Abstract
Press working causes structural deformation of the machine tool, especially the machine tool with large-span gantry or double columns used for the large-sized workpiece. The structural deformation makes the press tool out of accurate positioning, which leads to dimension deviation of the pressed workpiece. Even more, for thin-walled panel riveting, the structural deformation of the riveting machine will cause local deformations of the panel at rivet joints; this accumulated deformation will make the panel out of tolerance. An online deformation measurement and compensation method is developed for adaptive riveting with high accuracy and efficiency in this paper. During the process of servo driving riveting combined with force measurement, the force–displacement data points can be online obtained, and the recognized feature data points by a robust algorithm can represent the critical points during rivet deformation. Combined with the analytical springback of the rivet joint, the deformation of the machine tool can be accurately solved and compensated to the displacement of press tool for highprecision riveting. Simultaneously, with this innovative measurement method, the online quantity inspection for rivet joints can be realized synchronously. Also, a contrast experiment is conducted to validate the effectiveness of the online adaptive deformation compensation based on force–displacement data analysis. The results demonstrate the feasibility of the proposed method in riveting error compensation and riveting quantity inspection.
Similar content being viewed by others
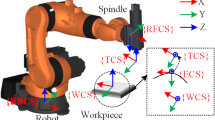
References
Xi FF, Yu L, Tu XW (2013) Framework on robotic percussive riveting for aircraft assembly automation. Adv Manuf 1(2):112–122. http://doi.org/10.1007/s40436-013-0014-5
Szolwinski MP, Farris TN (2000) Linking riveting process parameters to the fatigue performance of riveted aircraft structures. J AIRCRAFT 37(1):130–137. http://doi.org/10.2514/2.2572
Figueira JAN, Trabasso LG (2015) Riveting-induced deformations on aircraft structures. J AIRCRAFT 52(6):1–19. http://doi.org/10.2514/1.C033140
Müller RPG (1995) An experimental and analytical investigation on the fatigue behaviour of fuselage riveted lap joints: the significance of the rivet squeeze force and a comparison of 2024-T3 and Glare 3. Ph.D. Dissertation, Delft University of Technology, Delft
Gemcor (2017) Wing fastening systems http://www.gemcor.com/wp/automation-products/wing-fastening-systems/. Accessed 14 Feb 2017
Electroimpact (2017) E7000 fuselage riveting machine https://www.electroimpact.com/Products/Fastening/E7000.aspx. Accessed 14 Feb 2017
Zhang ZL, Liu ZF, Cheng Q, Qi Y, Cai LG (2017) An approach of comprehensive error modeling and accuracy allocation for the improvement of reliability and optimization of cost of a multi-axis NC machine tool. Int J Adv Manuf Technol 89(1):561–579. http://doi.org/10.1007/s00170-016-8981-x
Sun LJ, Ren MJ, Hong HB, Yin YH (2017) Thermal error reduction based on thermodynamics structure optimization method for an ultra-precision machine tool. Int J Adv Manuf Technol 88(5):1267–1277. http://doi.org/10.1007/s00170-016-8868-x
Cheng Q, Luo R, Gu PH, Wang ZL, Guo HS (2013) Load induced error identification and camber curve design of a large-span crossbeam. Adv Mech Eng 5:847194. http://doi.org/10.1155/2013/847194
Huang ND, Bi QZ, Wang YH, Sun C (2014) 5-Axis adaptive flank milling of flexible thin-walled parts based on the on-machine measurement. Int J Mach Tools Manuf 84:1–8. http://doi.org/10.1016/j.ijmachtools.2014.04.004
Slavkovic NR, Milutinovic DS, Glavonjic MM (2014) A method for off-line compensation of cutting force-induced errors in robotic machining by tool path modification. Int J Adv Manuf Technol 70(9):2083–2096. http://doi.org/10.1007/s00170-013-5421-z
Bi QZ, Huang ND, Sun C, Wang YH, Zhu LM, Ding H (2015) Identification and compensation of geometric errors of rotary axes on five-axis machine by on-machine measurement. Int J Mach Tools Manuf 89:182–191. http://doi.org/10.1016/j.ijmachtools.2014.11.008
Wang Z, Maropolous PG (2013) Real-time error compensation of a three-axis machine tool using a laser tracker. Int J Adv Manuf Technol 69(1):919–933. http://doi.org/10.1007/s00170-013-5019-5
Schneider U, Drust M, Ansaloni M, Lehmann C, Pellicciari M, Leali F, Gunnink JW, Verl A (2016) Improving robotic machining accuracy through experimental error investigation and modular compensation. Int J Adv Manuf Technol 85(1):3–15. http://doi.org/10.1007/s00170-014-6021-2
Rao VS, Rao PVM (2006) Tool deflection compensation in peripheral milling of curved geometries. Int J Mach Tools Manuf 46(15):2036–2043. http://doi.org/10.1016/j.ijmachtools.2006.01.004
Zhang YL, Bi QZ, Yu L, Wang YH (2017) Online adaptive measurement and adjustment for flexible part during high precision drilling process. Int J Adv Manuf Technol 89(9):3579–3599. http://doi.org/10.1007/s00170-016-9274-0
Rans CD (2007) The role of rivet installation on the fatigue performance of riveted lap joints. Ph.D. Dissertation, Carleton University, Ottawa
Уиксов ЕП (1959) Engineering theory of plasticity. Машги, Russia [in Russian]
Zhang KF, Cheng H, Li Y (2011) Riveting process modeling and simulating for deformation analysis of aircraft’s thin-walled sheet-metal parts. Chinese J Aeronaut 24:369–377. http://doi.org/10.1016/S1000-9361(11)60044-7
Halicioglu R, Dulger LC, Bozdana AT (2017) Modeling, design, and implementation of a servo press for metal-forming application. Int J Adv Manuf Technol. http://doi.org/10.1007/s00170-016-9947-8
Shiee M, Sharifi KA, Fathi M, Najafi F (2016) An experimental comparison of PWM schemes to improve positioning of servo pneumatic systems. Int J Adv Manuf Technol 82(9):1765–1779. http://doi.org/10.1007/s00170-015-7501-8
Osakada K, Mori K, Altan T, Groche P (2011) Mechanical servo press technology for metal forming. CIRP Ann-Manuf Technol 60:651–672. http://doi.org/10.1016/j.cirp.2011.05.007
Müller P, Kranz B, Kriechenbauer S, Schlegel H (2015) Experimental and numerical modal analysis of a servo-screw press with coupled drives as a basis for increasing flexibility and dynamics. Prod Eng-Res Devel 9:203–214. http://doi.org/10.1007/s11740-014-0596-1
Shanghai TOPNC (2017) Automatic riveting machines for rocket cabin http://www.topnc.com.cn/adre5/adre11.shtml. Accessed 14 Feb 2017 [in Chinese]
SIEMENS (2017) HMI software http://w3.siemens.com/mcms/human-machine-interface/en/visualization-software/Pages/Default.aspx. Accessed 18 April 2017
Author information
Authors and Affiliations
Corresponding author
Rights and permissions
About this article
Cite this article
Zhang, Y., Bi, Q., Yu, L. et al. Online compensation of force-induced deformation for high-precision riveting machine based on force–displacement data analysis. Int J Adv Manuf Technol 94, 941–956 (2018). https://doi.org/10.1007/s00170-017-0945-2
Received:
Accepted:
Published:
Issue Date:
DOI: https://doi.org/10.1007/s00170-017-0945-2