Abstract
Generating value from wastes via pyrolysis has been increasingly researched in recent times. Biochar is a versatile pyrolysis product with yields based on many process parameters, including feedstock type and particle size, and operating conditions such as pyrolysis reactor, heating rate, residence time, and reaction temperature. The heterogeneous nature of waste biomass creates challenges in controlling the pyrolysis’ product selectivity. Intensive and time-consuming experimental studies are often required to determine product distribution for the pyrolysis of each unique feedstock. Alternatively, prediction models that learn from a wide range of existing experimental data may provide insight into potential yields for different biomass sources. Several advanced models exist in the literature which can predict the yield of biochar and subsequent products based on operating temperature. However, these models do not consider the combined effect of biomass characteristics and operating conditions on biochar yield, which is considered a decisive factor for biochar formation. As such, the objective of this study is to develop a prediction model based on the biomass’ fixed carbon content (14–22%), reaction temperature (350–750 °C), and heating rate (5–10 °C/min) using the response surface methodology. Biomasses, date stones, spent coffee grounds, and cow manure have been used to design a Box-Behnken experiment based on the three factors for the biochar yield response. An empirical equation is developed based on a statistically significant quadratic model to produce optimized biochar yield with high prediction accuracy. The study discussed the 3D response and diagnostic plots and conducted validation experiments to confirm the applicability of the developed model. The biochar yields are significantly affected by the fixed carbon content of the feedstock and the reaction temperature, and the experimental validation confirms the accuracy of biochar yield quantification. The model can be easily applied for further process flow modeling of biomass pyrolysis, only relying on proximate feed analysis, operating temperature, and heating rate.
Similar content being viewed by others
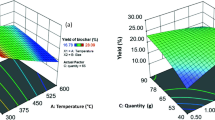
Avoid common mistakes on your manuscript.
1 Introduction
In recent years, the pursuit of sustainable waste management technologies has increased significantly due to several reasons including the increasing waste generation along with the increasing population and food production, pollution from traditional waste management technologies such as incineration and landfilling which led to growing concerns in waste management [1, 2]. Alternatively, the interest in generating valuable products from waste and developing a circular economy is eminent [3]. Pyrolysis is a thermochemical conversion technology that is considered a recent solid waste management technology with many advantages, including value-added product generation, efficient waste conversion, feedstock flexibility, fast reaction times, and environmental friendliness [4, 5]. Process parameters including feedstock type and operating conditions such as pyrolysis reactor, heating rate, residence time, reaction temperature, and particle size are crucial in defining the pyrolysis products [6]. The process occurs at high temperatures with the absence of oxygen, where biomass components (lignin, cellulose, and hemicellulose) degrade into solids, liquids, and gas fractions [7]. The volatile components (liquid and gas fractions) are promising as intermediate products for bioenergy and the chemicals industry. The solid fractions called “biochar” (the interest of this study) are used for a variety of applications. Several literature reviews have discussed biochar uses in agriculture, wastewater treatment (adsorption), energy (capacitors, batteries, catalysts), construction, composite production, soil conditioning, and carbon sequestration due to its unique physical and chemical properties [8, 9]. The abundance and renewability of biomass feeds make them attractive, although there are worries about competition between food production and bioenergy production. Therefore, there has recently been a shift from food-grade biomass towards waste biomass [10]. A number of recent reviews have evaluated different aspects of biochar, including its combustion and mechanical behavior [9], environmental applications [11], and lignocellulosic biomass feeds [12]. Product yield is crucial for modeling purposes, considering biochar’s versatility and complex production nature. Experimental quantification of biochar yields is expensive and energy- and time-consuming, requiring quick predictive models.
A recent publication predicted biochar and bio-oil yields due to co-pyrolysis (mixed biomass and plastics) using supervised machine learning (ML), an artificial intelligence tool [13]. Investigations often are conducted on one factor—usually based on operating conditions—a one-variable-at-a-time (OVAT) approach. However, the design of experiments (DOE) is employed due to its efficiency in controlled experimentation based on different process factors [14]. Furthermore, accurate predictions of liquid yields due to other experimental conditions and optimization of mixed waste feeds, using an experimental factorial design based on response surface methodology, were accomplished in another study [15]. The formation of gaseous and liquid compounds was based on operating conditions of reaction temperature, reaction time, and initial pressure leading to significant liquid yields. Alternatively, a full factorial design was employed in another study to characterize all three product yields based on operating conditions of heating rate, temperature, and isothermal time [14]. Several studies have attempted to develop prediction models using machine learning tools based on the biomass characteristics, such as its proximate and ultimate analyses for product yields [16, 17]. Such studies do not provide an empirical model for biochar yield prediction, but rather reflect the main factor that influences the product yields based on analyzing a collection of experimental results. For instance, the volatile matter, ash content, and hydrogen content influenced the char yields [16], and the heating rate was the most important factor for bio-oil oxygen contents [17]. Meanwhile, Neves et al. [18] developed a prediction model based on mass and energy balance approaches, considering the pyrolysis yield of more than 60 biomass samples. However, Song [19] has further developed the former model by considering the reaction kinetics, where the product yields and (C-H–O) elemental composition were linked to the process’ operating temperature. Nevertheless, Swagathnath et al. [20] have further modified Neves and Song’s models to account for biomass composition effect on the bio-oil and syngas compositions and yield.
While the former key models provided a good insight on biomass pyrolytic decomposition behavior, a main research gap persists in the prediction of biochar yield considering biomass characteristics combined with operating conditions, where biochar yield calculation is a vital prerequisite step required for the calculation of other products distribution and composition. The fixed carbon of biomass is directly linked to its lignin content [21], while both values are crucial in determining the potential biochar yield for each specific biomass [22], whereas the combination of process’ operating temperature (°C) and heating rate (°C/min) is a decisive factor for the definition of final biochar yield. As such, this study aims to understand the effects of biomass composition—specifically fixed carbon—and main operating conditions in a multifactorial design experiment. Among the different methods of response surface methodology (RSM), the Box-Behnken design (BBD) is one of the most successfully applied multivariate statistical tools for multi-factor optimization for a variety of processes due to its efficiency and a minimum number of experiments [23,24,25]. They are known to be more efficient than other designs—3-level factorial design, central composite design, Doehlert design—since they are rotatable with an absence of combinations where factors are at extreme points (highest and lowest) [26].
An RSM study showed that temperature is the most significant parameter rather than particle size and residence time for hydrochar production using hydrothermal carbonization [23]. A recent study found that temperature and heating rate are the most significant factors contributing to biochar yields compared to gas flow rate [27]. A previous study has also reported the highest significant influence for temperature and heating rate for Eichhornia crassipes stem biochar production [28]. However, to the authors’ knowledge, this study is the first to understand the effect of fixed carbon and operating conditions using RSM. Temperature and heating rate directly reflect the slow and fast pyrolysis and the associated increase in solid and liquid yields [29], and biomass components have been known to affect char yield [30]. Proximate analysis is a commonly conducted characterization method when undertaking biomass thermal conversions, since the moisture, volatile matter, and fixed carbons affect the thermal behavior and therefore plant designs [31]. Additionally, the applicability of the empirical model developed from the statistical analysis of the results as a biochar yield prediction model could be a valuable tool for researchers, process simulators, and private and government entities working on converting wastes to biochar using pyrolysis. Therefore, the main hypothesis of this study is the fixed carbon in biomasses significantly affects the biochar yields during pyrolysis, which could help develop a prediction model.
Three different biomasses were examined—date stones (DS), spent coffee grounds (SCG), and cow manure (CM)—in this study to understand the effect of fixed carbon and, thereby, the feedstock type on biochar yield. The authors have previously studied the feeds to understand the potential for bio-oil production using a micro-scale pyrolyzer [32]. The biomasses are chosen due to (i) the significant production of the waste biomasses in the authors’ country (Qatar) and the world as described in the published paper; (ii) the requirement to understand the biochar production for the single, binary, and ternary feeds; and (iii) the novelty in the significant difference in fixed carbon content among the three feeds could be utilized for developing prediction models. The prediction model developed in this study to understand the biochar yields is validated against experimental analysis using tubular reactors and thermogravimetric analysis (TGA) and another published prediction model for single, binary, and ternary co-pyrolysis.
2 Materials and methods
2.1 Biomass feedstock acquisition, characterization, and fixed carbon quantification
The three biomasses (DS, SCG, and CM) were separately acquired. While the DS was extracted from commercially purchased dates (Doha Dates, National Food Co.), SCG was collected from the university coffee shop. CM was collected from a dairy products company based in Qatar. All samples were washed, and DS was dried at 105 °C for 24 h, then electrically ground and sieved to 710 µm using a sifter supplied by Haver & Boecker, Germany. The proximate and ultimate analyses were conducted for the single (DS, SCG, CM), binary (DS:SCG, DS:CM, SCG:CM), and ternary feeds (DS:SCG:CM) and published in another paper by the authors [32]. The feeds are abbreviated as DP, CW, and CD instead of DS, SCG, and CM, although they are sourced from the same place.
The calorific values of the feeds were measured using an Automated Osoperibol Fixed Bomb Parr 6300 bomb calorimeter in an atmosphere of O2 that assures the complete combusting of the sample. A dried sample of 0.2 to 0.6 g was measured and placed inside the bomb with a magnetic thread and filled with oxygen with a pressure of 4000 psi. After filling with oxygen, the bomb was placed inside the water bucket with 2 L of water. The mercury-in-glass thermometers, platinum resistance thermometers, quartz oscillators, and thermistor systems measure the temperature rise in the bucket. Finally, the pseudo-component analysis of the feed—quantifying the hemicellulose, cellulose, and lignin content—was conducted following a published methodology [33].
2.2 Biochar production using a tube furnace for biomass pyrolysis
A tube furnace (TF) (OTF-1200X, MTI CORPORATION) was used to conduct the co-pyrolysis process and collect the products generated for further analysis. Figure 1 is a schematic representation of the laboratory set-up to collect biochar products. Samples of about 3.00 ± 0.1 g placed in a quartz crucible were heated from room temperature to study operating conditions in the presence of constant high-purity nitrogen (99.99%) at a 100 mL/min flow rate and for a residence time of 20 min. The biochar was collected, and the yield was calculated using Eq. 1.
2.3 Response surface methodology for prediction modeling
RSM is an optimization tool based on statistical and mathematical techniques for optimizing processes by reducing the number of runs and simultaneously establishing a relationship between the variables and responses. The Design Expert 13 software (Stat-Ease, Inc., Minneapolis, MN) was used to design the experiment, tabulate the responses, and analyze the experimental results. Optimization for maximum biochar yield was employed using a Box-Behnken Design (BBD). Three numeric factors are included in the design: fixed carbon of the feed (A) in %, reaction temperature (B) in °C, and heating rate (°C) in (°C /min). Table 2 states the lower and higher values of the numerical factors. The total number of runs amounts to 22, which follows the formula N = k2 + k + r, where k is the number of factors and r is the repeated center points (k = 3 and r = 10). Analyses include factors significantly affecting the responses using the analysis of variance (ANOVA) and coefficient of determination (R2), 3D, and contour plots based on the interactions between parameters. The ANOVA results show P-values, model F-values, and lack of fit F-values. P-values less than 0.05 indicate model terms are significant, and the higher F-values implied model significance and less chance that the values could be due to noise.
Most importantly, the software suggests optimum factor conditions for specific product yields, reflecting the sensitivity of the variable factors. The R2 values (close to 1), adjusted R2, and predicted R2 values were analyzed to optimize process parameters. The difference between predicted and adjusted R2 is supposed to be less than 0.2 in well-fit models. Also, a good precision value higher than 4 reflects a desirable signal-to-noise ratio. The diagnostic tools present in the software helped ensure the model helps predict biochar yields. The following section, 3, discusses the diagnostics and validation of the model in detail.
2.4 Optimized char production and characterization
The characterization of the char produced from the optimized operating conditions for the three feeds is essential for future applications. The proximate, elemental, and calorific value analyses were conducted like feedstocks following the methodology described in Sect. 2.1. Furthermore, the surface area, zeta potential, and energy yield percentages were quantified using various instruments. The surface area was quantified using a Brunaeuer-Emmett-Teller (ET) nitrogen sorption analyzer (Tistar 3200, Micrometrics, Nocross, GA, USA). The zeta potential of the feeds was quantified using an analyzer to measure the charge of the biochar samples (Zetasizer Nano-ZS, Malvern P analytical, Malvern, UK). The methodology for the surface area and zeta potential analysis has been described in [34]. The energy yield of the biochar was quantified using Eq. 2.
2.5 Validation of prediction modeling
The validation of the developed empirical model for accurate char prediction follows two approaches.
-
(i)
Optimizing based on DesignExpert suggested experimental conditions; predicting char yields from single biomasses of this study and the literature.
-
(ii)
The level of accuracy based on further experiments and models for single, binary, and ternary co-pyrolysis. The experiments are conducted at 350, 450, 550, and 650 °C, at 10 K/min, and inert nitrogen conditions mentioned in Sect. 2.2. The char yields from this study are compared to experimental analysis using TF and TGA; and predictive model (PM) based on a published empirical model [18, 20, 35] following Eq. 3 where the temperature is in °C.
$$\text{Char yield }(\mathrm{\%})=0.106+2.43*\mathrm{exp}(-0.66*\mathrm{T}*{10}^{-2})$$(3)
3 Results and discussion
3.1 Biomass characterization and design parameters
The studied biomasses have different characteristics, as reported in the previous publication by the authors [32]. The main differences arise from the percentage of volatiles in the feeds (CM < DS < SCG) and ash content (DS < SCG < CM). The moisture and volatile contents were higher in SCG than in the other samples. The critical component of interest in this study, the fixed carbon, was 21.68, 17.98, and 13.81% for DS, CM, and SCG, respectively. The values are considered for the experiment design in this study; the lowest and highest values of the fixed carbon (A) range between 14 and 22%. However, the binary and ternary mixtures are considered for validation purposes. In addition to the proximate and ultimate analysis reported in the authors’ previous publication (refer to Table 1), the calorific value and biomass composition of the single feeds are reported in Table 2. The calorific value is highest for CM, followed by SCG and DS. The main biomass component, hemicellulose, was the highest in composition for DS and SCG; however, in the case of CM, lignin was the highest. Each component was less than 30% of the total constituent, thereby reflecting a varied composition in all feeds. Also, CM and SCG have the least and highest extractives, respectively.
3.2 Effect of study parameters
As mentioned in the methodology, the study parameters include feed composition (fixed carbon) and pyrolysis operating conditions (reaction temperature and heating rate). Table 3 shows the studied factors and results from the experiments. The three factors fixed carbon, reaction temperature, and heating rate have lower and higher value inputs ranging from 14 to 22%, 350–550 °C, and 5–10 °C/min, respectively. The fixed carbon ranges were chosen due to a previously published article by the authors [32]; the temperature and heating rate ranges are typically known to be the best for biochar production [36, 37]. The biochar yield ranged between 23 and 54%, with the lowest for DS at 750 °C and 7.5 °C/min and the highest for CM when 350 °C and 5 °C/min. The studies show the char yields are higher with lower temperatures, as expected [38,39,40,41]. Low pyrolysis temperatures yield higher biochar due to primary forward reactions and the lack of heavy compound breakdown [42]. Furthermore, the minimum and maximum biochar yields were 37.27 and 38.02% when the biochar yields increased from 5 to 10 °C /min (A = 18 and B = 550). This finding is consistent with heating rates ranging from 1 to 20 °C/min [39] but inconsistent with results in the range of 30–50 °C/min [43] and 5–50 °C/min [44]. Therefore, the significant effects of biochar require high heating rates, generating fast pyrolysis products. Furthermore, the biochar yields increased with fixed carbon and reduced slightly (34.90 at 14 A to 29.90% and 22 A when B = 550, C = 7.5). The char yield trends concerning the fixed carbon content are like the calorific values—the highest and lowest values are found in CM and DS, respectively. Additionally, as seen in Table 2, the hemicellulose, cellulose, and lignin contents are highest for CM, which is also reflected by the highest char yields [45]. Furthermore, the statistical significance of the model, factors, and other terms are discussed in Sect. 3.3.
3.3 Statistical significance of RSM results and diagnostics
Table 4 shows the ANOVA results based on the RSM study produced by Design Expert. The P-value for the quadratic model is significant (< 0.0001), which shows that the results are significant, and the model is excellent for predicting the response (char yield percentage). Furthermore, the model F-value of 21.63 implies the model is significant since there is only a 0.01% chance that an F-value this large could occur due to noise. In this case, A, B, A2, B2, C2, and BC are significant model terms (note: A is fixed carbon; B is temperature; C is heating rate). Therefore, the hypothesis of this study—the significant effect of fixed carbon on biochar yields—is confirmed. Values greater than 0.1000 indicate the model terms are not significant. The insignificant terms have P-values of 0.7424 (C) and 0.6429 (AB and AC). The statistical insignificance reflects a lack of interaction between fixed carbon has no relation to temperature and heating rate, but temperature and heating rate have a significant relationship. Most importantly, the heating rate does not have significance in the model (P-value = 0.7424).
Additionally, the lack-of-fit F-value of 0.83 and P-value of 51.23% show insignificance and therefore reflect an excellent model. More importantly, the statistical fitting shows the R2 value of 0.9419—which is excellent for a regression model fit. Also, the difference between the predicted R2 (0.7433) and adjusted R2 (0.8984) is less than 0.2, which shows the model can predict the response accurately. The adequate precision value of 15.579 shows that it is higher than 4 and, therefore, offers an adequate signal-to-noise ratio. The mean biochar yield was 39.18%, with significant char production using the waste biomass feeds and studied conditions. The standard deviation in biochar yield was ± 3.15, which is acceptable, while the coefficient of variation (CV %) in biochar yield was 8.05%, below the acceptable level of 10%, reflecting a good model. The descriptive statistics of the model, factors’ sum of the squares, and mean square values are shown in Table 4.
Considering the positive note of the prediction model from the statistics, the Design Expert Software gives other diagnostic tools based on the experimental data and model for further analysis. The four major diagnostic tools are discussed here—the normal plot of residuals, residuals versus predicted, residuals versus the run, and Box-Cox plot for power transformations. The graphs help understand if there are any outliers in the experimental results (Fig. 2). The normal plot of residuals is roughly a straight line, which shows the model’s good quality in predicting the responses. Since the R2 value is 0.9419, 94% of the data points were around the fitted regression line, with only 6% of residues. Both the residual versus predicted and residual versus run plots show constant variants with no specific trends and no outliers (no points above the red line). The Box-Cox plot is based on the normal probability plot and computed correlation coefficient. The plot recommended no need for transformation of the model required to normalize the data, confirming the normality assumption for this experiment.
3.4 Optimization of biochar yield: an empirical model for prediction and perturbation
Figure 3a shows the correlation between the predicted and actual biochar yields, and the linearity shows the model is useful for predicting the yields efficiently. Also, Fig. 3b shows the perturbation curve for the biochar yield under the pyrolysis conditions of this study (A, B, and C). The slope of the curve shows the sensitivity of the response (biochar yield) due to the factors. Since the slope is greatest for B, the temperature is the most sensitive factor. The sensitivity follows B > C > A, with the least sensitive of the factors being the fixed carbon.
The RSM was used to analyze the link between biochar yield, feeds fixed carbon content, reaction temperature, and heating rate. The best-fitting model was found to be a quadratic model. Equation 3 is the empirical model equation. The + sign in the equation denotes the positive effects of variables, and the negative effects are indicated by the − sign in the equation. While the fixed carbon (A) and temperature (B) had adverse effects on the yield, the heating rate (°C) had a positive effect on the yield. Furthermore, the interaction of fixed carbon with temperature and heating rate was equally positive, and temperature and heating rate were more positive. The second-order terms A2 and C2 posed unfavorable effects, while B2 was favorable.
Figure 4 shows the 3D RSM plots and the contour plots of the different factors on the biochar yields. The plots showing the effect of biochar yield due to fixed carbon and temperature when the heating rate is 7.5 is shown in Fig. 4a and b. An increase in both parameters reduced the char yields. Figure 4c and d show the yield effect due to heating rate and temperature when the fixed carbon is 18 (CM). The reduced temperature was a significant effect in increasing yield in the range of studied heating rates. The significance of the heating rate on the char yield is probably not reflected in this study due to the range being so small (5–10 K/min). The statistical analysis shows that the fixed carbon and heating rate interaction is insignificant. Additionally, Fig. 3e and f show the interactions on the biochar yields at 550 °C, and the maximum yield is when the fixed carbon is 18, and the heating rate is 7.5. Lower and higher than these points, the yields decrease.
3.5 Characterization and validation of biochar yields
The optimization was based on specific fixed carbon targets (A = 22, 18, and 14) but with temperature and heating rate in the range. For the 22, 18, and 14, the optimized solutions have the desirability of 0.940, 1.00, and 0.983. The conditions and the results are mentioned in Table 5. The results show that the optimized biochar yields are in the suggested confidence intervals and percentage error. Table 5 also reports the characterization of the optimized biochar yields. While the highest and lowest biochar yields were observed in CM and DS, respectively, the energy yield was highest and lowest for SCG and DS. The moisture, volatiles, hydrogen, and nitrogen contents were reduced when the feeds were pyrolyzed compared to the feeds. However, the ash, carbon, and oxygen content varied when pyrolyzed. The fixed carbon content increased considerably after pyrolysis and was the major component of the biochar (80.61–91.5%) (ultimate analysis). Due to the high ash content, the fixed carbon content was lowest for CM biochar. Furthermore, the surface area and pore volume ranged from 2.100–4.230 m2/g to 0.03–0.10 cm3/g, respectively, in typical biochar value ranges [46]. The negative zeta potential reflects the potential for removal of positively charged pollutants, therefore, its applicability as an adsorbent [34].
Furthermore, the point prediction tool on Design Expert suggests conditions for biochar yield predictions using the developed model using further experimentation (Table 6). The literature data for Prosopis juliflora, rice straw, and water buffalo manure (within the range of the studied operating parameters) were considered for validation. The results were 95% confidence in prediction intervals, with yields predictions with less than 18.52% error. Furthermore, the experiments based on the feeds in this study were undertaken based on the point prediction values. Compared to the predicted mean value noted in Table 6, the results show that the model helps predict the biochar yields well with minimal error (≤ 5.43%). However, the comparison shows more variation regarding other feeds; further analysis needs to be conducted to reduce the difference in prediction and actual yields.
The second approach of validation is to check the accuracy of the developed empirical model (Eq. 3) against two experimental study results and one published prediction model. Figure 5 and the RSM study show that char yields decrease with increasing temperatures (Table 3)[50, 51]. The yields at the lowest studied temperature increase in the following order CM (51%) > SCG (40%) > DS (38%). When the feeds are mixed, the yields are higher than DS and SCG and less than the CM. Combining DS and SCG has also increased char yields compared to individual pyrolysis (50% for binary versus 38 and 40%). Furthermore, the ternary biomass yielded 47%, closer than CM, then DS, or SCG. The yields decrease with temperature the most for DS: SCG and SCG, with a difference of 21 and 17%, respectively, from the yields at 350–650 °C. Although CM produced the highest char at all temperatures, SCG produced lower chars than DS at temperatures other than the lowest. This difference is due to SCG’s higher volatile content than DS (Table 1). The TF analysis of the binary and ternary feeds shows higher yields when mixing DS and SCG. When CM is mixed with the other feeds, the yields are lower than CM but higher than the others.
Furthermore, TGA was chosen as an experimental analysis due to its quick analysis time using small quantities of feeds (≤ 10 mg) and has been previously employed to study the char yields from food waste vegetable mixtures [52] and sewage sludge and microalgae mixtures [53]. If accurate results are retrieved from the study, it could prove to be a valuable and efficient way to analyze char yields. Our analysis has shown that the yields have been over and under the expected values compared to TF. Especially in the case of SCG, the yields were over 9% high at all temperatures. The maximum difference was observed for the CM when yields of under 15, 14, and 13% were found at 450, 550, and 650 °C. However, the difference in yields significantly reduced for the binary and ternary feeds; the highest and lowest differences were seen for DS:SCG (− 9%) and SCG:CM (+ 1%), DS:CM (+ 1%) at 650 °C. The significant difference in yields, especially in the case of SCG, shows that TGA is not a viable option to quantify char yields accurately. Rather, prediction models could be a helpful complementary tool to do so.
The published empirical model has often been utilized to quantify chars; however, our comparative study shows that the difference from TF char was the highest in most cases. The predicted values are lower than experimental values and range from − 6% at 350 °C for DS to − 17% at 350 and 450 °C for DS:SCG. The empirical prediction model (RSM) showed an excellent prediction of char yields. This section further confirms the validity of prediction char yield for binary and ternary wastes. The model accurately predicted with ≤ 2% difference of char yields for 16 out of the 28 studied conditions. The highest difference in predicted values was when DS and SCG were mixed (+ 7%) at 650 °C. The synergistic effects when mixing these two feeds have been the most significant (as seen in TF and TGA studies), therefore proving to be more difficult to predict.
In summary, adding CM improved char yields significantly in the binary and ternary feeds. The best temperature for char yield (among the four studied) was 350 °C. The absolute difference with the experimental TF yields for most feeds increases in the order of PM > TGA > RSM. However, in the case of CM and SCG (at all temperatures), it follows TGA > PM > RSM; and at 650 °C, SCG:CM and DS:CM, follow PM > RSM > TGA. Therefore, this study’s empirical model (RSM) is the best methodology to quantify char yields. The model should be validated for other feeds with varying fixed carbon contents and against pilot-scale studies.
4 Conclusion
This study aimed to develop a prediction model for biochar yield based on feed and operating parameters by studying three different biomasses—date stones (DS), spent coffee grounds (SCG), and cow manure (CM). The response surface methodology (RSM), a regression-based statistical technique, was used to study the relationship feedstock fixed carbon, reaction temperature, and heating rate for biochar yields, driven by the main hypothesis that fixed carbon significantly affects biochar yields. The system parameters are optimized based on the Box-Behnken method, and the proposed model was quadratic (R2 = 0.9401), with fixed carbon (P < 0.0446) and temperature (P < 0.0001) being significant factors. The empirical equation suggested the fixed carbon (A) and temperature (B) had adverse effects on the biochar yield, and the heating rate (C) had a positive effect on the yield. The model was validated by running experiments for optimized conditions, point predictions, and comparison with experimental and another prediction model. This study has developed an accurate predictive model for biochar yields (for single, binary, and ternary feeds). Since fixed carbon analysis of the feed is often conducted in thermochemical conversion studies of wastes, the developed quadratic model can easily be employed to quantify biochar yields via pyrolysis. The model can be further utilized to study the techno-economic feasibility of co-pyrolysis processes by utilizing the developed empirical model in process flow software such as Aspen Plus. Finally, researchers interested in upscaling biochar for various applications (carbon sequestration, activated carbons, and adsorption) can produce high-yield chars using the developed prediction model. This study aims to significantly minimize the time and energy required to produce enough biochar.
Data availability
Data available on request.
References
Tayibi S, Monlau F, Bargaz A et al (2021) Synergy of anaerobic digestion and pyrolysis processes for sustainable waste management: a critical review and future perspectives. Renew Sustain Energy Rev 152:111603. https://doi.org/10.1016/j.rser.2021.111603
Foong SY, Liew RK, Lee CL et al (2022) Strategic hazard mitigation of waste furniture boards via pyrolysis: pyrolysis behavior, mechanisms, and value-added products. J Hazard Mater 421:126774. https://doi.org/10.1016/j.jhazmat.2021.126774
Engamba Esso SB, Xiong Z, Chaiwat W et al (2022) Review on synergistic effects during co-pyrolysis of biomass and plastic waste: significance of operating conditions and interaction mechanism. Biomass Bioenergy 159:106415. https://doi.org/10.1016/j.biombioe.2022.106415
Mariyam S, Shahbaz M, Al-Ansari T et al (2022) A critical review on co-gasification and co-pyrolysis for gas production. Renew Sustain Energy Rev 161:112349. https://doi.org/10.1016/j.rser.2022.112349
Gao N, Humphrey Milandile M, Tariq Sipra A et al (2022) Co-pyrolysis of municipal solid waste (MSW) and biomass with Co/sludge fly ash catalyst. Fuel 322:124127. https://doi.org/10.1016/j.fuel.2022.124127
Suriapparao DV, Tejasvi R (2022) A review on role of process parameters on pyrolysis of biomass and plastics: present scope and future opportunities in conventional and microwave-assisted pyrolysis technologies. Process Saf Environ Prot 162:435–462. https://doi.org/10.1016/j.psep.2022.04.024
del Pozo C, Rego F, Yang Y, et al. (2021) Converting coffee silverskin to value-added products by a slow pyrolysis-based biorefinery process. Fuel Process Technol 214:. https://doi.org/10.1016/j.fuproc.2020.106708
Al-Rumaihi A, Shahbaz M, Mckay G et al (2022) A review of pyrolysis technologies and feedstock: a blending approach for plastic and biomass towards optimum biochar yield. Renew Sustain Energy Rev 167:112715. https://doi.org/10.1016/j.rser.2022.112715
Shanmugam V, Sreenivasan SN, Mensah RA et al (2022) A review on combustion and mechanical behaviour of pyrolysis biochar. Mater Today Commun 31:. https://doi.org/10.1016/j.mtcomm.2022.103629
Reddy BR, Sridevi V, Kumar TH et al (2022) Synthesis of renewable carbon biorefinery products from susceptor enhanced microwave-assisted pyrolysis of agro-residual waste: a review. Process Saf Environ Prot 164:354–372. https://doi.org/10.1016/j.psep.2022.06.027
Saravanan A, Kumar PS (2022) Biochar derived carbonaceous material for various environmental applications : systematic review. Environ Res 214:113857. https://doi.org/10.1016/j.envres.2022.113857
Yogalakshmi KN, Poornima Devi T, Sivashanmugam P et al (2022) Lignocellulosic biomass-based pyrolysis: a comprehensive review. Chemosphere 286:131824. https://doi.org/10.1016/j.chemosphere.2021.131824
Alabdrabalnabi A (2021) Utilization of machine learning to predict bio-oil and biochar yields from copyrolysis of biomass with waste polymers. Fuel 328:125303. https://doi.org/10.1016/j.fuel.2022.125303
Al-Mrayat T, Al-Hamaiedeh H, El-Hasan T et al (2022) Pyrolysis of domestic sewage sludge: influence of operational conditions on the product yields using factorial design. Heliyon 8:e09418. https://doi.org/10.1016/j.heliyon.2022.e09418
Pinto F, Paradela F, Gulyurtlu I, Ramos AM (2013) Prediction of liquid yields from the pyrolysis of waste mixtures using response surface methodology. Fuel Process Technol 116:271–283. https://doi.org/10.1016/j.fuproc.2013.07.012
Song J, Tang C, Yu S et al (2022) Prediction of product yields using fusion model from co-pyrolysis of biomass and coal. Bioresour Technol 353:127132. https://doi.org/10.1016/j.biortech.2022.127132
Yang K, Wu K, Zhang H (2022) Machine learning prediction of the yield and oxygen content of bio-oil via biomass characteristics and pyrolysis conditions. Energy 254:124320. https://doi.org/10.1016/j.energy.2022.124320
Neves D, Thunman H, Matos A et al (2011) Characterization and prediction of biomass pyrolysis products. Prog Energy Combust Sci 37:611–630. https://doi.org/10.1016/j.pecs.2011.01.001
Song B (2016) Biomass pyrolysis for biochar production: kinetics, energetics and economics. Biochar 227
Swagathnath G, Rangabhashiyam S, Parthsarathi K et al (2019) Modeling biochar yield and syngas production during the pyrolysis of agro-residues BT - Green Buildings and Sustainable Engineering. In: Pillai RG, Tharian MG, Majeed AZ (eds) Drück H. Springer Singapore, Singapore, pp 325–336
Demirbaş A (2003) Relationships between lignin contents and fixed carbon contents of biomass samples. Energy Convers Manag 44:1481–1486. https://doi.org/10.1016/S0196-8904(02)00168-1
Gul E, Al BkoorAlrawashdeh K, Masek O et al (2021) Production and use of biochar from lignin and lignin-rich residues (such as digestate and olive stones) for wastewater treatment. J Anal Appl Pyrolysis 158:105263. https://doi.org/10.1016/j.jaap.2021.105263
Raheem A, Ding L, He Q et al (2022) Effective pretreatment of corn straw biomass using hydrothermal carbonization for co-gasification with coal: response surface methodology–Box Behnken design. Fuel 324:. https://doi.org/10.1016/j.fuel.2022.124544
Ferreira SLC, Bruns RE, Ferreira HS et al (2007) Box-Behnken design: an alternative for the optimization of analytical methods. Anal Chim Acta 597:179–186. https://doi.org/10.1016/j.aca.2007.07.011
Muthukumar M, Mohan D, Rajendran M (2003) Optimization of mix proportions of mineral aggregates using Box Behnken design of experiments. Cem Concr Compos 25:751–758. https://doi.org/10.1016/S0958-9465(02)00116-6
Yiga VA, Lubwama M, Pagel S et al (2021) Optimization of tensile strength of PLA/clay/rice husk composites using Box-Behnken design. Biomass Convers Biorefinery. https://doi.org/10.1007/s13399-021-01971-3
Gupta S, Patel P, Mondal P (2022) Biofuels production from pine needles via pyrolysis: process parameters modeling and optimization through combined RSM and ANN based approach. Fuel 310:122230. https://doi.org/10.1016/j.fuel.2021.122230
Zhou R, Zhang M, Zhou J, Wang J (2019) Optimization of biochar preparation from the stem of Eichhornia crassipes using response surface methodology on adsorption of Cd2+. Sci Rep 9:1–17. https://doi.org/10.1038/s41598-019-54105-1
Magalhães D, Gürel K, Matsakas L et al (2021) Prediction of yields and composition of char from fast pyrolysis of commercial lignocellulosic materials, organosolv fractionated and torrefied olive stones. Fuel 289:. https://doi.org/10.1016/j.fuel.2020.119862
Huang Z, Manzo M, Xia C et al (2022) Effects of waste-based pyrolysis as heating source: meta-analyze of char yield and machine learning analysis. Fuel 318:123578. https://doi.org/10.1016/j.fuel.2022.123578
Kim SW (2015) Prediction of product distribution in fine biomass pyrolysis in fluidized beds based on proximate analysis. Bioresour Technol 175:275–283. https://doi.org/10.1016/j.biortech.2014.10.107
Mariyam S, Alherbawi M, Rashid N et al (2022) Bio-oil production from multi-waste biomass co-pyrolysis using analytical Py–GC/MS. Energies 15:. https://doi.org/10.3390/en15197409
Mansor AM, Lim JS, Ani FN et al (2019) Characteristics of cellulose, hemicellulose and lignin of MD2 pineapple biomass. Chem Eng Trans 72:79–84. https://doi.org/10.3303/CET1972014
Zuhara S, Pradhan S, Pasha M, McKay G (2022) Potential of GTL-derived biosolids for water treatment: fractionization, leachate, and environmental risk analysis. Water 14
Song B (2016) Biomass pyrolysis for biochar production: kinetics, energetics and economics. In: Biochar. Cambridge University Press
Zuhara S, Mackey HR, Al-Ansari T, McKay G (2022) A review of prospects and current scenarios of biomass co-pyrolysis for water treatment. Biomass Convers Biorefinery. https://doi.org/10.1007/s13399-022-03011-0
Lia C, Hayashib J-I, Sun Y et al (2021) Impact of heating rates on the evolution of function groups of the biochar from lignin pyrolysis. J Anal Appl Pyrolysis 155:105031. https://doi.org/10.1016/j.jaap.2021.105031
Yang X, Kang K, Qiu L et al (2020) Effects of carbonization conditions on the yield and fixed carbon content of biochar from pruned apple tree branches. Renew Energy 146:1691–1699. https://doi.org/10.1016/j.renene.2019.07.148
Zhao B, O’Connor D, Zhang J et al (2018) Effect of pyrolysis temperature, heating rate, and residence time on rapeseed stem derived biochar. J Clean Prod 174:977–987. https://doi.org/10.1016/j.jclepro.2017.11.013
Abbas Q, Liu G, Yousaf B et al (2018) Contrasting effects of operating conditions and biomass particle size on bulk characteristics and surface chemistry of rice husk derived-biochars. J Anal Appl Pyrolysis 134:281–292. https://doi.org/10.1016/j.jaap.2018.06.018
Qin L, Wu Y, Hou Z, Jiang E (2020) Influence of biomass components, temperature and pressure on the pyrolysis behavior and biochar properties of pine nut shells. Bioresour Technol 313:123682. https://doi.org/10.1016/j.biortech.2020.123682
Ahmad J, Patuzzi F, Rashid U et al (2021) Exploring untapped effect of process conditions on biochar characteristics and applications. Environ Technol Innov 21:101310. https://doi.org/10.1016/j.eti.2020.101310
Vieira FR, Romero Luna CM, Arce GLAF, Ávila I (2020) Optimization of slow pyrolysis process parameters using a fixed bed reactor for biochar yield from rice husk. Biomass and Bioenergy 132:. https://doi.org/10.1016/j.biombioe.2019.105412
Koçer AT, Mutlu B, Özçimen D (2020) Investigation of biochar production potential and pyrolysis kinetics characteristics of microalgal biomass. Biomass Convers Biorefinery 10:85–94. https://doi.org/10.1007/s13399-019-00411-7
Chen D, Cen K, Zhuang X et al (2022) Insight into biomass pyrolysis mechanism based on cellulose, hemicellulose, and lignin: evolution of volatiles and kinetics, elucidation of reaction pathways, and characterization of gas, biochar and bio‐oil. Combust Flame 242:. https://doi.org/10.1016/j.combustflame.2022.112142
Leng L, Xiong Q, Yang L et al (2021) An overview on engineering the surface area and porosity of biochar. Sci Total Environ 763:144204. https://doi.org/10.1016/j.scitotenv.2020.144204
Baghel P, Sakhiya AK, Kaushal P (2022) Influence of temperature on slow pyrolysis of Prosopis Juliflora: an experimental and thermodynamic approach. Renew Energy 185:538–551. https://doi.org/10.1016/j.renene.2021.12.053
Wang T, Meng D, Zhu J, Chen X (2020) Effects of pelletizing conditions on the structure of rice straw-pellet pyrolysis char. Fuel 264:116909. https://doi.org/10.1016/j.fuel.2019.116909
Özbay G, Koçak E, Ahmad MS (2021) Pyrolysis of water buffalo manure: influence of temperature and alkali hydroxide additives on the quality of bio-oil. Biocatal Agric Biotechnol 38:102230. https://doi.org/10.1016/j.bcab.2021.102230
Patra BR, Mukherjee A, Nanda S, Dalai AK (2021) Biochar production, activation and adsorptive applications: a review. Environ Chem Lett 19:2237–2259. https://doi.org/10.1007/s10311-020-01165-9
Hassan M, Liu Y, Naidu R et al (2020) Influences of feedstock sources and pyrolysis temperature on the properties of biochar and functionality as adsorbents: a meta-analysis. Sci Total Environ 744:140714. https://doi.org/10.1016/j.scitotenv.2020.140714
Elkhalifa S, Parthasarathy P, Mackey HR et al (2022) Biochar development from thermal TGA studies of individual food waste vegetables and their blended systems. Biomass Convers Biorefinery. https://doi.org/10.1007/s13399-022-02441-0
Bolognesi S, Bernardi G, Callegari A et al (2021) Biochar production from sewage sludge and microalgae mixtures: properties, sustainability and possible role in circular economy. Biomass Convers Biorefinery 11:289–299. https://doi.org/10.1007/s13399-019-00572-5
Funding
Open Access funding provided by the Qatar National Library. The authors thank Qatar National Research Fund for supporting this research under the National Priorities Research Program Award Number NPRP11S-0117–180328. Any opinions, findings, conclusions, or recommendations expressed in this material are those of the authors. They do not necessarily reflect the views of Hamad Bin Khalifa University or the Qatar Foundation.
Author information
Authors and Affiliations
Contributions
Sabah Mariyam: conceptualization, methodology, formal analysis, writing—original draft. Mohammad Alherbawi: conceptualization, review, and editing. Snigdhendubala Pradhan: methodology, formal analysis. Tareq Al-Ansari: reviewing and editing. Gordon McKay: supervision, reviewing, and editing,
Corresponding author
Ethics declarations
Ethics approval
Not applicable.
Conflict of interest
The authors declare no competing interests.
Additional information
Publisher's note
Springer Nature remains neutral with regard to jurisdictional claims in published maps and institutional affiliations.
Rights and permissions
Open Access This article is licensed under a Creative Commons Attribution 4.0 International License, which permits use, sharing, adaptation, distribution and reproduction in any medium or format, as long as you give appropriate credit to the original author(s) and the source, provide a link to the Creative Commons licence, and indicate if changes were made. The images or other third party material in this article are included in the article's Creative Commons licence, unless indicated otherwise in a credit line to the material. If material is not included in the article's Creative Commons licence and your intended use is not permitted by statutory regulation or exceeds the permitted use, you will need to obtain permission directly from the copyright holder. To view a copy of this licence, visit http://creativecommons.org/licenses/by/4.0/.
About this article
Cite this article
Mariyam, S., Alherbawi, M., Pradhan, S. et al. Biochar yield prediction using response surface methodology: effect of fixed carbon and pyrolysis operating conditions. Biomass Conv. Bioref. (2023). https://doi.org/10.1007/s13399-023-03825-6
Received:
Revised:
Accepted:
Published:
DOI: https://doi.org/10.1007/s13399-023-03825-6