Abstract
This paper presents the workspace analysis of calibrated multi-position synthesized 3-prismatic-revolute-spherical (3-PRS) manipulator. The synthesis and workspace analysis of a multi-position manipulator are carried out by least square and Renka Cline gridding approaches. The position parameters such as position, orientation, direction, location of revolute-spherical joints are designed based on loop techniques. Based on manipulator constraints, the position parameters are synthesized and calibrated by comparing prescribed and obtained positions of revolute and spherical joints. The results are in close agreement with the positions of the 3-PRS manipulator. This work is used to obtain tip-tilt-position of the manipulator and is suitable in surgical, telescopic and space applications.









Similar content being viewed by others
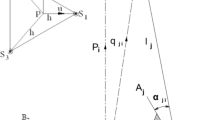
Data Availability
Data of manuscript was transparent.
Code Availability
Not applicable.
References
H.S. Kim, L.-W. Tsai, Kinematic synthesis of a spatial 3-RPS parallel manipulator. J. ASME 125, 92–97 (2003). https://doi.org/10.1115/1.1539505
P.S. Rao, N.M. Rao, Position analysis of Spatial 3-RPS parallel manipulator. Int. J. Mech. Eng. Rob. Res. 2(2), 80–90 (2013)
Y. Li, Q. Xu, Kinematic analysis of a 3-PRS parallel manipulator. J. Robot. Comput. Integr. Manuf. 23, 395–408 (2007). https://doi.org/10.1016/j.rcim.2006.04.007
S.R. Pundru, M.R. Nalluri, Spatial three degree of freedom parallel manipulator forward kinematic position analysis. Int. J Eng. Tech. (UAE) 7(4.5), 147–150 (2018). https://doi.org/10.14419/ijet.v7i4.5.20032
S.R. Pundru, M.R. Nalluri, Three degree of freedom spatial parallel manipulator inverse kinematic position analysis. Int. J Eng. Tech. (UAE) 7(45), 98–101 (2018). https://doi.org/10.14419/ijet.v7i4.5.20020
F. Tahmasebi, Kinematics of a new high-precision three-degree- of- freedom parallel manipulator. J. ASME 129, 320–325 (2007). https://doi.org/10.1115/1.2406103
G. Pond, J. Carretero, Singularity analysis and workspace optimization of the inclined PRS manipulator. CSME Forum 1–7 (2004) (Proceedings of the CCToMM M^3 Symposium (2004). www.researchgate.net/profile/Juan_Carretero/publication/229018477
S.R. Pundru, M.R. Nalluri, Synthesis of 3-PRS manipulator using exact method. J. Inst. Eng. India Ser. C 100, 1031–1042 (2019). https://doi.org/10.1007/s40032-018-0499-6
S. Lu, Y. Li, B. Ding, Multi-objective dimensional optimization of a 3-dof translational PKM considering transmission properties. Int. J. Autom. Comput.Autom. Comput. 16, 748–760 (2019). https://doi.org/10.1007/s11633-019-1184-9
S.R. Pundru, M.R. Nalluri, Synthesis of multi-positions 3-prismatic-revolute-spherical manipulator. J. SN Appl. Sci. 1, 1114 (2019). https://doi.org/10.1007/s42452-019-1085-0
S.R. Pundru, M.R. Nalluri, Synthesis of 3-PRS manipulator based on revolute and cone angle of spherical constraints on range of rotational motion of spherical joints. J. Inst. Eng. India Ser. C 102, 209–219 (2021). https://doi.org/10.1007/s40032-020-00599-y
A.Y. Fan LiangZhi, L.X. Elatta, Kinematic calibration for a hybrid 5DOF manipulator based on 3-RPS in-actuated parallel manipulator. Int. J. Adv. Manuf. Technol. 25, 730–734 (2005). https://doi.org/10.1007/s00170-003-1987-1
A. Jain, H.P. Jawale, Study of the effects of link tolerances to estimate mechanical errors in 3-RRS parallel manipulator. J. Mech. Eng. Sci. (2021). https://doi.org/10.1177/09544062211021451
P.S. Rao, Calibrating a synthesized 3-PRS manipulator by minimizing the errors in positions of revolute joints. J. Inst. Eng. India Ser. C 103(5), 1083–1093 (2022). https://doi.org/10.1007/s40032-022-00866-0
Q. Li, Z. Chen, Q. Chen, C. Wu, X. Hu, Parasitic motion comparison of 3-PRS parallel mechanism with different limb arrangements. J. Robot. Comput. Integr. Manuf. 27, 389–396 (2011). https://doi.org/10.1016/j.rcim.2010.08.007
S.R. Pundru, Synthesis of multi-position 3-PRS manipulator based on spherical constraints by eliminating the parasitic motion. J. Inst. Eng. India Ser. C 103(6), 1447–1454 (2022). https://doi.org/10.1007/s40032-022-00887-9
J.W. Yoon, J. Ryu, Y.K. Hwang, Optimum design of 6-dof parallel manipulator with translational/rotational workspaces for haptic device application. J. Mech. Sci. Technol. 24(5), 1151–1162 (2010). https://doi.org/10.1007/s12206-010-0321-8
J.-S. Zhao, M. Chen, K. Zhou, J.-X. Dong, Z.-J. Feng, Workspace of parallel manipulators with symmetric identical kinematic chains. J. Mech. Mach. Theory 41, 632–645 (2006). https://doi.org/10.1016/j.mechmachtheory.2005.09.007
Lu. Yi, Xu. Jiayin, Yu. Jianping, Using CAD geometric variation approach machining complex workpiece by a 3-SPR parallel machine tool. Robot. Comput. Integr. Manuf. 26(2), 130–136 (2010). https://doi.org/10.1016/j.rcim.2009.09.003
Acknowledgements
Very much thankful to Editor. The authors declare that they have no acknowledgments.
Funding
The authors declare that they have no funding.
Author information
Authors and Affiliations
Contributions
All authors contributed to the study conception and design. Material preparation, data collection and analysis were performed by [Srinivasa Rao Pundru]. The first draft of the manuscript was written by [Srinivasa Rao Pundru] and all authors commented on previous versions of the manuscript. All others read and approved the final manuscript. Conceptualization: [Srinivasa Rao Pundru]. Methodology: [Srinivasa Rao Pundru]. Formal analysis and investigation: [Srinivasa Rao Pundru]. Writing-original draft preparation: [Srinivasa Rao Pundru]. Writing-review and editing: [Srinivasa Rao Pundru]. Funding acquisition: The authors declare that they have no funding. Resources: The authors declare that they have no funding resources.
Corresponding author
Ethics declarations
Conflict of interest
The authors declare that they have no conflict of interest.
Disclosure of Potential Conflict of interest
Not applicable.
Potential Conflict of interest (Financial or Non-financial)
Not applicable.
Compliance with Ethical Standards
Not applicable.
Research Involving Human Participants and/or Animals
Not applicable.
Informed Consent
Not applicable.
Additional information
Publisher's Note
Springer Nature remains neutral with regard to jurisdictional claims in published maps and institutional affiliations.
Rights and permissions
Springer Nature or its licensor (e.g. a society or other partner) holds exclusive rights to this article under a publishing agreement with the author(s) or other rightsholder(s); author self-archiving of the accepted manuscript version of this article is solely governed by the terms of such publishing agreement and applicable law.
About this article
Cite this article
Pundru, S.R. Workspace Analysis of Calibrated Multi-position Synthesized 3-Prismatic-Revolute-Spherical Manipulator. J. Inst. Eng. India Ser. C 105, 195–214 (2024). https://doi.org/10.1007/s40032-023-01017-9
Received:
Accepted:
Published:
Issue Date:
DOI: https://doi.org/10.1007/s40032-023-01017-9