Abstract
In the present work, a novel technique is introduced to enhance thermal conductivity of the surface by grinding process with predefined location of diamond abrasive particles on wheel surface. Grinding process with modified wheel led to an increase the bubble nucleation site formation and departure frequency in surface channels. For a more detailed study, grinding results were compared with the surface produced by the laser with the same morphology. Although both the structured surfaces revealed better heat transfer coefficient in comparison with to unstructured surface (grinding by 455% and laser by 348%), abrasive-structured surface present 130% improvement comparing the surface produced by laser for wall superheat of 10 K. The cause of this phenomenon is the formation of an oxide layer during the laser processing, which has led to a decrease in the thermal conductivity of the surface. This phenomenon was clearly detected by X-ray-spectroscopy mapping analysis, and to better understand it, the heating surfaces reached two consecutive critical heat flux. The result showed that after the first achieving CHF, the sample surface oxidizes, which leads to a decrease in the CHF and an increase in wall superheat. The hypothesis of formation of the oxide layer on the surface after CHF was also proved by static contact angle testing, which the angle increased from 115 to 133° after boiling. This 13.5% improvement was due to an increase in surface roughness stems from the formation of the oxide layer. Increasing the hydrophobicity of the surface led to a problem to facile water refilling (surface rewet ability) and capillary wicking of the surface and to delay the nucleation site formation, bubble formation, its growth, and finally departure frequency.
Graphical abstract
















Similar content being viewed by others
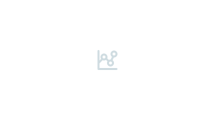
Availability of data and material
The authors confirm that the data supporting the findings of this study are available within the article [and/or] its supplementary materials.
Code availability
Not applicable.
References
Zhang BJ, Kim KJ, Lee CY (2018) Behavior of an Evaporating Water Droplet on Lubricant-impregnated Nano-structured Surface. Exp Thermal Fluid Sci. https://doi.org/10.1016/j.expthermflusci.2018.02.035
Patel D, Jain V, Ramkumar J (2016) Micro texturing on metallic surfaces: State of the art. Proc Inst Mech Eng Part B J Eng Manuf 232(6):941–964
Zhu Y, Antao D, Chu K et al (2016) Surface Structure Enhanced Microchannel Flow Boiling. J Heat Transf 138(9). https://doi.org/10.1115/1.4033497
Bourassia B, Brahim B (2020) Analysis of the evolution of the structure of a surface with pyramidal asperities in contact with a hard and smooth plane. J Heat Transf 141(1). https://doi.org/10.1115/1.4045303
Musavi SH, Adibi H, Rezaei SM (2022) Development of an innovative grinding process for producing functional surfaces. Tribol Int 173:107652. https://doi.org/10.1016/j.triboint.2022.107652
Kong L, Cheung Ch, To S (2012) Design, fabrication and characterization of three-dimensional patterned microstructured surfaces with self-cleaning properties from hydrophilic materials. Proc Inst Mech Eng Part B J Eng Manuf 226(9):1536–1549. https://doi.org/10.1177/0954405412447483
Wang M, Zi Y, Zhu J et al (2021) Construction of super-hydrophobic PDMS@MOF@Cu mesh for reduced drag, anti-fouling and self-cleaning towards marine vehicle applications. Chem Eng J 417:129265
Paik B, Pyun Y, Kim K et al (2015) Study on the micro-dimpled surface in terms of drag performance. Exp Thermal Fluid Sci 68:247–256
Park Ch, Kim T, Kim Y et al (2021) Supersonically sprayed transparent flexible multifunctional composites for self-cleaning, anti-icing, anti-fogging, and anti-bacterial applications. Compos B Eng 222:109070
Moon IY, Lee HW, Oh YS et al (2019) Characterization of microfibril development on PTFE surface during hot imprinting process and its application for oil–water separation. Int J Adv Manuf Technol 102:1871–1883. https://doi.org/10.1007/s00170-019-03303-2
Yang L, Luo X, Chang W et al (2020) Manufacturing of anti-fogging super-hydrophilic microstructures on glass by nanosecond laser. J Manuf Process 59:557–565. https://doi.org/10.1016/j.jmapro.2020.10.011
Hu H, Zhao Y, Lai Zh, Hu Ch (2021) Influence of surface wettability on pool boiling heat transfer on metal foam covers. Int J Therm Sci 168:107069
Tangwarodomnukun V, Kringram S, Zhu H et al (2021) Fabrication of superhydrophobic surface on AISI316L stainless steel using a nanosecond pulse laser. Proc Inst Mech Eng Part B J Eng Manuf. https://doi.org/10.1177/09544054211040682
Liu F, Han Y, Guo X et al (2021) Adhesion and machining performance of PVD AlCrN coatings with an ion beam/laser textured substrate. Surf Coat Technol 423:127607. https://doi.org/10.1016/j.surfcoat.2021.127607
Gao L, Zhou W, Wang Y (2016) Fabrication of hydrophobic structures on stent by direct three-beam laser interference lithography. Optik 127(13):5211–5214
Liang X, Liu Y, Chen Sh et al (2020) Fabrication of microplastic parts with a hydrophobic surface by micro ultrasonic powder moulding. J Manuf Process 56:180–188. https://doi.org/10.1016/j.jmapro.2020.04.086
Musavi SH, Davoodi B, Niknam SA (2019) Effects of reinforced nanofluid with nanoparticles on cutting tool wear morphology. J Cent South Univ 26:1050–1064. https://doi.org/10.1007/s11771-019-4070-2
Musavi SH, Davoodi B, Niknam SA (2018) Environmental-friendly turning of A286 superalloy. J Manuf Process 32:734–743. https://doi.org/10.1016/j.jmapro.2018.04.005
Hatami O, Adibi H, Rezaei SM (2022) Evaluation of the grinding process utilizing an auxiliary compressed air jet on cleaning the grinding wheel surface. Proc Inst Mech Eng Part E J Process Mech Eng. https://doi.org/10.1177/09544089221109835
Esmaeili H, Adibi H, Rezaei SM (2021) Study on surface integrity and material removal mechanism in eco-friendly grinding of Inconel 718 using numerical and experimental investigations. Int J Adv Manuf Technol 112:1797–1818. https://doi.org/10.1007/s00170-020-06528-8
Hatami O, Adibi H, Rezaei SM (2022) Application of a compressed air jet for cleaning of wheel surface in grinding nickel-based super alloy Inconel 718. CIRP J Manuf Sci Technol 37:233–244. https://doi.org/10.1016/j.cirpj.2022.02.004
Bayat M, Adibi H, Barzegar A, Rezaei SM (2022) Experimental and numerical investigation of heat generation and surface integrity of ZrO2 bioceramics in grinding process under MQL condition. J Mech Behav Biomed Mater 131:105226. https://doi.org/10.1016/j.jmbbm.2022.105226
Zhang X, Zhang Zh, Deng Zh et al (2019) Precision grinding of silicon nitride ceramic with laser macro-structured diamond wheels. Opt Laser Technol 109:418–428
Daneshi A, Muller K, Azarhoushang B. Cylindrical plunge grinding of twist free surfaces by structured wheels. Precision Eng. https://doi.org/10.1016/j.precisioneng.2017.10.003
Zhang Zh, Yao P, Wang J (2021) The mechanisms of high-efficiency grinding for micro/meso-structural arrays on ceramic moulds through an innovative wheel truing technology. Ceram Int 47:27624–27638
Gupta S, Misra R (2020) Development of micro/nanostructured-Cu-TiO2-nanocomposite surfaces to improve pool boiling heat transfer performance. Heat Mass Transf 56:2529–2544. https://doi.org/10.1007/s00231-020-02878-x
Ranjan A, Ahmad I, Kumar R et al (2022) Enhancement of critical heat flux (CHF) in pool boiling with anodized copper surfaces. Int J Thermal Sci 172(B):107338
Rajabzadeh F, Haghshenasfard M, Esfahany MN et al (2018) Experimental investigation of time and repeated cycles in nucleate pool boiling of alumina/water nanofluid on polished and machined surfaces. Heat Mass Transf 54:1653–1668. https://doi.org/10.1007/s00231-017-2266-2
Arya H, Sarafraz MM, Arjomandi M (2019) Pool boiling under the magnetic environment: experimental study on the role of magnetism in particulate fouling and bubbling of iron oxide/ethylene glycol nano-suspension. Heat Mass Transf 55:119–132. https://doi.org/10.1007/s00231-018-2438-8
Chen W, Wang J (2017) Experimental analysis of nanofluid pool boiling heat transfer in copper bead packed porous layers. Heat Mass Transf 53:877–885. https://doi.org/10.1007/s00231-016-1854-x
Lu YM, Kandlikar SG (2011) Nanoscale surface modification techniques for pool boiling enhancement-a critical review and future directions. Heat Transfer Eng 32:827–842
Mohanty RL, Das MK (2017) A critical review on bubble dynamics parameters influencing boiling heat transfer. Renew Sustain Energy Rev 78:466–494
Agostini B, Fabbri M, Park JE et al (2007) Michel, State of the art of high heat flux cooling technologies. Heat Transfer Eng 28:258–281
Natali M, Kenny JM, Torre L (2016) Science and technology of polymeric ablative materials for thermal protection systems and propulsion devices: a review. Prog Mater Sci 84:192–275. https://doi.org/10.1016/j.pmatsci.2016.08.003
Rahman MM, Dongxu J, Beni MS et al (2016) Supercritical water heat transfer for nuclear reactor applications: a review. Ann Nucl Energy 97:53–65. https://doi.org/10.1016/j.anucene.2016.06.022
Serdyukov V, Starinskiy S, Malakhov I et al (2021) Laser texturing of silicon surface to enhance nucleate pool boiling heat transfer. Appl Therm Eng 194:117102. https://doi.org/10.1016/j.applthermaleng.2021.117102
Gouda R, Pathak M, Khan M (2018) Pool boiling heat transfer enhancement with segmented finned microchannels structured surface. Int J Heat Mass Transf 127(A):39–50. https://doi.org/10.1016/j.ijheatmasstransfer.2018.06.115
Musavi SH, Davoodi B, Nankali M (2021) Assessment of Tool Wear and Surface Integrity in Ductile Cutting Using a Developed Tool. Arab J Sci Eng 46:7773–7787. https://doi.org/10.1007/s13369-021-05560-4
Musavi SH, Sepehrikia M, Davoodi B (2022) Performance analysis of developed micro-textured cutting tool in machining aluminum alloy 7075–T6: assessment of tool wear and surface roughness. Int J Adv Manuf Technol 119:3343–3362. https://doi.org/10.1007/s00170-021-08349-9
Musavi SH, Davoodi B, Niknam SA (2021) Eco-green machining of superalloy A286: Assessment of tool wear morphology and surface topology. Proc Inst Mech Eng Part B J Eng Manuf 235(9):1412–1424. https://doi.org/10.1177/0954405421995618
Musavi SH, Davoodi B, Eskandari B (2020) Evaluation of surface roughness and optimization of cutting parameters in turning of AA2024 alloy under different cooling-lubrication conditions using RSM method. Journal of Central South University 27:1714–1728. https://doi.org/10.1007/s11771-020-4402-2
Musavi SH, Davoodi B (2021) Risk assessment for hazardous lubricants in machining industry. Environ Sci Pollution Res 28:625–634. https://doi.org/10.1007/s11356-020-10472-1
Musavi SH, Davoodi B, Niknam SA (2019) Effects of reinforced nanoparticles with surfactant on surface quality and chip formation morphology in MQL-turning of superalloys. J Manuf Process 40(128–139):1526–6125. https://doi.org/10.1016/j.jmapro.2019.03.014
Jafari R, Cloutier C, Allahdini A et al (2019) Recent progress and challenges with 3D printing of patterned hydrophobic and superhydrophobic surfaces. Int J Adv Manuf Technol 103:1225–1238. https://doi.org/10.1007/s00170-019-03630-4
Ivey HJ (1967) Relationships between bubble frequency, departure diameter, and rise velocity in nucleate boiling. Int J Heat Mass Transf 10:1023–1040. https://doi.org/10.1016/0017-9310(67)90118-4
Author information
Authors and Affiliations
Contributions
The research results in this work were presented in the Ph.D. thesis of Mr. Musavi. S.H. Musavi designed and performed experiments, analysed data and wrote the paper. Dr. Adibi and Dr. Rezaei also acted as the supervisors of Mr. Musavi. All authors have read and agreed to the published version of the manuscript.
Corresponding author
Ethics declarations
Ethics approval
Not applicable.
Consent to participate
Not applicable.
Consent for publication
All authors permit the publisher to publish the work.
Conflicts of interest
The authors declare no conflict of interest. The funders had no role in the design of the study, in the collection, analyses, or interpretation of data, in the writing of the manuscript, or in the decision to publish the results.
Additional information
Publisher's Note
Springer Nature remains neutral with regard to jurisdictional claims in published maps and institutional affiliations.
Highlights
• Structured surfaces were manufactured by laser engraving and a modified grinding process, and their results were compared.
• Up to 455% improvement was observed in the heat transfer coefficient for surface produced by grinding process compared to the as-received samples at wall superheat of 10 K, in addition, it improvement comparing the surface produced by laser was 130%.
• The best HTC improvement has been achieved at the wall superheat about 9 K.
• The HTC for second achieving the critical heat flux was approximately 17% less than first one.
• The X-ray spectroscopy showed that after achieving the first CHF, the surface is severely oxidized. It leads to a decrease in heat transfer coefficient.
• A 3.4 times improvement in bubble diameter and a 2.2 times improvement in bubble departure frequency are the main reasons for the enhanced heat transfer conditions of abrasive-structured surface.
• The reason for the superiority of the grinding method for improving the thermal conductivity over the laser process can be attributed to the lack of oxide layer formation.
Rights and permissions
Springer Nature or its licensor holds exclusive rights to this article under a publishing agreement with the author(s) or other rightsholder(s); author self-archiving of the accepted manuscript version of this article is solely governed by the terms of such publishing agreement and applicable law.
About this article
Cite this article
Musavi, S.H., Adibi, H. & Rezaei, S.M. An experimental study on bubble dynamics and pool boiling heat transfer of grinding/laser-structured surface. Heat Mass Transfer 59, 681–698 (2023). https://doi.org/10.1007/s00231-022-03287-y
Received:
Accepted:
Published:
Issue Date:
DOI: https://doi.org/10.1007/s00231-022-03287-y