Abstract
Cylindrical grinding is an important way to form the external shape error of the crank journal, and the accuracy consistency directly affects the interchangeability of products. To study the accuracy consistency of crank journal, a dynamic model of the grinding wheel-crankshaft grinding system based on Timoshenko beam is established, and the grinding transition process simulation algorithm with iterative convergence of grinding force-transient grinding amount cycle adapted to the model is proposed, which realizes the simulation of the roundness of the crank journal coupled with the process parameters of the grinding system. Aiming at the grinding position of each crank journal, the grinding roundness of five crank journals is simulated, respectively. On this basis, the crank journal roundness consistency prediction model is established, and the effectiveness of the prediction model is verified by field experiments. Finally, the influence of grinding parameters on the consistency of the roundness of crank journal is studied. The research conclusion can provide a reference for the grinding accuracy consistency design of this type of crank journal.

















Similar content being viewed by others
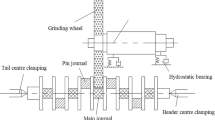
References
Liu HF, Zhou XZ, Qiu-Ming YU (2015) Modes and causes of torsional fatigue failure of automobile engine crankshafts. Fail Ana Prev 42(24):8606–8616. https://doi.org/10.1039/c3dt00115f
Kareem B (2017) Mechanical failure analysis of automobile crankshafts under service reconditioned modelling approach. Eng Fail Anal. https://doi.org/10.1016/j.engfailanal.2017.05.036
Shi X, Xiu S, Meng Z (2019) Research on machining topography of point grinding based on correlation function method. Proc Inst Mech Eng Part B J Eng Manuf 233:850–862. https://doi.org/10.1177/0954405418755827
Fan ZG, Gong YD, Dong Y (2011) Research on surface morphology of three-dimensional in CNC cylindrical grinding. Adv Mater Res 299–300:945–948. https://doi.org/10.4028/www.scientific.net/AMR.299-300.945
Yuan J, Yao W, Zhao P (2015) Kinematics and trajectory of both-sides cylindrical lapping process in planetary motion type. Int J Mach Tools Manuf 92:60–71. https://doi.org/10.1016/j.ijmachtools.2015.02.004
Yao W, Yuan J, Zhou F (2016) Trajectory analysis and experiments of both-sides cylindrical lapping in eccentric rotation. Int J Adv Manuf Technol 88:1–11. https://doi.org/10.1007/s00170-016-8980-y
Yuan JL, Lou FY, Wang ZW (2004) Research on ultra-precision machining technology for KTP. Mater Sci Forum 473–476. https://doi.org/10.4028/www.scientific.net/MSF.471-472.473
Lv BH, Yuan JL, Yao YX (2006) Study on wear mode of silicon nitride balls in lapping process. Key Eng Mater 403–407. https://doi.org/10.4028/www.scientific.net/KEM.304-305.403
Wang WF, Gao PF, Wen DH (2010) Theoretical analysis and uniformity of trajectories in lapping process. Adv Mater Res 102:625–629. https://doi.org/10.4028/www.scientific.net/AMR.102-104.625
Zhang J, Wang WF, Wen DH (2011) Methods of evaluation the uniformity in the lapping process. Adv Mater Res 215:47–52. https://doi.org/10.4028/www.scientific.net/AMR.215.47
Chen S, Yang S, Liao Z (2021) Curvature effect on surface generation and uniform scallop height control in normal grinding of optical components. Opt Express 29(6). https://doi.org/10.1364/OE.418599
Liu Z, Jin Z, Wu D (2019) Investigation on material removal uniformity in electrochemical mechanical polishing by polishing pad with holes. Ecs J Solid State Sci Technol 8(5):3047–3052. https://doi.org/10.1149/2.0071905jss
Wei H, Peng C, Hang G (2018) On establishment and validation of a new predictive model for material removal in abrasive flow machining. Int J Mach Tools Manuf 138. https://doi.org/10.1016/j.ijmachtools.2018.12.003
Zhou W, Tang J, Shao W (2020) Study on surface generation mechanism and roughness distribution in gear profile grinding. Int J Mech Sci 187. https://doi.org/10.1016/j.ijmecsci.2020.105921
Pavlenko I, Saga M, Kuric I (2020) Parameter identification of cutting forces in crankshaft grinding using artificial neural networks. Materials 13(23):5357. https://doi.org/10.3390/ma13235357
Yu H, Zhang W, Lyu Y (2019) Research on grinding forces of a bionic engineered grinding wheel. J Manuf Process 48:185–190. https://doi.org/10.1016/j.jmapro.2019.10.031
Rudrapati R, Pal PK, Bandyopadhyay A (2016) Modeling and optimization of machining parameters in cylindrical grinding process. Int J Adv Manuf Technol 9:2167–2182. https://doi.org/10.1007/s00170-015-7500-9
Fujiwara T, Tsukamoto S, Miyagawa M (2005) Analysis of the grinding mechanism with wheel head oscillating type CNC crankshaft pin grinder. Key Eng Mater 291:163–170. https://doi.org/10.4028/www.scientific.net/KEM.291-292.163
Xiong W, Chen J, Ding W (2019) Dual-rotor coupling model and simulation algorithm for round journal grinding process. Chin J Mech Eng 55(21):170–177. https://doi.org/10.3901/JME.2019.21.170
Zeng X, Xiong W, Sun W (2021) Research on double-rotor dynamic grinding model and simulation algorithm for crankshaft main journal. Int J Adv Manuf Technol 1–10. https://doi.org/10.1007/s00170-021-06761-9
Hou Z, Xiong W, Lang L (2016) Study on the influence of the journal shape error for hydrostatic spindle rotational error motion. Chin J Mech Eng 52(15):147–154. https://doi.org/10.3901/JME.2016.15.147
Zhang Y, Yang B (2020) Medium-frequency vibration analysis of Timoshenko beam structures. Int J Struct Stab Dyn 2041009. https://doi.org/10.1142/S0219455420410096
Nelson HD (1980) A finite rotating shaft element using Timoshenko beam theory. J Mech Des 102:793–803. https://doi.org/10.1115/1.3254824
Lai HY, Jywe WY, Chen CK (2000) Precision modeling of form errors for cylindricity evaluation using genetic algorithms. Precis Eng 24:310–319. https://doi.org/10.1016/S0141-6359(00)00041-6
Kumar C, Sarangi S (2017) Dynamic response of unbalanced rigid rotor bearing system with non-linear hydrodynamic force. J Comput Nonlinear Dyn 13(9). https://doi.org/10.1115/1.4037995
Chiu N, Malkin S (1993) Computer simulation for cylindrical plunge grinding. CIRP Ann Manuf Technol 42(1):383–387. https://doi.org/10.1016/S0007-8506(07)62467-6
Zhou J, Zhou Y (2007) A new simple method of implicit time integration for dynamic problems of engineering structures. Acta Mech Sin 1(v.23):95–103. https://doi.org/CNKI:SUN:AMSI.0.2007-01-010
Lei X, Gao Z, Duan M (2015) Method for cylindricity error evaluation using geometry optimization searching algorithm. Precis Eng 44(9):1556–1563. https://doi.org/10.1016/j.measurement.2011.06.010
Anandan KP, Ozdoganlar OB (2013) An ldv-based methodology for measuring axial and radial error motions when using miniature ultra-high-speed (uhs) micromachining spindles. Precis Eng 37(1):172–186. https://doi.org/10.1016/j.precisioneng.2012.08.001
Fricker DC, Speight A, Pearce TRA (2006) The modelling of roundness in cylindrical plunge grinding to incorporate wave shift and external vibration effects. Proc Inst Mech Eng Part B J Eng Manuf 220(8):1347–1358. https://doi.org/10.1243/09544054JEM509
Pearce TRA, Flicker DC, Speight A (2007) The effect of workpiece roundness of the run-out of CBN electroplated grinding wheels. Key Eng Mater 329:483–488. https://doi.org/10.4028/www.scientific.net/KEM.329.483
Funding
This work was financially supported by the National Natural Science Foundation of China (Grant No. 51575173) and the Science and Technology Major Project-Advanced NC Machine Tools &Basic Manufacturing Equipment (Grant No. 2016ZX04003001).
Author information
Authors and Affiliations
Corresponding author
Ethics declarations
Ethics approval
Not applicable.
Consent to participate
Not applicable.
Consent for publication
Not applicable.
Competing interests
The authors declare no competing interests.
Additional information
Publisher's note
Springer Nature remains neutral with regard to jurisdictional claims in published maps and institutional affiliations.
Rights and permissions
About this article
Cite this article
Zeng, X., Xiong, W., Ye, H. et al. Research on roundness error consistency model for crank journal cylindrical grinding. Int J Adv Manuf Technol 120, 3705–3717 (2022). https://doi.org/10.1007/s00170-022-08738-8
Received:
Accepted:
Published:
Issue Date:
DOI: https://doi.org/10.1007/s00170-022-08738-8