Abstract
The sustainable development of the paint and varnish industry is a prerequisite for action to minimize the negative environmental impact of paint products. They consist not only in reducing the emission of harmful VOC substances into the atmosphere but also in modifying the composition of the paint material in order to improve the properties of the coatings and at the same time reduce the amount of waste. Selection of the appropriate composition of the water-borne composition is still a problem to be solved. Therefore, aqueous polymer dispersions of Arlberdingk AC 2514 containing an acrylic resin modified with an ionic liquid of didecyldimethylammonium nitrate (DDANO3) were tested. Non-ionic surfactants (Rokanol L-10 and Rokacet S-24), polyurethane thickener (DSX 1514), and mineral thickener (bentonite) were also used for stabilization. The influence of individual components on changes in the stability and particle size of dispersion systems was investigated. Physicomechanical tests of coatings obtained from polymer dispersion systems were also performed. Studies have shown that with the increase in the amount of DDANO3 in the system, the particle size of the varnish composition decreases and the gloss and relative hardness of the coatings decrease. The optimal amount of DDANO3 in the dispersion is 1.5% w/w. DSX 1514 increased the stability, reduced the migration rate of the dispersion particles, and improved the elasticity and impact resistance of the protective membranes. It has been shown that the stability varies depending on the type of thickener and surfactant (SAA) used. SAA increases the value of the TSI (Turbiscan Stability Index), which takes the values of 3.8 (0.3 g bentonite) and 3.6 (0.6 g bentonite), respectively, with Rokanol L-10 16% w/w. Water-soluble acrylic resin with the tested additives can be potentially used for the production of stable dispersions with extended life.
Similar content being viewed by others
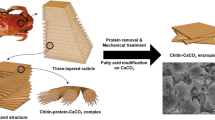
Avoid common mistakes on your manuscript.
Introduction
In recent years, the paint and varnish industry has significantly reduced the emission of volatile organic compounds (VOCs) into the atmosphere. This has been helped by existing legislation and the increasing awareness of consumers about health and environmental risks. The ecological alternative to solvent-based coatings has become dispersive hydroaqueous polymers (Yanbin et al. 2022; Geurts et al. 2008). Among many water systems, acrylic dispersions are widely available and popular systems that meet different end-user requirements. They have low VOC content, fast curing rates, and a good decorative effect. Therefore, they are widely used in the field of anti-corrosive metal coatings, in architectural coatings, or in wood painting (Elrebii et al. 2014; Yan et al. 2022; Jiao et al. 2020). However, due to a number of defects in acrylic resin such as poor water resistance and low solids, it requires further development toward high efficiency and multi-functionality. For this purpose, resin modification agents are used (Jiao et al. 2021). As auxiliary substances are used, inter alia, ionic liquids. They belong to biologically active substances and at the same time are environmentally safe. They are therefore appropriate as wood protection measures (Kędzierski et al. 2020; Xue et al. 2015). In addition, their small particle size and charged character improve the colloidal stability in aqueous and non-aqueous dispersion. This is an important aspect when selecting the composition of the painting system (Rozik et al. 2013; Saljooqi 2022). Surfactants and thickeners are also used to increase the stability of polymer dispersion (Akther et al. 2008). The nature and quantity of the surfactant used is an important indicator of the behavior of the system during polymerization, film formation, and throughout the lifetime of the coating. The surfactant used to stabilize the particles also affects the adhesion of the paint, as it better wets the surface of the substrates (Wang et al. 2017; Butler et al. 2005). To understand the relationships between the formulation and paint performance, a large number of studies of latex coatings using thickeners and surfactants have been carried (Larson et al. 2022; Bobsein et al. 2010; Souza et al. 2017).
The simultaneous selection of any auxiliary agents used to develop the composition of the polymer dispersion is very difficult. The additives introduced into aqueous acrylic dispersions significantly deteriorate the resistance to water, temperature, and mechanical properties of the system. The aim of this study was therefore to investigate the effect of the ionic liquid, thickeners, and non-ionic surfactants on the properties of the obtained coatings. The mechanical and thermomechanical resistance of the tested systems was determined, which influences the essential functional properties of the coating. The influence of additives on the stability of the polymer dispersion was presented and the morphology of the system was investigated by means of particle size analysis.
Experimental studies
Materials
To prepare water compositions, the following components were used:
-
distilled water,
-
AC 2514 water-dilutable acrylic resin with a dry weight within the range of 42–44%, viscosity 30–300 mPas, pH 7–8, MTTF = 316 K, and Köenig hardness = 105 s, produced by Alberdingk Boley,
-
ionic liquid didecyldimethylammonium nitrate (V) p. a., (DDANO3), produced at the Delta Innovation and Implementation Company in Śrem according to the method developed at the Department of Chemical Technology of the Poznań University of Technology,
-
non-ionic surfactant, ethoxylated unsaturated fatty alcohol p. a., (Rokanol L-10) ethoxy number 10, molecular weight 626.86 g/mol (producer PCC Rokita Spółka Akcyjna in Brzeg Dolny),
-
non-ionic surfactant, ethoxylated stearic acid p. a., (Rokacet S-24), ethoxylated number 24, molecular weight 1326 g/mol (producer PCC Rokita Spółka Akcyjna in Brzeg Dolny)
-
polyurethane thickener DSX 1514 by IMCD Polska Sp. zoo.
-
inorganic thickener bentonite—mineral containing 72.1 wt.% SiO2, 14.3 wt.% Al2O3, 2.2 wt.% Na2O + K2O, 2 wt.% MgO, 1.7 wt.% Fe2O3, and other compounds (Zakłady Górniczo-Metalowe Zębiec, Polska).
Measurement methods
The principle of Turbiscan LAB measurement
Turbiscan LAB was employed to quantitatively and objectively characterize the stability of dispersion system samples without destruction, avoid the interference of subjective factors, and show the cause of instability (Manca et al. 2016).
The analyzed emulsion was placed in a cylindrical measuring glass cell. The optical reading head scanned the length of the sample (55 mm) acquiring backscattering data as a function of the distance along the axis of the tube and time (transmitted light was neglected because the emulsion is opaque). Backscattered light (BS) and Turbiscan Stability Index (TSI) are used to quantify the stability of samples. The calculation method of this coefficient is as follows:
where xi (i = 1,…, N) is the mean backscattering, xm is the mean value of xi, and N is the number of scans. The smaller the TSI value, the more stable the sample. Samples were scanned first day, fourth (48 h) and after seven days (168 h) in the case of systems with bentonite.
Particle size tests
The particle size testing was performed with a Fritsch GmbH laser particle size analyzer using the “wet” method. It consisted in introducing a certain amount of sample into the device until the proper absorption of the stream was obtained. The analyzer uses two lasers during the measurement. The green laser is responsible for the measurement of very fine particles, while the infrared laser is responsible for the analysis of large particles. The prepared acrylic dispersion of 2 cm3 was introduced into the measuring cell, where it was diluted with water. The dosing time was about 10 s, and the whole measurement cycle was 2 min. The measurement range from 0.08 to 2000 µm, the pump 5, the absorption of the stream 7%. The tests were repeated three times for each trial. On the basis of the research, the curves of the particle size distribution were determined. The test results were interpreted using the notions of Volume Mean Diameter D3.0VMD and the Sauter mean diameter D3.2 SMD, which is the equivalent dimension of the particle set (Liu et al. 2017).
where n is the size of the set.
Consistency tests
The test material was introduced into the measuring cell, which was then placed in the Höppler consistometer. A load equal to 250 g was mounted on the top of the device. After making sure that the micrometer dial was set to 0, the silicone oil filling the thermostat was heated. As the temperature increased, the sample deformed, which resulted in the indenter falling. Each change was recorded by the sensor, allowing the detection of deformations on the micrometer dial to be within ± 0.01 mm. The experiment was carried out in the temperature range from 293 to 390 K.
Sample preparation
In order to prepare the aqueous polymer dispersion systems, appropriate amounts of DDANO3, Rokacet S-24 or Rokanol L-10, have been introduced into 100-cm3 acrylic dispersion and appropriate amounts of DSX 1514 or bentonite. All was dispersed for about 10 min using an IKA-ULTRA-TURRAX T25 laboratory homogenizer with an S25N-18Gz type stirrer at 1500 rpm. The compositions of selected acrylic dispersion systems are presented in Tables 1 and 2. Immediately after the dispersion was prepared and after 7 days of exposure, the surface tension was tested using a Kruss du Nouy tensiometer balance.
Coating testing methodology
The obtained compositions were applied to metal and glass substrates previously cleaned of corrosion products and degreased, and then hardened at the temperature of 353 K.
The obtained coatings were subjected to physicochemical and physicomechanical tests. The films from the dispersion containing bentonite were subjected to consistometric tests, and the coatings containing the ionic liquid applied on the glass plates were subjected to water extraction at room temperature for 24 h. Then, spectrophotometric tests of the aqueous solutions were performed with the use of the Agilent Technologies G1103A spectrophotometer.
The following properties were tested:
-
softening point of varnish films using the Höppler consistometer (Zalewska and Grubecki 2017),
-
thickness with the magnetic method according to PN-EN ISO 2808,
-
relative pendulum hardness of films on steel plates according to PN-EN ISO 1522,
-
adhesion to steel substrates—by making a grid of cuts with a Peters circular knife according to PN-EN ISO 2409,
-
scratch resistance of varnish films according to PN-EN ISO 1518,
-
gloss of coatings according to PN-EN ISO 2813.
Analysis of results and discussion
Test results for dispersion systems with ionic liquid
Particle stability and size studies
Modification of the dispersion composition changes the stability of the acrylic dispersion itself. Mixing, diluting incorrect dispersion of system components, or inadequate selection of system components also contribute to the acceleration of the coalescing process.
From a number of prepared dispersion systems with variable composition, differing in the amount of SAA, ionic liquid, and the presence of a thickener, 8 exemplary dispersions were selected. All dispersions were slightly cream colored and foamed upon homogenization. The surface tension of the tested dispersions, right after their preparation, increased with the amount of DDANO3 and ranged from 34 to 39 mN/m. In the state of sedimentation equilibrium, the surface tension slightly increased. The kinetics of instability of systems containing different amounts of ionic liquid from time are presented in Fig. 1. The change is expressed by the TSI calculated from the light signal backscattered over the whole height of the sample. Figure 2 shows the changes in TSI depending on the amount of DDANO3 in the dispersion on the first and seventh day of storage. The increase in the amount of DDANO3 in the dispersion causes an increase in TSI, which indicates changes in the stability of the samples. During the test, an increase in backscatter due to an increase in the concentration of the dispersed phase was visible in the lower part of the vial. The most unstable system was dispersion 2 and 6 containing 1% w/w ionic liquid, where the particles were associated with their sedimentation. In the remaining dispersions, it was found that the polyurethane thickener caused slight changes in TSI over time, which proves the high durability of these dispersion systems.
The particle migration rate parameter was also established for dispersion to observe the kinetics of sedimentation (Fig. 3).
The particle migration rate increases after 7 days of exposure for systems without thickening, which indicates coagulation and sedimentation. After adding a polyurethane thickener, a reduction in the rate of migration after 7 days of exposure was observed in 1.5% and 2% of DDANO3 dispersion which indicates a reduction in the coalescence and sedimentation process.
Another research task was to determine the size of the dispersion particles using a laser particle size analyzer from Fritsch GmbH. The size of the dispersion particles determines the parameters of coatings, such as gloss, water resistance, and physical and mechanical properties. It depends primarily on the type of emulsifier used, but also on the other components of the dispersion. An example of the particle size distribution of the selected dispersion system is shown in Fig. 4.
For the analyzed samples, the curves follow the Gauss distribution. The course of the curves is symmetrical. The slender shape of the graph indicates less dispersion around the mean.
To interpret the results of the particle distribution, the equivalent diameter D (3.0) volume mean diameter (VMD) was used, using the concept of the equivalent sphere and describing the dimension of a single non-spherical particle. The equivalent dimension of the particle set was determined using the Sauter D (3.2) Sauter mean diameter (SMD) see Fig. 5.
The mean equivalent particle diameter (VMD) ranges from 0.230 to 1.433 µm. It increases with the content of DDANO3 in the dispersion. The introduction of the polyurethane thickener caused the particle diameter to increase in all cases.
The Sauter particle size (SMD) also increases with increasing ionic liquid in the system. The presence of the polyurethane thickener increased the SMD value. In the case of dispersion systems 7 and 8, the size of the set of particles in the emulsion is similar and amounts to approximately 0.420 µm see Fig. 6.
The analysis of the data presented in Table 3 shows that as the amount of ionic liquid in the dispersion increases, its arithmetic mean particle size decreases from 99.33 to 84.46 µm. The standard deviation informing about the scatter of the results around the mean decreases with the increase of the amount of DDANO3. In dispersions containing also a polyurethane thickener, the particle size of the dispersion increased. However, as the amount of ionic liquid increases, their size decreases. In these dispersions, the standard deviation was approximately 40 µm see Table 3.
Physicomechanical tests of coatings
Films were made from the tested dispersions, which were subjected to physicomechanical tests. The influence of the amount of ionic liquid on the film formation process and the change of its properties was determined. Based on the tests, it was found that all coatings have very good adhesion to the substrate, amounting to 0 see Fig. 7.
Films containing DDANO3 and Rokacet S-24 in their composition have a higher value of relative hardness, which is about 0.11 to 0.20. In the case of the dispersion with the addition of a thickener, the hardness of the films was about 0.16. Only the coating with 2% w/w DDANO3 has a lower hardness of 0.14. These coatings have a gloss of 25 to 68 degrees, which decreases with the ionic liquid content in the dispersion. The addition of a DSX 1514 increased the flexibility of the coating. These films had a high impact resistance of 36 to 45 cm, which increased with higher concentrations of DDANO3.
The coatings were also subjected to cold water extraction to determine the amount of eluted ionic liquid from the film. After water extraction, the content of ionic liquid in the extraction water was examined by spectroscopy. The concentration of DDANO3 in the water after extraction was read from the determined standard curve. About 0.97% to 1.54% of the DDANO3 was found to leach from the coating. The leachability increases with the higher concentration of the ionic liquid in the dispersion. The addition of a DSX1514 to the dispersion reduced the leachability to a maximum of 0.61% for the system containing 1.5% of the DDANO3. This proves the good compatibility of the dispersion components and their binding during the coalescence and coating process.
Test results for dispersion systems with an inorganic thickener—bentonite
Stability studies
The systems containing bentonite were milky white. The value of surface tension in all tested dispersions is similar (Table 2). Slight changes in the values of individual quantities for fresh and equilibrium dispersion testify to its high stability. This phenomenon is particularly advantageous in the case of storage and warehousing of the finished product, which is therefore distinguished by an extended shelf life. In order to thoroughly investigate the stability of the obtained dispersion systems, tests were performed using TurbiscanLab. The TSI for the systems has been defined see Figs. 8 and 9.
The figures show that the addition of a surfactant increases the value of the TSI index, which has values equal to approximately 3.8 for the Rokanol L-10 content of 16% (w/w) with 0.3 g of bentonite and 3.6 for the Rokanol L-10 content of 16% (w/w) with 0.6 g of bentonite. By following the changes of the TSI index, it can be concluded that all dispersions analyzed show stability, which is confirmed by slight differences in the values of the TSI index lower than 0.4 (Manca et al. 2016). The increase in the surfactant content causes a significant increase in the TSI value. This regularity occurs regardless of the amount of thickener in the system. It should be noted that the analysis of the TSI indicator is not always sufficient to recognize the system as stable.
Comparing the BS characteristics presented in Figs. 10 and 11, respectively, for 2% Rokanol L-10 and bentonite content of 0.3 and 0.9 g, it can be concluded that in both cases, with too short exposure times, the system was less stable (curves from 1 to 8) showing higher BS values of about 50% for a content of 2% (w/w) SAA and 0.3 g of bentonite, and from about 29% to 33% for a content of 2% SAA and 0.6 g of bentonite. Scanning samples after a longer time, after 4 and 7 days, respectively, causes a change in BS characteristics, as evidenced by the reduction of BS intensity to a value from 37 to 40% for a bentonite content of 0.3 g and from 19 to 22% (curves 3–6), for a bentonite content of 0.6 g. Similar dependencies were observed for the remaining systems during the cyclic scanning of the sample.
The same course of the curves confirms the uniform distribution of particles over the entire height of the measuring cell and is a consequence of the accumulation of surfactant on the interface surface, as a result of which micelles are formed that increase the stability of the system. However, it should be observed that the addition of a thickener causes an increase in the BS intensity in the lower part of the measuring cell, which is most likely the result of emulsion delamination due to sedimentation. The decrease in BS in the upper part of the vial is associated with a decrease in concentration, followed by clarification.
Therefore, it should be noted that destabilization processes occurred in all systems, as evidenced by the formation of a small layer of sediment at the bottom of the measuring cell. However, it can be concluded from the course of the curves that the systems stabilized over time.
Consistometric studies
Consistometric tests allowed to observe the behavior of the films under the conditions of increasing temperature with constant load. The result of the measurements was the determination of the softening and flow temperatures of the tested materials (Table 4).
By analyzing the results of thermomechanical tests, it can be concluded that the addition of an inorganic thickener has a significant impact on the course of the deformation curve. In practical applications, where significant resistance of coatings to mechanical damage is required, it is necessary to optimally select individual components of the varnish composition.
The obtained curves (Figs. 12 and 13) show that all compositions tested in the temperature range from 289 to 329 K were characterized by good thermomechanical stability. When it is exceeded, the coatings clearly lose their thermomechanical stability, which is manifested by an increase in the value of deformation with temperature.
The initial stability is explained by the difficult flow of polymer segments in the films, which slows down the destruction of internal bonds and leads to an increase in its crystallinity. The described behavior of the coatings is observed only up to the temperature of approximately 329 K. This is followed by an increase in deformation, which is stabilized slightly at temperatures close to the final value of the test range (365–370 K).
It should be noted that the addition of bentonite in the amount of 0.3 and 0.6 g causes a faster increase in deformation in the lower temperature range, compared to the film without the thickener. The increase in the SAA content in the system is conducive to increasing the deformation increment. For the value of 2% in the case of 0.3 g of bentonite and 16% for 0.6 g of bentonite, its positive effect is noticeable. The course of the deformation curve for these systems is very similar to the course of the curve for the AC 2514 lacquer resin itself. The faster increase in deformation is caused by the destruction of intermolecular bonds. It is therefore noted that the amount of thickener and surfactant have a beneficial effect on the thermomechanical properties of the system.
Physicomechanical studies
An important element of the research discussed was to analyze the changes in the basic properties of the formed coatings depending on the amount of surfactant and thickener. The results of the physicomechanical tests are presented in Table 5 and shown in Figs. 14 and 15.
As the amount of densities (bentonite) in the water dispersion increases, the number of pendulum oscillation increases.
As a result, the relative hardness of the varnish coat increases, with a maximum of 0.27 with the thickener content of 0.6 g and the mass SAA content 16% in dispersion (Fig. 14).
The positive effect of the added thickener quantity is also noted in the case of the resistance of the paint coating to scratches, expressed in the size of the load on the stylus, which is an essential element of the test bench in this respect (Fig. 15).
In this case, an increase in the thickener content in the liquid composition leads to coatings, for which mechanical scratches are created on both the surface of the coating and the substrate at increasing loads. It proves the increasing scratch resistance of the formed film with the increase of the thickener content.
The adhesion of the coating was determined by the cross-cut method. In all these tests, the values of the score grid are similar to each other, so it can be concluded that the thickener content does not affect the adhesion of the formed coating, which suggests its good adhesion to the metal substrate. The same regularity is noticeable in the analysis of the gloss of the varnish coat.
Conclusions
The protective properties of varnish coatings are closely related to the content of thickener, ionic liquid, and surfactants in the system. Thickeners and DDANO3 have a positive effect on the physicomechanical properties of the coatings, such as relative hardness, impact, and scratch resistance. Within the analyzed values of the mass fraction of bentonite, it is recommended to use 0.6 g of its content, while the DDANO3 in the amount of 1.5% w/w. The obtained results are the basis for the selection of parameters for the development of a varnish composition for the creation of protective coatings as an effective protection of steel substrates.
Based on the analysis of the selection of the amount of SAA and the thickener in order to ensure dispersion stability, it was found that despite a slight increase in the TSI value along with the increase in the content of SAA and the thickener in the considered amounts, the state of the system is close to stable.
The described acrylic compositions undoubtedly improve the parameters of the painting material, while taking care of ecological aspects, being an alternative to conventional solvent-based products. The use of painting materials based on the tested compositions improves the physicomechanical properties of the obtained coatings, extends the service life of the product, and thus reduces the amount of generated waste.
Data availability
The data sets used or analyzed during the current study are available from the corresponding author upon reasonable request.
References
Akther S, Hwang J, Lee H (2008) Sedimentation characteristics of two commercial bentonites in aqueous suspensions. Clay Miner 43:449–457. https://doi.org/10.1180/claymin.2008.043.3.09
Bobsein BR, Johnson MM, Rabasco JJ, Zeszotarski C (2010) Thickener composition and method for thickening aqueous systems. US Patent 7:741-402
Butler LN, Fellows CM, Gilbert RG (2005) Effect of surfactants used for binder synthesis on the properties of latex paints. Prog Org Coat 53(2):112–1181. https://doi.org/10.1016/j.porgcoat.2005.02.001
Elrebii M, Ben Mabrouk A, Boufi S (2014) Synthesis and properties of hybrid alkyd-acrylic dispersions and their use in VOC-free waterborne coatings. Prog Org Coat 77(4):757–764. https://doi.org/10.1016/j.porgcoat.2013.12.016
Geurts J, Bouman J, Overbeek A (2008) New waterborne acrylic inders for zero VOC paints. J Coat Technol Res 5:57–63. https://doi.org/10.1007/s11998-007-9036-x
Jiao C, Shao Q, Wu M, Zheng B, Guo Z, Yi J, Zhang J, Lin J, Wu S, Dong M, Guo Z (2020) 2-(3,4-Epoxy) ethyltriethoxysilane-modified waterborne acrylic resin: preparation and property analysis. Polymer 190:122–196. https://doi.org/10.1021/acsomega.0c05593
Jiao C, Sun L, Shao Q, Song J, Hu Q, Naik N, Guo Z (2021) Advances in waterborne acrylic resins: synthesis principle, modification strategies, and their applications. ACS Omega 6(4):2443–2449. https://doi.org/10.1021/acsomega.0c05593
Kędzierski M, Wiejak A, Janiszewska J, Wiśniewska A, Grzywa-Niksińska I, Kurzepa K (2020) Efficiency of selected biocide compounds in the protection of building coatings against colonization by mold fungi, cyanobacteria and algae. Polymers 65(5):371–379. https://doi.org/10.14314/polimery.2020.5.5
Larson RG, Van Dyk AK, Chatterjee T, Ginzburg VV (2022) Associative thickeners for waterborne paints: structure, characterization, rheology, and modeling. Prog Polym Sci 129:101546. https://doi.org/10.1016/j.progpolymsci.2022.101546
Liu Z, Li B, Qi F, Cheumg SCP (2017) Populationa balance modeling of polydispersed bubbly flow in continuous costing using average bubble number density approach. Powder Technol 319:139–147. https://doi.org/10.1016/j.powtec.2017.06.034
Manca ML, Matricardi P, Cencetti C, Peris JE, Melis V, Carbone C, Escribano E, Zaru M, Fadda AM, Manconi M (2016) Int J Pharm 505:204–211. https://doi.org/10.1016/j.ijpharm.2016.04.008
Rozik N, Antonietti M, Yuan J, Tauer K (2013) Polymerized ionic liquid as stabilizer in aqueous emulsion polymerization enables a hydrophilic-hydrophobic transition during film formation. Macromol Rapid Commun 34(8):665–67125. https://doi.org/10.1002/marc.201200827
Saljooqi A (2022) Introduction to ionic liquids and their environment-friendly applications. Ionic Liquid-Based Technologies for Environmental Sustainability. 1–15. https://doi.org/10.1016/B978-0-12-824545-3.00001-5
Souza TV, Souza PRS, Pereira MR, Nunes JS, Fonseca JLC (2017) A novel approach to thickening characterization of an acrylic latex thickener. Prog Org Coat 106:1–10. https://doi.org/10.1016/j.porgcoat.2016.12.024
Wang L, Xu F, Li H et al (2017) Preparation and stability of aqueous acrylic polyol dispersions for two-component waterborne polyurethane. J Coat Technol Res 14:215–223. https://doi.org/10.1007/s11998-016-9845-x
Xue Y, Xiao H, Zhang Y (2015) Antimicrobial polymeric materials with quaternary ammonium and phosphonium salts. Int J Mol Sci 16:3626–3655
Yan Z, Wang S, Bi J et al (2022) Strengthening waterborne acrylic resin modified with trimethylolpropane triacrylate and compositing with carbon nanotubes for enhanced anticorrosion. Adv Compos Hybrid Mater 5:2116–2130. https://doi.org/10.1007/s42114-022-00554-8
Yanbin M, Yunfang G, Jingyu L et al (2022) Preparation and characterization of cross-linked waterborne acrylic/PTFE composite coating with good hydrophobicity and anticorrosion properties. Colloids and Surfaces A: Physicochemical and Engineering Aspects 65320:129872. https://doi.org/10.1016/j.colsurfa.2022.129872
Zalewska A, Grubecki I (2017) Inż Ap Chem 56(4):152–153
Author information
Authors and Affiliations
Contributions
All authors contributed to the study conception and design. Material preparation and data collection and analysis were performed by Anna Zalewska, Joanna Kowalik, and Magdalena Tworek. The first draft of the manuscript was written by Anna Zalewska and Joanna Kowalik, and all authors commented on previous versions of the manuscript. All authors read and approved the final manuscript.
Corresponding author
Ethics declarations
Ethics approval and consent to participate
This is not applicable.
Consent for publication
All authors read and approved the final manuscript. All authors are fully aware of this manuscript and have permission to submit the manuscript for possible publication.
Competing interests
The authors declare that they have no known competing financial interests or personal relationships that could have appeared to influence the work reported in this paper.
Additional information
Responsible Editor: George Z. Kyzas
Publisher's note
Springer Nature remains neutral with regard to jurisdictional claims in published maps and institutional affiliations.
Rights and permissions
Open Access This article is licensed under a Creative Commons Attribution 4.0 International License, which permits use, sharing, adaptation, distribution and reproduction in any medium or format, as long as you give appropriate credit to the original author(s) and the source, provide a link to the Creative Commons licence, and indicate if changes were made. The images or other third party material in this article are included in the article's Creative Commons licence, unless indicated otherwise in a credit line to the material. If material is not included in the article's Creative Commons licence and your intended use is not permitted by statutory regulation or exceeds the permitted use, you will need to obtain permission directly from the copyright holder. To view a copy of this licence, visit http://creativecommons.org/licenses/by/4.0/.
About this article
Cite this article
Zalewska, A., Kowalik, J. & Tworek, M. Investigation of the properties of a water-based acrylic dispersion modified with an ionic liquid, surfactant, and thickener. Environ Sci Pollut Res (2023). https://doi.org/10.1007/s11356-023-25384-z
Received:
Accepted:
Published:
DOI: https://doi.org/10.1007/s11356-023-25384-z