Abstract
Precipitation is a common phenomenon that occurs during heat treatments. There is internal stress around the precipitate owing to the lattice misfit between the precipitate and matrix. This internal stress has a significant influence not only on the precipitation kinetics but also on the material properties. The misfit stress can be obtained by numerically solving the mechanical equilibrium equations. However, this process is complex and time-consuming. We developed a new approach based on deep learning to accelerate the solution process. The training data were first generated by a phase-field model coupled with elastic mechanical equilibrium equations, which were solved using the finite difference method. The obtained precipitate morphologies and corresponding stress distributions were input data for training the physics-informed (PI) UNet model. The well-trained PI-UNet model can then be applied to predicting stress distributions with the precipitate morphology as the input. Prediction accuracy and efficiency are discussed in this study. The results showed that the PI-UNet model was an appropriate approach for quickly predicting the misfit stress between the precipitate and matrix.







Similar content being viewed by others
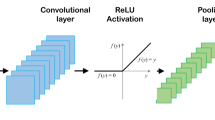
Reference
Ma CZ, Zhang RJ, Li ZX et al (2022) Solidification shrinkage and shrinkage-induced melt convection and their relations with solute segregation in binary alloys. Comp Mater Sci 215:111815. https://doi.org/10.1016/j.commatsci.2022.111815
LeCun Y, Bengio Y, Hinton G (2015) Deep learning. Nature 521:436–444
Warmuzek M, Zelawski M, Jalocha T (2021) Application of the convolutional neural network for recognition of the metal alloys microstructure constituents based on their morphological characteristics. Comp Mater Sci 199:110722. https://doi.org/10.1016/j.commatsci.2021.110722
Li Y, Zhou X, Colnaghi T et al (2021) Convolutional neural network-assisted recognition of nanoscale L12 ordered structures in face-centred cubic alloys. NPJ Comput Mater 7:8. https://doi.org/10.1038/s41524-020-00472-7
Ma B, Ban X, Huang H et al (2018) Deep learning-based image segmentation for Al-La alloy microscopic images. Symmetry 10(4):107–119
Yang K, Cao Y, Zhang Y et al (2021) Self-supervised learning and prediction of microstructure evolution with convolutional recurrent neural networks. Patterns 2(5):100243. https://doi.org/10.1016/j.patter.2021.100243
Zapiain DMD, Stewart JA, Dingreville R (2021) Accelerating phase-field-based microstructure evolution predictions via surrogate models trained by machine learning methods. NPJ Comput Mater 7:3. https://doi.org/10.1038/s41524-020-00471-8
Yang ZJ, Yabansu YC, Jha D et al (2019) Establishing structure-property localization linkages for elastic deformation of three-dimensional high contrast composites using deep learning approaches. Acta Mater 166:335–345
Buades A, Coll B, Morel JM (2005) A review of image denoising algorithms, with a new one. Multiscale Model Sim 4(2):490–530
Chan T, Esedoglu S, Park F et al (2005) Recent developments in total variation image restoration. Math Models Comput Vis 17(2):17–31
Ronneberger O, Fischer P, Brox T (2015) U-Net: convolutional networks for biomedical image segmentation. Lect Notes Comput Sc 9351:234–241
Kim JW, Cherukara MJ, Tripathi A et al (2021) Inversion of coherent surface scattering images via deep learning network. Appl Phys Lett 119(19):191601. https://doi.org/10.1063/5.0063903
Deshpande S, Lengiewicz J, Bordas SP (2022) Probabilistic deep learning for real time large deformation simulations. Comput Methods Appl Mech 398:115307. https://doi.org/10.1016/j.cma.2022.115307
Peivaste I, Siboni NH, Alahyarizadeh G et al (2022) Machine-learning-based surrogate modeling of microstructure evolution using phase-field. Comput Mater Sci 214:111750. https://doi.org/10.1016/j.commatsci.2022.111750
Mianroodi JR, Siboni NH, Raabe D (2021) Teaching solid mechanics to artificial intelligence—a fast solver for heterogeneous materials. NPJ Comput Mater 7:99. https://doi.org/10.1038/s41524-021-00571-z
Raissi M, Perdikaris P, Karniadakis GE (2019) Physics-informed neural networks: a deep learning framework for solving forward and inverse problems involving nonlinear partial differential equations. J Comput Phys 378:686–707
Yonekura K, Maruoka K, Tyou K et al (2023) Super-resolving 2D stress tensor field conserving equilibrium constraints using physics-informed U-Net. Finite Elem Anal Des 213:103852. https://doi.org/10.1016/j.finel.2022.103852
Zhu Q, Liu Z, Yan J (2021) Machine learning for metal additive manufacturing: predicting temperature and melt pool fluid dynamics using physics-informed neural networks. Comput Mech 67:619–635
Chen LQ (2002) Phase-field models for microstructure evolution. Annu Rev Mater Res 32(1):113–140
Kim SG (2007) A phase-field model with antitrapping current for multicomponent alloys with arbitrary thermodynamic properties. Acta Mater 55:4391–4399
Kim SG, Kim WT, Suzuki T (1999) Phase-field model for binary alloys. Phys Rev E 60(6):7186–7197
Hu SY, Murray J, Weiland H et al (2007) Thermodynamic description and growth kinetics of stoichiometric precipitates in the phase-field approach. Calphad 31(2):303–312
Hwang JY, Banerjee R, Doty HW et al (2009) The effect of Mg on the structure and properties of Type 319 aluminum casting alloys. Acta Mater 57(4):1308–1317
Loginova I, Ågren J, Amberg G (2004) On the formation of Widmanstätten ferrite in binary Fe-C phase-field approach. Acta Mater 52(13):4055–4063
Weakley-Bollin SC, Donlon W, Wolverton C et al (2004) Modeling the age-hardening behavior of Al-Si-Cu alloys. Metall Mater Trans A 35(8):2407–2418
Zhu JZ, Chen LQ, Shen J (2001) Morphological evolution during phase separation and coarsening with strong inhomogeneous elasticity. Model Simul Mater Sci Eng 9(6):499–511
Sharma S, Sharma S, Athaiya A (2017) Activation functions in neural networks. Towards Data Sci 6(12):310–316
Chen H, Wang YH, Fan CH (2021) A convolutional autoencoder-based approach with batch normalization for energy disaggregation. J Supercomput 77:2961–2978
Balasundaram S, Prasad SC (2020) Robust twin support vector regression based on Huber loss function. Neural Comput Appl 32:11285–11309
Sun RY (2020) Optimization for deep learning: an overview. J Oper Res Soc China 8(2):249–294
Park H, Stefanski L (1998) Relative-error prediction. Stat Probabil Lett 40(3):227–236
Acknowledgments
This work was financially supported by the National Natural Science Foundation of China (Grant No. 52271019), and the Key Area Research and Development Program of Guangdong Province (Grant No. 2019B010942001).
Author information
Authors and Affiliations
Corresponding author
Rights and permissions
Springer Nature or its licensor (e.g. a society or other partner) holds exclusive rights to this article under a publishing agreement with the author(s) or other rightsholder(s); author self-archiving of the accepted manuscript version of this article is solely governed by the terms of such publishing agreement and applicable law.
About this article
Cite this article
Guo, CX., Yang, HY. & Zhang, RJ. Accelerating the solving of mechanical equilibrium caused by lattice misfit through deep learning method. Adv. Manuf. (2024). https://doi.org/10.1007/s40436-024-00494-0
Received:
Revised:
Accepted:
Published:
DOI: https://doi.org/10.1007/s40436-024-00494-0