Q}_{u}\)) using a simple equation (Eq. 1) to drive in the screw pile until achieving design capacity. This cross-correlation method even though has inherent flaws, is used widely as an accepted criterion to confirm whether screw piles are installed according to their geotechnical design criteria [6].
\({ }Q_{{\text{u}}} :u{\text{ltimate pile capacity}}\), \(K_{{\text{t}}} :{\text{an emprical value dependent on the pile shaft size}}\), \(T:p{\text{lanetary drive torque}}\).
\(K_{{\text{t}}}\) is a function of soil properties, size of the helix, helix configuration, and pile shaft size. The planetary drive torque measured, T, during the pile installation is a function of both measurable and unmeasurable parameters. Measurable parameters are pile dimensions and configuration, and soil strength-related parameters, whereas unmeasurable parameters are installation procedure, method of torque measurements, the accuracy of measurements and operator experience [5]. The unmeasurable parameters are difficult to quantify and usually do not affect the torsional resistance of the pile section, but they can adversely affect the measurement of torque values [5].
The applied torque to penetrate the pile into the ground during the installation should be monitored in real time to not exceed the torsional capacity of the pile section. If the screw pile is to penetrate stiff layers to reach its founding depth, the required torque capacity should be proportionally higher than the installation torque to avoid twisting or breaking the shaft along the welded stem. Once a screw pile is advanced into the ground, the adjacent soil around the pile shaft is remoulded and displaced away by helical plates. This installation process disturbs the soil stress state equilibrium near the pile and may cause a reduction in the soil shear strength in the vicinity of the pile tip due to the generation of excess pore-water pressure in saturated fine-grained soils [7]. Australian Piling-Design and Installation Standard [8] recommends a geotechnical strength reduction factor (φg) for calculating design geotechnical strength. The geotechnical strength reduction factor is a function of testing type and its value increases with the number of performed static load tests according to the following equation:
φg = φgb + (φtf − φgb)K, φgb = basic geotechnical strength reduction factor, φtf = intrinsic test factor, Rd,g: design geotechnical strength, Rd,ug: design ultimate geotechnical strength, K: testing benefit factor, K = 1.33p/(P + 3.3) ≤ 1, for static or rapid load testing, K = 1.13p/(P + 3.3) ≤ 1, for dynamic load testing, P = percentage of the total piles that are tested and meet the specified acceptance criteria.
There are different test methods including static load testing, rapid load testing, bi-directional load testing and dynamic load testing that can be used to determine the design geotechnical strength of piles of different sizes. The number of static load tests on screw piles required at a site depends on several factors and should be determined based on engineering judgement, project-specific considerations, geotechnical conditions, desired level of design confidence, pile variability and the importance level of the project. For critical or high-risk projects, more load tests might be advisable to ensure a higher level of confidence. If the site’s subsurface profile includes stiff to very stiff layers at shallow depths, the number of tests can be reduced. However, in soft deposits, to enhance the design confidence a larger number of tests is required. AS 2159 [8] correlates the geotechnical reduction factor to the number of tests in a site as indicated in Eq. 2. The larger number of tests provides confidence to use a higher geotechnical reduction factor which results in a higher design geotechnical strength.
Research on the load–displacement behaviour of screw piles is mostly limited to the laboratory-scale physical models, and to the best of the authors’ knowledge, there is no comprehensive field study of a full-scale screw pile in low to medium-bearing clay layers with the assistance of miniature instrumentations to investigate the pile tip and pile head loads and the excess pore-water pressure at the vicinity of the pile tip during the loading and unloading scenarios. This research study explains the design of screw piles based on the Australian Piling-Design and Installation Standard [8] and monitoring its (1) load at the pile head and tip, (2) displacement at the pile head, and (3) the pore-water pressure at the pile tip, which would assist in developing a better understanding of screw pile design and testing for geotechnical designers and practitioners. In this research, instead of relying on the torque-capacity correlation method of screw pile, authors have embarked on using geotechnical strength calculations and validated it against field static load test in determining the ultimate capacity of the screw pile.
Design Method
The design procedure of screw piles is based on two major failure modes [9] including (i) the cylindrical shear failure model; and (ii) the individual plate bearing model. The appreciation of each model to calculate the ultimate bearing capacity of the pile is based on the ratio of spacing (S) and average diameter (D) of helix and the soil type.
Cylindrical Shear Failure Model
The cylindrical shear failure model is valid when a multi-helix screw pile with an inter-helix spacing ratio (S/D) of less than 3 penetrates the ground [11]. The overall ultimate compressive capacity of the screw pile includes the sum of the end bearing resistance of the bottom helix, the shear resistance along a soil cylinder from the lower helix to the top helix and the shaft skin friction above the top helix [12]. In tension mode loading, the bearing resistance of a screw pile is the sum of the bearing resistance of the top helix, the shear resistance along a soil cylinder from the lower helix to the top helix and the shaft skin friction above the top helix. The ultimate bearing resistance of multi-helix screw piles (tension/compression) is governed by Eq. 3 [13] in cohesive soils and by Eq. 4 [14] in cohesionless soils. The authors have combined Eqs. 3 and 4 and concluded Eq. 5 as the general form of bearing resistance of screw piles in compression/tension mode for both short-term and long-term conditions (i.e. undrained, and drained conditions, respectively).
In the above equations \({Q}_{{\text{u}}}^{{\text{c}}/{\text{t}}}\) is the ultimate bearing resistance of the pile in compression or tension (uplift). \({S}_{{\text{f}}}\) is spacing ratio factor (Eq. 6), and D and d are the average helix diameter and shaft diameter, respectively. \({L}_{{\text{c}}}\) is the distance between the uppermost and lowermost helices. \(\alpha , {c}_{{\text{u}}}\) and \(\varphi\) are the adhesion factor, soil undrained cohesion and internal friction angle of the soil, respectively. \({A}_{{\text{H}}}\) is the cross-sectional area of the helix (i.e. \({A}_{{\text{H}}}=\frac{\pi }{4}({D}^{2}-{d}^{2})\)). When compression open-ended piles penetrated in cohesive soils, a soil plug may form at the pile tip and, therefore, the area of the helix can be increased to \({A}_{{\text{H}}}=\frac{\uppi }{4}{D}^{2}\). \({N}_{{\text{c}}/{\text{u}}}\) and \({N}_{{\text{q}}}\) are the compressive/uplift bearing capacity factors for cohesive soils and cohesionless soils, respectively. \({\gamma }^{\mathrm{^{\prime}}}\)H and d are the effective stress at the top helix and the shaft diameter, respectively. \({H}_{{\text{eff}}}\) is the effective length of the pile above the top helix that is equal to the depth of the top helix reduced by the diameter of the helix (H–D). \(H_{{\text{b}}}\) and \(H_{{\text{t}}}\) are the depth of bottom and top helices from the ground level. \(K_{{\text{s/u}}}\) is the coefficient of lateral effective stress in compression/uplift. \({\Sigma }_{z}^{\prime}\) is the effective stress at the middle depth of the top and bottom helices from the ground level (\(\sigma_{z}^{\prime} = \gamma^{\prime}Z_{{\text{m}}}\)). The shaft skin resistance is found to be negligible for H/D < 3 in cohesive soils [15] and for H/D < 5 in cohesionless soils [16].
\(S_{{\text{f}}}\) is determined from Eq. 6 [17] as a function of spacing ratio (H/D). \(N_{{\text{c}}}\), \(N_{{\text{u}}}\) and \(N_{{\text{q}}}\) are calculated from Eq. 7 [18], Eq. 8 [19] and Eq. 9 [20], respectively. The adhesion factor is 1 for \(c_{{\text{u}}} \le\) 25 kPa, 0.5 for \(c_{{\text{u}}} \ge 75\) kPa and it linearly changes for other values.
Individual Plate Failure Model
The individual plate bearing failure model is applicable for all single and multi-helix screw piles with the inter-helix spacing ratio \(\frac{S}{D} \ge 3\). In this method, it is assumed that each helix has an independent bearing capacity and the overall ultimate capacity of the screw pile is the sum of the individual capacity of each helix and the skin friction capacity along the section of the pile shaft above the uppermost helix to the ground level [12] (Eq. 10). This method is exercised for helical piles both in compression and tension modes.
In sizing a screw pile based on AS2159 [8], the first step is to choose a proper shaft which provides enough torsion and axial load capacity to satisfy the installation torque and the vertical load at the required depth. The torsion capacity of hollow sections can be calculated from Eq. 11 [21].
According to AS2159 [8], the ultimate design geotechnical strength (\({R}_{{\text{d}},{\text{ug}}}\)) of a screw pile reduced by the geotechnical strength reduction factor (\({\varphi }_{{\text{g}}}\)) must be greater than the design action effect (\({E}_{{\text{d}}}\)) as an assorted combination of dead, live and wind load.
Installation Effects
As the screw pile advances to the targeted subsurface saturated fine-grained soil layer, excess pore-water pressure is generated near the pile tip and alters stress state in soil. The generated excess pore-water pressure is positive in normally to lightly over-consolidated soils and might be negative in heavily over-consolidated soils. The dissipation rate of the generated excess pore-water pressure is a function of soil type and grain size. The bearing resistance of screw piles is also a function of time, approaching the long-term drained condition after pile installation. The post-peak resistance of the pile is dependent on the soil type and the degree of soil over-consolidation. The drained post-peak resistance of the pile might be greater (i.e. in normally consolidated soils) or lower (i.e. in over-consolidated soils) than the resistance during the installation [22].
Weech [7] measured the installation-induced excess pore-water pressure in a soft sensitive clay at various distances away from the pile shaft. The ultimate capacity of the loaded pile was measured in intervals of 19 h, 7 days and 6 weeks following the installation. It was found that most of the generated excess pore-water pressure was due to the increase in total stress caused by the penetration of the pile shaft during the installation. Once the installation is completed, the excess pore-water pressure gradually dissipates due to the soil consolidation that results in the increase in the soil shear strength and hence the bearing resistance of the pile. This process is called soil setup and the rate of soil setup is directly related to the rate of consolidation near the pile end [23]. Seed and Reese [24] reported the load test results of a pile driven into soft clay, which showed a sixfold increase in bearing capacity over 30 days. Karkush and Hussein [25], based on a series of static load tests on a model screw pile with length/helix diameter ratios of 20, 13.3 and 10 in a soft saturated soil tank, concluded that the excess pore-water pressure generated during the loading stage approaches its maximum value at a displacement/helix diameter ratio of 3%, followed by a continuous reduction of pore-water pressure towards the end of the test at 20% helix diameter penetration.
Static Load Test Setup
The traditional torque correlation method used in the field during the installation to estimate and validate the ultimate bearing resistance of screw piles is relatively unreliable, as the correlation parameter is dependent on the pile size, type and condition of the soil, and the depth of the water table [10]. Therefore, due to the uncertainty associated with the compressive capacity of installed screw piles in soft saturated deposits, it is advantageous to perform a static load test to verify the serviceability and ultimate loads in loading/unloading cycles. AS 2159 [8] requires pile load testing for piles when the basic geotechnical reduction factor (φgb) is greater than 0.4 and the average risk factor rating (ARR) is greater than 2.5. The setup of the static load test rig includes a reaction beam, two reaction screw piles, a test screw pile and equipment to apply and measure load and pile displacement. Figure 1 shows the pile test rig used in this study. Figure 2 shows the schematic of the test setup. The test screw pile was installed to the required depth with a portion of the pile remaining above the ground. Two reaction piles were installed adjacent to the test pile to support the reaction beam which provides uplift resistance when the compression force is applied on the test pile. An integrated load cell-hydraulic jack system was mounted on top of the test pile below the reaction beam. A linear variable displacement transducer (LVDT) was mounted to the test pile to measure its pile head displacement. Two LVDTs were mounted on each reaction pile to correct the test screw pile displacement measurements. A rugged waterproof multi-channel 16-bit universal data logger was used to log the data during the long-term tests in the field. The loading test was initiated with the application of incremental loading using the hydraulic jack. The static load test in this study was carried out based on the procedure mentioned in Sect. 8.4.2.2 and Table A1 of AS2159 [8].
The load–deformation relationship after a pile static load test is analysed to define the ultimate bearing resistance of the pile. Elkasabgy and El Naggar [26] defined the ultimate bearing resistance as the load corresponding to a movement equivalent to the sum of the elastic deformation of the pile under applied load and 3.5% of the largest helical diameter. The elastic deformation of the pile is calculated from Eq. 12 where \(\delta\) is the deformation under the applied test load P on a pile shaft with a length of L and a cross-sectional area of A and elastic modulus of E.
Another method to estimate the ultimate resistance of a screw pile from the load–displacement relationship is to draw a tangent line to the first linear portion of the load–displacement graph and intersect it with the tangent to the second segment of the graph after yielding [27]. The intersection of these lines determines the ultimate load resistance of the pile. Davisson offset limit method [28] determines the ultimate load as the load corresponding to a pile head displacement of 3.8 mm plus the diameter of the pile. AS2159 [8] recommends the ultimate design resistance of a pile (Rt,ug) as the load required to create a pile head net displacement of the greater of the following:
-
(i)
the pile head load that can be kept constant for 10 min; and
-
(ii)
the pile head load corresponding to a pile head deflection limit at the failure of the supporting structure or 0.05D for screw piles and all other precast piles and 0.10D for cast-in-place piles (D is the diameter of the helices in a screw pile or the nominal diameter of the pile shaft for other pile types).
The net displacement of the pile is defined as the total deflection at the pile head beyond the elastic shortening of the shaft under compression (Eq. 12).
Case Studies
With the recent construction boom, demand for new housing estates has exceeded the supply. The suburbs located to the Southeast of Melbourne have now transformed from grazing fields to dense residential areas with houses built by volume builders using waffle pod slabs mostly supported on screw piles. Geologically, the Southeast suburbs are mainly underlain by fill and Quaternary-aged alluvial deposits. Fill and alluvial clays are well known for their reactive nature and low undrained shear strength. In this area, the soil profile consists mainly of a thick layer of soft clay overlaying sandy soil. In such soils, the usage of screw piles as a quick, inexpensive efficient workable option outweighs the benefits of the traditional bored piers. Therefore, most volume builders opt to use waffle pods (instead of raft-slab) in conjunction with screw piles to build their concrete slab. Concrete slabs are poured within a few days after screw piling. However, a rapid screw pile installation in saturated fill or soft clay could introduce high excess pore-water pressure during the installation and hence reduces the shear strength in the vicinity of the screw pile end. This strength reduction may cause settlement to a slab in the short term with serviceability issues for the future occupants of the overlying residential building. Therefore, a sound understanding of the pile behaviour and its interactions with the soil and water table is a prerequisite to provide safe and sustainable design work for future stakeholders of residential/commercial buildings. The current practice of validating screw pile installation in saturated fine-grained soils using cross-correlation between the planetary drive torque and the ultimate bearing capacity of the pile is questionable and therefore comprehensive static/dynamic pile testing is required to determine the safe working loads upon screw piles.
This study evaluates the axial compressive geotechnical strength of low-capacity screw piles installed in cohesive soils based on the results of static load tests and compares them with the calculated ultimate design strengths. The following four full-scale static load tests as per AS2159-2009 [8] section 8.3 were carried out at four different sites of which two sites were underlain by swamp deposits, the third in stiff clay deposit and the fourth site in an alluvial deposit:
-
(i)
Field Test 1: Western Suburb of Melbourne: a swamp deposit along the Kororoit Creek Road in Williamstown.
-
(ii)
Field Test 2: Southeast Suburb of Melbourne: a swamp deposit along Infantry Way, Berwick.
-
(iii)
Field Test 3: Southeast of Regional Victoria: stiff clay along Burke Street, Warragul, Victoria.
-
(iv)
Field Test 4: Southeast Suburb of Melbourne: alluvial deposit along Muddy Gate Lane, Clyde, Victoria.
Figure 3 shows the geological maps of all four sites. All tests and reaction piles in this study were installed using a 15-tonne excavator equipped with a PD12 drive motor with a maximum of 12,000 N.m torque.
Geological maps of selected sites for testing [29]
Williamstown Site
This site is located on the southern side of Kororoit Creek Road in Williamstown (Victoria 3016). The ground surface at the test location was flat lying. The geological map series of Queenscliff by natural resource management maps [29] indicates that the site is underlain by Quaternary age swamp deposits comprising fine sand, silt and silty clay often with shell beds. The swamp deposits may be possibly underlain by Newer Volcanics comprising residual clays underlain by weathered basalt. A detailed site investigation including six boreholes was undertaken to characterise the underground layers. Figure 4 shows the results of one of the boreholes. Groundwater was encountered at a depth of 2.8 m. The test screw pile was made of a CHS shaft with an outer diameter of 88.9 mm and a thickness of 5.5 mm and a single helix with an outer diameter of 400 mm and a thickness and a flight pitch of 12 mm and 100 mm, respectively. The yield strength values of the circular hollow section and helix plate were 350 MPa and 250 MPa, respectively. Figure 5 shows the detailed drawings of the test pile. A static pile load test was carried out on the test pile driven 8 m into the ground. Figure 6 shows the load–displacement graph of the static load test on the tested pile at the Williamstown site.
Site investigation results of Williamstown site [30]
The elastic deformation of the pile under the applied load was calculated as 1.53 mm using Eq. 12 based on the section properties. The ultimate bearing resistance of the pile was determined using the recommended methods by AS2159 [8], Davisson [28], Elkasabgy and El Naggar [25] and double tangent lines [26] as 95 kN, 95 kN, 89 kN and 128 kN, respectively. The estimated ultimate resistance of the pile according to AS2159 [8] is in the middle range between Elkasabgy and El Naggar [26] and Samtani and Nowatzki [27] double tangent methods. The design geotechnical strength (Rd,g) of the pile was calculated using Eq. 2. The φg was adopted as 0.6 in this study based on an overall risk category of low to medium and a piled raft foundation (as per AS2159 [8]). The design geotechnical strength of this pile was calculated as 57 kN.
However, apart from the ultimate limit state check, the settlement of the pile must also be calculated under the combination of dead load and reduced (factored) live load to satisfy the serviceability criteria and limit it to the desired value which is beyond the scope of this study.
Based on the site investigation information, the undrained cohesion of the clay at sublayers of 0–0.3, 0.3–2.0 and 2 m and beyond was assumed to be 0 kPa, 75 kPa and 120 kPa, respectively. At these sublayers, the bulk unit weight of the soil was assumed to be 15.5 kN/m3, 16.5 kN/m3 and 17.5 kN/m3, respectively. The short-term (undrained) geotechnical ultimate strength of the pile based on the abovementioned estimated soil properties using Eq. 10 was calculated as 192 kN, thus yielding a geotechnical design strength (Rd,g) equivalent to 115 kN which is twice the Rd,g value determined by static load test carried out in conjunction with the criteria mentioned in AS2159 [8] to estimate the geotechnical ultimate strength of the pile. The back-calculation of the results shows that if the undrained cohesion values of soil layers are reduced by 40% and the skin friction along soil layers is reduced by 90%, the calculated Rd,g is similar to that was recorded during the static load test. Assuming φg = 0.4 (in the absence of a pile load test), the geotechnical design strength of the pile is determined as 77 kN which is 35% more than the geotechnical design strength determined by the static load test. Two unloading/reloading tests were also carried out to investigate the repeatability of the elastic behaviour of the pile. The results showed that both scenarios achieved a similar gradient (rate of load/displacement) at displacements of 80 mm and 96 mm to that of the initial loading. After each reloading, the axial load of the pile was resumed to the load before unloading which showed the ultimate capacity of the pile is not increasing with further displacement of the pile. Therefore, it is shown that a static load test can accurately estimate the real bearing capacity of a screw pile which differs significantly from the design geotechnical strength calculated using theoretical equations. Thus, it is rational to adopt a geotechnical reduction factor of 0.4 in the absence of static load test results. The application of rapid static load testing on screw piles is an invaluable practice as it elucidates the core relationship between load application and subsequent pile settlement. This relationship is pivotal, not only for accurately determining the requisite dimensions of the screw pile, but also for observing the behaviour of the pile under stress within the founding zone characteristics that encompass elasticity, yielding, and plasticity. In the specific context of the Lake Side Avenue project in Williamstown, the deployment of 448 screw piles, each extending to a depth of 8 m were fabricated and installed. Through precise determination of pile length requirements facilitated by static load tests, the approach used in this specific site prevented the need for additional pile sections, which, in turn, translated to significant cost reductions. It is worth noting that fabricating extensions for the entire suite of 448 piles would have incurred substantial expenses, not merely through materials and labour but also in terms of manufacturing time and logistics. Delays associated with the production and transportation of these extensions would have further compounded costs, jeopardizing the project timeline. Given these points, the primary advantages of this testing method manifested in stark financial and temporal economies. Furthermore, the accuracy imparted by static load testing enhances the overall safety and performance efficacy of the screw pile installations. It is also pertinent to mention that the foreknowledge granted by the testing results affords an additional layer of security in the planning stages, allowing engineers to devise contingency plans for identified potential failure points, promoting an overall safer construction environment.
Berwick Site
This site is underlain by Quaternary swamp sediments comprising clayey silts overlying clays based on the geological map series of Queenscliff by natural resource management [29]. Table 2 shows the summary of the soil stratigraphy at the testing site based on one of the boreholes to a depth of 4.9 m below the existing surface level. No groundwater table was observed in any of the boreholes. Similar CHS profiles and configurations as in the static load test at the Williamstown site were used for both reaction and test screw piles in this site. However, the length of the test pile was extended to 8.25 m and 9 m reaction piles were used to stabilise the reaction beam during the test. Figure 7 shows the load–displacement graph of the static load test on the tested piles at this site.
The elastic deformation of the pile under the applied load was calculated as 2.3 mm according to Eq. 12. The ultimate bearing resistance of the pile was determined as 85 kN, 133 kN, 58 kN and 144 kN based on AS2159 [8], Davisson [28], Elkasabgy and El Naggar [26] and double tangent lines methods. The design geotechnical strength (Rd,g) of the pile based on φg = 0.6 and the estimated ultimate resistance of the pile using the AS2159 [8] method is therefore 51 kN. Based on the soil site investigation information, the undrained cohesion of the clay at sublayers of 0–0.2 m, 0.2–3.4 m and 3.4+ m was assumed to be 0, 30 and 90 kPa, respectively. At the same soil sublayers, the bulk unit weight of the soil was assumed to be 15.5 kN/m3, 17 kN/m3 and 18 kN/m3, respectively. The short-term (undrained) geotechnical ultimate strength of the pile based on the abovementioned data and Eq. 10 was calculated as 184 kN. Therefore, the geotechnical design strength (Rd,g) is equivalent to 73.6 kN assuming φg = 0.4 (in the absence of pile load test) which is 1.44 times the Rd,g determined by static load test in accordance to AS2159 [8] in estimating the ultimate geotechnical strength of the pile. However, if φg is set to 0.6, the geotechnical design strength will be equivalent to 110 kN. The back-calculation of the results shows that if undrained cohesion values of the layers are reduced by 30% and the skin friction values along soil layers are reduced by 90%, the resulting Rd,g is similar to that recorded during the static load test.
An unloading/reloading test carried out soon after showed the gradient of the loading/unloading line was almost 69% higher than the gradient of the initial tangent. This could be explained by the presence of fill material at the top 3.4 m of the ground which may have been compacted with the penetration of the pile.
Warragul Site
The map extracted from the Warragul sheet of the Department of Natural Resources Management [29] indicates that the site is underlain by tertiary extrusive Tholeiitic and minor alkaline basalts. Three boreholes including two of 1.5 m deep and one of 3 m deep were drilled. Table 3 summarises the visual site investigation results. No groundwater or perched water table was observed in any boreholes undertaken at this site.
For this test, reaction piles were made of CHS profiles with an outer diameter of 76.1 mm and thickness of 5 mm welded to a single 300 mm diameter helix of 12 mm thickness and 100 mm flight pitch. However, the test pile was made of a CHS shaft with an outer diameter of 88.9 mm and a thickness of 5.5 mm welded to a single 400 mm diameter helix of 12 mm thickness with 100 mm flight pitch. The reaction piles were 3 m long, and the test pile was 2 m long. Figure 8 shows the load–displacement graph of the static load test on the tested piles at this site.
The elastic deformation of the pile under the applied load was calculated as 1.12 mm according to Eq. 12. The ultimate bearing resistance of the pile was determined as 128 kN, 144 kN, 70 kN and 186 kN based on AS2159 [8], Davisson [28], Elkasabgy and El Naggar [26] and double tangent line methods. The loading–reloading part of the graph was extended to find the geotechnical ultimate strength based on the Davisson method [28] as shown in Fig. 9. The ultimate bearing resistance of the pile based on the double tangent method was determined assuming the load–displacement curve slope is still increasing after 30 mm of displacement. Therefore, the second tangent line was drawn at an axial load of 186 kN. The estimated ultimate resistance of the pile using AS2159 method [8] is 128 kN. Therefore, the design geotechnical strength (Rd,g) of the pile based on φg = 0.6 is estimated to be 77 kN. Based on the site investigation information, the undrained cohesion values of the clay at sublayers of 0–0.2 m, 0.2–0.6 m and 0.6–3.0 m were assumed to be 50 kPa, 75 kPa and 100 kPa, respectively. At the same soil sublayers, the bulk unit weight of the soil was assumed to be 15.5 kN/m3, 16 kN/m3 and 17.5 kN/m3, respectively. The short-term (undrained) geotechnical ultimate strength of the pile based on the abovementioned data and Eq. 10 was calculated as 120 kN yielding a geotechnical design strength (Rd,g) equivalent to 72 kN, which is almost equal to the Rd,g value obtained from static load test based on criteria mentioned in AS2159 [8] in estimating the ultimate geotechnical strength of the pile. However, in the absence of a pile load test using a geotechnical reduction factor of 0.4, the estimated geotechnical design strength would have been 48 kN. The full skin friction value along soil layers was used for the calculation of Ru,g. The unloading/reloading test was also carried out and the gradient of the reloading curve was slightly higher than the gradient of the initial loading. Unlike previous tests involving soft soils, the load–displacement graph did not display any plateau but instead, the load kept increasing with displacement. The test was terminated at a displacement of almost 35 mm due to reaching the capacity of the load cell which was 200 kN.
Clyde Site
The geological maps provided by the department of Natural Resource Management in Queenscliff sheet [29] indicate that the site is underlain by a Quaternary fluvial, alluvial, gravel and silt. Based on the local unpublished information, shallow water tables were reported when the farming communities dug drainages. Visual inspection of the site confirms that the site surface is always wet and at some places saturated throughout the wet seasons. The water table was estimated to be 3.3–3.5 m below the ground level. The swelling–shrinking behaviour of clays upon saturation or shrinkage may influence the bearing capacity of the soil and subsequently may dictate the geotechnical strength of the embedded pile. The test pile was a 3.5 m long CHS with an outer diameter of 76.1 mm welded to a single helix of 350 mm diameter of 10 mm thickness with 100 mm flight pitch positioned 175 mm from the tip of the pile. Reaction piles were 6 m long CHS with an outer diameter of 88.9 mm welded to a single helix of 400 mm diameter of 12 mm thickness with 100 mm flight pitch. The static load test at this site was aimed at investigating the generated excess pore-water pressure (PWP) and total stress at the pile tip within the saturated clay during the installation, loading and unloading stages. This test pile was instrumented with a miniature pore-water pressure sensor (PWPS) and a miniature earth pressure cell (EPC) at the pile tip. Figure 9 shows the field setup and Fig. 10 shows installed transducers. The pore-water pressure transducer was saturated for 24 h before the test and saturated kaolinite paste was smeared on the pore-water pressure transducer surface to keep it saturated during the test and provide a seamless interface with the surrounding soil.
The test screw pile was penetrated to the ground on 29th May 2022 without the installation of reaction screw piles and the reaction beam and the EPC readings at the pile tip were recorded for 5 weeks to monitor the dissipation of installation-induced stresses. This was followed by the first loading on 8th July and subsequent unloading/reloading stages till 3rd August 2022. The loading/unloading test stages were carried out over 66 days.
Figure 11 shows the total stress readings at the test pile tip at 3.5 m below the ground level for the first 6 days after installation of the test pile. The observed end bearing pressure increase after the installation was due to the reaction of the soil layer underneath the pile end with the helix and the circular shaft end and also the generated excess pore-water pressure. This graph has three transient phases including I) excess total stress buildup, II) volatile behaviour and III) steady-state stage. In phase I, after installation, the end bearing pressure of the pile increased to 126 kPa and quickly started dissipating to 66 kPa within the first 5 h. It is to be noted that the subsequent fluctuating end bearing pressure observed between the 36th hour and 96th hours in phase II is mainly attributed to the machinery movement on the ground in the vicinity of the test area. In this phase, the end bearing pressure varied between 16 and 140 kPa within a short interval of 6 h (between 8 AM and 2 PM). Soon afterwards, the end bearing pressure reached a steady state at a pressure of 55 kPa with characteristics synonymous with soil setup behaviour. It is obvious that when the helix cuts through the soil it causes significant disturbance to the soil causing a reduction in its strength and increase in pore-water pressure. However, the soil consolidates with time with a gradual reduction in the excess pore-water pressure which comes along with an increase in effective stress and shear strength, called soil setup behaviour.
Readings of the EPC at the pile tip are total stress values including any generated pore-water pressure. Therefore, the peak pressure recorded by the transducer in Fig. 11 immediately after the installation is for the undrained condition and not a true reflection of the long-term soil strength (drained condition). This observation further supports the argument that the resistance measured during the pile installation is not a true representation of its ultimate geotechnical strength and that the cross-correlation method to quantify the ultimate geotechnical strength of the screw pile is not accurate. The undrained strength (short-term strength) of over-consolidated clays is higher than its drained strength (long-term strength) due to the generated negative excess pore-water pressure in the short term.
The first loading stage was initiated on 8th July 2022 at 22:00 followed by several unloading and reloading stages until the 3rd of August 2022. Figure 12 shows the end bearing pressure, pore-water pressure, and pile head load changes for 144 h after the initial loading followed by subsequent unloading and reloading stages. Upon loading the pile from the top to 30 kN, the EPC transducer at the pile tip responded quickly and showed a prompt increase to values beyond 300 kPa. The loaded pile was monitored for 20 h or more and during this monitoring period, both the pile head load and the end bearing pressure dissipated gradually. An interesting observation on the pile head displacement was that despite the pile head load being reduced to zero during the unloading stage, the pile was still undergoing downwards movement, meaning the screw pile is experiencing creep settlements. This was in tandem with the lower limit of the end bearing pressure observed after unloading which did not return to zero and remained in a range of 100–130 kPa. The measured pore-water pressure at the pile tip showed that upon the first loading stage, there was an excess pore-water pressure of 94 kPa which dissipated to about 30 kPa after 24 h. However, with the subsequent loading/reloading stages, the pore-water pressure did not change significantly and remained consistently below 50 kPa until the end of the test. This observation can be explained using the level of the water table which was slightly above the pile tip. The pore-water pressure after the first loading was not influenced by subsequent loading stages due to the deformation made in the soil during the initial loading stage and possible additional void formation after the first unloading stage which caused the soil to over-consolidate. The pore-water pressure reduction due to over-consolidation was slightly balanced off when subsequent loading took place, and the results were seen in a form of a steady increase in pore-water pressure. However, the difference between EPC and PWP readings remained somewhat constant, which shows that effective stress has not been fully realised and the soil consolidation is ongoing. Soil consolidation around the pile tip is governed by the excess pore-water pressure dissipation rate, seepage, and the hydraulic conductivity of the soil. The consolidation process continues until the excess pore-water pressure is fully dissipated. Figure 13 shows the whole view of the loading/dissipation and unloading from the initial loading stage in late May until the end of the test in early August. A continuous reduction in EPC transducer reading was observed during the dissipation stage from 144 to 448 h (i.e. more than 12.5 days) when the final loading/dissipation stage was undertaken afterwards. Therefore, although the dissipation stage was extended, more time was required to reach a constant effective stress level at the pile tip to determine the true bearing strength of the pile in the host saturated clay.
Screw piles in high water table conditions present several challenges during the design, installation and post-installation phases as evidenced by field testing. The presence of a high water table introduces factors such as buoyancy and hydrostatic pressure, which can significantly affect the structural integrity and load-bearing capacity of screw piles. This often requires specialised design modifications such as increased pile length and diameter, as well as selecting materials that can resist corrosion due to prolonged exposure to moisture. Installation issues are also complex. The high water table can resist against the applied torque to penetrate the pile with the potential for sidewall collapses in the pile insertion point. It may require installation techniques that minimise water ingress and soil disturbance, such as using casing or grouting. Moreover, screw pile installation in saturated soils can lead to soil liquefaction, making it difficult to achieve the desired pile depth and bearing capacity. Long-term field tests have further demonstrated that high water table grounds can lead to increased rates of corrosion and degradation of the pile material, as the constant exposure to water and dissolved minerals accelerates these processes. Additionally, fluctuations in the water table can lead to cyclic loading effects, soil structure changes, and heave, all of which may compromise the pile’s stability and capacity over time.
Conclusions
With the rapid development across Melbourne’s suburbs causing more conversion of agricultural lands underlain by Quaternary-aged cohesive soil deposits to residential blocks, builders tend to adopt low-capacity screw piles as a viable economical option in managing risk involving settlement in shallow foundations. Meanwhile, the Australian Piling Code (AS2159 [8]) in estimating screw pile geotechnical strength does not restrict the shape, type or number of plates that can be used to obtain the desired end bearing resistance, but it does provide specific methods to test screw piles and limit their risks by adopting stringent reduction factors on the geotechnical ultimate strength of the soil. The following conclusions were made based on the results of this study.
-
AS 2159 [8] requires pile load testing for piles where the basic geotechnical reduction factor (φgb) is greater than 0.4 and the average risk factor rating (ARR) is greater than 2.5. The results of this study showed that in saturated clays with shallow water tables, the widely used cross-correlation between installation torque and ultimate resistance of screw piles method is not valid and there is a risk to relying on the estimated strength from this approach. In the short term (during the installation), the soil around the shaft and more importantly at the vicinity of the pile tip will undergo an undrained loading that increases the excess pore-water pressure in normally consolidated clays and reduces the excess pore-water pressure in over-consolidated clays. However, once the excess pore-water pressure at the pile end has dissipated, the true drained strength of the soil which may be lower or higher than the undrained strength appears which impacts the ultimate capacity of the pile.
-
Based on the reported data from four full-scale static load tests in different suburbs of Victoria and the observed discrepancies between the values obtained from engineering design works and results from field static load tests, it is highly recommended that in the absence of a static load test in the vicinity of the site, at least one static load test is undertaken to verify the design works and provide a safe foundation design for the future occupants of the building.
-
Moreover, in the absence of detailed soil testing and classification, a static pile load test can be a useful and accurate tool in determining the ultimate axial capacity of a screw pile. In all cases reported in this study, the suggested pile length based on the engineering design calculations was shorter than what was required to achieve the required design strength. This was concluded after static load tests, and therefore an amended design was provided to satisfy the design action effects based on [31]. Therefore, it is highly recommended to adopt a geotechnical reduction factor of 0.4 in the absence of static load test results.
-
The helix diameter, skin friction, soil type and groundwater profile have significant individual effects on the formation of pile capacity. In this study, the observed differences in the geotechnical design strength between that from calculations and that recorded from static load tests might have been due to the conservative nature of AS2159 [8] to determine the ultimate strength of the pile based on the load–displacement graph of the static load test.
Data Availability
The data that support the findings of this study are available on request from the corresponding author.
References
Carol M, Roy RM (2018) Ultimate load bearing capacity and settlement of triangular screw pile based on design parameter. Int Res J Eng Technol 5(6):475–477
Ali OK, Abbas HO (2019) Performance assessment of screw piles embedded in soft clay. Civ Eng J 5(8):1788–1798
Mondal S, Disfani MM, Mehdizadeh A (2023) Behaviour of bio-inspired grouped battered minipiles under lateral loading in clay. Acta Geotech:1–20
Aydin M et al (2011) Osterberg cell load testing on helical piles. In: Geo-frontiers 2011, pp 66–74
Sakr M (2013) Relationship between installation torque and axial capacities of helical piles in cohesive soils. DFI J J Deep Found Inst 7(1):44–58
Bagheri F, El Naggar MH (2015) Effects of installation disturbance on behavior of multi-helix piles in structured clays. DFI J J Deep Found Inst 9(2):80–91. https://doi.org/10.1179/1937525515y.0000000008
Weech CN (2002) Installation and load testing of helical piles in a sensitive fine-grained soil. M.Sc Thesis, University of British Columbia
AS 2159 (2009) Piling-design and installation (AS2159-2009). Standards Australia, Sydney
Mohajerani A et al (2016) Analysis and design methods of screw piles: a review. Soils Found 56(1):115–128. https://doi.org/10.1016/j.sandf.2016.01.009
Beim J, Luna SC (2012) Results of dynamic and static load tests on helical piles in the varved clay of Massachusetts. DFI J J Deep Found Inst 6(1):58–67
Tappenden KM, Sego DC (2007) Predicting the axial capacity of screw piles installed in Canadian soils. In: The Canadian geotechnical society (CGS), OttawaGeo2007 conference, pp 1608–1615
Hawkins K, Thorsten R (2009) Load test results-large diameter helical pipe piles. In: Contemporary topics in deep foundations. American Society of Civil Engineers, USA
Mooney JS et al (1985) Uplift capacity of helical anchors in clay and silt. In: Unknown host publication title. American Society of Civil Engineers (ASCE), pp 48–72
Mitsch, MP, Clemence SP (1985) Uplift capacity of helix anchors in sand. Paper presented at the In: uplift behaviour of anchor foundations in soil. American Society of Civil Engineers, New York
Nasr MH (2004) Large-capacity-screw-piles. Paper presented at the In: proceedings of the international conference: future vision and challenges for urban development, Cairo, Egypt
Zhang DJY (1999) Predicting capacity of helical screw piles in Alberta Soil. M.Sc Thesis, University of Alberta, Edmonton, Alberta
Rao SN, Prasad YVSN (1993) Estimation of uplift capacity of helical anchors in clays. J Geotech Eng 119(2):352–357
Meyerhof GG (1976) Bearing capacity and settlement of pile foundations. J Geotech Eng Div 102(3):197–228
Budhu M (2011) Soil mechanics and foundations, 3rd edn. Wiley, New York
Meyerhof GG, Adams JI (1968) The ultimate uplift capacity of foundation. Can Geotech J 5(4):224–244
AS 4100 (2020b) Steel structures AS4100:2020. Australia Standards
ASTM D1143/D1143M (2007) Test methods for deep foundations under static axial compressive load. ASTM International
Soderberg LO (1962) Consolidation theory applied to foundation pile time effects. Geotechnique 12(3):217–225
Seed HB, Reese LC (1957) The action of soft clay along friction piles. Trans Am Soc Civ Eng 122(1):731–754
Karkush MO, Hussein AA (2021) Experimental investigation of bearing capacity of screw piles and excess porewater pressure in soft clay under static axial loading. Paper presented at the E3S Web of Conferences
Elkasabgy M, El Naggar MH (2015) Axial compressive response of large-capacity helical and driven steel piles in cohesive soil. Can Geotech J 52(2):224–243. https://doi.org/10.1139/cgj-2012-0331
Samtani NC, Nowatzki EA (2006) Soils and foundations: reference manual (No. FHWA-NHI-06-088). Federal Highway Administration, USA
Davisson MT (1972) High capacity piles. In: Proc. innovations in found. const., p 52
VandenBerg AHM (1997) Melbourne SJ 55-5 Edition 2, 1:250 000 Geological map series. 1:250 000 geological map. Geological Survey of Victoria
Creation Homes (2021) Unpublished geotechnical investigation report for proposed residential development-1 Lakeview Avenue, Williamstown
AS1170 (2020) Structural design actions AS1170-2020. Standards Australia, Sydney
Acknowledgements
The authors would like to thank Mr Henwood from R&A concreting for using the R&A concreting job sites and facilities in carrying out field tests and GeotechTronics Pty Ltd for assisting to provide and install instrumentations and data logging systems for this study.
Funding
Open Access funding enabled and organized by CAUL and its Member Institutions.
Author information
Authors and Affiliations
Corresponding author
Ethics declarations
Conflict of Interest
The authors have no competing interests to declare that are relevant to the content of this article.
Additional information
Publisher's Note
Springer Nature remains neutral with regard to jurisdictional claims in published maps and institutional affiliations.
Rights and permissions
Open Access This article is licensed under a Creative Commons Attribution 4.0 International License, which permits use, sharing, adaptation, distribution and reproduction in any medium or format, as long as you give appropriate credit to the original author(s) and the source, provide a link to the Creative Commons licence, and indicate if changes were made. The images or other third party material in this article are included in the article's Creative Commons licence, unless indicated otherwise in a credit line to the material. If material is not included in the article's Creative Commons licence and your intended use is not permitted by statutory regulation or exceeds the permitted use, you will need to obtain permission directly from the copyright holder. To view a copy of this licence, visit http://creativecommons.org/licenses/by/4.0/.
About this article
Cite this article
Verumandy, K., Arulrajah, A., Mirzababaei, M. et al. Static Load Testing of Instrumented Screw Piles in Soft Soil Deposits. Int. J. of Geosynth. and Ground Eng. 10, 10 (2024). https://doi.org/10.1007/s40891-023-00519-x
Received:
Accepted:
Published:
DOI: https://doi.org/10.1007/s40891-023-00519-x