Abstract
Nickel-based alloys are classified as difficult-to-cut metals due to their low thermal conductivity and strength even at high temperatures. The crucial challenge when turning these alloys is the obtainment of a high surface integrity since they are often used in critical applications like aerospace and oil and gas ones. This is usually fulfilled using cutting fluids that may lead to ecological and health-related issues as well as increase of the production costs. In this context, the paper evaluates the feasibility of sustainable turning of the Inconel 718 alloy using the minimum quantity lubrication strategy based on graphene nanofluids. Graphene nanoplatelets of two sizes, namely 5 μm and 15 μm, were used as additives to a vegetable oil to form nanofluids. The effectiveness of using nanofluids with the respect to dry, flood, and pure minimum quantity lubrication strategies was investigated at different cutting speeds. Results showed that the nanofluid with the lowest size of graphene nanoplatelets promoted the best surface quality assuring a 6% and 15% reduction in surface roughness at the highest and lowest cutting speed, respectively, compared to flood condition that represents the current machining standard. In addition, the use of the graphene nanoplatelets of the lowest size promoted the formation of a 23% thicker severe plastic deformed layer compared to the flood case at the highest cutting speed. These findings prove that the nanoparticles’ efficiency as additives in a metalworking fluid depends on their size, which, in turn, influences their thermo-physical characteristics.
















Similar content being viewed by others
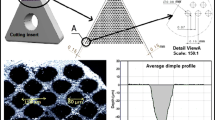
References
Pusavec F, Krajnik P, Kopac J (2010) Transitioning to sustainable production - Part I: application on machining technologies. J Clean Prod 18:174–184. https://doi.org/10.1016/j.jclepro.2009.08.010
Shokrani A, Dhokia V, Newman ST (2017) Hybrid cooling and lubricating technology for CNC milling of Inconel 718 nickel alloy. Procedia CIRP 11:625–632. https://doi.org/10.1016/j.promfg.2017.07.160
Brinksmeier E, Walter A, Jansscn R, Diersen P (1999) Aspects of cooling lubrication reduction in machining advanced materials. Proc Inst Mech Eng Part B J Eng Manuf 213:769–778. https://doi.org/10.1016/j.promfg.2017.07.160
Howes T (1990) Assessment of the cooling and lubricative properties of grinding fluids. CIRP Ann 39(1):313–316. https://doi.org/10.1016/S0007-8506(07)61061-0
Cholakov GS, Guest TL, Rowe GW (1992) Lubricating properties of grinding fluids: 1. Comparison of fluids in surface grinding experiments. Lubr Eng 48:155–163
Soković M, Mijanović K (2001) Ecological aspects of the cutting fluids and its influence on quantifiable parameters of the cutting processes. J Mater Process Technol 109:181–189. https://doi.org/10.1016/S0924-0136(00)00794-9
Krajnik P, Pusavec F, Rashid A (2011). Nanofluids: properties, applications and sustainability aspects in materials processing technologies. In Advances in sustainable manufacturing (pp. 107-113). Springer, Berlin, Heidelberg. https://doi.org/10.1007/978-3-642-20183-7_16
Da Silva LR, Bianchi EC, Fusse RY, Catai RE, Franca TV, Aguiar PR (2007) Analysis of surface integrity for minimum quantity lubricant—MQL in grinding. Int J Mach Tools Manuf 47(2):412–418. https://doi.org/10.1016/j.ijmachtools.2006.03.015
Krolczyk GM, Maruda RW, Krolczyk JB, Wojciechowski S, Mia M, Nieslony P, Budzik G (2019) Ecological trends in machining as a key factor in sustainable production–a review. J Clean Prod 218:601–615. https://doi.org/10.1016/j.jclepro.2019.02.017
Maruda RW, Krolczyk GM, Wojciechowski S, Zak K, Habrat W, Nieslony P (2018) Effects of extreme pressure and anti-wear additives on surface topography and tool wear during MQCL turning of AISI 1045 steel. J Mech Sci Technol 32(4):1585–1591. https://doi.org/10.1007/s12206-018-0313-7
Maruda RW, Krolczyk GM, Wojciechowski S, Powalka B, Klos S, Szczotkarz N, Matuszak M, Khanna N (2020) Evaluation of turning with different cooling-lubricating techniques in terms of surface integrity and tribologic properties. Tribol Int 106334:106334. https://doi.org/10.1016/j.triboint.2020.106334
Krolczyk GM, Maruda RW, Krolczyk JB, Nieslony P, Wojciechowski S, Legutko S (2018) Parametric and nonparametric description of the surface topography in the dry and MQCL cutting conditions. Measurement. 121:225–239. https://doi.org/10.1016/j.measurement.2018.02.052
Singh R, Dureja JS, Dogra M, Gupta MK, Mia M, Song Q (2020) Wear behavior of textured tools under graphene-assisted minimum quantity lubrication system in machining Ti-6Al-4 V alloy. Tribol Int 145:106183. https://doi.org/10.1016/j.triboint.2020.106183
Rahman SS, Ashraf MZI, Amin AN, Bashar MS, Ashik MFK, Kamruzzaman M (2019) Tuning nanofluids for improved lubrication performance in turning biomedical grade titanium alloy. J Clean Prod 206:180–196. https://doi.org/10.1016/j.jclepro.2018.09.150
Ali MAM, Azmi AI, Khalil ANM (2018) Specific cutting energy of Inconel 718 under dry, chilled-air and minimal quantity nanolubricants. Procedia CIRP 77:429–432. https://doi.org/10.1016/j.procir.2018.08.290
Bryant PJ, Gutshall PL, Taylor LH (1964) A study of mechanisms of graphite friction and wear. Wear 7(1):118–126. https://doi.org/10.1016/0043-1648(64)90083-3
Jamil M, Khan AM, Hegab H, Gupta MK, Mia M, He N, Zhao G, Song Q, Liu Z (2020) Milling of Ti–6Al–4 V under hybrid Al2O3-MWCNT nanofluids considering energy consumption, surface quality, and tool wear: a sustainable machining. Int J Adv Manuf Technol 107(9-10):4141–4157. https://doi.org/10.1007/s00170-020-05296-9
Khan AM, Gupta MK, Hegab H, Jamil M, Mia M, He N, Song Q, Liu Z, Pruncu CI (2020) Energy-based cost integrated modelling and sustainability assessment of Al-GnP hybrid nanofluid assisted turning of AISI52100 steel. J Clean Prod 257:120502. https://doi.org/10.1016/j.jclepro.2020.120502
Yi S, Mo J, Ding S (2019) Experimental investigation on the performance and mechanism of graphene oxide nanofluids in turning Ti-6Al-4V. J Manuf Process 43:164–174. https://doi.org/10.1016/j.jmapro.2019.05.005
Gutnichenko O, Bushlya V, Bihagen S, Ståhl JE (2018) Influence of GnP additive to vegetable oil on machining performance when MQL-assisted turning alloy 718. Procedia Manuf 25:330–337. https://doi.org/10.1016/j.promfg.2018.06.091
Hegab H, Umer U, Soliman M, Kishawy HA (2018) Effects of nano-cutting fluids on tool performance and chip morphology during machining Inconel 718. Int J Adv Manuf Technol 96:3449–3458. https://doi.org/10.1007/s00170-018-1825-0
Alberts M, Kalaitzidou K, Melkote S (2009) An investigation of graphite nanoplatelets as lubricant in grinding. Int J Mach Tools Manuf 49:966–970. https://doi.org/10.1016/j.ijmachtools.2009.06.005
Marcon A, Melkote S, Kalaitzidou K, Debra D (2010) An experimental evaluation of graphite nanoplatelet based lubricant in micro-milling. CIRP Annals - Manu Techno 59:141–144. https://doi.org/10.1016/j.cirp.2010.03.083
Standard ASTM (2010) E112–10. Standard test method for determining average grain size. ASTM International, West Conshohocken, Pa
Calleja A, Urbikain G, González H, Cerrillo I, Polvorosa R, Lamikiz A (2018) Inconel® 718 superalloy machinability evaluation after laser cladding additive manufacturing process. Int J Adv Manuf Technol 97:2873–2885. https://doi.org/10.1007/s00170-018-2169-5
Ren X, Liu Z (2016) Influence of cutting parameters on work hardening behavior of surface layer during turning superalloy Inconel 718. Int J Adv Manuf Technol 86:2319–2327. https://doi.org/10.1007/s00170-016-8350-9
Behera BC, Alemayehu H, Ghosh S, Rao PV (2017) A comparative study of recent lubri-coolant strategies for turning of Ni-based superalloy. J Manuf Process 30:541–552. https://doi.org/10.1016/j.jmapro.2017.10.027
Teng TP, Hung YH (2014) Estimation and experimental study of the density and specific heat for alumina nanofluid. J Exp Nanosci 9:707–718. https://doi.org/10.1080/17458080.2012.696219
ISO I (2012) 25178-2: 2012—Geometrical product specifications (GPS)—surface texture: areal—Part 2: Terms, Definitions and Surface Texture Parameters. Geneva, Switzerland, International Standards Organization
American Society for Testing and Materials (2017) ASTM E384: standard test method for microindentation hardness of materials. ASTM, West Conshohocken
Zaman PB, Dhar NR (2019) Design and evaluation of an embedded double jet nozzle for MQL delivery intending machinability improvement in turning operation. J Manuf Process 44:179–196. https://doi.org/10.1016/j.jmapro.2019.05.047
Khan A, Maity K (2017) Comparative study of some machinability aspects in turning of pure titanium with untreated and cryogenically treated carbide inserts. J Manuf Process 28:272–284. https://doi.org/10.1016/j.jmapro.2017.05.018
Xiong S, Qi W, Cheng Y, Huang B, Wang M, Li Y (2011) Universal relation for size dependent thermodynamic properties of metallic nanoparticles. Phys Chem Chem Phys 13(22):10652–10660. https://doi.org/10.1039/C0CP90161J
Yıldırım ÇV, Sarıkaya M, Kıvak T, Şirin Ş (2019) The effect of addition of hBN nanoparticles to nanofluid-MQL on tool wear patterns, tool life, roughness and temperature in turning of Ni-based Inconel 625. Tribol Int 134:443–456. https://doi.org/10.1016/j.triboint.2019.02.027
Özbek O, Saruhan H (2020) The effect of vibration and cutting zone temperature on surface roughness and tool wear in eco-friendly MQL turning of AISI D2. J Mater Res Technol 9(3):2762–2772. https://doi.org/10.1016/j.jmrt.2020.01.010
Liu W, Do IH, Fukushima H, Drzal LT (2010) Influence of processing on morphology, electrical conductivity and flexural properties of exfoliated graphite nanoplatelets-polyamide nanocomposites. Carbon Lett 11(4):279–284. https://doi.org/10.5714/CL.2010.11.4.279
Trent EM (1988) Metal cutting and the tribology of seizure: II movement of work material over the tool in metal cutting. Wear 128:47–64. https://doi.org/10.1016/0043-1648(88)90252-9
Khan MMA, Mithu MAH, Dhar NR (2009) Effects of minimum quantity lubrication on turning AISI 9310 alloy steel using vegetable oil-based cutting fluid. J Mater Process Technol 209:5573–5583. https://doi.org/10.1016/j.jmatprotec.2009.05.014
Sartori S, Ghiotti A, Bruschi S (2017) Temperature effects on the Ti6Al4V machinability using cooled gaseous nitrogen in semi-finishing turning. J Manuf Process 30:187–194. https://doi.org/10.1016/j.jmapro.2017.09.025
Zhou JM, Bushlya V, Stahl JE (2012) An investigation of surface damage in the high speed turning of Inconel 718 with use of whisker reinforced ceramic tools. J Mater Process Technol 212(2):372–384. https://doi.org/10.1016/j.jmatprotec.2011.09.022
Zhou J, Bushlya V, Peng RL, Chen Z, Johansson S, Stahl JE (2014) Analysis of subsurface microstructure and residual stresses in machined Inconel 718 with PCBN and Al2O3-SiCw tools. Procedia CIRP 13:150–155. https://doi.org/10.1016/j.procir.2014.04.026
Umbrello D (2013) Investigation of surface integrity in dry machining of Inconel 718. Int J Adv Manuf Technol 69:2183–2190. 9:2. https://doi.org/10.1007/s00170-013-5198-0
Pusavec F, Hamdi H, Kopac J, Jawahir IS (2011) Surface integrity in cryogenic machining of nickel based alloy—Inconel 718. J Mater Process Technol 211(4):773–783. https://doi.org/10.1016/j.jmatprotec.2010.12.013
Jawahir IS, Van Luttervelt CA (1993) Recent developments in chip control research and applications. CIRP Ann 42(2):659–693. https://doi.org/10.1016/S0007-8506(07)62531-1
Behera BC, Ghosh S, Rao PV (2016) Application of nanofluids during minimum quantity lubrication: a case study in turning process. Tribol Int 101:234–246. https://doi.org/10.1016/j.triboint.2016.04.019
Ahammed N, Asirvatham LG, Wongwises S (2016) Effect of volume concentration and temperature on viscosity and surface tension of graphene–water nanofluid for heat transfer applications. J Therm Anal Calorim 123(2):1399–1409. https://doi.org/10.1007/s10973-015-5034-x
Peng DX, Kang Y, Hwang RM, Shyr SS, Chang YP (2009) Tribological properties of diamond and SiO2 nanoparticles added in paraffin. Tribol Int 42:911–917. https://doi.org/10.1016/j.triboint.2008.12.015
Acknowledgments
The authors wish to acknowledge with the financial support of this research by China Scholarship Council (grant no. 201906830023) and Nanjing University of Aeronautics and Astronautics PhD short-term visiting scholar project (grant no. 190114DF05).
Author information
Authors and Affiliations
Corresponding author
Additional information
Publisher’s note
Springer Nature remains neutral with regard to jurisdictional claims in published maps and institutional affiliations.
Rights and permissions
About this article
Cite this article
Gong, L., Bertolini, R., Ghiotti, A. et al. Sustainable turning of Inconel 718 nickel alloy using MQL strategy based on graphene nanofluids. Int J Adv Manuf Technol 108, 3159–3174 (2020). https://doi.org/10.1007/s00170-020-05626-x
Received:
Accepted:
Published:
Issue Date:
DOI: https://doi.org/10.1007/s00170-020-05626-x