Abstract
To address defects in the recast layer and microcracks in laser drilling, this study adopted laser-electrolytic composite machining technology to conduct a boring test on nickel-based superalloy In718 through flushing outside the ring electrode and hydrostatic machining. This method obtained the characteristics of recast layer removal via composite machining and identified the influence rule of the residual rate of the recast layer via composite machining parameters. Results show that the recast layer exhibits a random distribution and gathers together at the exit when adopting the laser to rotationally cut and make the hole. Electrolytic post-processing for laser prefabricated small holes with a diameter larger than 1 mm by flushing outside the ring electrode proceeded as follows: using an electrolytic voltage of 20 V, NaNO3 electrolyte of 7.5 g/L, and electrolytic machining time of 20s, the reaming amount can reach 70–100 μm and steadily achieve recast layer removal. Electrolytic post-processing for prefabricated small holes with a diameter smaller than 1 mm can be carried out using hydrostatic machining under different flushing methods (continuous static electrolyte machining, free flushing, and forced flushing), indicating that forced flushing can remove the recast layers of the holes and achieve a better hole shape to create holes with good inwall quality.
Similar content being viewed by others
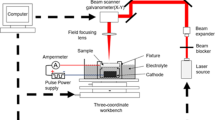
References
Tagliaferri F, Genna S, Leone C, Palumbo B, De Chiara G (2017) Experimental study of fibre laser microdrilling of aerospace superalloy by trepanning technique. Int J Adv Manuf Technol 93:3203–3210. https://doi.org/10.1007/s00170-017-0773-4
Leone C, Genna S, Caggiano A, Tagliaferri V, Molitierno R (2016) Influence of process parameters on kerf geometry and surface roughness in Nd: YAG laser cutting of Al 6061T6 alloy sheet. Int J Adv Manuf Technol 87:2745–2762
Daxiang L, Jie J (2004) The development trends and prospect of world aero propulsion technology in the 21st century. Eng Sci 6(9):1–8
Guo W, Wang M, Xiaobing Z (2003) Recast layer formed by laser drilling of Ni-based superalloys and progress on its control. J Laser 24(4):1–3
Biffi CA, Previtali B (2013) Spatter reduction in nanosecond fibre laser drilling using an innovative nozze. Int J Adv Manuf Technol 66:1231–1245
Przestacki D, Kuklinski M, Bartkowska A (2017) Influence of laser heat treatment on microstructure and properties of surface layer of Waspaloy aimed for laser-assisted machining. Int J Adv Manuf Technol 93:3111–3123. https://doi.org/10.1007/s00170-017-0775-2
Changjun C, Wenyuan G, Maocai W, Xiaobing Z (2004) An experimental study on the chemical etching of the remelt layers formed on Ni-based superalloy. Gas Turbine Exp Res 17(3):44–50
Zhang Y, Xu Z, Di Zhu NQ (2016) Drilling of film cooling holes by a EDM/ECM in situ combined process using internal and side flushing of tubular electrode. Int J Adv Manuf Technol 83:505–517
Caiazzo F, Alfieri V, Corrado G, Argenio P (2017) Laser powder-bed fusion of Inconel 718 to manufacture turbine blades. Int J Adv Manuf Technol 93:4023–4031. https://doi.org/10.1007/s00170-017-0839-3
Jain VK, Lal GK, Kanetkar Y (2005) Stray current attack and stagnation zones in electrochemical drilling. Int J Adv Manuf Technol 26(5–6):527–536
Kurita T, Hattori M (2006) A study of EDM and ECM/ECM-lapping complex machining technology. Int J Mach Tools and Manuf 46(14):1804–1810
Low DKY, Li L, Byrd PJ (2003) Spatter prevention during the laser drilling of selected aerospace materials. J Mater Pro Technol 139(1–3):71–76
Xiao C, Rongqing X, Zhonghua S (2000) Influence of assisted gas on laser drilling. J Laser 21(6):44–46
Xiao C, Rongqing X, Zhonghua S (2004) Mechanisms of laser processing in water and air. J Nanjing Univ Sci Technol 28(3):248–252
Zhu XS, Choi JW, Cole R, Ahn CH (2002) A new laser micromachining technique using a mixed-mode ablation approach. The Fifteenth IEEE International Conference on MICRO Electro Mechanical Systems. IEEE:152–155
Nguyen MD, Rahman M, Wong YS (2013) Modeling of radial gap formed by material dissolution in simultaneous micro-EDM and micro-ECM drilling using deionized water. Int J Mach Tools Manuf 66:95–101
Sibailly O, Manley J, Richerzhagen B (2003) Mixing laser and water-the use of new wavelengths in water jet-guided laser technology bodes well for applications for transparent material. Ind Laser Solut 18(12):18–19
LIUXIN (2014) Research on EDM-ECM combined machining process for small-hole without recast layer. Nanjing UNIVERSITY of Aeronautics and Astronautics, Nanjing
Datta M, Romankiw LT, Vigliotti DR, Gutfeld RJV (1989) Jet and laser-jet electrochemical micromachining of nickel and steel. J Electrochem Soc 136(8):2251–2256
Lescuras V, Andri JC, Lapicque F, Zouari I (1995) Jet electrochemical etching of nickel in a sodium chloride medium assisted by a pulsed laser beam. J App Electrochem 25(10):933–939
Lau WS, Yue TM, Wang M (1994) Ultrasonic-aided laser drilling of aluminum-based metal matrix composites. CIRP Annals-Manuf Technol 43(1):177–180
Lixin Y, Jiawen X, Jianshe Z (2013) Experimental study of machining characteristics in hybrid proceeding of JECM-LBM on nickel-based superalloy. China Mech Eng 24(3):302–308
Zhang Y, Xu Z, Di Zhu JX (2015) Tube electrode high-speed electrochemical discharge drilling using low-conductivity salt solution. Int J Mach Tools Manuf 92:10–18
Huang SF, Zhu D, Zeng YB (2011) Micro-hole machined by electrochemical discharge machining (ECDM) with high speed rotating cathode. Manuf Sci Technol 295:1794–1799
Funding
This research is supported by National 863 Program (2013AA040101).
Author information
Authors and Affiliations
Corresponding author
Rights and permissions
About this article
Cite this article
Li, X., Zhou, J. & Wang, K. Research on removal characteristics of recast layer of laser-electrolytic machining on small holes. Int J Adv Manuf Technol 97, 3903–3914 (2018). https://doi.org/10.1007/s00170-018-2014-x
Received:
Accepted:
Published:
Issue Date:
DOI: https://doi.org/10.1007/s00170-018-2014-x