Abstract
Generation of hydrogen is very important, as it is one of the most desired alternatives to fossil fuels. Moreover, designing of cheap and stable electrocatalysts is the task for the efficient generation of hydrogen with reasonable activity. Materials hybridization can be considered a tool for engineering different material properties. Composites of modified silicon such as C–Si, Ni/(C–Si), Pt/(C–Si), and Pt–Ni/(C–Si) were prepared (in weight percent) and studied as electrocatalysts for the hydrogen evolution reaction (HER) in 0.5 M H2SO4 solution. The surface morphologies and chemical compositions of the composites were confirmed using transmission electron microscopy (TEM), scanning electron microscopy (SEM), energy-dispersive X-ray analysis (EDX), X-ray photoelectron spectroscopy (XPS), X-ray diffraction (XRD), X-ray fluorescence analysis (XRF), elemental mapping, and BET surface analysis. The electrochemical measurements of linear sweep voltammetry (LSV), Tafel plots, chronoamperometry, and electrochemical impedance spectroscopy (EIS) were used to study the behaviour of the prepared electrodes toward the hydrogen evolution process. Among the various prepared composites, [7%Pt–3%Ni]/[C–Si (1:1)] composite shows the best catalytic activity with the highest HER rate (940.95 µA cm−2 s−1), the lowest overpotential [0.358 V vs. (Ag/AgCl) ≈ 0.161 V vs. (RHE)] at 10 mA cm−2, and the lowest charge transfer resistance (2.657 Ω) compared to other prepared electrodes. In addition, it gives the highest values of 4.219 × 10−3 s−1 turn over frequency (TOF) and 642 mA g−1 mass activity. It shows good stability towards the hydrogen evolution reaction as the current density reaches about 34.28 mA cm−2 after 5 h.
Graphical abstract

Similar content being viewed by others
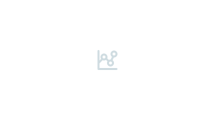
Avoid common mistakes on your manuscript.
1 Introduction
The majority of energy is supplied by fossil fuels, but their long-term use is unacceptable. Therefore, increasing interest has been paid to renewable energy sources because of the energy crisis and environmental contaminants [1, 2]. To meet the demand for energy supply in the framework of a sustainable society, it becomes necessary to produce electricity from renewable energy sources [3].
Hydrogen is considered to be one of the most important future sources of clean energy because it is one of the most desired alternatives to fossil fuels [4,5,6,7,8,9,10,11,12]. The generation of hydrogen economically and sustainably is very important to the future realization of the hydrogen economy. The electrocatalytic hydrogen evolution reaction (HER) has attracted great interest because of its ease and generality [2, 5, 13,14,15,16,17,18,19]. Using renewable energy sources to produce hydrogen via electrolysis is a promising carbon-free method, but it must be improved in terms of efficiency and durability before it can be commercially viable [20,21,22].
Long-term stability of HER catalysts is of great importance for the material that has potential practical applications, especially considering that the HER catalyst mostly works in the acidic environment [13, 23, 24]. The key issue for HER is to search for cheap electrocatalysts with excellent activity in order to produce hydrogen massively and efficiently [13, 25,26,27]. Thus, designing stable catalysts that work well in an acidic environment is of great significance [28, 29].
It is well known that the interaction between the metal and the support materials may greatly influence the catalytic performance [30, 31]. Silicon (Si) and silicon-related materials are used in various applications, including solar cells and current electric devices [2, 32, 33]. Silicon supports have attracted much attention because of their novel physical and electrochemical properties. Several methods have been developed for the fabrication of Si, such as a laser-ablation metal-catalytic method [34], an oxide-assisted method [35, 36], and a solution technique [37, 38]. Si has several benefits, including low cost, abundance, nontoxicity, and well-understood processing methods. Also, it is relatively cathodically stable, has a suitable band gap resulting in the formation of an electrochemically passive oxide upon interaction with aqueous media, and in principle can produce a significant portion of the total photovoltage needed for water splitting [21, 39]. Functionalization of Si nanostructures is one way to further improve the properties of these devices. The chemical bonds between Si and metals prevent the aggregation of the loaded metal nanoparticles [40, 41], which could greatly enhance the electrocatalytic stability.
Carbon Black Vulcan XC 72 is one of the commonly used conducting supports in the preparation of catalysts, where it showed good properties such as porous nature, light weight, large surface area, and good adsorption of the catalyst on its surface [42]. They possess high electrical conductivity, high chemical stability, and extremely high mechanical strength and modulus [43]. Accordingly, they were applied and used as supports in electrocatalysis [44, 45].
Platinum (Pt) is regarded as the best catalyst with the highest efficiency at the current stage. Because of their high current densities and near-zero overpotential, Pt and Pt-based materials have been widely used as HER catalysts [14, 46,47,48,49,50]. The high cost and rareness of Pt have motivated scientists to design new materials as acceptable replacements for Pt or to contain as little Pt as possible [48]. So, adding a small amount of platinum to other metals is preferred to avoid the high cost of platinum and obtain the advantages of the synergy of the added metals.
Ni is considered an efficient and stable electrocatalyst for producing hydrogen in an alkaline medium [51, 52]. By adjusting the applied overpotential, Ni can also be used as an efficient electrocatalyst in an acidic medium [53]. Even though Ni has sufficient electrocatalytic activity for hydrogen ion reduction, there is a great need for increasing its activity through alloying or increasing specific surface area through various structures [50,51,52, 54,55,56,57]. Ni possesses the best electrocatalytic activity among all nonprecious metals, and particularly its nanoparticles have a major impact on improving electrocatalytic activity [52, 58, 59].
This work is an attempt to design cheap and stable electrocatalysts for HER with reasonable activity to produce hydrogen. Silicon–carbon composite is used as a host material for metals, namely Ni and/or Pt, in small amounts to be used as hybrid electrocatalysts. The stability and catalytic activity of the as-prepared catalysts towards the HER in the acidic medium are the main targets of this study.
2 Experimental
2.1 Materials
All the chemical materials used in this study are of analytical grade and were used as received without further purification. The used chemicals; Mg powder, carbon black (XC 72), H2SO4, HCl, HF, CH3COOH, Polytetrafluoroethylene (PTFE), Ni(NO3)2·6H2O, H2PtCl6, ethylene glycol, and hydrazine were purchased from Fluka-Honeywell Research Chemicals. The crushed silica (SiO2) is prepared by crushing the Sinai white sand with a ball mill for 8 h at a speed of 200 rpm to obtain particles with an average size of 100 nm. The double-distilled water with a resistivity of 17 MΩ cm−1 was used for the preparation of various solutions.
2.2 Extraction of silicon from white sand
Si is extracted by mixing crushed SiO2 and Mg powder with a molar ratio of 1:2, respectively, and blending them thoroughly using a stainless steel spatula. 100 g of the mixture was placed in a sealed stainless steel reactor and put in a programmed muffle furnace. The temperature was raised at a rate of 5 °C min−1 to the target temperature of 850 °C. After the desired holding time (2 h), the furnace was switched off, and the sample was cooled slowly to room temperature within the furnace. Then, the reaction product cake was removed and crushed to a fine powder [60]. Recovery of Si from the reduction products was achieved by leaching the reduction products in three stages: (a) In the first stage, the powders were leached in 2 M HCl at 70 °C with continuous magnetic stirring to remove MgO and Mg2Si; (b) The second stage involved leaching the material with 2 M HCl and 25% acetic acid for the removal of Mg2SiO4; (c) To remove the remaining Mg2SiO4, unreacted silica, and other contaminated metallic impurities, the material was further leached with 4.8% HF and 25% acetic acid at 70 °C in a polypropylene container for 1 h. Finally, all acids were removed by washing with warm demineralized water, and the product was filtered and dried.
From the economic and practical point of view, the filtrate produced in the first stage of leaching contains pure MgCl2:
So, the filtrate was evaporated under reduced pressure at 110 °C to obtain pure MgCl2·6H2O to be used for other purposes [61, 62].
2.3 Synthesis of C–Si, Ni/C–Si, Pt/C–Si, and Pt–Ni/C–Si catalysts
10 mg of carbon black was accurately weighed and heated for 1 h at 160 °C for activation. Then, definite amounts of silicon were added to prepare pastes with different wt% ratios of silicon:carbon composite. Each paste was synthesized by adding the appropriate weight of silicon to carbon, and 5 mL of methanol was added. The components were stirred well on the hot plate to ensure good mixing between carbon and silicon. 1–2 drops of polytetrafluoroethylene (PTFE) were added to bind the components together to form a paste. Each paste was heated for 1 h at 160 °C for activation before each experiment.
The prepared electrodes were encapsulated in the form of a disc with an apparent circular surface area of 0.135 cm2. The best-chosen silicon–carbon powder, according to their mixing ratio, was modified with nickel and/or platinum metals. The silicon–carbon powder was mixed with a calculated amount of hydrated nickel nitrate Ni(NO3)2·6H2O and dispersed in 20 mL of ethylene glycol with constant mechanical stirring on a hot plate for 3 h at 60 °C to intercalate the precursor ions into C–Si support pores. Then, the in-situ reduction of Ni2+ was achieved by adding the hydrazine dropwise to reduce Ni2+ into Nio nanoparticles. After filtration and washing with acetone, the composite was collected and dried in an oven at 90 °C for 1 h. By applying the same procedures, the Pt/C–Si and Pt–Ni/C–Si hybrid materials were prepared using hexachloroplatinic acid H2PtCl6 as a platinum precursor.
2.4 Characterization procedures
The surface morphologies and chemical compositions of the prepared composites have been investigated using TEM, SEM, EDX, XPS, XRF, BET, and XRD. The TEM profile was investigated using the transmission electron microscope model Jeol jem 1400, Japan. The SEM images, elemental mapping, and EDX analysis were examined on a Zeiss Sigma 300 vp Field Emission electron microscope. X-ray Fluorescence analyzer, Malvern Panalytical, Epsilon 1, was used for the XRF analysis. An X-ray diffractometer, PANalytical model X, pert PRO, with a Cu K radiation (k = 1.5418 Å) and a scanning rate of 0.3 min−1, was used for the XRD analysis. The X-ray photoelectron spectroscopy (XPS) data were collected on K-alpha (Thermo Fisher Scientific, USA) using monochromatic X-ray Al K-alpha radiation with a spot size of 400 µm at a pressure of 10−9 mbar and a full-spectrum pass energy of 200 eV and a narrow-spectrum pass energy of 50 eV. The textural analysis of the as-prepared composite catalytic systems was characterized by nitrogen adsorption–desorption isotherms at 196 °C using the NOVA 3200 apparatus, USA. For surface degassing, the samples were pretreated under vacuum (10−4 Torr) at 150 °C for 2 h. From the adsorption isotherm branch, the surface areas (SBET) were estimated using the BET equation. The pore size distribution was calculated from the isotherm’s desorption branch using the Barrett, Joyner, and Halenda (BJH) method.
2.5 Electrochemical measurements
The electrochemical measurements towards the HER were carried out using C–Si, Ni/C–Si, Pt/C–Si, and Pt–Ni/C–Si catalysts as working electrodes in a three-electrode cell. The reference electrode was a silver/silver chloride electrode (Ag/AgCl/sat. KCl solution), and the counter electrode was a Pt sheet. The electrochemical measurements were performed using linear sweep voltammetry (LSV), chronoamperometry, electrochemical impedance spectroscopy (EIS), and Tafel plots. The chronoamperometry measurements were recorded at − 0.6 V, and the EIS measurements were recorded at the onset potential of HER according to each electrode within a frequency range from 105 to 102 Hz at an alternating current amplitude of 5 mV. All these electrochemical studies were performed using a potentiostat (CHI 660 Potentiostat/Galvanostat). The measurements were carried out in a 0.5 M H2SO4 solution at a room temperature of 25 ± 0.2 °C.
3 Results and discussion
3.1 Constitutional investigation
To confirm the composition and the proportion of the metallic species of the as-prepared composite catalysts, 10%Ni/[C–Si (1:1)], 10%Pt/[C–Si (1:1)], and [7%Pt–3%Ni]/[C–Si (1:1)], the metallic elemental analysis was achieved via XRF analysis, Table 1. From the table the concentration of metallic species in each catalyst is very close to its weight during the preparation, which confirms the good accuracy of the preparation.
The scanning electron microscopy (SEM) images in Fig. 1a–e show the surface morphology of Si, C–Si (1:1), 10%Ni/[C–Si (1:1)], 10%Pt/[C–Si (1:1)], and [7%Pt–3%Ni]/[C–Si (1:1)], respectively. The surface morphology of Si (Fig. 1a) shows large agglomerates of white Si sheets with mesopores (cf. Table 3). The SEM image of C–Si (1:1) (Fig. 1b) exhibits a homogeneous distribution between carbon and silicon. On the other hand, the SEM image of 10%Ni/[C–Si (1:1)] (Fig. 1c) shows the same image of C–Si (1:1) but with lighted, homogeneously distributed dots that could indicate the presence of Ni particles on the surface. The SEM image of 10%Pt/[C–Si (1:1)] (Fig. 1d) is similar to the previous composite, but Pt is shown as grey-coloured dots and aggregates. Figure 1e represents the surface morphology of the composite [7%Pt–3%Ni]/[C–Si (1:1)], and it shows a very large homogeneity between the components of this composite. The elemental composition of this composite [7%Pt–3%Ni]/[C–Si (1:1)] is determined by the energy-dispersive X-ray (EDX) technique and is represented in Fig. 1f. Values of the wt% of the elements Si, C, O, Ni, and Pt for this composite are represented in Table 2. The relatively high percentage of C compared to Si (even though their ratio in the prepared composite is 1:1) is due to the small size of carbon, which in turn causes a higher distribution compared to Si.
Figure 2 shows the acquired N2 adsorption–desorption isotherms across Si pristine material, [C–Si (1:1)], 10%Ni/[C–Si (1:1)], and [7%Pt–3%Ni]/[C–Si (1:1)]. All material isotherms belong most probably to type III according to the IUPAC classification, exhibiting an H3 hysteresis loop that suggests slit-like pores with capillary condensation in heterogeneous micro- and/or mesopores (cf. the SEM and PSD profiles). Table 3 shows the surface parameters derived from adsorption–desorption isotherms, including specific surface areas (SBET m2g−1), pore volumes (Vp, cm3 g−1), estimated at 0.95 p/po, and average pore diameter (Dpcp), assuming a cylindrical pore (cp) model derived from PSD curves depicted in Fig. 2. It is evident from the Table that adding C to the extracted Si may result in significant increases in surface area and pore size, where the hydraulic diameter is shifted from 1.2 nm for Si to 3.5 nm for [C–Si (1:1)], with the elimination of wider pores that are most probably filled with carbon. By loading the electrode surface with metallic species, a marked increase in surface area and pore volume, accompanied by a decrease in pore diameters, is observed. This may be related to the restructuring of the surface network.
XPS is a powerful analysis tool that is used to identify the surface chemical compositions and the oxidation states of the elements of the prepared composites. The XPS survey spectra of the as-prepared composite electrodes and their constituent metallic species are shown in Fig. 3. The presence of carbon, silicon, oxygen, nickel, and platinum are detected as the main peak elements in the prepared composite electrodes. The XP-spectra of Ni and Pt in the various composites display different peaks-relative intensities due to the difference in the environment and synergism between the metallic species [63,64,65,66,67]. The relative intensity of the peak characteristic for clean platinum, viz., PtO, is higher in [7%Pt–3%Ni]/[C–Si (1:1)] than in 10%Pt/[C–Si (1:1)], which is consistent with the catalytic performance in which the PtO species provides the active sites for the oxidation reaction rather than Pt4+ [68]. Furthermore, the XP-spectra of Ni and Pt in the 10%Ni/[C–Si (1:1)] and 10%Pt/[C–Si (1:1)] differ markedly from the spectra in the [7%Pt–3%Ni]/[C–Si (1:1)], confirming Ni–Pt synergism.
XRD is another technique that is used to elucidate the phase analysis of the prepared composites. XRD analysis of [7%Pt–3%Ni]/[C:Si (1:1)] is represented in Fig. 4. It is noted in the figure that the characteristic peak of C has a very low intensity compared to Si, referring to the difference in the degree of crystallinity. The diffraction patterns illustrate well-defined diffraction peaks for Si according to the standard card (00-005-0565); peaks at 28.5°, 47.3°, 56.1°, 69.2°, and 76.3°; assigned to (111), (220), (311), (400), and (331) planes, respectively. A small, broad peak for C appeared at 25.5°, corresponding to the (002) plane according to the standard card (00-001-0640). The peaks assigned to Ni appear as a small broad peak at 43.1° and a small peak at 60.2° characteristic for (200) and (220), respectively, according to the standard card (00-001-1258). The peaks characteristic of Pt appear as a small broad peak at 39.6°, a peak at 47.1°, and a small peak at 68.3° assigned to (111), (200), and (220) planes, respectively, according to the standard card (01-085-5658).
3.2 Electrochemical properties and catalytic performance
Silicon has attracted much attention because of its novel physical and electrochemical properties [69]. Silicon in its pristine form has a high specific surface area, but it was found to have very little activity for the HER. So, modification of silicon was necessary to obtain a good catalyst towards HER. In this study, the bi-constitute composite material C–Si was first prepared and investigated in different ratios. In the second stage of the study, tri- and tetra-constitute composites of Ni/C–Si, Pt/C–Si, and Pt–Ni/C–Si were prepared and optimized.
Firstly, carbon powder was mixed with silicon in various weight ratios to increase the specific surface area of the prepared electrodes and optimize the best ratio for obtaining good catalytic performance. The electrocatalytic activity of the prepared composites towards HER was studied using the LSV technique at 25 °C in the potential range from + 0.1 to − 1.3 V (Ag/AgCl) at a scan rate of 5 mV s−1 in 0.5 M H2SO4, as shown in supplementary Fig. s1. This study showed that, carbon enhances the activity of silicon, and the composite C:Si with a ratio of 50%:50% gives the best results compared to the other ratios either with respect to the value of the onset potential of this reaction or the rate of HER. This ratio gives the least negative onset hydrogen evolution potential (− 0.741 V) and the highest rate of HER (45.49 µA cm−2 s−1) compared to other C:Si ratios in this study. The rate value of hydrogen evolution was deduced from the slope of the straight segment of the cathodic current of hydrogen evolution (mA cm−2 V−1) multiplied by the scan rate [5 mV s−1].
For all the foregoing studies, a carbon–silicon mixture with a ratio of 50%:50% was chosen as the host composite material for supporting the metal particles. Nickel metal was incorporated into the silicon–carbon matrix via the in-situ reduction of Ni precursor to obtain Ni/(C–Si) composites. Various electrodes were prepared by loading different weight ratios of Ni onto C:Si (1:1), and their activity towards the HER was studied in the potential range from + 0.1 to − 1.0 V (Ag/AgCl) at a scan rate of 5 mV s−1. The electrochemical behaviour of the prepared nickel-modified composites is represented in supplementary Fig. s2. It is noticed that the composite with a ratio of 10% Ni and 90% [C:Si (1:1)] shows the highest rate of HER (170.2 µA cm−2 s−1), the least onset hydrogen evolution potential (− 0.288 V), and the lowest overpotential [0.671 V vs. (Ag/AgCl)] at 10 mA cm−2 compared to other ratios.
Despite the initial high electrochemical activity of nickel, it may be deactivated during operation due to hydrogen adsorption, promoted by the strong Ni–Had bond strength, causing the shielding of Ni-surface active sites. Also, this results in performance degradation with an increase in the overpotential under constant current stress [70,71,72]. So, adding another active metal with nickel would solve this problem by increasing the activity and stability towards the HER. Platinum is considered the best catalyst for HER [73, 74], as it exhibits high current density and nearly zero HER overpotential [47]. However, platinum is also livery expensive, and therefore, its amount should be reduced as much as possible to reduce the cost. So, platinum is prepared in a composite with a ratio of 10% Pt and 90% [C:Si (1:1)] for comparison with Ni composite, and this amount is reduced during the modification with Ni metal in the composite.
HER was investigated using the following prepared electrodes; Si, C–Si (1:1), 10%Ni/[C–Si (1:1)], 10%Pt/[C–Si (1:1)], and [7%Pt–3%Ni]/[C–Si (1:1)] (optimized ratio) in 0.5 M H2SO4 solution in the potential range from + 0.1 to − 1.0 V (Ag/AgCl) at a scan rate of 5 mV s−1 as shown in Fig. 5. It is observed that the electrode [7%Pt–3%Ni]/[C–Si (1:1)] gives the best result compared to other prepared electrodes [highest HER rate (940.95 µA cm−2 s−1), lowest overpotential [0.358 V vs. (Ag/AgCl) ≈ 0.161 V vs. (RHE)] at 10 mA cm−2]. This means that the incorporation of a small amount of platinum and nickel metals into the carbon–silicon composite enhanced their activity towards the HER. This may be linked with the synergetic effects of the binary metallic species in the prepared composites, as discussed in the XPS analysis, and the intrinsic activity of platinum [50, 75, 76]. The values of hydrogen evolution onset potential, overpotential at 10 mA cm−2 and the rate of HER (µA cm−2 s−1) are shown in Table 4. The rate values were calculated from the slopes of the straight line relations represented in Fig. s3. These lines are obtained by plotting a relation between potential values, selected from the straight segments of hydrogen evolution in Fig. 5 at potential values from − 1.0 V till − 0.4 V, and their corresponding current density values.
The enhanced catalysis of the prepared composites as shown in Table 4 may be due to the increase in the electroactive surface area. So, the active surface area of the prepared composites was evaluated by recording the CV response of 1.0 mM [Fe(CN)6]3−/4− (1:1) in 0.1 mol L−1 KCl solution at different scan rates as shown in Fig. s4. The surface area is calculated using the Randles–Sevcik equation [77]:
where Ip is the peak current (A), n is the number of the transferred electrons in the electrochemical process (n = 1), A is the electrode surface area (cm2), D is the diffusion coefficient (6.5 × 10−6 cm2 s−1 [77]), C is the concentration of the redox probe (mol cm−3), and ν is the applied scan rate (V/s). By substituting the slope of Ip versus ν1/2 (see Fig. s4) in the above equation, the electroactive surface area was calculated to be 0.370, 1.939, and 2.056 for 10%Ni/[C–Si (1:1)], 10%Pt/[C–Si (1:1)], and [7%Pt–3%Ni]/[C–Si (1:1)], respectively.
Another activity metric used as a reaction kinetics indicator is turnover frequency (TOF). It shows the amount of hydrogen that evolves each unit of time at a single catalytically active site [78]. The following equation [79] can be used to get TOF for the hydrogen evolution reaction under the assumption that Faradic efficiency is 100%:
where I is the current (A), 2 is the number of electrons needed to produce a molecule of the product H2, F is the Faraday constant (96,500 C mol−1), m is the number of moles of metallic active species in the composite. The number of moles of metallic species is calculated according to the mass values obtained from XRF analysis, and each composite mass was 10 mg. Then, the number of moles of metallic species in 10%Ni/[C–Si (1:1)], 10%Pt/[C–Si (1:1)], and [7%Pt–3%Ni]/[C–Si (1:1)] are 1.64 × 10−5, 5.03 × 10−6, and 7.89 × 10−6 mol. A comparison between current density (mA cm−2), mass activity (mA g−1), current per active surface area (mA cm−2), and turn over frequency (s−1) for the prepared composites Si, C–Si (1:1), 10%Ni/[C–Si (1:1)], 10%Pt/[C–Si (1:1)], and [7%Pt–3%Ni]/[C–Si (1:1)] is tabulated in Table 5. It is observed that all the current density values are increased with the sequence; Si < C–Si (1:1) < 10%Ni/[C–Si (1:1)] < 10%Pt/[C–Si (1:1)] < [7%Pt–3%Ni]/[C–Si (1:1)] except the current density per active surface area. The lower value for 10%Pt/[C–Si (1:1)] compared to 10%Ni/[C–Si (1:1)] may be due to the large size of Pt compared to Ni of the same ratio. The values obtained in case of [7%Pt–3%Ni]/[C–Si (1:1)] may be due to the synergism between Pt and Ni in the prepared composite.
Tafel plot represents the relation between the polarization current density and the overpotential as a probe of the intrinsic behaviour of the electrocatalysts according to the following equation [48, 80]:
where “ƞ” is the overpotential (V), “a” represents the intercept, “b” represents the Tafel slope, and “i” represents the cathodic current density. The exchange current density (io) is an important parameter for the HER, and it can be calculated from the relation: log io = (− b/a). The high value of io represents the better electrocatalyst towards the HER. Figure 6 represents the Tafel plots for Si and the composites C–Si (1:1), 10%Ni/[C–Si (1:1)], 10%Pt/[C–Si (1:1)], and [7%Pt–3%Ni]/[C–Si (1:1)] in 0.5 M H2SO4 solution at a scan rate of 1 mV s−1. It is observed that all the prepared composites have nearly the same slope, which indicates that the mechanism of hydrogen evolution is the same. The slope and exchange current density values of the prepared composites are represented in Table 6. From these results, it is indicated that the prepared composite [7%Pt–3%Ni]/[C–Si (1:1)] is the best one towards the HER compared to other prepared composites. A comparison between our work and other work in literature is represented in Table 7.
Electrochemical impedance spectroscopy (EIS) was used to evaluate the electrode polarization and understand the charge transfer kinetics towards the HER. The observed EIS spectra from these measurements at lower frequencies indicate the material behaviour, and at a higher frequency, they are usually associated with the bulk electrolyte behaviour [25]. EIS measurements were recorded at the onset potential of each electrode within a frequency range from 105 to 102 Hz at an alternating current amplitude of 5 mV.
Bode plots of the prepared composites are shown in Fig. s5. The impedance (Z) of HER decreases in the order Si > C–Si (1:1) > 10%Ni/[C–Si (1:1)] > 10%Pt/[C–Si (1:1)] > [7%Pt–3%Ni]/[C–Si (1:1)]. The lowest value of (Z) indicates the high conductivity and catalytic activity towards the charge transfer reaction of the HER, which confirms that the composite [7%Pt–3%Ni]/[C–Si (1:1)] is the best catalyst towards the HER among the employed electrodes. The Nyquist plot for the prepared composites is constructed and represented in Fig. 7. The capacitive semicircle diameters decrease with the insertion of carbon and Pt–Ni metal particles till reaching the best behaviour for the composite [7%Pt–3%Ni]/[C–Si (1:1)]. Magnification Nyquist plot of the prepared composites C–Si (1:1), 10%Ni/[C–Si (1:1)], 10%Pt/[C–Si (1:1)] and [7%Pt–3%Ni]/[C–Si (1:1)] is represented in inset Fig. 7.
Nyquist plot of the Si-neat material and the prepared composites C–Si (1:1), 10%Ni/[C–Si (1:1)], 10%Pt/[C–Si (1:1)] and [7%Pt–3%Ni[/[C–Si (1:1)] at HER onset potential of each composite. The inset figure represents magnification of Nyquist plot of the prepared composites C–Si (1:1), 10%Ni/[C–Si (1:1)], 10%Pt/[C–Si (1:1)] and [7%Pt–3%Ni]/[C–Si (1:1)]
The fitting data were applied for these composites, and the equivalent circuit that is used for fitting is represented in Fig. 8. The equivalent circuit was found to compose of solution resistance (Rs), constant phase element [Q(0.5)], charge transfer resistance (R1), Warburg diffusion component (W), surface adsorption capacitance (C1), and surface adsorption resistance (R2) [25, 91, 92]. All fitting parameters for the prepared composites as calculated by the instrument software are represented in Table 8. All parameters are tabulated as taken from the device without being multiplied by surface area. The presence of Warburg impedance in the circuit confirms that mass transport is limited by the surface protective film. The presence of a constant phase element confirms the porosity of the prepared composites. In comparison to other materials, the composite 7%Pt–3%Ni/[C–Si (1:1)] delivers the lowest values of the charge transfer resistance which supports the electrode’s maximum activity towards the HER.
3.3 Durability test
The stability of the prepared catalysts is an essential parameter for the practical application of the synthesized electrocatalysts. It is measured by the variation in current versus time (I–t curve), where the catalyst with excellent stability shows a negligible loss in current density with time. I–t curves of the Si-neat material and the prepared composites: C–Si (1:1), 10%Ni/[C–Si (1:1)], 10%Pt/[C–Si (1:1)] and [7%Pt–3%Ni]/[C–Si (1:1)] at − 0.6 V (Ag/AgCl) in 0.5 M H2SO4 for 5 h are represented in Fig. 9. It is observed that the stability of the prepared composites can be arranged in the following order: Si < C–Si (1:1) < 10%Ni/[C–Si (1:1)] < 10%Pt/[C–Si (1:1)] < [7%Pt–3%Ni]/[C–Si (1:1)], as indicated from the cathodic current density values obtained for these composites. The current density in case of 10%Pt/[C–Si (1:1)] composite decreases rapidly from the start current density and reaches 22.35 mA cm−2 after 5 h compared to that at [7%Pt–3%Ni]/[C–Si (1:1)] which attains stability early and reaches 34.28 mA cm−2 after 5 h. This means that the presence of Pt and Ni in the composite add extra stability to the catalyst towards HER compared to the presence of Pt only in the composite. To confirm the stability of [7%Pt–3%Ni]/[C–Si (1:1)] as a promised catalyst, the exploited catalyst was investigated by TEM, SEM, and elemental mapping as shown in Fig. 10. The figure exhibits the homogeneity of the composite catalyst and its stability during the catalytic HER.
4 Conclusion
The study shows that the Si-neat material has very low activity towards HER. However, doping with C, Ni, and Pt significantly enhances the electrocatalytic activity by increasing the composite electrode surface area and the synergism between the constitutional species. Ni/C–Si composite electrode exhibits deactivation during the HER process. The incorporation of Pt in a small ratio with Ni into [C–Si (1:1)] enhances the stability and activity of the electrode via the synergism between Ni–Pt bimetallic species. All the tests done for the as-prepared composite electrodes show that [7%Pt–3%Ni]/[C–Si (1:1)] has the best activity and stability towards the HER in acidic medium compared to other prepared composites in this study. It shows the lowest overpotential [0.358 V vs. (Ag/AgCl) ≈ 0.161 V vs. (RHE)] at 10 mA cm−2, best exchange current density (5.345 mA cm−2), and the lowest charge transfer resistance (2.657 Ω). It gives the highest turn over frequency (TOF) value of 4.219 × 10−3 s−1, and 642 mA g−1 for mass activity compared to other prepared composites. In addition, it shows good stability towards the hydrogen evolution reaction as the current density reaches about 34.28 mA cm−2 after 5 h. Therefore, this work represents a promising approach for designing and fabricating electrocatalysts with improved electric energy for the production of green hydrogen to improve energy conversion efficiency.
References
Potocnik J (2007) Renewable energy sources and the realities of setting an energy agenda. Science 315:810–811
Ray U, Sarkar S, Banerjee D (2022) Silicon nanowires as an efficient material for hydrogen evolution through catalysis: a review. Catal Today. https://doi.org/10.1016/j.cattod.2022.11.025
Chow J, Kopp RJ, Portney PR (2003) Energy resources and global development. Science 302:1528–1531. https://doi.org/10.1126/science.1091939
Uyar TS, Beşikci D (2017) Integration of hydrogen energy systems into renewable energy systems for better design of 100% renewable energy communities. Int J Hydrogen Energy 42:2453–2456. https://doi.org/10.1016/j.ijhydene.2016.09.086
Wang J, Xu F, Jin H et al (2017) Non-noble metal-based carbon composites in hydrogen evolution reaction: fundamentals to applications. Adv Mater. https://doi.org/10.1002/adma.201605838
Schalenbach M, Tjarks G, Carmo M et al (2016) Acidic or alkaline? Towards a new perspective on the efficiency of water electrolysis. J Electrochem Soc 163:F3197–F3208. https://doi.org/10.1149/2.0271611jes
Hosseini SE, Wahid MA (2016) Hydrogen production from renewable and sustainable energy resources: promising green energy carrier for clean development. Renew Sustain Energy Rev 57:850–866. https://doi.org/10.1016/j.rser.2015.12.112
Yang L, Zhou W, Hou D et al (2015) Porous metallic MoO2-supported MoS2 nanosheets for enhanced electrocatalytic activity in the hydrogen evolution reaction. Nanoscale 7:5203–5208. https://doi.org/10.1039/c4nr06754a
Armaroli N, Balzani V (2011) The hydrogen issue. ChemSusChem 4:21–36. https://doi.org/10.1002/cssc.201000182
Zhou W, Chen S, Meng X et al (2023) Energy-saving cathodic H2 production enabled by non-oxygen evolution anodic reactions: a critical review on fundamental principles and applications. Int J Hydrogen Energy. https://doi.org/10.1016/j.ijhydene.2023.01.063
Yu X, Gao B, Feng B et al (2023) Modular electrochemical production of hydrogen using Mott–Schottky Co9S8/Ni3S2 heterojunction as a redox mediator. Int J Hydrogen Energy 48:16184–16197
Li X, Liu Y, Wu Y et al (2021) Vanadium doped nickel cobalt phosphide as an efficient and stable electrode catalyst for hydrogen evolution reaction. J Electroanal Chem 902:115812
Abdel Hamid Z, Hassan HB, Sultan M (2020) Electrodeposition of Ni–W and Ni–W–P films using a pulse current technique and their application for hydrogen evolution in an acidic solution. Anti-Corros Methods Mater 67:38–47. https://doi.org/10.1108/ACMM-09-2019-2176
Yin H, Zhao S, Zhao K et al (2015) Ultrathin platinum nanowires grown on single-layered nickel hydroxide with high hydrogen evolution activity. Nat Commun 6:1–8. https://doi.org/10.1038/ncomms7430
Gao MR, Liang JX, Zheng YR et al (2015) An efficient molybdenum disulfide/cobalt diselenide hybrid catalyst for electrochemical hydrogen generation. Nat Commun. https://doi.org/10.1038/ncomms6982
Zheng Y, Jiao Y, Zhu Y et al (2014) Hydrogen evolution by a metal-free electrocatalyst. Nat Commun 5:2–9. https://doi.org/10.1038/ncomms4783
Fei H, Dong J, Arellano-Jiménez MJ et al (2015) Atomic cobalt on nitrogen-doped graphene for hydrogen generation. Nat Commun 6:1–8. https://doi.org/10.1038/ncomms9668
Liu Q, He YM, Weng X et al (2018) One-pot aqueous fabrication of reduced graphene oxide supported porous PtAg alloy nanoflowers to greatly boost catalytic performances for oxygen reduction and hydrogen evolution. J Colloid Interface Sci 513:455–463. https://doi.org/10.1016/j.jcis.2017.11.026
Liu M, Yang L, Liu T et al (2017) Fe2P/reduced graphene oxide/Fe2P sandwich-structured nanowall arrays: a high-performance non-noble-metal electrocatalyst for hydrogen evolution. J Mater Chem A 5:8608–8615. https://doi.org/10.1039/c7ta01791j
Milazzo RG, Privitera SMS, Scalese S, Lombardo SA (2019) Effect of morphology and mechanical stability of nanometric platinum layer on nickel foam for hydrogen evolution reaction. Energies. https://doi.org/10.3390/en12163116
Helm ML, Stewart MP, Bullock RM et al (2011) A synthetic nickel electrocatalyst with a turnover frequency above 100,000 s−1 for H2 production. Science 333:863–866. https://doi.org/10.1126/science.1205864
Jaramillo TF, Jørgensen KP, Bonde J et al (2007) Identification of active edge sites for electrochemical H2 evolution from MoS2 nanocatalysts. Science 317:100–102. https://doi.org/10.1126/science.1141483
Morales-Guio CG, Stern LA, Hu X (2014) Nanostructured hydrotreating catalysts for electrochemical hydrogen evolution. Chem Soc Rev 43:6555–6569. https://doi.org/10.1039/c3cs60468c
Shi Y, Zhang B (2016) Recent advances in transition metal phosphide nanomaterials: synthesis and applications in hydrogen evolution reaction. Chem Soc Rev 45:1529–1541. https://doi.org/10.1039/c5cs00434a
Shen W, Wu B, Liao F et al (2017) Optimizing the hydrogen evolution reaction by shrinking Pt amount in Pt–Ag/SiNW nanocomposites. Int J Hydrogen Energy 42:15024–15030. https://doi.org/10.1016/j.ijhydene.2017.03.110
Walter MG, Warren EL, McKone JR et al (2010) Solar water splitting cells. Chem Rev 110:6446–6473. https://doi.org/10.1021/cr1002326
Zeng M, Li Y (2015) Recent advances in heterogeneous electrocatalysts for the hydrogen evolution reaction. J Mater Chem A 3:14942–14962. https://doi.org/10.1039/c5ta02974k
Zhang G, Wang G, Liu Y et al (2016) Highly active and stable catalysts of phytic acid-derivative transition metal phosphides for full water splitting. J Am Chem Soc 138:14686–14693. https://doi.org/10.1021/jacs.6b08491
Moon JS, Jang JH, Kim EG et al (2015) The nature of active sites of Ni2P electrocatalyst for hydrogen evolution reaction. J Catal 326:92–99. https://doi.org/10.1016/j.jcat.2015.03.012
Karunadasa HI, Montalvo E, Sun Y et al (2012) A molecular MoS2 edge site mimic for catalytic hydrogen generation. Science 335:698–702. https://doi.org/10.1126/science.1215868
Nørskov JK, Bligaard T, Logadottir A et al (2005) Trends in the exchange current for hydrogen evolution. J Electrochem Soc 152:J23. https://doi.org/10.1149/1.1856988
Chen YW, Prange JD, Dühnen S et al (2011) Atomic layer-deposited tunnel oxide stabilizes silicon photoanodes for water oxidation. Nat Mater 10:539–544. https://doi.org/10.1038/nmat3047
Fukata N, Subramani T, Jevasuwan W et al (2017) Functionalization of silicon nanostructures. Energy Storage 13:1701713. https://doi.org/10.1002/smll.201701713
Morales AM, Lieber CM (1998) A Laser ablation method for the synthesis of crystalline semiconductor nanowires. Science 279(5348):208–211. https://doi.org/10.1126/science.279.5348.208
Shi WS, Peng HY, Xu L et al (2000) Coaxial three-layer nanocables synthesized by combining laser ablation and thermal evaporation. Adv Mater 12:1927–1930. https://doi.org/10.1002/1521-4095(200012)12:24%3c1927::AID-ADMA1927%3e3.0.CO;2-C
Zhang RQ, Lifshitz Y, Lee ST (2003) Oxide-assisted growth of semiconducting nanowires. Adv Mater 15:635–640. https://doi.org/10.1002/adma.200301641
Holmes JD, Johnston KP, Doty RC, Korgel BA (2000) Control of thickness and orientation of solution-grown silicon nanowires. Science 287(5457):1471–1473
Heitsch AT, Fanfair DD, Tuan HY, Korgel BA (2008) Solution-liquid-solid (SLS) growth of silicon nanowires. J Am Chem Soc 130:5436–5437. https://doi.org/10.1021/ja8011353
Bolton JR, Stricklert SJ, Connolly J (1985) Limiting and realizable efficiencies of solar photolysis of water. Nature 316:495–500
Vargas-Hernández RA (2020) Bayesian optimization for calibrating and selecting hybrid-density functional models. J Phys Chem A 124:4053–4061. https://doi.org/10.1021/acs.jpca.0c01375
Klime J, Bowler DR, Michaelides A (2011) Van der Waals density functionals applied to solids. Phys Rev B 83:1–13. https://doi.org/10.1103/PhysRevB.83.195131
Verma LK (2000) Studies on methanol fuel cell. J Power Sources 86:464–468
Luong JHT, Hrapovic S, Wang D et al (2004) Solubilization of multiwall carbon nanotubes by 3-aminopropyltriethoxysilane towards the fabrication of electrochemical biosensors with promoted electron transfer. Electroanalysis 16:132–139
Wang Z, Liu J, Liang Q et al (2002) Carbon nanotube-modified electrodes for the simultaneous determination of dopamine and ascorbic acid. Analyst 127:653–658
Luo H, Shi Z, Li N et al (2001) Investigation of the electrochemical and electrocatalytic behavior of single-wall carbon nanotube film on a glassy carbon electrode. Anal Chem 73:915–920
Cao X, Han Y, Gao C et al (2014) Highly catalytic active PtNiCu nanochains for hydrogen evolution reaction. Nano Energy 9:301–308. https://doi.org/10.1016/j.nanoen.2014.08.008
Sheng W, Gasteiger HA, Shao-Horn Y (2010) Hydrogen oxidation and evolution reaction kinetics on platinum: acid vs alkaline electrolytes. J Electrochem Soc 157:B1529. https://doi.org/10.1149/1.3483106
Zhu L, Lin H, Li Y et al (2016) A rhodium/silicon co-electrocatalyst design concept to surpass platinum hydrogen evolution activity at high overpotentials. Nat Commun. https://doi.org/10.1038/ncomms12272
Zhang J, Zhao Y, Guo X et al (2018) Single platinum atoms immobilized on an MXene as an efficient catalyst for the hydrogen evolution reaction. Nat Catal 1:985–992
Hüner B, Demir N, Kaya MF (2023) Ni–Pt coating on graphene based 3D printed electrodes for hydrogen evolution reactions in alkaline media. Fuel 331:125971
Gong M, Wang D-Y, Chen C-C et al (2016) A mini review on nickel-based electrocatalysts for alkaline hydrogen evolution reaction. Nano Res 9:28–46
Vij V, Sultan S, Harzandi AM et al (2017) Nickel-based electrocatalysts for energy-related applications: oxygen reduction, oxygen evolution, and hydrogen evolution reactions. ACS Catal 7:7196–7225. https://doi.org/10.1021/acscatal.7b01800
Lu J, Xiong T, Zhou W et al (2016) Metal nickel foam as an efficient and stable electrode for hydrogen evolution reaction in acidic electrolyte under reasonable overpotentials. ACS Appl Mater Interfaces 8:5065–5069. https://doi.org/10.1021/acsami.6b00233
Rao D, Wang L, Zhu Y et al (2016) Electrochemical preparation of Ni–Mo coated coral-like cu micro-arrays for electrocatalytic hydrogen evolution reaction in acidic solution. J Electrochem Soc 163:H1026–H1032. https://doi.org/10.1149/2.1021610jes
Gomez Vidales A, Omanovic S (2018) Evaluation of nickel-molybdenum-oxides as cathodes for hydrogen evolution by water electrolysis in acidic, alkaline, and neutral media. Electrochim Acta 262:115–123. https://doi.org/10.1016/j.electacta.2018.01.007
Di HX, Xu F, Li F et al (2017) Composition-performance relationship of NixCuy nanoalloys as hydrogen evolution electrocatalyst. J Electroanal Chem 799:235–241. https://doi.org/10.1016/j.jelechem.2017.05.050
Shen Y, Zhou Y, Wang D et al (2018) Nickel–copper alloy encapsulated in graphitic carbon shells as electrocatalysts for hydrogen evolution reaction. Adv Energy Mater 8:1–7. https://doi.org/10.1002/aenm.201701759
Shen Y, Lua AC, Xi J, Qiu X (2016) Ternary platinum–copper–nickel nanoparticles anchored to hierarchical carbon supports as free-standing hydrogen evolution electrodes. ACS Appl Mater Interfaces 8:3464–3472. https://doi.org/10.1021/acsami.5b11966
Wan L, Zhang J, Chen Y et al (2017) Varied hydrogen evolution reaction properties of nickel phosphide nanoparticles with different compositions in acidic and alkaline conditions. J Mater Sci 52:804–814. https://doi.org/10.1007/s10853-016-0377-7
Larbi KK, Barati M, McLean A (2011) Reduction behaviour of rice husk ash for preparation of high purity silicon. Can Metall Q 50:341–349
Barati M, Sarder S, McLean A, Roy R (2011) Recovery of silicon from silica fume. J Non-Cryst Solids 357:18–23
Larbi KK (2010) Synthesis of High Purity Silicon from Rice Husks; Master of Applied Science, Department of Materials Science and Engineering, University of Toronto
Shyu JZ, Otto K (1988) Identification of platinum phases on γ-alumina by XPS. Appl Surf Sci 32:246–252
Dupin J-C, Gonbeau D, Vinatier P, Levasseur A (2000) Systematic XPS studies of metal oxides, hydroxides and peroxides. Phys Chem Chem Phys 2:1319–1324
Sirtori V, Lombardi L, Cavallotti PL, Magagnin L (2003) Determination of correct composition in nickel–phosphorus films by XPS angle resolved technique. Appl Surf Sci 217:163–169
de Souza MO, Mendes FMT, de Souza RF, dos Santos JHZ (2004) XPS characterization of nickel-acetylacetonate impregnated in NaX and NaY zeolites. Microporous Mesoporous Mater 69:217–221
Biesinger MC, Payne BP, Lau LWM et al (2009) X-ray photoelectron spectroscopic chemical state quantification of mixed nickel metal, oxide and hydroxide systems. Surf Interface Anal 41:324–332
Şen F, Gökaǧaç G (2007) Different sized platinum nanoparticles supported on carbon: an XPS study on these methanol oxidation catalysts. J Phys Chem C 111:5715–5720
Yang J, Lu S, Kan S et al (2009) Electrochemical preparation of silicon nanowires from nanometre silica in molten calcium chloride. Chem Commun. https://doi.org/10.1039/b902029b
Abouatallah RM, Kirk DW, Thorpe SJ, Graydon JW (2001) Reactivation of nickel cathodes by dissolved vanadium species during hydrogen evolution in alkaline media. Electrochim Acta 47:613–621
Huot JY, Brossard L (1987) Time dependence of the hydrogen discharge at 70 C on nickel cathodes. Int J Hydrogen Energy 12:821–830
Rommal HEG, Moran PJ (1985) Time-dependent energy efficiency losses at nickel cathodes in alkaline water electrolysis systems. J Electrochem Soc 132:325
Laursen AB, Varela AS, Dionigi F et al (2012) Electrochemical hydrogen evolution: Sabatier’s principle and the volcano plot. J Chem Educ 89:1595–1599
Sarkar S, Peter SC (2018) An overview on Pd-based electrocatalysts for the hydrogen evolution reaction. Inorg Chem Front 5:2060–2080
Sial MAZG, Mateen M, Naz R et al (2023) Alloying platinum single atoms with nickel iron nanoalloys for high performance hydrogen evolution reaction. Int J Hydrogen Energy. https://doi.org/10.1016/j.ijhydene.2023.06.291
Mu R, Fu Q, Xu H et al (2011) Synergetic effect of surface and subsurface Ni species at Pt−Ni bimetallic catalysts for CO oxidation. J Am Chem Soc 133:1978–1986
Zoski CG (2007) Handbook of Electrochemistry. https://doi.org/10.1016/B978-044451958-0.50000-8
Anantharaj S, Kundu S (2019) Do the evaluation parameters reflect intrinsic activity of electrocatalysts in electrochemical water splitting? ACS Energy Lett 4:1260–1264
Roy SB, Akbar K, Jeon JH, Jerng S-K, Truong L, Kim K, Yi Y, Chun S-H (2019) Iridium on vertical graphene as an all-round catalyst for robust water splitting reactions. J Mater Chem A 7:20590–20596
Lasia A (2014) Electrochemical impedance spectroscopy and its applications. Springer, New York. https://doi.org/10.1007/978-1-4614-8933-7
Yang L, Lu S, Wang H et al (2017) The self-activation and synergy of amorphous Re nanoparticle–Si nanowire composites for the electrocatalytic hydrogen evolution. Electrochim Acta 228:268–273
Ensafi AA, Ghadirian F, Jafari-Asl M, Rezaei B (2018) WS2 grafted on silicon and nano-silicon particles etched: a high-performance electrocatalyst for hydrogen evolution reaction. J Iran Chem Soc 15:613–620
Khdary NH, Ghanem MA, Abdelsalam ME et al (2019) Copper–N–SiO2 nanoparticles catalyst for hydrogen evolution reaction. Int J Hydrogen Energy 44:22926–22935
Eiler K, Suriñach S, Sort J, Pellicer E (2020) Mesoporous Ni-rich Ni–Pt thin films: electrodeposition, characterization and performance toward hydrogen evolution reaction in acidic media. Appl Catal B 265:118597
Cui M, Wang F, Zhao W et al (2023) Plasma-synthesized platinum single atom and nanoparticle catalysts for high-current–density hydrogen evolution. Chem Eng J 460:141676
Jiang G, Zhang C, Liu X et al (2022) Electrocatalytic hydrogen evolution of highly dispersed Pt/NC nanoparticles derived from porphyrin MOFs under acidic and alkaline medium. Int J Hydrogen Energy 47:6631–6637
Chen T, Ye B, Dai H et al (2021) Ni-doped CoP/Co2P nanospheres as highly efficient and stable hydrogen evolution catalysts in acidic and alkaline mediums. J Solid State Chem 301:122299
Du Z, Wang Y, Li J, Liu J (2019) Facile fabrication of Pt–Ni alloy nanoparticles supported on reduced graphene oxide as excellent electrocatalysts for hydrogen evolution reaction in alkaline environment. J Nanopart Res 21:1–15
Xu W, Chang J, Cheng Y et al (2022) A multi-step induced strategy to fabricate core-shell Pt–Ni alloy as symmetric electrocatalysts for overall water splitting. Nano Res 15:965–971
Fu M, Zhang Q, Sun Y et al (2020) Ni–Fe nanocubes embedded with Pt nanoparticles for hydrogen and oxygen evolution reactions. Int J Hydrogen Energy 45:20832–20842
Lasia A (2002) Electrochemical impedance spectroscopy and its applications. In: Modern aspects of electrochemistry. Springer, pp 143–248
Shi H, Liu L, Shi Y et al (2019) Silicon monoxide assisted synthesis of Ru modified carbon nanocomposites as high mass activity electrocatalysts for hydrogen evolution. Int J Hydrogen Energy 44:11817–11823
Funding
Open access funding provided by The Science, Technology & Innovation Funding Authority (STDF) in cooperation with The Egyptian Knowledge Bank (EKB).
Author information
Authors and Affiliations
Contributions
MNE: methodology; resources; software; validation; visualization; roles/writing—original draft. MAAR: conceptualization; data curation; formal analysis; resources; supervision; validation; visualization; writing—review & editing. NHS: conceptualization; data curation; formal analysis; investigation; methodology; resources; software; validation; visualization; roles/writing—original draft. MAS: conceptualization; data curation; formal analysis; methodology; resources; supervision; validation; visualization; writing—review & editing.
Corresponding author
Ethics declarations
Conflict of interest
There are no conflicts to declare.
Additional information
Publisher's Note
Springer Nature remains neutral with regard to jurisdictional claims in published maps and institutional affiliations.
Supplementary Information
Below is the link to the electronic supplementary material.
Rights and permissions
Open Access This article is licensed under a Creative Commons Attribution 4.0 International License, which permits use, sharing, adaptation, distribution and reproduction in any medium or format, as long as you give appropriate credit to the original author(s) and the source, provide a link to the Creative Commons licence, and indicate if changes were made. The images or other third party material in this article are included in the article's Creative Commons licence, unless indicated otherwise in a credit line to the material. If material is not included in the article's Creative Commons licence and your intended use is not permitted by statutory regulation or exceeds the permitted use, you will need to obtain permission directly from the copyright holder. To view a copy of this licence, visit http://creativecommons.org/licenses/by/4.0/.
About this article
Cite this article
Elsodany, M.N., Abdel Rahim, M.A., Shalaby, N.H. et al. Nickel and/or platinum modified crystalline silicon–carbon composites and their electrochemical behaviour towards the hydrogen evolution reaction. J Appl Electrochem 54, 531–546 (2024). https://doi.org/10.1007/s10800-023-01988-8
Received:
Accepted:
Published:
Issue Date:
DOI: https://doi.org/10.1007/s10800-023-01988-8