Abstract
Purge flow is of great importance in cooling turbine disks and sealing rotor-stator disc cavity to reduce hot gas ingestion in gas turbines. The amount of cooling air extracted from the compressor is crucial to engine efficiency. Excessive sealing air will cause not only a reduction in work transfer but also an increase in aerodynamic losses caused by the mixing of main and sealing flow. In order to simplify rim seal structure while ensuring high sealing efficiency, the current paper optimizes the flow path of the secondary air system and presents a new rim seal structure with auxiliary sealing holes transporting a certain amount of secondary sealing flow. The new structure was compared with the conventional counterpart using validated CFD methods, showing that the additional secondary sealing flow is possible to improve sealing efficiency in disk cavity. The current paper investigates the secondary sealing flow with and without swirl (the angle of auxiliary sealing hole inclination is 0° and 45° respectively), while maintaining the total amount of the sealing flow, flowrate ratio of sealing air (main sealing flow rate versus secondary sealing flow rate=1:1, 2:1, 3:1, 4:1), found that both two parameters have essential impacts on sealing efficiency. The relationship between these two parameters and sealing efficiency was obtained, and it provides a new philosophy for the design of rim seal in gas turbines.
Similar content being viewed by others
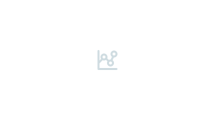
References
Scobie J.A., Sangan C.M., Owen J.M., Lock G.D., Review of ingress in gas turbines. Journal of Engineering for Gas Turbines and Power, 2016, 138(12): 120801.
Sangan C.M., Measurement of ingress through gas turbine rim seals. University of Bath, Bath, United Kingdom, 2011.
Sangan C.M., Scobie J.A., Owen J.M., Lock G.D., Tham K.M., Laurello V.P., Performance of a finned turbine rim seal. Journal of Turbomachinery, 2014, 136(11): 111008.
Scobie J.A., Teuber R., Li Y.S., Sangan C.M., Wilson M., Lock G.D., Design of an improved turbine rim-seal. Journal of Engineering for Gas Turbines and Power, 2016, 138(2): 022503.
Li J., Gao Q., Li Z., Feng Z., Numerical investigations on the sealing effectiveness of turbine honeycomb radial rim seal. Journal of Engineering for Gas Turbines and Power, 2016, 138(10): 102601.
Clark K., Barringer M., Thole K., Clum C., Hiester P., Memory C., Robak C., Using a tracer gas to quantify sealing effectiveness for engine realistic rim seals. In ASME Turbo Expo 2016: Turbomachinery Technical Conference and Exposition, American Society of Mechanical Engineers, June 2016, Seoul, South Korea, Paper No.: GT2016-58095, V05AT15A034.
Clark K., Barringer M., Thole K., Clum C., Hiester P., Memory C., Robak C., Effects of purge jet momentum on sealing effectiveness. Journal of Engineering for Gas Turbines and Power, 2017, 139(3): 031904.
Patinios M., Ong I.L., Scobie J.A., Lock G.D., Sangan C.M., Influence of leakage flows on hot gas ingress. Journal of Engineering for Gas Turbines and Power, 2019, 141(2): 021010. Paper No.: GTP-18-1403.
Clark K., Barringer M., Johnson D., Thole K., Grover E., Robak C., Effects of purge flow configuration on sealing effectiveness in a rotor-stator cavity. Journal of Engineering for Gas Turbines and Power, 2018, 140(11): 112502.
Durocher E., Synnott R., Blais D., Pratt and Whitney Canada Corp, Airfoil platform impingement cooling. U.S. Patent 7,452,184. 2008.
Wu K., Research on the mechanism of sealing and ingestion in gas turbine rotor-stator rim. Tsinghua University, Beijing, China, 2014. (in Chinese)
Cheng S., Li Z., Li J., Investigations on the sealing effectiveness and unsteady flow field of 1.5-stage turbine rim seal. Journal of Engineering for Gas Turbines and Power, 2019, 141(8): 081003.
Boutet-Blais G., Lefrancois J., Dumas G., Julien S., Harvey J.F., Marini R., Caron J.F., Passive tracer validity for cooling effectiveness through flow computation in a turbine rim seal environment. In ASME 2011 Turbo Expo: Turbine Technical Conference and Exposition, American Society of Mechanical Engineers Digital Collection, June 2011, Vancouver, British Columbia, Canada, Paper No.: GT2011-45654, pp. 821–831.
Zhou K.Y., Hot gas ingestion mechanism in gas turbines. Beihang University, Beijing, China, 2011.
Acknowledgement
Thanks are given to the National Natural Science Foundation of China for their financial support (Grant No.51776200). The Innovation Promotion Association, Chinese Academy of Sciences is also thanked for the support and help.
Author information
Authors and Affiliations
Corresponding authors
Rights and permissions
About this article
Cite this article
Wang, R., Du, Q., Liu, G. et al. Influence of Secondary Sealing Flow on Performance of Turbine Axial Rim Seals. J. Therm. Sci. 29, 840–851 (2020). https://doi.org/10.1007/s11630-020-1317-z
Received:
Published:
Issue Date:
DOI: https://doi.org/10.1007/s11630-020-1317-z